Here’s how to keep them dependable.
Historically, automotive ignition systems needed more maintenance than just about anything else on the car. Not only would the points, plugs and condenser need to be replaced frequently, but to assure good performance the ignition timing had to be reset between tune-ups because as the points’ rubbing block wore, spark was retarded. Also, the distributor cap, rotor, coil and spark plug wires were all subject to various kinds of damage, such as carbon tracking, so were routinely replaced.
Today, of course, everything is different, and the term “tune-up” has become an anachronism. On the other hand, ignition systems are vastly more sophisticated, so everything involved has to be in nearly perfect condition or you can expect driveability, performance and ignition problems, and diagnosis has definitely gone high-tech.
The purpose of the ignition system is to ignite the compressed air/fuel mixture at the instant that will generate the maximum power and the minimum amount of emissions. Spark timing is determined by a table of data inside the electronic control module (ECM), which looks at engine rpm, load, temperature, etc. Feedback from a knock sensor will cause the ECM to retard the timing to prevent engine damage. Timing may also be retarded while the engine is being cranked both to make it easier to crank and to prevent kickback.
Traffic COP
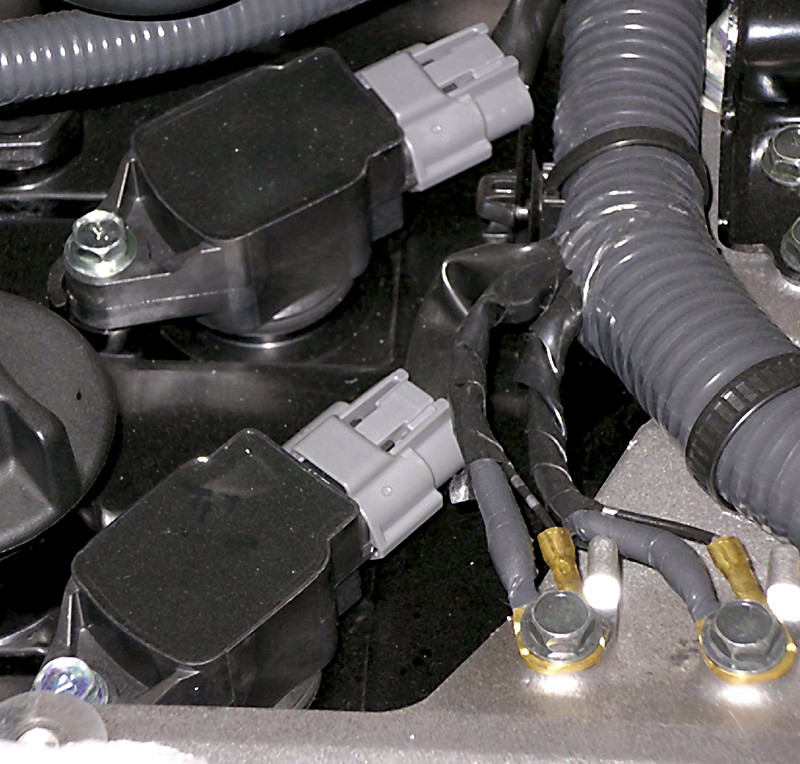
Nissan was one of the first carmakers to use Coil-On-Plug technology, which eliminates many of the components that were prone to problems.
The ECM utilizes crankshaft and camshaft position sensors to know where the engine is in the firing order and when a particular piston is approaching top dead center (TDC). Distributors, rotors, and spark plug wires have mostly been replaced by Coil-On-Plug (COP) technology, which Nissan was one of the first to employ.
When the time is right to fire the spark, the ECM will send a signal to an ignitor circuit within the COP. The ECM monitors the current flowing to the coil during the dwell period and can detect an open or shorted coil. An ignitor is little more than a power transistor with some added circuitry to limit the maximum current flow through the primary side of the coil. Turning the transistor off causes electrical current to stop flowing through the coil, and a spark is generated as the magnetic field of the coil collapses, producing high voltage in the secondary, which is connected directly to the spark plug itself. The actual power for the coils is supplied through the ignition relay; the ECM simply switches it on and off using the transistor in the ignitor circuit much like a normally-closed relay.
Killing cylinders with the Consult II
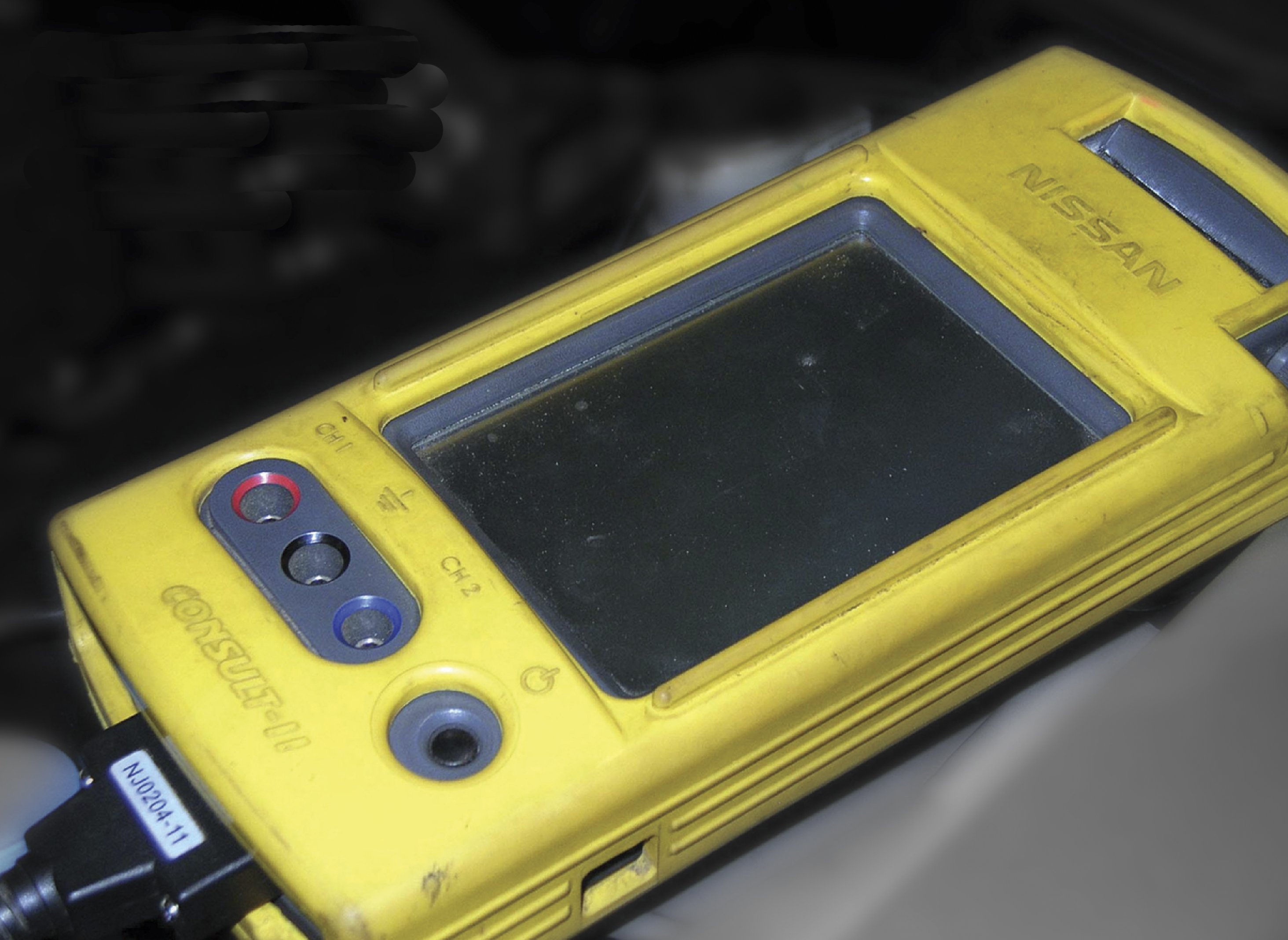
The Nissan Consult II not only allows you to access DTCs, but also gives you the capability of disabling cylinders, which is a great diagnostic help.
Using the Consult II, a technician can disable one cylinder at a time to determine cylinder balance or “contribution.†A sufficiently serious misfire will set a DTC; a potentially cat-damaging misfire will cause the MIL not just to illuminate, but to flash. The challenge comes with a very slight misfire, one not occurring frequently enough to set a misfire code. Often a coil just beginning to fail will cause a P1320 to set. The customer may come in with complaints of a “stumble†or “fishbite†along with the MIL.
Using a clamp-on current probe, Nissan and Infiniti techs can identify the problematic coil by watching the current “ramp†of all six ignitors. A current flow of less than 7.5 amps will often point to the troublesome coil. That number isn’t hard and fast; looking at the scope pattern is the trick. If one “ramp†or “waveform†is noticeably lower than the rest, or deformed (as if the ignitor’s power transistor is fried), there’s the problem. Measuring several good vehicles before having to diagnose a problem one will help the tech in learning to “read†current ramp waveforms. Note that a piece of white tape around the bundle of wires leading from the ECM to the coils provides an ideal location to put the amp clamp. If you’re not fluent using an oscilloscope, this is the perfect diagnostic situation in which to learn. Simply adjust the timebase and gain on your scope until you’ve got a reasonably sized and scaled image, and identify the coil waveform that’s noticeably different from the rest.
Attached to the crankshaft (on some engines, the flywheel) is a toothed ring that allows the crank position sensor (CKP) to tell where the engine is relative to TDC. A double-wide tooth creates a sync pulse that tells the ECM, “I’m at the top now.†Regular teeth give the ECM the ability to determine how far the crank has rotated, how fast, and whether it is accelerating or decelerating. This last point is important. Each time a piston fires, the engine accelerates slightly. An engine idling at 800 rpm is actually running at speeds between (approximately) 775 and 825 rpm, speeding up when a piston fires, slowing down before the next one fires. If the signal from the crank sensor fails to show the expected acceleration, the usual cause is a misfire; one cylinder not making its normal contribution.
Measuring the flywheel’s acceleration or lack of acceleration has to be done carefully, however, since a vehicle being driven off-road can, because of bumps and holes, cause false readings. Newer vehicles are less prone to this problem than older ones, the ECM software having been improved over the years. Misfires occurring while the engine is decelerating in fuel cutoff mode “don’t count†either.
A crank sensor can’t do it all. As with any four-stroke engine, at top dead center, the #1 piston could be either on a compression or an exhaust stroke, and the ECM has no way of knowing which. This is where the cam position sensor (CMP) comes in. Since the cams are driven at half the speed of the crankshaft, a sensor on the camshaft provides the additional information the ECM needs to tell whether a particular piston is on a compression stroke or an exhaust stroke.
Singing solo
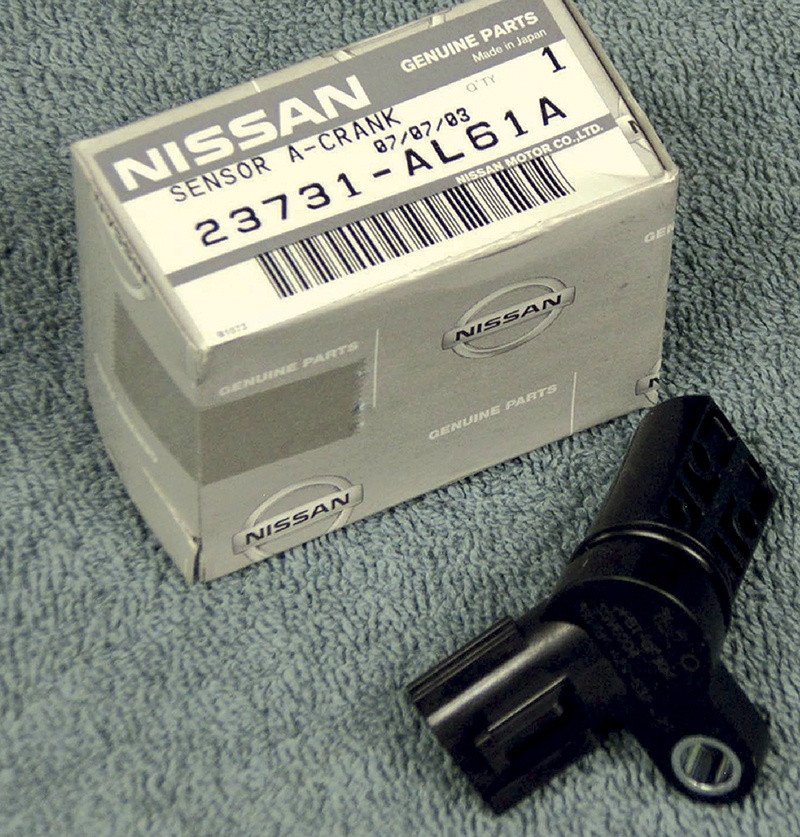
Since the crank sensor is such a critical component, you should probably think twice before installing anything but an OEM replacement.
When the engine is first started, the ECM doesn’t know where any of the pistons are, or where to send a spark.. The engine must rotate one or two times for the ECM to see the sync pulse from the crank sensor and get an internal phase-locked loop in sync. Think of it as the ECM electronically “humming along†with the crank sensor. If the crankshaft suddenly “falls behind,†as it does in a misfire situation, the ECM notices its lovely duet has suddenly become a solo act and it will set a code.
But that’s not the only synchronization that needs to happen. While the engine is being cranked the ECM needs to synchronize the signal coming from the camshaft position sensor with the crank sensor to determine which piston will be the next to reach TDC on a compression stroke, so it can send a spark to that cylinder, and have the engine actually fire up and run.. Before it does this, the ECM performs a sort of relevancy check. If the signals are too far out of whack, indicating, perhaps, a stretched timing chain, a P0350 DTC may be set.
Cam and crank sensors work the way most automotive sensors do, with a toothed ring sporting either one double-wide tooth or a double wide (Arkansas) gap for sync, a magnet, and a Hall effect sensor that can detect presence of tooth or gap. How can and do these sensors go wrong? For starters, heat may cause them to fail. Or, they may break down physically and allow oil to seep in.
Scope and DMM
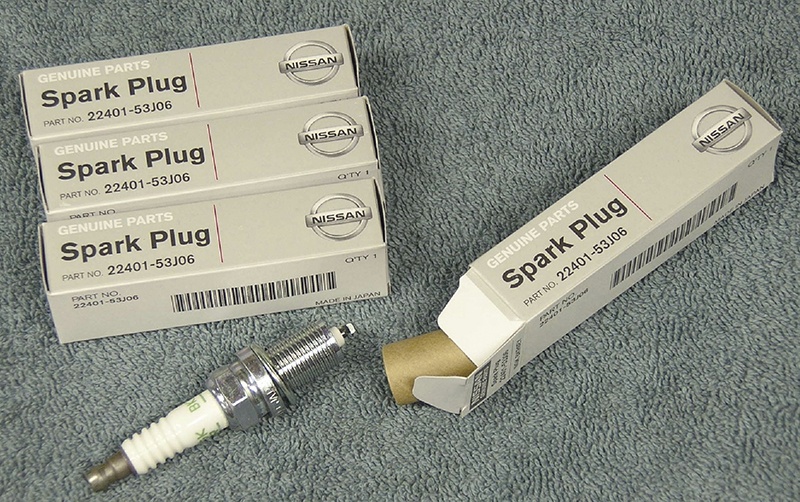
To avoid misfire codes and other possible issues, spark plugs should be original equipment specification. You can be sure of that if you go OEM.
There are a number of checks a Nissan or Infiniti tech can make on cam and crank position sensors. The best is using an oscilloscope to view the output waveform, especially when there’s a concern over whether or not a sensor is intermittent. Far less reliable, but quick and easy, is a resistance check of the sensor, using a DMM. Resistance specs can be found in the Nissan/Infiniti TIS system, although with Hall effect devices, all you’re usually doing is ruling out shorts and opens. Measuring the AC amplitude with a voltmeter isn’t generally advised with Hall effect CKP and CMP sensors.
What happens if the CMP signal is lost while the engine is running, say, due to an intermittently open connection? The ECM won’t know when to fire the spark. The ECM may be humming along, but after a second or two the engine itself may have sped up or slowed down to where a spark arrived too early, and engine damage could result from kickback. Far too early could cause a backfire through the intake manifold, and damage the MAF.
In contrast, if the crank position sensor CKP drops out, it doesn’t have to be quite as big a deal. Misfire detection gets lost. However, the ECM can continue running on CMP information alone. A DTC gets set because if the signal doesn’t come back, the owner won’t be able to restart the car after turning it off. A recent Nissan TSB calls for a software update that ensures that the engine doesn’t stall in the event of a temporary CKP dropout.
Older Nissans with breakerless (optical disc) systems built into the distributor generally have only one type of failure: Oil contamination. If the PCV system on the vehicle isn’t adequately maintained excessive crankcase pressure can force oil up into the distributor and foul the disc. Cleaning occasionally works. Otherwise, distributor replacement is required as the disc is not designed for R&R. You should check for other “common†distributor problems like moisture intrusion and carbon tracking as well.
Aftermarket parts problem
Driveability issues (hesitation, stalling, misfires) may be caused by some aftermarket parts, or by consumer installation. Today’s ignition systems are electrically “tuned†including the length of spark plug wires, sensor impedance, coil resistance, etc. Even use of some aftermarket spark plugs can result in misfires and codes getting set, especially on supercharged engines. Some aftermarket COPs may sometimes set a P1320 right out of the box. A recent posting on iATN described a tech who installed two full sets of aftermarket coils (12) and continued getting a P1320; current ramping (as described above) and replacement of the questionable coils with OEM Nissan parts immediately cured the problem. Once again, the cost of a comeback far exceeds the few dollars that might be saved on a non-OEM ignition part.
0 Comments