Turbocharging is a way to produce more power when needed, but still get small-displacement fuel economy. With the best of both worlds it’s becoming popular again. Let’s learn how to keep up the boost!
Turbocharging has been around for over a century — the idea goes back to the birth of the automobile. The supercharger was awarded a patent in 1885 and the turbocharger was patented in 1905. It was used in some cars, such as the Corvair, in the early 1960s, then fell out of popularity until interest revived in the late 1970s. Volkswagen has long seen the wisdom and efficiencies of getting big horsepower out of a small engine, so has been in the forefront of the recent turbo revival.
Priming the Pump
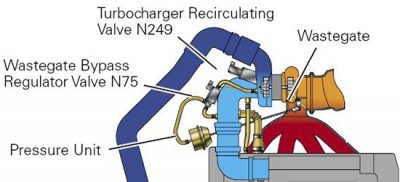
Picture an engine as an air pump. The more air you can pump through the engine the more power you will make. But the old saying, “There’s no substitute for cubic inches,†doesn’t necessarily apply when you factor in pressurizing the intake tract with a turbocharger. Volkswagen has been using turbos on its diesel engines for many years, but in 1998 put a 1.8L turbo gasoline engine in a Passat sedan and dubbed it the AEB engine. In 1999, the New Beetle got the 1.8 liter APH turbo, and in 2000 the Jetta, Golf, and GTI were next with the turbo option. In 2005, the 2.0L TFSI® engine was being phased into most Volkswagen models. As a result, there are quite a few turbo models that are going to eventually need work. So, you’ll need a solid understanding of how turbo work and what special problems crop up with wear and tear. Due to the nature of turbocharging, there are differences in diagnosing drivability troubles, and some other, different symptoms that may occur. Be prepared.
The Basics
Turbocharging is actually a form of supercharging. Supercharging simply means intake air is pressurized and forced into the engine. A supercharger uses the mechanical energy of the crankshaft to turn a high-volume air pump, the output of which is ducted to the intake manifold. This can provide a significant horsepower gain, but some of this horsepower is lost in running the pump. A turbocharger, on the other hand, uses the exiting waste exhaust energy to spin a turbine shaft at high rpm. This shaft is attached to an impeller that compresses the intake air. Since more air is being pumped into and out of the engine, more power is produced than if the same engine were what’s called “normally aspirated,†meaning it relies on atmospheric pressure alone to fill its cylinders. Since a turbo relies on exiting exhaust to spin the turbine, it is more effective at high rpm where there is plenty of exhaust gas. At low rpm, a turbo is not spinning as fast so it pumps less air. As the engine is accelerated, you may notice what is referred to “turbo lag†— the time it takes for the turbine to “spool up†and start producing significant boost.
Boost Control
Engineers have come up with ways to help reduce turbo lag. A smaller turbo can be fitted, which will spool up faster, but will add less ultimate horsepower than a larger one. To help reduce the lag effect, yet still get maximum horsepower, Volkswagen has come up with an optimal design. The turbo is designed to always produce enough boost throughout the rpm range.
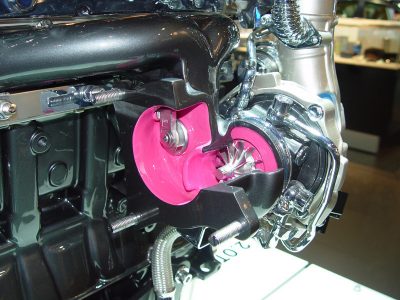
There is the possibility that a turbocharged engine can go into “over-boost!†This is very dangerous for an engine’s internals because too much compression is created in the combustion chamber. Just as in a diesel engine (with very high compression), the fuel/air mixture may ignite from the pressure alone, and not when the spark fires it. This is known as pre-ignition or detonation and can cause severe engine damage as well as poor engine performance. So, the amount of boost in the intake must be accurately controlled. In the event the engine is making too much boost, a waste-gate bypass regulator valve allows the excessive pressure to open the waste-gate actuator.
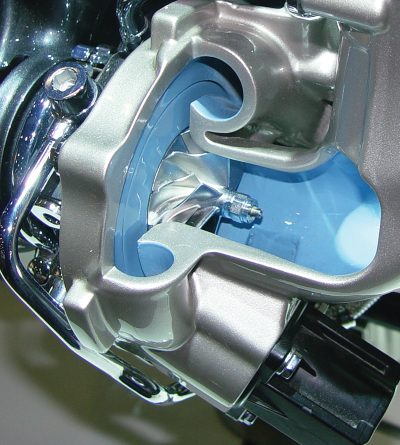
As the pressure builds in this actuator, it pushes on a rod that is connected to a flap on the exhaust side of the turbo. This flap opens an exhaust “bypass†valve allowing the gasses to bypass the turbine and exit directly out of the exhaust. By bypassing the turbine, the impeller is now spinning at a slower, safer speed. The waste-gate bypass regulator valve is always open allowing boost pressure to actuate the waste-gate and produce less boost. If the Motronic control unit wants to increase boost, such as during rapid acceleration, it can pulse the solenoid closed and restrict boost pressure to the waste-gate. This keeps the waste-gate closed longer and exhaust pressure continues to speed up the turbine, producing more boost.
Lag Drag
While under hard acceleration, maximum boost is produced. If the driver suddenly gets off the throttle, backpressure increases in the exhaust side of the turbo. This backpressure also serves to reduce the output of the turbo by slowing down the impeller. If the driver wants to accelerate again, he or she will have to wait for boost pressure to build up, once again experiencing turbo-lag. To prevent this from happening, Volkswagen AXX-series engines have a Charge Pressure Bypass Valve. This valve redirects the pressurized air coming out of the turbo back into the intake air stream before the turbo. The turbo is still spinning fast enough to produce boost, it is just directed to the low pressure air intake side of the turbo. This allows the turbine to keep its speed up in case the throttle is applied rapidly again and boost needs to be made quickly. The bypass valve is held open by manifold vacuum at idle and under rapid deceleration. Under boost, the valve closes keeping pressurized air in the intake system. When the driver decelerates the manifold vacuum opens the valve again allowing pressurized air to recycle back into the inlet side of the turbo’s intake system. On early AXX engines, a solenoid mounted on the intake tube could block the boost pressure that is being directed to the bypass valve if the PCM commands it.
On later 2.0 liter TFSI® turbo engines, the bypass valve is built right into the intake side of the turbo and is called the Turbocharging Recirculating Valve, but is sometimes referred to as the Divert Air Valve. The principle is the same just with a few less components. The PCM controls the recirculating valve electrically. It grounds the valve under deceleration to open it, and releases the ground to allow it to close. This valve opens and returns the pressurized air to the intake stream.
Troubleshooting
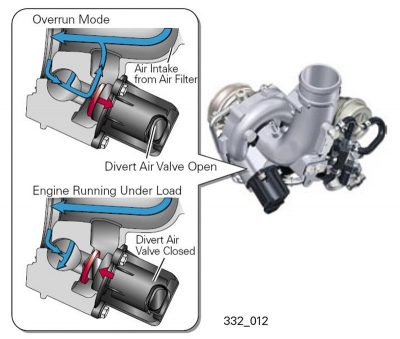
Turbocharged engines are also just engines underneath, and can have the same drivability symptoms as any other vehicle. Proper valve timing, fuel pressure and exhaust flow still need to be verified. If you feel you cannot tell if it is a turbo-related problem, then simply eliminate the turbocharger. Manually open the waste-gate. You should operate the waste-gate anyway just to verify that it is not sticking and moves freely. The engine should now perform as a normally-aspirated engine, it just will not make as much power. If you still have a hesitation or stumble, the cause is not in the turbo system. Remember, a seized turbo can result in an exhaust system blockage that will restrict air flow through the engine. You should always perform a visual inspection of the air intake hoses, clamps, and, of course, the turbo itself. Make sure the shaft spins freely and you do not feel any play or resistance. Turbos can spin upwards of 100,000 rpm, so there is no room for error.
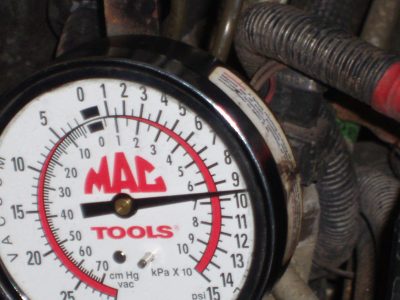
When diagnosing a drivability problem with a turbo engine, realize that there are a few more components in the system so there are also a few more tests to be performed. For instance, you should always measure manifold vacuum to verify that the mechanical side of things is in order. With a normally-aspirated engine under heavy acceleration, vacuum should drop to near zero as the open throttle plate allows atmospheric pressure to enter the intake manifold. However, under acceleration a turbo should be producing pressure or boost. First “T†into a vacuum line with a pressure gauge and, either on a dynamometer or during a road test, watch how much pressure builds (on the road, it is always safer to have someone else assist you and drive the vehicle). This way you can focus your attention on reading the boost pressure gauge. If your road test involves going up a hill, that will offer an additional load that should increase boost output to maximum capacity. Limit each test run to 10 seconds. See how much boost you can make. You can also use a VAG 1397 or equivalent to measure boost pressure. You should normally see 20 to 24 psi. Any higher or lower and there may be a problem.
Lower than normal pressure means you either have a leak in the system, or you simply have a turbo that is not up to the task. Leaks can be tricky to diagnose. If the leak is present all the time, then there will also be an air leak after the Mass Air Flow sensor. This will probably also lead to fuel trim and idle control issues (“false airâ€). You can use a smoke machine to find the source of the leak. Volkswagen also makes available an engine leak detection spray, Part # G 001 800 A1. This spray will help you find vacuum leaks by decreasing the ignition quality of the mixture it has leaked into. You can also use a generic scan tool to perform this test. On a VAG 5052 you enter into address word 33 (aka Generic OBD II). Select “Check Measured Values,†or “Live Data†and look at PIDs 06 Short-Term Fuel Correction and 12 Engine RPM. As you spray around the air intake system watch both PIDs for changes in value. The rpm should drop and the short-term fuel trim should move further away from 0%. In the past, you may have been instructed to do this test with carburetor cleaner, but it is combustible and is a dangerous fire hazard.
Losing Boost
Due to the stiffness of air intake boots, the leak may only be present under boost conditions. That is to say, as pressure builds up in the intake manifold it may force open a crack in a hose. Once the pressure has dropped, the hose reforms into its original shape and reseals itself. At idle there is not enough airflow through this cracked hose to have an effect. With little to no load on the engine at idle, it is almost impossible to generate enough boost while in park. If you are working on a 2.0 liter TFSI® (BPY) engine), you can use special service tool VAG 1687, which has an adapter that allows you to seal the intake system. You can then set the tool to .5 bar (7.35psi) and listen for leaks, use a leak detection spray, or a VAG 1842. Do not pressurize the intake system higher than .5 bar or engine damage may occur. Since at some point an intake valve is open in the engine the pressure will eventually bleed down, so don’t be alarmed. Typically, if you have a boost leak the engine will run rich under the boost condition as the air is being lost, but extra fuel is still being injected. You may come up with fuel system rich codes in the computer’s self-diagnostic system.
A good understanding of Volkswagen’s turbo systems will help you provide faster and more accurate diagnosis. Look at the turbo’s boost ability, the waste-gate and solenoid to verify you are getting the correct amount of boost. Under deceleration and idle, verify that the bypass valve system can open and close properly. Check the intake system for leaks that can alter the performance potential of the engine and you will have a satisfied customer.
Download PDF
0 Comments