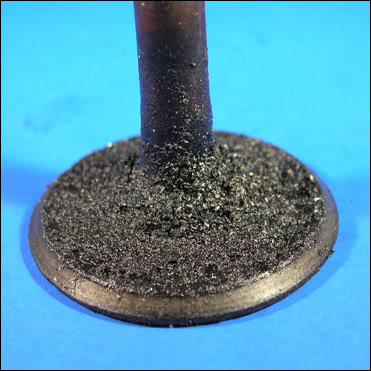
The Associated Press has recently run several articles that say stricter emissions standards may be required in areas of the country that currently have smog check programs, and that places that don’t currently have such a program may be forced to implement one. The Environmental Protection Agency would require an area to meet these new proposed standards, or face sanctions such as the loss of federal highway funds. These stricter emission standards may also be applied to vintage carburetor-equipped vehicles that are currently not required to meet any smog standards.
Tuning a vintage carbureted engine to be less polluting does not necessarily mean that the engine will lose power and driveability. In fact, proper tuning of the ignition system and carburetor should actually improve how the engine performs. Having both spark advance and air/fuel mixture curves properly tailored for the unleaded and reformulated gasoline of today will produce the most drivable power and the least possible exhaust emissions. The people who own these vintage carburetor-equipped vehicles have a passion for their cars, and are always searching for ways to make their engines run better.
In these days when everyone is trying to get the most value from every dollar spent, your shop can offer a service that will provide customers with great running engines that produce the lowest possible exhaust emissions for a reasonable price. The three main areas that need to be addressed in tuning an engine to reduce exhaust emissions are engine deposit removal, the ignition spark timing curve, and the air/fuel mixture curve.
Engine Deposits and Exhaust Emissions
Back in the days of leaded gasoline and carburetor-equipped engines, part of a proper tune-up included the use of a cleaner to remove the carbon deposits that build up on the intake valves and in the combustion chambers. Even with modern fuel-injected engines, decarbonization should be part of any tune-up because the act of burning any gasoline unavoidably produces deposit build-up. These carbon deposits will reduce the engine’s power, fuel mileage, and driveability and can contribute to detonation and NOx formation.
Those that form on the top of the piston and in the combustion chamber can also cause detonation and excessive NOx emissions because they increase both the heat of the burn and the compression ratio. The carbon deposits that form on the intake valves restrict the flow of the air/fuel mixture into the cylinders, interfere with proper swirl, and negatively affect fuel vaporization. When the fuel is not fully vaporized and properly mixed with the air, part of it will leave the cylinders as unburned hydrocarbons, and too much HC can cause a vehicle to fail a smog check. Also, carbon deposits can cause cold-start and driveability problems as the engine warms up because they can actually act as a sponge by momentarily absorbing, then releasing, some of the fuel.
Blasting Deposits
Most of the gasoline sold at your local station has some level of detergents to help prevent and reduce the build-up of fuel-related carbon deposits that both increase exhaust emissions and reduce engine performance. Several of the world’s top automakers worked together to establish a “Top Tier†standard for gasoline that would contain a higher level of deposit control additives. Many retailers sell gasoline with a lower-quality additive package, so unless your customer’s are using gasoline that conforms to Top Tier standards, you should recommend the regular use of some form of deposit-control additive.
The use of a in-tank fuel system cleaner such as Chevron’s Techron Concentrate Plus is a good idea as a part of your customers’ regular maintenance routine on a schedule of every 3,000 to 5,000 miles. There are also several air/fuel system cleaning chemicals on the market, such as BG 44K, Sea Foam, Run Rite, etc. that can be used to rapidly and thoroughly clean the deposits in the combustion chambers and on the intake valves.
Fuel System Deposits
A carburetor-equipped engine does not have anywhere near the fuel system deposit problems that a modern fuel-injected engine has. The injectors are designed to spray the fuel the engine needs in a precise pattern of fine droplets that mix with the incoming air charge. If any deposits form on or near the injector tips, they may degrade the spray pattern or reduce the flow of fuel from the injector. These deposits form on the tip of a port fuel injector mainly during the hot soak period after the engine is shut off. This condition causes the gasoline that is left in the fuel injectors to overheat and turn into a hard varnish, thus beginning deposit formation. The use of a Top Tier gasoline will help prevent this phenomenon and clean fuel injectors as you drive, but sometimes more cleaning is necessary. The chemicals mentioned above can be used to clean fuel injectors, but even the best cleaner cannot confirm that the injectors are flowing properly.
The best method we’ve found to both clean and then check the flow from the injectors is the use of an ultrasonic fuel injector cleaner/flow bench. The ultrasonic cleaning method breaks up deposits (you should also replace the tiny filters that are in the inlets of the injectors). The flow bench allows you to both confirm the volume of flow from the fuel injectors and actually see the flow pattern from each injector, which lets you confirm that all the injectors are working as new. Unless all the injectors supply all the cylinders with an equal and correct amount of atomized in a perfect pattern, the engine will not perform as well as it should, and it will produce higher levels of exhaust emissions.
The CNG Alternative
CNG, or compressed natural gas, is an environmentally-friendly alternative to gasoline because it is a very clean burning fuel. CNG-powered vehicles have lower maintenance costs than gasoline powered vehicles, but they still need service. The fuel injectors that are used with CNG have much higher flow rates than those for gasoline, but they still use the same tiny filter. The CNG injectors we have serviced have had filters that are much dirtier than any other injectors we have seen. The debris that flows thru the fuel system, plus the oil vapors from the CNG compressor can cause fuel injector flow problems as the filter becomes restricted and deposits build up on the fuel injector tip. It would a good idea to have the fuel injectors cleaned and flow tested on a cleaner/flow bench whenever the engine is in your shop for a scheduled tune-up.
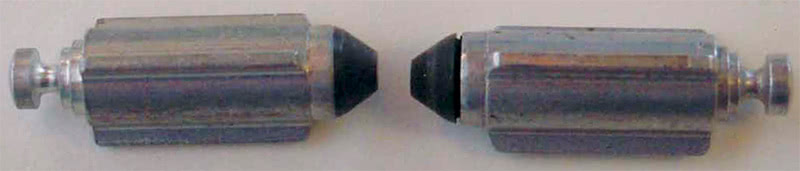
Modern Reformulated Unleaded Gasoline
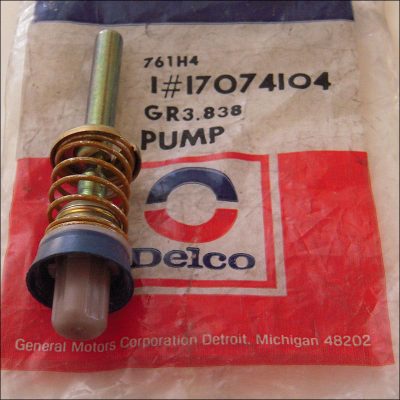
The gasoline of today is quite different when compared to the leaded gasoline that was sold at a corner station in the 1960s and 1970s. The main differences between today’s gasoline and the leaded gasoline of days past that effect how your engine performs are density, volatility, and burn time. The leaded gas that most carbureted engines were engineered to operate on allowed the engine to perform quite well even if the ignition spark timing or the air/fuel mixture was not properly tuned. The same cannot be said for the reformulated unleaded gasoline of today. Unless the ignition spark timing and the air/fuel mixtures are properly tuned to match the needs of the engine, performance and drivability will suffer dramatically.
Modern gasoline is blended with the goal in mind of reducing the evaporative and exhaust emissions of a EFI engine. Reformulated unleaded gasoline does not vaporize as easily in a carburetor-equipped engine as leaded gasoline of days past did. These changes in how new fuel vaporizes can cause driveability problems when it is used in a vintage carbureted engine. We’ve found that many we tune perform better with more initial advance than the original factory setting for leaded gasoline. Reformulated unleaded gasoline actually burns at a different rate than that of leaded gasoline. The total mechanical ignition spark advance (including the initial timing) the engine needs is about the same as it was with leaded, but we’ve found that the vacuum-based spark advance an engine needs is less than it was with leaded. This means that the mechanical and vacuum ignition advance systems will need to be tuned for the blend of gasoline you are using if you want the engine to run at its best.
Modern Gasoline and Carb Parts
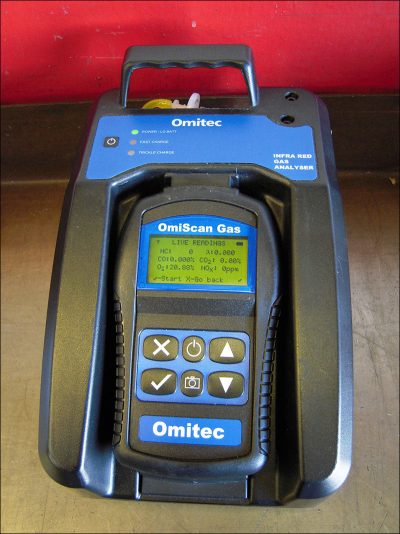
Most carburetors have parts that contain natural or synthetic rubber (such as the needle and seat’s rubber tip, o-rings and the accelerator pump) that may swell or leak when they are exposed to today’s reformulated gasoline. The parts containing rubber that are in a carburetor kit in most cases have been updated to reduce the swelling problems, but this can still be an issue with gasoline that has a high percentage of oxygenates. The formulation of today’s gasoline can also cause the rubber fuel lines and the fuel pump diaphragm to swell, crack or leak. Whenever you work on a carburetor-equipped vehicle, you should inspect all of the rubber fuel lines for potential problems and replace any older rubber hose with fuel lines made from materials that are designed for the gasoline of today.
The density and formulation of these new blends of unleaded gasoline will cause a carburetor to supply the engine an air/fuel mixture that is about 3% leaner than it was with the leaded gasoline. Since exhaust emissions were not a major concern until about 1966, most engines were tuned slightly richer than the ideal air/fuel mixture the engine would need to run its best on. As exhaust emissions standards became stricter, many new carburetor-equipped vehicles began to have driveability problems since they were being tuned on the lean side of ideal in an effort to reduce exhaust emissions. The stoichiometric or chemically ideal a/f (air/fuel) mixture for an engine running on pure gasoline is about 14.7 parts of air to one part of gasoline by weight, while for a gasoline that contains 10% ethanol this is about a 14.2 to one. So, the 14.7/1 ratio is often too lean for the needs of a vintage engine. This means that the carburetor should be tuned or “jetted†richer. This can be done with an exhaust gas analyzer and/or a wideband oxygen/lambda sensor-based air/fuel meter. An engine that has had both its air/fuel mixture and ignition spark advance systems tuned for today’s gasoline will give its owner great performance along with the lowest possible emissions.
The air/fuel meter has the advantages of low cost and a very fast response rate to changes in the air/fuel mixture. A exhaust gas analyzer is more expensive and its response rate is in the five to eight second range, but because it looks at the five main gases in the exhaust its reading can provide a tuner with a lot more information than just than just the air/fuel ratio. The CO (carbon monoxide) reading is used to determine the a/f mixture; the HC (hydrocarbon) reading tells the misfire rate; the CO2 (carbon dioxide) reading is an indicator of engine efficiency; and a high NOx reading points to over-advanced ignition spark timing.
The best tuning results will be achieved by first using an exhaust gas analyzer to establish a baseline, then switching to a digital air/fuel meter to read the a/f ratio curve in real time on a engine dyno, or on a road test. Many of the top race engine tuners and builders use an air/fuel meter system with one lambda sensor per cylinder so they can see the ratio of each cylinder both on a dyno and in the transient conditions the engine will see on the track.
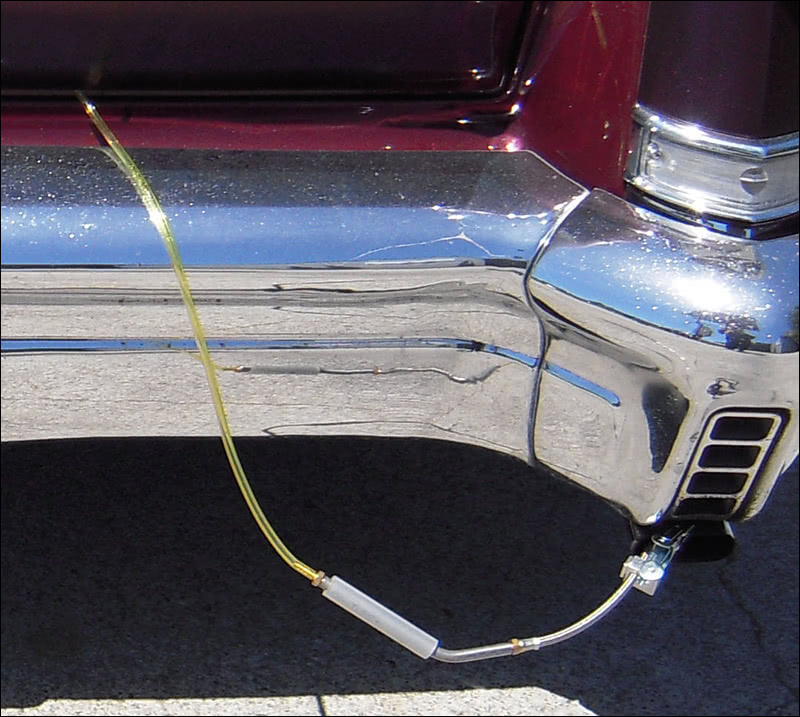
By Henry P. Olsen
0 Comments