Carbon fiber parts will be in certain 2012 Mercedes-Benz production series vehicles
Lightweight vehicle construction continues to be the Holy Grail for leading automakers such as Mercedes-Benz. Driven by environmental, economic, and other considerations, the reduction of vehicle mass is achieved by choosing from a spectrum of lighter materials. The recent shift to lighter and stronger steels and alloys illustrates this. But just as the collision repair industry has begun to adapt from mild steels to higher-strength varieties, there is a new wave of lighter and stronger materials inbound for mainstream automobiles — carbon fiber reinforced plastics (CFRP). Now is the time to ready yourself and your business for the coming changes.
Carbon fiber is not just coming sometime; for Mercedes-Benz, it is already here
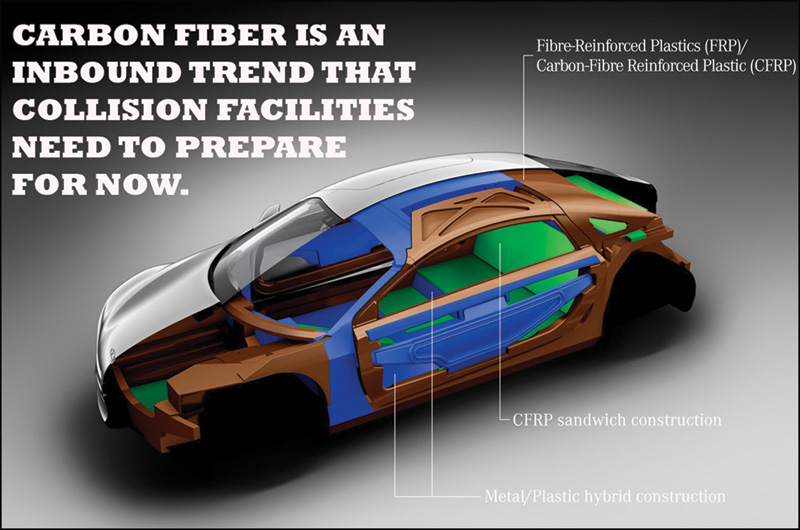
Lightweight Construction Via An Intelligent Vehicle Material Mix
By incorporating a mix of lighter-weight materials — higher-strength steels and alloys, fiber-reinforced plastics (FRP), carbon fiber reinforced plastics (CFRPs) — it was possible to reduce the bodyshell weight of the Mercedes-Benz F 125 concept by 550 pounds. But the high CFRP content (body parts and structural components) isn’t just futuristic dreaming. CFRP parts and components are now in MY2102 vehicles, such as the SLK, CL, CLS, and other models.
Lightweight construction is an integral part of Daimler’s growth strategy toward sustainable mobility, occupant safety, improved fuel efficiency, and reduced exhaust emissions. According to Dr. Dieter Zetsche, chairman of the board of management of Daimler AG (parent of Mercedes-Benz), the company has set a specific development goal of reducing the body-in-white weight for all Mercedes-Benz vehicles by up to 10 percent, when compared with the immediately preceding versions.
This weight-saving initiative will partially offset any increase in weight caused by additional safety and comfort features, or new technologies used in alternative drive systems, or required by regulators. Furthermore, CFRP parts contribute to an increased stiffness of the vehicle body, thereby further increasing the crash integrity of the passenger cell as well as the safety and comfort of vehicle occupants.
Beyond using CFRP parts in Formula 1 racing, Mercedes-Benz demonstrated its CFRP for production-series vehicles over a decade ago with its SLR model. With thousands produced, Mercedes-Benz has put more vehicles with CFRP materials on the road than any other automaker, and demonstrated that CFRP meets the most stringent safety and performance requirements.
In the years since, Mercedes-Benz has worked intensively on the advanced development of CFRP, with the objective of reducing costs so as to enable a broad-scale production-series rollout of the technology. For example, at the automaker’s recent Tech Day event, plans to actively adopt CFRP parts and increase the number of models using such parts were shared.
“Daimler will be investing in the expansion of its production network, continuing its product offensive and intensifying the development of new technologies,†stated Zetsche. “This includes a joint venture between Daimler AG and Toray Industries Inc. to produce and market automotive parts made of carbon fiber.â€
Under this agreement, Toray will utilize its proprietary short-cycle Resin Transfer Molding process technology — which enables the mass-production of CFRP parts with a significantly shorter molding cycle — to develop optimized CFRP parts and components for Daimler’s brands. Daimler’s role will include designing CFRP parts and components, as well as developing joining technologies and procedures. “We intend to start supplying these mass-produced CFRP parts for more production series Mercedes-Benz passenger vehicles that will be launched in 2012,†Zetsche emphasized.
What is a CFRP composite?
Jason Bartanen, technical director for I-CAR agrees that shops and technicians need to prepare now for CFRP. “We’re certainly starting to see a lot more carbon fiber applications in production-series vehicles, such as hoods, roofs, body panels, other parts and structural components. We’re going to see even more CFRP in the years ahead.â€
Bartanen shared that the advent of CFRP in everyday vehicles was one of the factors that prompted I-CAR to develop a working relationship with Abaris Inc., a firm with CFRP repair expertise in several industries. The goal is to begin providing CFRP-themed collision repair education to the industry.
Recently, StarTuned had the opportunity to visit with Bartanen, who introduced us to Jay Carpenter, the technical instructor for Abaris Training Resources Inc. His experience ranges from concrete to automobiles (his personal passion) to aerospace to developing CFRP parts that are on the Hubble space telescope.
“CFRP are composite materials,†said Carpenter. “They consist of are a combination of two or more materials — a matrix and some reinforcing element.†He used reinforced concrete as an easy-to-understand example of a composite. “Cement is the matrix material, while rebar provides the reinforcement. Together, the composite is stronger, safer and opens up a wider range of applications for the construction industry.â€
Likewise, fiber composites are also a combination of different materials. They combine resin as a matrix together with some reinforcing fiber. “For fiber composites, the woven fibers carry the load; the weave is effective at handling tension, torsion, shear and compression stresses, but they do not handle heat and fire well,†Carpenter explained. “The resin system encapsulates the fiber, resists moisture, maintains the shape and also offers some resistance to compression stress.â€
Physical properties, such as weight, strength, stress resistance, etc. vary depending on the quality of resins and type of reinforcing fiber used. “But the composite ingredients themselves — both resin and fiber types — do not care where they are or what they’re doing,†adds Carpenter. “They are going to perform to their design specifications where and when a quality repair process is employed.
CFRP collision repair basics
Matrix materials are available in three categories — polyesters, vinyl esters and epoxies. “While each might be able to be used for a specific CFRP repair, think toward high-end quality epoxies when working with CFRP,†Carpenter suggested.
“Unlike low-end polyester and vinyl ester resins, epoxies provide a stronger molecular link and better adhesion, which results in a higher-value vehicle repair,†he continued. “Epoxies utilize a hardener, rather than a catalyst, which allows more flexible and precise cure times, ranging from minutes to years. To me, it makes zero sense to take a high-end fiber and blend it with a low-end resin, such as polyesters or vinyl esters, because any compromise of the quality of your repair to save a few bucks might come back to haunt you down the road.â€
There are three primary classes of fiber composites used in collision repair:
- Fiberglass is the weakest and least-expensive type of fiber composite. It consists of a plastic matrix reinforced by fine fibers of glass. Fiberglass composites are sensitive to alkaline environments.
- Aramid fiber is a more expensive, but stronger, class of composites. Aramid has a much tighter weave than fiberglass, which in itself adds strength, but when combined with resin forms a stronger and more solid-feeling composite. Aramid can corrode if exposed to chlorine.
- Carbon fiber is stronger and more expensive than Aramid. Thermal manufacturing processes evaporate non-carbon constituents of a raw polymer leaving a fiber that is typically 93 to 95 percent carbon. Note that carbon fiber can exhibit galvanic corrosion in the presence of carbon steel or aluminum.
Different CFRP composites have unique structural properties and temperature tolerance. Besides outright replacement with a new CFRP part, two other repair options are using pre-impregnated (prepeg) fabrics, or “wet resin systems.â€Â
- Although more expensive, the use of prepeg CFRPs provide technicians with more control, as they contain resins that have been applied in a very uniform and controlled manner that achieves the optimal fiber-to-resin ratio. In addition, prepeg materials require controlled storage — typically freezers — to hold and retard the resins’ natural propensity to advance.
- Repairers desiring a more economical option might employ a wet resin system, wherein they buy the raw fiber materials in rolls and resins in five-gallon pails, then apply the resins themselves. Using a good, readily available wet resin system and sound repair procedures, repairers can effect complete, safe repairs, but doing so requires sound technique to ensure the optimum and critical fiber-to-resin ratio is achieved to match the application.
“When trying to understand the fiber-to-resin ratio, think of achieving the optimal ratio as the Goldilocks effect,†Carpenter suggests. “If the composite has too much resin, then the composite will be heavier and more brittle than desired. If there is too much fiber content, then the composite will be prone to coming apart more easily, especially under compression, tension, or torsion stresses that can occur in an accident.â€
To provide customers with a complete, safe, and lasting repair, Bartanen and Carpenter both agree that technicians should use quality resources from the vehicle manufacturer to determine which of three repair paths are approved and recommended. For instance, technicians must know when and where:
- OEM-approved CFRP replacement parts, assemblies, or components are required.
- Prepeg CFRP products and procedures are approved.
- Using a wet resin system is permitted.
For Mercedes-Benz vehicles, collision professionals can use the StarTekInfo website (www.startekinfo.com) to access service information and procedures, approved parts, tools, and supplies, as well as training details and other resources through traditional Mercedes-Benz channels.
For example, before beginning a repair, technicians should be trained in the use of ultrasonics to detect the presence of delamination or extent of other hidden damage to CFRP parts and components. As another example, an automaker knows the design and composition of its CFRP parts and will require certain resins and procedures to effect repair. Those who rely on non-genuine sources for critical repair information and procedures, if proven to be incorrect or out-of-date, could face expensive consequences.
Preparing now will provide opportunities sooner than many realize
Expect MY2012 SLK, CL, CLS, and other models with CFRP to soon begin arriving at your collision facility. CFRP content will migrate into less-expensive models by 2020.
There is a gulf of knowledge between the general perception of CFRP and the hard-earned expertise of those who deal with CFRP regularly, most of whom work in other industries, or in motorsports. For insurers, CFRP will become more common as new production capacity comes on-stream and is applied to mainstream vehicles. Many initial applications will be bolted or riveted single panels, but future applications will include sub-frames and body structure subassemblies. Those insurers who recognize that CFRP repair is specialized, but far from impossible, should begin today to secure CFRP-ready repair facilities in order to reduce waste as well as cost.
For mainstream collision facilities, understanding the complexity and limitations of new CFRP materials is critical. To achieve this, begin seeking access to CFRP-related information and training to develop CFRP repair expertise. Those collision facilities and professionals who plan and prepare early for CFRP — like Mercedes-Benz did while other automakers did not — will be better positioned to seize opportunities than their more cautious competitors. Adopting and adapting to innovation is a matter of choice. In the case of CFRP, that choice is yours to make. Just know that time, like opportunity, moves on.Â
Like Steels, There are Many Grades of CFRPJust as various high-strength steels and alloys are suitable for certain applications and not others, CFRPs also come in various grades designed to fit certain applications. For example, the highest-strength grade may not be suitable where controlled crush in a collision is the goal. Mercedes-Benz engineers choose among the grades on the basis of suitability, not cost. The type of weave — the number of fibers and type of repeating weave pattern — that a CFRP fabric has affects the strength, flexibility, and other attributes of a structural component, part, or repair. The 2 x 2 Twill Weave (left) has two-CFRP fiber pairs that are woven at a 90-degree angle over two other pairs, then under the next two pairs, and so on. Note how the weave in adjacent rows is offset. This weave will easily conform or drape to complex shapes, but is not the strongest type. Where more strength is needed, the Eight Harness Satin Weave (right) is available. This pattern has fibers that are woven under one and then over seven fibers that run in the perpendicular direction, repeated across the breadth of the fabric. Like the Twill, each neighboring fiber’s weave is offset by one space. In addition, the Eight Harness Satin Weave has less void space, which therefore requires less resin to fill for a quality repair that does not compromise strength, stress-resistance or load-carrying capacity. (Images — Twill Weave/Mercedes-Benz; Harness Weave/Abaris Inc.) |
Â
0 Comments