Chemical bonding is increasingly the preferred joining technology
Chemical bonding through the use of structural adhesives is not new to the collision industry, but the need for repair professionals to keep pace with advanced adhesive materials, equipment, and procedures is now on the front burner. Going forward, the repair of Mercedes-Benz body panels and other components demands a commitment to continuing learning about bonding techniques and practices. It’s also an opportunity.
Advanced adhesive formulations are now available
Structural adhesives are not new; they’ve been used for more than 25 years in the automobile industry. Early adhesives were of the single-component variety, which at that time was sufficient for some repairs involving conventional mild-strength steels. These yielded to two-component adhesive formulations that provided improved bonding properties and allowed more working time.
That was fine until the materials that vehicles were manufactured with began to change in response to demands for lighter weight, more rigidity, better driving and environmental performance, improved safety, and lower manufacturing costs. To stop the ever-increasing mass spiral without penalizing safety and comfort, automakers have transitioned from using mild tensile-strength steels to lighter weight, but stronger materials, such as higher-strength steels, other metals (aluminum, magnesium, titanium, etc.), thermoplastics, carbon fiber-reinforced plastics, and other composites.
This ongoing evolution is driving the increased use of chemical bonding (using structural adhesives) as the preferred and recommended joining method, rather than welding, riveting, or other practices. Body panel repair instructions, for example, commonly prescribe chemical bonding procedures that use adhesives.
But challenges exist for adhesives (as they do for other technologies). The reason: High-strength steels, alloys, and plastics come in different grades, which impacts how each material performs under various stresses during normal operation and during a collision. Automakers are now aware that the mix of material choices used to manufacture a vehicle requires adhesives that were formulated to match the materials being repaired.
Modern adhesives are more crash resistant
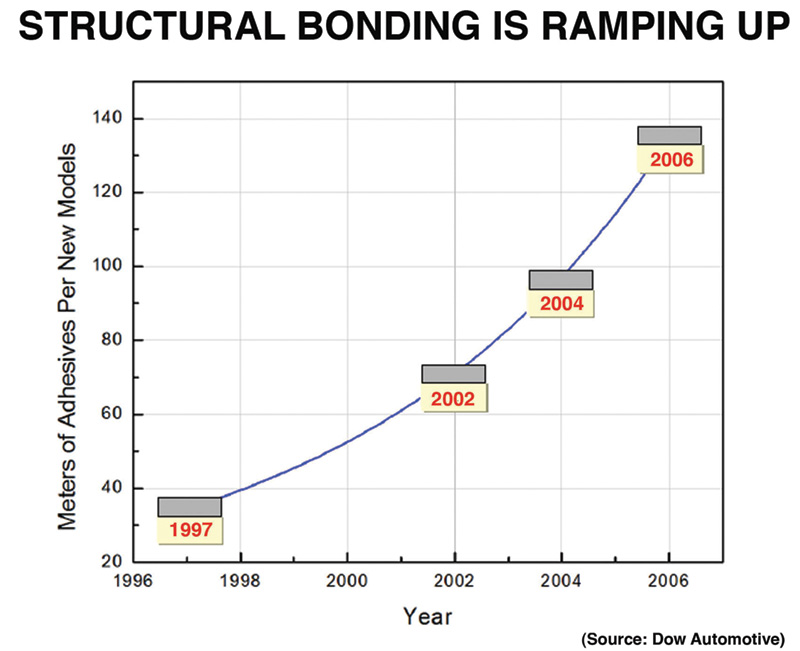
Beginning in the mid-1990s, structural adhesives usage began to accelerate. In 1996, for example, approximately 35 meters of adhesives could be found in a new Mercedes-Benz S-Class model. By 2006, the S-Class had over 135 meters present. It’s continued to grow since and this trend is prevalent in other Mercedes-Benz classes. (Image — Dow Automotive Systems)
Applying adhesive is a more complicated process than just slathering on some glue and clamping the parts together. Modern automotive structural adhesives are made from chemicals called epoxies, which typically come with two parts, a resin and a catalyst that are kept separate until used. When combined during a repair, the catalyst initiates a chemical reaction in the resin. Expect to feel the bonded parts heating up as the resin develops its bonding properties and the mixture cures.
The two-stage structural adhesives in use today include polyurethane epoxies, glassy matrix epoxies (which have glass beads embedded in the resin), and rubber-based epoxies. Glassy matrix epoxies are extremely strong and rigid, and they resist shearing stress — the lateral separation of the bonded parts — at very high force levels. Polyurethane epoxies are more flexible and provide a better fit for some components, but they break under shearing forces at much lower force levels than glassy matrix epoxies. Newer rubber-based adhesives contain additives that allow synergistic rubber toughening of adhesives to provide high-strength epoxies with greater flexibility — a hybrid of earlier formulations.
The curing ability is built in to the adhesive, but it requires a lot of testing and some impressive chemistry to meet an automaker’s specifications. In some cases, curing may be aided by baking or some other procedure involving applied heat. Some epoxies even cure with the application of ultraviolet light. Note that the curing times for various adhesives can range from just a few minutes to a day or even longer. Automakers know their vehicles, so following their collision repair procedures and using the approved resources ensures that technicians have adequate working time to effect a safe, complete repair.
For example, some repairs may only require a two-stage adhesive, while others may require the use of adhesives and rivets — a process known as rivet-bonding — or the combination of spotwelding. Technicians should note that repairs involving aluminum should use aluminum rivets, those involving steel should use steel rivets, and that a coating of zinc dust to prevent corrosion may be required. Be sure to use the number of rivets specified in Mercedes-Benz service information.
Chemical bonding provides stronger and more durable repairs
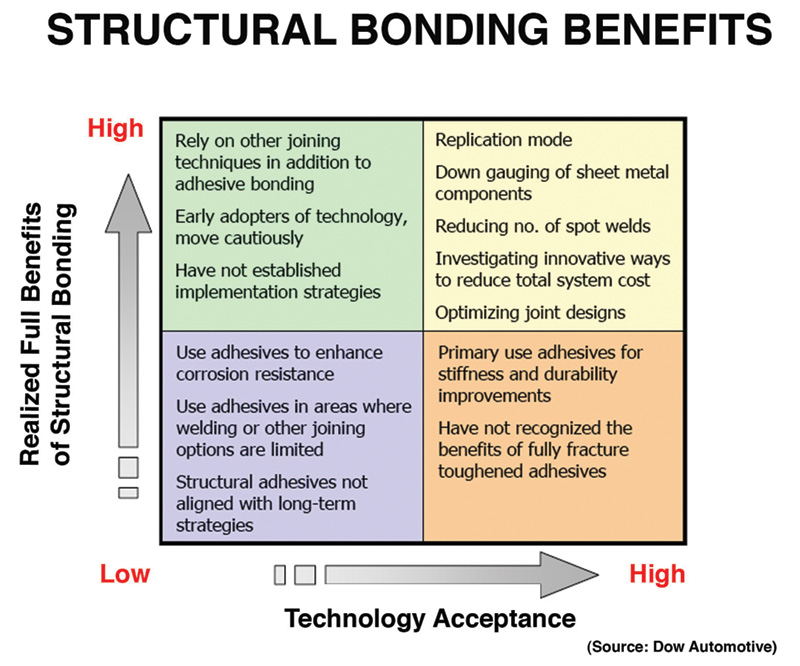
The shift in the acceptance of chemical bonding technologies by automakers is leading to the realization of many benefits, some of them unexpected surprises, such as the opportunity to use thinner body panels without sacrificing performance or safety. (Image — Dow Automotive Systems)
While based on earlier two-component structural adhesives, newer adhesives also include advanced special polymers, epoxy resins, adhesion promoters, and other additives that improve bonding, manage stress more effectively, provide better mechanical properties and resist corrosion when compared to alternative joining technologies.
According to several industry sources, these newer adhesives provide a number of advantages. Dow Automotive Systems and 3M note that using the new two-part adhesives and procedures recommended by Mercedes-Benz for chemical bonding repairs:
Provides more durable and stronger repairs with less corrosion risk than welds alone. In fact, adhesives usually form a bond stronger than the materials they’re bonding together. In the future, as carbon composites are increasingly used, adhesives might be the only way to bond them, as carbon fiber panels cannot be welded together.
Reduces the number of welds that would have otherwise been required. For example, Mercedes-Benz requires OEM rivets and OEM structural adhesive to be used in areas that squeeze-type resistance spot welding (STRSW) arms cannot access, or when replacing USIBOR (boron) components. Adhesive bonding is also a well-known complement to help resolve problems with cracks around spot welds occurring as a result of fatigue loads.
Allows the various stresses during vehicle operation or a collision to be more evenly distributed across a region that is joined with adhesives compared to those joined only by welds, rivets, or other joining methods.
Enables the flow of energy force transferred in an accident to remain truer to the automaker’s design intent.
Facilitates the down-gauging of metals (e.g. thinner and lighter body panels, less steel reinforcement) for lightweight, optimized vehicle construction.
Replacing otherwise necessary sealant materials with adhesive not only seals out water, it also improves noise, vibration, and harshness (NVH) by dampening airborne noise distribution and minimizing body vibrations.
Improves the structural integrity during side-impact IIHS tests.
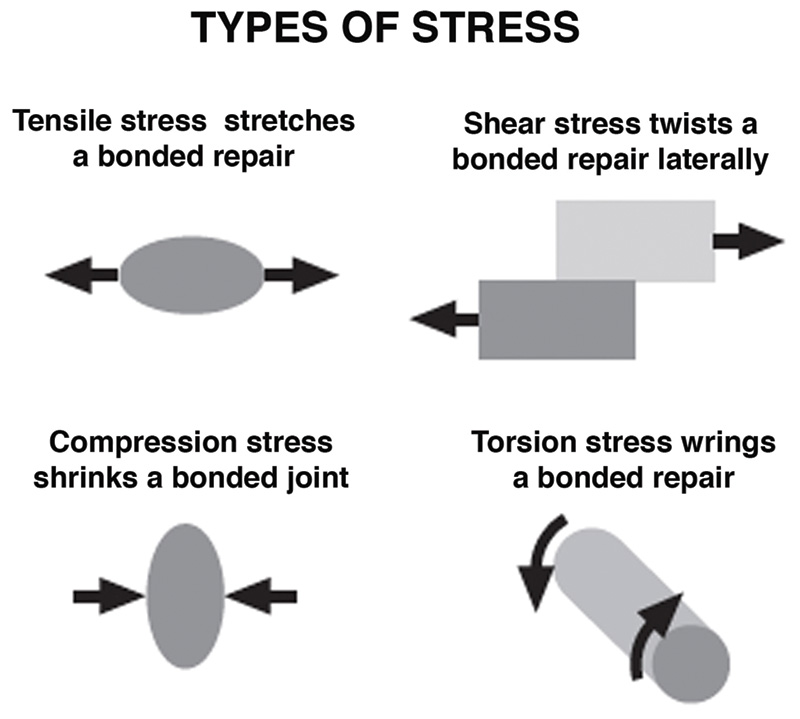
Chemical bonding using MBUSA-approved structural adhesives, tools and procedures enables body panel repairs to better handle various type of stress compared to other joining technologies. The best place to use a structural adhesive is in a location where the primary forces are either compression (where the joined pieces are pushed together), or shear, where the force tries to slide the joined surfaces against one another, like pressing your hands together and trying to slide them apart. Structural adhesives are typically not good to use if the force acting on the joint would pull the two pieces apart as most adhesives have poor peel strength. Another poor location for a structural adhesive would be one where there are forces that would bend the joint, which could allow the joint to cleave and then peel. In these latter two cases, repair procedures may specify that adhesives be used with rivets (rivet-bonding) or in conjunction with certain welding techniques. (Image — Dow Automotive Systems)
Empowers the introduction of lighter-weight carbon fiber roofs and other non-steel and non-alloy components without compromising strength, safety or durability.
Adhesives also enable hybrid sandwich construction to be employed in manufacturing. For instance, the front flexural and supporting structure in some models (e.g. CL) is a load-bearing assembly made of carbon fiber-reinforced plastic sandwiched between aluminum sheets.
It is important that adhesives not be the weakest link when joining adherent surfaces or components. Modern bonding adhesives provide acceptable or improved elasticity and flexibility, in addition to better tensile and shear stress strength than the materials being bonded. Be cognizant that Mercedes-Benz employs different mixes of construction materials than other automakers during manufacture. In addition, just like different grades of new and emerging steel can be used, repairers should be aware that there are also different grades of aluminum and other metal alloys, plastics, and even carbon fiber. Mercedes-Benz collaborates with adhesive manufacturers, such as Dow Automotive Systems and 3M, to develop structural adhesives that are best suited to their specific models and repair applications. These may or may not be the same ones required by other automakers.
MBUSA also has a number of position statements pertaining to body panels and chemical bonding adhesives. For instance:
MBUSA does not support the use of critical recycled parts and assemblies, especially parts and assemblies that are welded, riveted or bonded to the vehicle structure during the assembly/manufacturing process. Replacement of structural body panels/members/assemblies (clipping or partial clipping) with recycled parts is unacceptable and not approved by MBUSA.
Malfunctions caused by body repairs not performed in accordance with Mercedes-Benz specified repair procedures or otherwise not properly performed are not covered by the Mercedes-Benz New Vehicle Limited Warranty and may cause the car to not perform as originally designed in a subsequent collision to the repaired area.
Consequently, it is critical that repairers know and use repair procedures developed by Mercedes-Benz, along with lists of approved supplies, tools and equipment. Hence, it is crucial that technicians refer to Mercedes-Benz collision repair resources noted in the Need More Info? sidebar. Otherwise, a repair that looks fine cosmetically may in fact have durability and corrosion-related concerns, as well as less occupant safety should another accident occur in the future.
Need More Info About Using Adhesives? |
|
![]() The STAR Tek Info website is the official Mercedes-Benz USA LLC (MBUSA) site for hosting service and repair technical documentation, bulletins, recommended tools and equipment, training, and other resources for Mercedes-Benz vehicles. Visit www.startekinfo.com for more information. |
![]()
|
![]() Finally, Mercedes-Benz provides access to archived StarTuned Magazine articles to collision professionals at https://automotivetechinfo.com/mbst/, a website that allows repairers to search by year and date. For more information, use this link to access two earlier articles pertaining to the use of adhesives in collision repair — When Welding Won’t Do (May 2010) and Taking Stock in Bonds (December 2008). [UPDATE: All Mercedes-Benz StarTuned archives are available here, on StarTuned.com]  Â
|
An adhesive repair example: Rivet-bonding
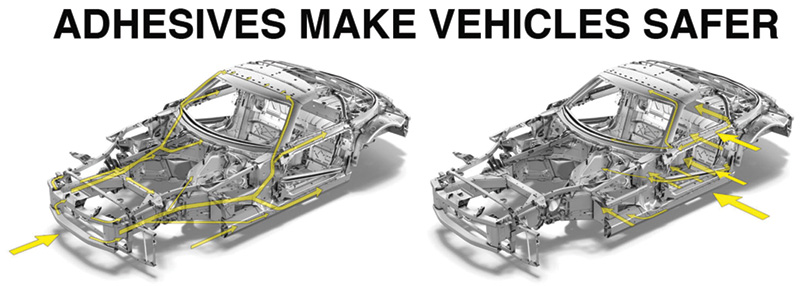
Chemical bonding using adhesives (illustrated in the SLS AMG diagrams above) helps keep the absorption of energy forces during a crash truer to designed load paths. The basic principle is to ensure that the joining of adherents, at manufacture or after a collision repair, remains stronger than the adherents themselves, so that the latter absorbs most of the unwanted crash energy, while the adhesive itself only absorbs a very small portion of this energy.
(Image — MBUSA)
New vehicle construction techniques mean new procedures in collision repair to maintain the integrity of a vehicle in the case of any following accidents. Specific year/model repair instructions can be found at the subscription-based StarTekInfo.com website. Be sure to refer to it and other MBUSA resources before beginning any repair.
For example, the new aluminum-body CL-Class uses aluminum panels as part of its load bearing structure. Outer body panels are constructed from aluminum, magnesium, and composite compounds. Aluminum is used for the roof, outer door panels, rear quarter panel, hood, and more. These new materials, such as load-bearing aluminum body panels, offer advantages. However, in many cases, standard welding methods cannot be used to join materials. Where welding is not approved for the repair, chemical bonding provides a viable alternative. In some cases, Mercedes-Benz requires a combination of riveting and bonding agents to maintain chassis strength.
Let’s consider a repair example where rivet-bonding is required. Here are some key considerations when making the repair:
Know the composition — Technicians must be aware of what they are going to cut into before doing so. MBcollisioncenters.com provides critical information regarding the construction of vehicle parts and components. For example, various body panels on new models — roof, hood, quarter, door, etc. — may be constructed of magnesium, aluminum, high-strength steels, and even carbon fiber composites.
Use the approved attachment methods, be it replacement, welding of some type, or chemical bonding with adhesives — Attaching vehicle parts that are of two different materials should only be done if approved by Mercedes-Benz using the repair procedures the automaker specifies. The StarTekInfo.com website is the best resource for specific information, especially the procedures laid out in the Workshop Information Systems (WIS). Different grades of carbon fiber material require different chemical bonding procedures and/or agents. In addition, should dissimilar metals such as steel and aluminum be joined, it is critical that repairers avoid any cross contamination by working on the separate metals in different areas and with different tools. In addition, repair procedures such as rivet-bonding may be required rather than welding, as the latter could deform the metals and the interaction between the metals may lead to premature corrosion beneath repainted finishes.
Source quality parts, fasteners and adhesives — When fastening body panels together, the use of proper fasteners is paramount. To rivet-bond aluminum, be sure to utilize aluminum rivets; to fasten steel panels, use steel rivets. Also, ensure that the rivet gun being used is strong enough for the job. Body panels, other parts, rivets and adhesives are available from Mercedes-Benz or aftermarket suppliers. Because aftermarket suppliers may not be as thoroughly versed in Mercedes-Benz vehicles — remember, it’s your responsibility to make the full, correct repair — be sure to ask what the specific steel grades of the rivets and body panels are, and also whether or not any adhesives or other supplies you purchase meet MBUSA requirements.
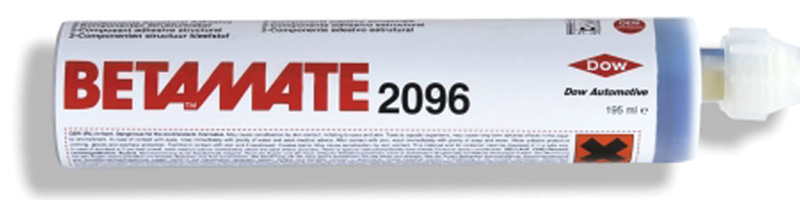
The adhesive kit Betamate 2096 from Dow Automotive Systems is now available (Part # A 009 989 36 71) and must be used for the repair procedures described in all WIS which require body adhesive. The structural adhesive must also be applied using the adhesive dispensing/metering gun for 2-component adhesives (Part # W 220 589 03 63 00). In some cases, Zinc Dust Paint (Part # A 000 986 36 42) may be required tp prevent corrosion. (Image — MBUSA)
Cleanliness is essential — Clean surfaces are required for proper bonding, just as they are for welding. It is also important that bare metal be bonded to bare metal and not painted surfaces. Repairers may need to grind a body panel down to bare metal by removing enough of the corrosion inhibitor layer to expose sufficient bare metal to assure a thorough bonding. Finally, if rivet-bonding is to be employed, be sure to bevel the drill holes so that panels can be compressed snugly together.
Be cautious during adhesive application final assembly — Use only MBUSA-approved adhesive kit formulations that have been matched to the automaker’s materials, so that collision repairs can meet the original safety specifications. Repairers should ensure that they understand application instructions before using the adhesive, so that the limited available working time is not wasted. Once the application is complete, clamp the body panel(s) into proper position.
Complete final assembly — Before the final assembly, ensure that the new panel aligns properly to where it will be attached. In addition, check for gaps. Mercedes-Benz says that if a panel needs to be repositioned, repairers should slide the panel into proper position rather than lift it. Lifting the panel separates the bonding material and allows the intrusion of air bubbles into the bonding material, which can compromise the quality of the repair. Once the panel is in its final position, remove any excess material visible to the eye. Refer to the adhesive kit’s instructions for curing time, which can range from one to 24 hours. Once cured, install the proper rivets and ensure they are fully covered. At this point, the rivet bonding process is complete. The repair is then ready for undercoating and painting.
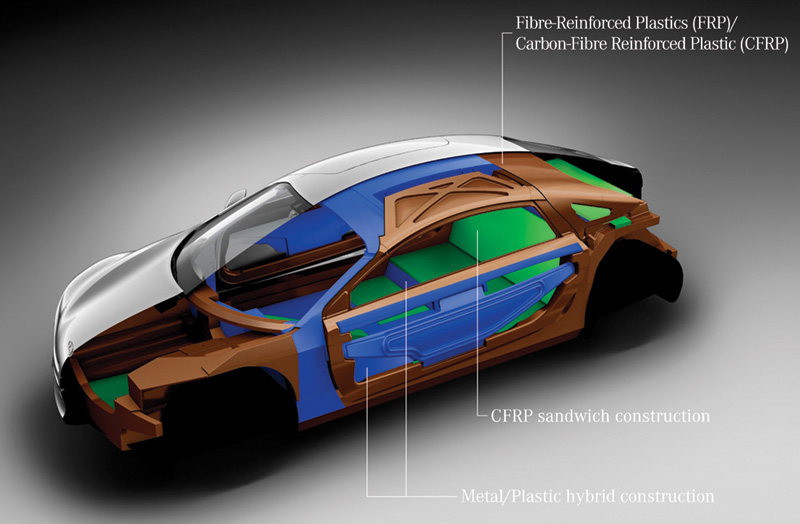
Mercedes-Benz says that 14 percent of all new developments relate to lightweight construction materials and production processes, such as new uses of carbon fiber-reinforced plastics, lightweight steels and metal alloys as well as other materials and processes. The automaker’s new F125 concept employs many of these innovations, which result in a 40 percent reduction in bodyshell weight, compared to current series production models. For example, the front flexural and supporting structure is a load-bearing assembly of hybrid aluminum-carbon fiber reinforced plastic sandwich construction. (Image — MBUSA)
Chemical bonding adhesives are ideally suited to modern vehicle bodywork repairs when high-strength metals, plastics, carbon fiber, and emerging composites are present. When compared to alternative joining technologies for current lightweight materials, modern two-component adhesive formulations and repair procedures allow all the properties of the body panel components to be returned almost, if not exactly, to their original state — namely improved surface bonding, more effective management of stresses, better mechanical properties and more corrosion-resistance.
The quest for safer, lighter, and more efficient vehicles will continue to spark the introduction of innovative materials. Expect future improvements in adhesives to have an increasingly important role for this joining technology, during both manufacture and post-collision repair.
0 Comments