Let’s explore the technical workings of the electrically-driven air conditioning systems found on Nissan Hybrids and the all-electric LEAF, system diagnosis, and why leak detection using dye must be avoided to prevent costly additional repairs.
It isn’t news that hybrid and electric vehicles are on the road to stay. Nissan has released plans to develop the luxury Infiniti M35 Hybrid, and has started manufacturing the all-electric LEAF. What were once familiar air conditioning repairs have evolved with the hybrid electric or all-electric drivetrain, and a system you might think is unrelated to hybrid components is actually inextricably woven together with them. Instead of merely being unsuccessful at the repair, you now risk extremely expensive collateral damage. Do it right the first time, and read up on the factory service procedures!
First things First: Precautions
Before you begin work on the electrical A/C systems of any Nissan hybrid, consult the service manual. Take note of two important warnings:
- DISCONNECT THE HV SERVICE PLUG. GRIP USING LINEMAN’S GLOVES AND DO NOT TOUCH THE HV CONNECTORS OR TERMINALS FOR 10 MINUTES AFTER THE PLUG IS REMOVED WHEN WORKING WITH THE ELECTRIC COMPRESSOR UNIT.
- DO NOT USE A/C EQUIPMENT THAT HAS NOT BEEN DEDICATED TO ELECTRIC COMPRESSORS USING ONLY ND-OIL 11, OR HAS NOT BEEN PROPERLY PREPARED FOR USE WITH ELECTRICAL A/C (DISCUSSED BELOW).
Failure to disconnect the service plug risks your life and the lives of others who may be unaware of the repair you’re performing. Remember to carry the service plug with you until the repair is completed to prevent another worker from accidentally restoring high voltage to the system.
We will discuss the second precaution in more detail later, but for now, know that the electric compressor uses an insulating oil to prevent high voltage leaks within the system. If you contaminate this oil by using standard PAG oil and dye, it can not only damage the compressor, but it could possibly infiltrate the entirety of the electrical A/C system and require total component replacement! Not cheap!
System differences and similarities
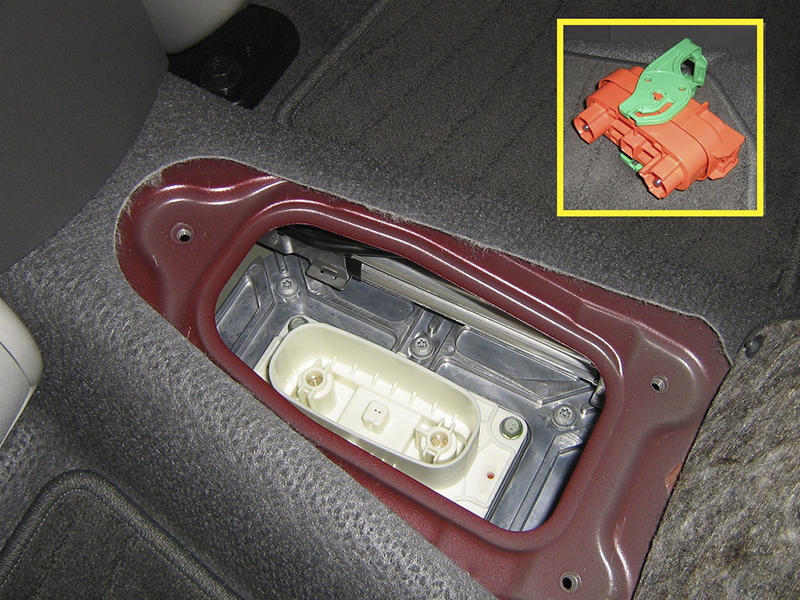
Locate and remove the high-voltage service plug to disconnect the battery from the electric compressor. This plug is on the LEAF.
Don’t be too intimidated by the electric compressor A/C system, because it is not at all conceptually different from your typical belt-driven air conditioning. If you follow the aforementioned precautions, and read the service manual, electrical A/C work can be profitable and rewarding.
Let’s take a quick look at everything that functions identically between normal and electric A/C systems:
- Refrigerant is the same (HFC-R134a).
- The HI and LO side pressures are similar. Consult the repair manual chart.
- Condenser is the same.
- Receiver/Drier is the same (Nissan calls it the Liquid Tank).
- Evaporator is the same.
- Thermal Expansion valve is the same.
Let’s make a short list of what’s different:
- The A/C oil is different. The electrical systems use ND-OIL 11, which is a non-conductive oil that CANNOT be interchanged with standard PAG.
- The electric compressor is driven by an electric motor, rather than a drive belt.
- Multiple computers control the electric compressor and other A/C systems.
Nissan also uses a refrigerant pressure sensor, which reports the high pressure liquid refrigerant pressure to the ECU. Some modern belt-driven A/C systems may also employ this sensor separately from the HI/LO pressure cut off switch or relief valve. It is located on the liquid tank.
The heart of the electric A/C system: the compressor
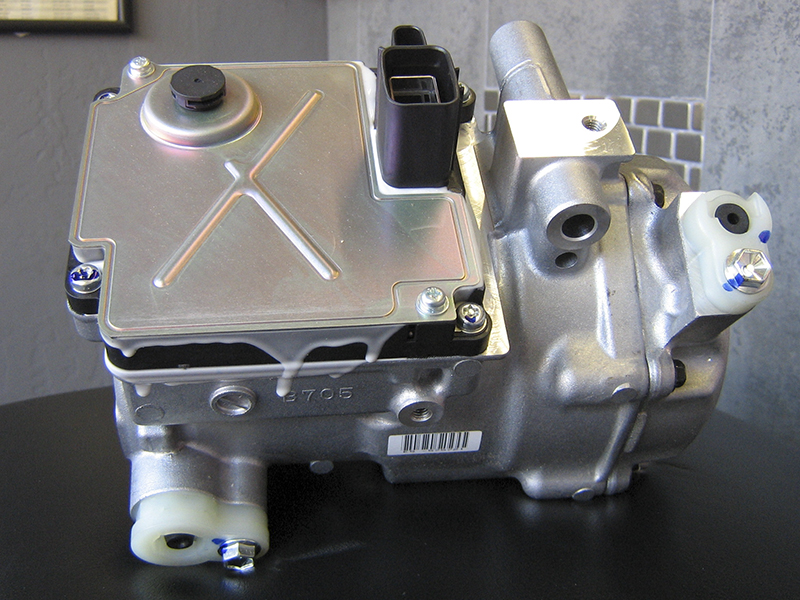
The electric compressor for a 2009 Altima Hybrid. Take note of the on-board inverter and control module. The insulating resin has leaked a bit from this unit, not a problem.
The electric compressor deserves its own section. First, we will discuss why hybrid systems utilize this design; then, we will outline the detailed workings of the device and its benefits.
The internal combustion engine of a hybrid vehicle shuts down intermittently when not required. Therefore, there is no guaranteed source of power from a crank pulley to drive a standard compressor. If the internal combustion engine shuts down to conserve power under light load or while sitting in traffic, a standard compressor would not spin. Therefore, the engineers at Nissan have bypassed the need to keep the engine idling for A/C by introducing the electric compressor. Due to the large demand for power from the A/C system, the electric compressor is directly linked to high voltage via the inverter.
Running the electric A/C compressor requires a large amount of power. If the battery becomes drained, the HV ECU may request that the internal combustion engine restart and begin charging. This causes a reduction in mileage and fuel economy. Yet, it is no different from the increased load from a standard compressor.
Additionally, in an electrical air conditioning system, the A/C control unit (Auto Amp) has the ability to constantly request a change in the RPM of the electric compressor for maximum efficiency. As a result, the electric compressor will not be cycling FULL ON or OFF as a typical belt-driven compressor with a clutch would. Instead, the RPM range will vary between 0 and 12,000, based on calculated need. This may change system pressures, but it allows the Auto Amp to more effectively match the driver’s requested temperature as efficiently as possible.
The three-phase power aspect of the electric compressor
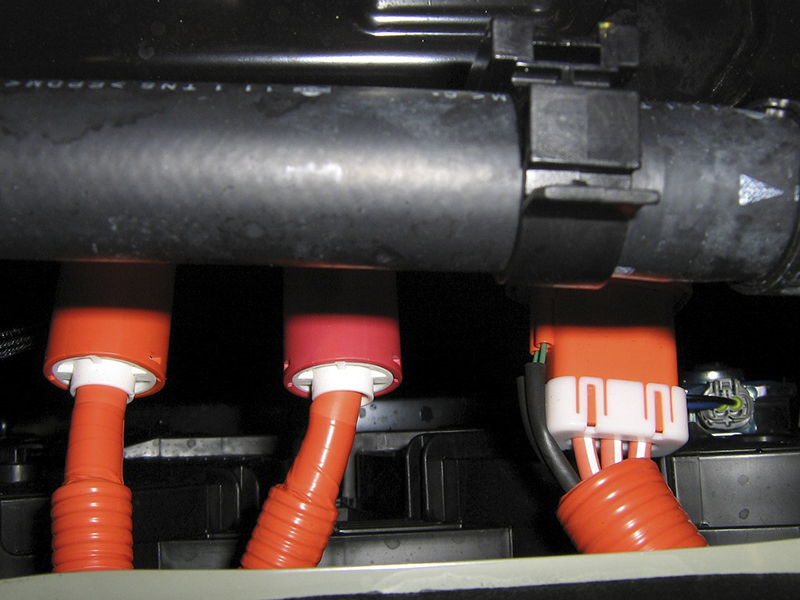
On the right, the three-wire connector attaches inverter to the electric compressor. System shown is the LEAF.
Because an electric compressor can be controlled with more accuracy, and does not require a spinning crank pulley, it is inherently more efficient. It can perform the same duty as a standard compressor with more consistency, and is therefore ideal for a high miles-per-gallon hybrid. However, this new system requires re-education about its design and control. Let’s investigate the electrical compressor’s physical design.
When inspecting the electric compressor, you will immediately see three high voltage lines attached. Three-phase power is provided from the hybrid inverter. Unlike standard 12V systems, power does not flow through chassis ground. Instead, the power flows from phase to phase, constantly changing as necessary. The compressor is also connected to the HV ECU in order to report its RPM, and to receive the command for the Auto Amp’s desired RPM. Like the hybrid motor/generator, the A/C compressor consecutively energizes three sets of windings to create sequential electromagnetic fields. In the electric compressor, a permanent magnet attached to the compressor input shaft will “chase†the ever-moving electric fields generated from the energized windings. The chase causes the compressor to spin.
In a three-phase motor of this kind, if a short-to-ground occurs, high voltage would be detected by the ECU. This highlights the importance of ND-OIL 11: insulation. Since this special oil is non-conductive, it prevents the windings from shorting to the metal housing of the compressor, which is grounded to the chassis. Using the wrong kind of oil or dye will create a potential for voltage to go to ground, creating a serious safety hazard, if someone were to come in contact with another high voltage line, he could be electrocuted.
Furthermore, there is a possibility for a phase-to-phase short to occur when the insulation is compromised. For this reason, it is not recommended to ignore or otherwise avoid any high voltage leak detected fault even though it’s “just the A/C.†A shorted winding could result in high temperatures and possibly smoke from under the hood!
High-voltage leak detected
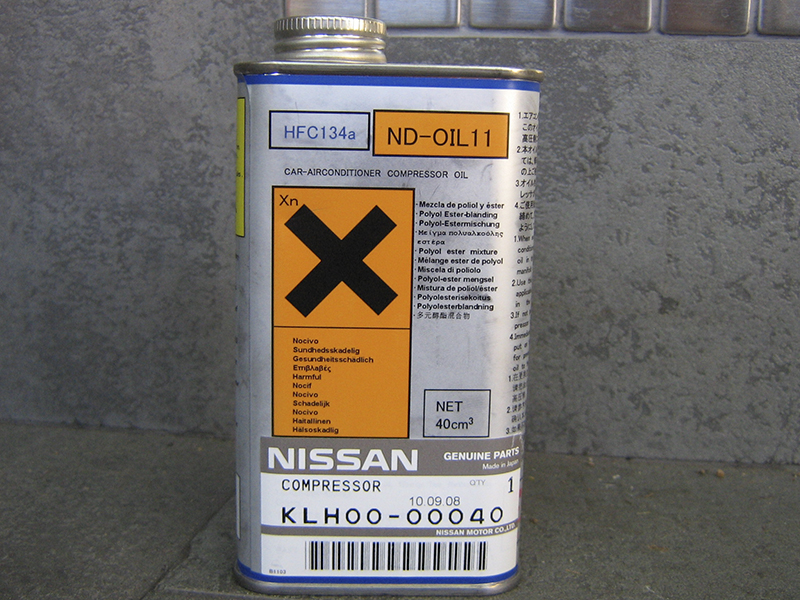
This special oil may take some time to receive, so be sure to have some on hand so you don’t cause a delay for your customer.
A breakdown in insulation will result in DTC P0AA6 with info code 611. You may be unable to command the A/C compressor to engage. If it operates, A/C performance may be degraded. If you put the wrong type of oil in, cycling the compressor will increase the exposure of the rest of the system, which may result in more expensive additional repairs. Nissan states that even if a small amount of oil is used or accidentally enters the refrigerant recharge cycle, the DTC can be set. Confirmation of a high voltage leak can be performed with a “megger” (megaohmmeter). Check resistance between any one of the high voltage cables on the compressor and ground; Nissan’s specification is at least two million ohms (2 MOhm): less than that indicates an internal short that would cause high voltage leakage.
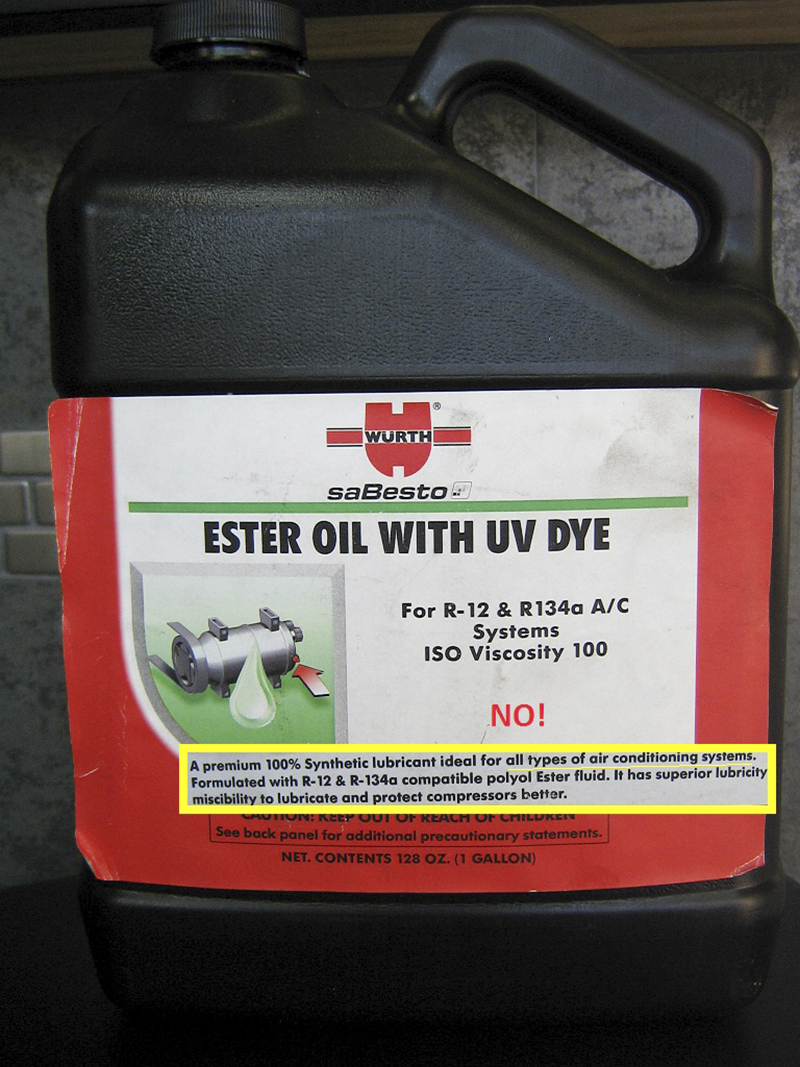
Don’t use standard compressor oil, despite what the bottle may advertise. You can cause a huge headache!
If you suspect the P0AA6 DTC is from contamination due to dye, moisture, or conductive oil, Nissan says to replace all of the main components – evaporator, condenser and compressor – then flush the lines. Obviously, total component replacement is not a cost-effective or realistic method for A/C repair.
It is required that you prepare your A/C equipment for electrical A/C work first to avoid contamination of the ND-OIL 11. The easiest method is to obtain dedicated equipment for electric A/C work; however, this is not always practical. It is possible to flush some A/C machines with R134a, eliminating all traces of traditional oil. Other machines have oil strippers that can remove oil before it enters the car’s A/C system. The A/C machine should be SAE J2788 standard-compliant, or it should not be used for electrical air conditioning repair. Once your machine is ready, DO NOT add UV dye to aid in leak detection. The dye is conductive, and it only takes a small amount to negate the insulating properties of ND-OIL 11. At this time, there are no Nissan-approved dyes.
Understanding electrical A/C controllers
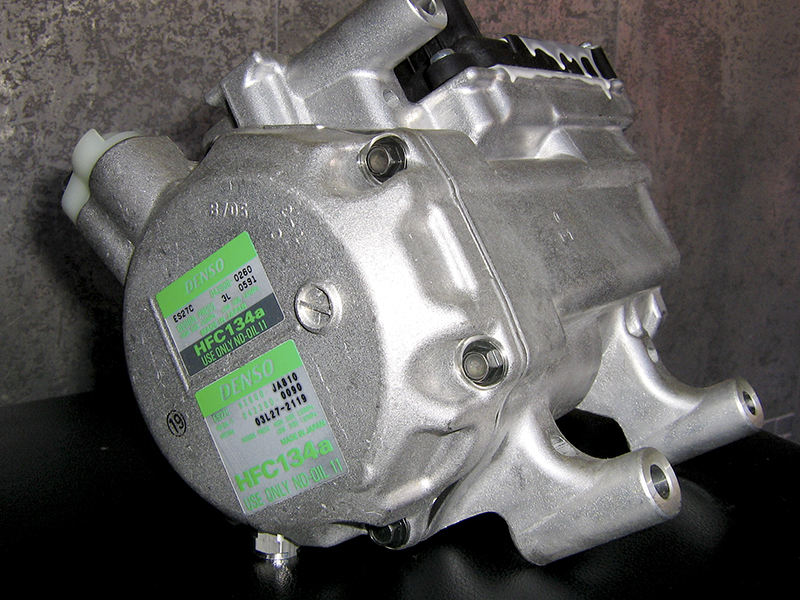
The Altima hybrid’s electric compressor has a sticker indicating the required refrigerant R134a and special oil, ND-OIL 11.
The automatic air conditioning is primarily controlled by a dedicated computer that Nissan calls the Auto Amp. The customer provides direct commands to the Auto Amp unit by manipulating the dash controls. Understanding the relationship the Auto Amp has with the other computers, the under-dash A/C unit, and the various A/C-related sensors is crucial. Understanding the relationship the Auto Amp has with the other computers, the under-dash A/C unit, and the various A/C-related sensors is crucial.
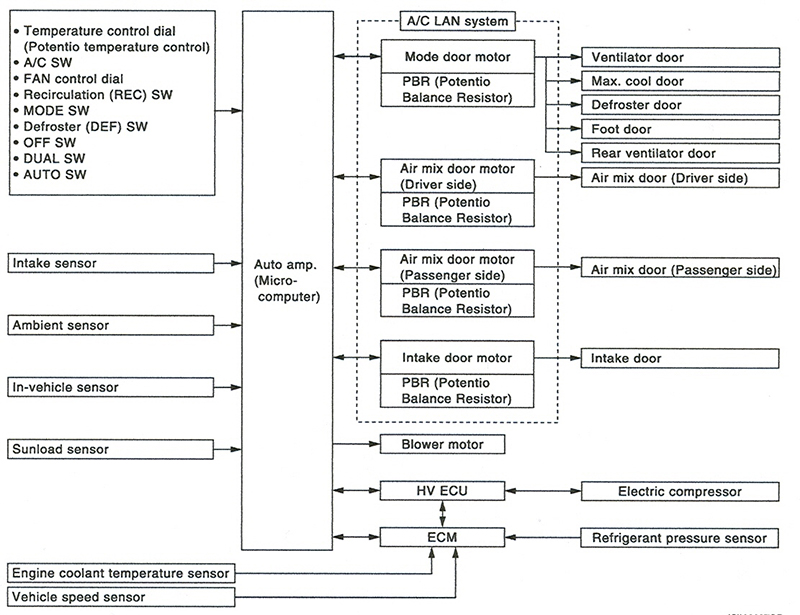
Nissan provides a system diagram to explain the flow of information among all the components. Altima Hybrid shown.
The Auto Amp communicates with multiple ECUs to control the various electronic A/C components as necessary, based on information it receives from the inlet temperature sensor, ambient temperature sensor, in-vehicle cabin temperature sensor, the sun load sensor, as well as engine coolant temperature, vehicle speed, and refrigerant pressure information from the main ECU. Using the A/C LAN system, the Auto Amp will automatically control the vent door and blower motors that reside within the A/C plenum beneath the dash.
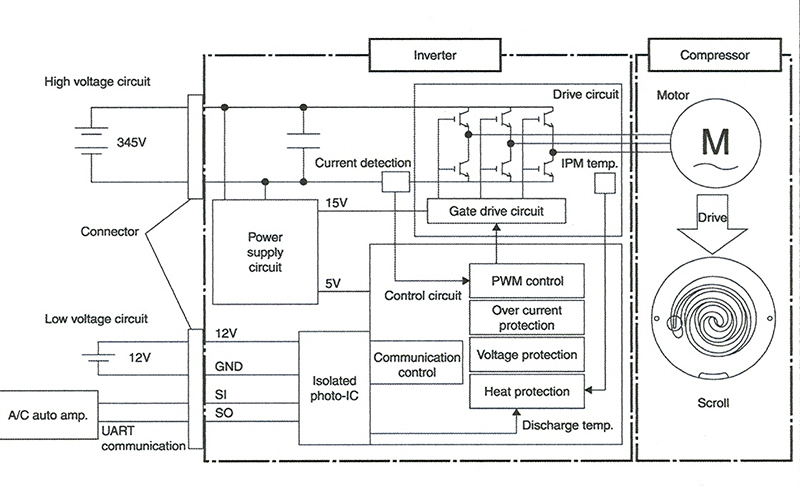
The electric compressor uses PWM (Pulse Width Modulation) within the inverter to control the three-phase motor based on input commands from the Auto Amp via the HV ECU. Nissan LEAF shown.
The ICE ECU shares useful information about vehicle speed and engine coolant temperature with the Auto Amp that then can prohibit compressor operation in the event of vehicle overheating, or stop the condenser fan from cycling above a certain vehicle speed. The compressor RPM is controlled by the HV ECU once the Auto Amp has calculated and requested the ideal speed from sensor input.
The under-dash A/C unit contains blend and vent door motors, a communications bridge to the Auto Amp, the evaporator and heater core, blower motor, and the evaporator inlet temperature sensor. The Auto Amp controls this unit via the CAN bus, so any failure along the CAN may result in A/C malfunction. The Auto Amp controls driver/passenger comfort zones by manipulating the vent and blend door motors within the under-dash A/C unit. It is important to remember for diagnosis that all electrical controls and motors must be checked before assuming there is a refrigerant charge issue.
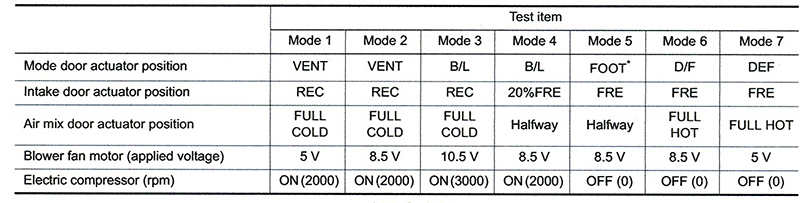
Using the CONSULT, choose from one of seven self-tests to verify compressor speeds, blend and vent positions, and blower motor operation.
Electrical A/C diagnosis
When working on modern hybrids, your first diagnostic tool should be the CONSULT. The electrical A/C system will have DTC information stored about any detected faults. The information gained from a DTC call will be invaluable for properly repairing the air conditioning. Furthermore, the CONSULT provides a self-check for air conditioning that will test various compressor speeds and vent/blend door positions. The CONSULT can also evaluate CAN-related errors, and illustrate a break in communication between two nodes. Why waste time and energy charging and recharging the A/C system when the problem is not the refrigerant, but the electrical control of some component?
The majority of the physical components within an electrical A/C system are identical to standard air conditioning: high-pressure hoses connect the compressor to the condenser to the expansion valve and the evaporator. Use some common-sense checks: If the low-pressure hose is cold to the touch, the A/C is operational. Check the high- and low-side pressures with gauges at the service ports; this information is still relevant to electrical A/C diagnosis. Use the pressure charts available in the repair manual to assist in diagnosis.
Use the CONSULT to gather DTC information directly from the A/C control units. Many A/C control malfunctions will store fault information, and the repair manual will include diagnostic trees to figure out the problems. Electrically-powered A/C systems require a slightly different approach than normal A/C, but don’t be intimidated. Just think about the CONSULT as your first tool available to gather information about the behavior of the controls and the various sensors necessary for normal A/C operation. Reference the System Diagram in the service manual to understand the interaction among all the players in this different A/C game.
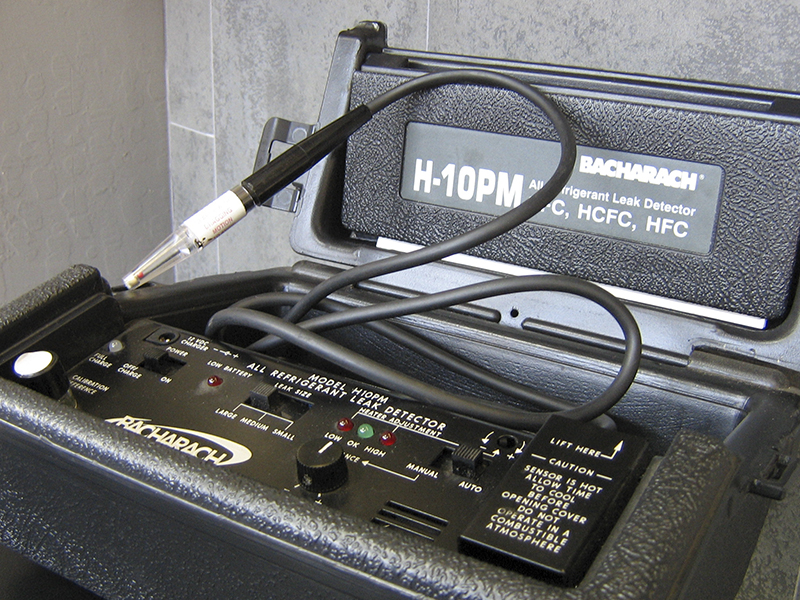
Electronic refrigerant detectors like this unit must be used in place of UV dye when searching for leaks.
You can also utilize the bi-directional controls within the CONSULT’s active test section to aid in diagnosis. Access the work-support section within CONSULT, then select the system you wish to command. For example, if a DTC is set about target compressor RPM not being met, you can determine at what load this occurs by commanding the compressor to incrementally increase RPM.
The CONSULT will also provide multiple PIDs (Parameter Identifiers) within the live data for all the A/C controls. From this section, you can monitor the sensor outputs and identify, at a glance, anything that seems out of specification. The repair manual details the PIDs available, including the units and “plain English†descriptions.
Some PIDs like HEATER NUP or NE HEATER might shed some light on strange A/C problems. HEATER NUP indicates a command has been made from the HV ECU to the CAN bus for the internal combustion engine to turn on. NE HEATER is the requested RPM of the engine necessary to provide the desired heater temperature, as interpreted and calculated by the Auto Amp. Maybe the customer complains that the engine is working hard with the heater on, but that’s because the NE HEATER PID shows that the A/C is requesting an unusually high engine RPM. The problem lies with the A/C system, not the engine!
Proper follow-up checking without using dye
After component replacement is completed, doing follow-up leak detection may be difficult without dye. However, Nissan recommends using an electronic refrigerant leak detector, or sniffer. Prior to leak detection, Nissan notes that the A/C static pressure should be at least 50 psi of pressure above 16 degrees Celsius. Consult the appropriate chart in the repair manual. Clean the areas to be checked, and begin with the high pressure side. Move the sniffer around the compressor, hose fittings, relief valve, service ports, condenser, and liquid tank. Do not stop to repair a single leak if detected! Continue checking the entire system making notes about potential leaks. Use compressed air to clear the areas and revisit the previously noted leaks to verify there is active seepage.
To check for leaks at the evaporator, turn the ignition ON, but not READY. Run the blower motor for at least 15 seconds to clear out any trace refrigerant. Wait about 10 minutes for enough refrigerant to accumulate, then insert the nose of the sniffer into the A/C unit drain tube to check for leaks.
The last step is to ready the vehicle. Run the A/C on MAX COLD with the vents set to RECIRC for at least two minutes. Shut off the A/C and check for leaks as outlined above immediately. Start at the high-pressure side of the compressor. The pressure will steadily decline when the system is shut off.
Because O-rings are common leak points, Nissan has issued a chart to aid in proper O-ring replacement. Any new component will utilize a new O-ring, so do not attempt to compare the O-ring removed from the old component, even if you have a stash of various sizes of A/C O-rings. If the wrong O-ring is installed, refrigerant will leak at or around the connection.
Nissan will always strive to create the most efficient systems for their cars. The hybrid and electric vehicles have the benefit of a direct, high voltage source that can power an electric compressor. The future of auto repair will not be in basic removal and replacement, but rather in the knowledge of interconnectivity among advanced systems and their electronic controls. Keeping up with the technology takes training and awareness, but it will continue to be necessary for working with all future automobiles.
0 Comments