Nissan’s all-electric LEAF incorporates both new and existing technologies. This article will familiarize readers with the unique features and design of this car, and provide insight into its expected maintenance and service needs in the future.
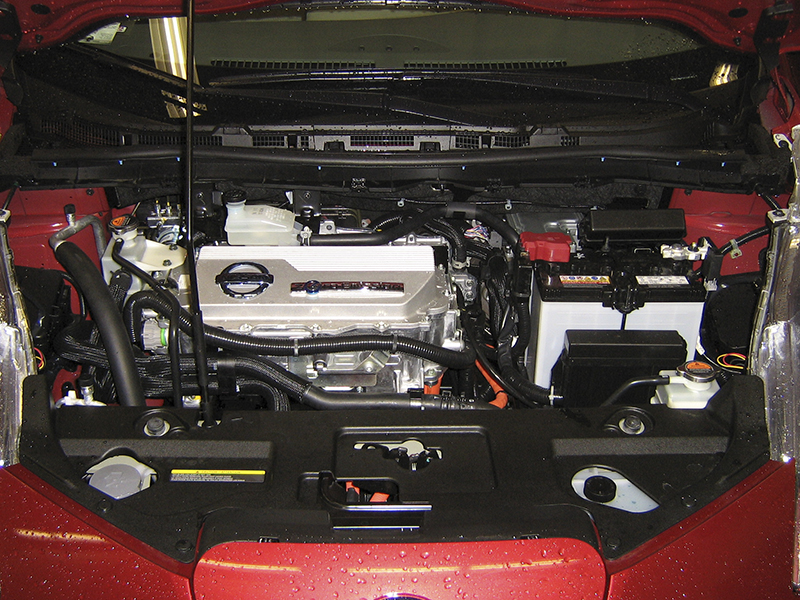
The stylish faux valve cover is set on top of the inverter unit and creates a traditional engine bay appearance.
The LEAF was introduced in 2011 as Nissan’s pioneer vehicle for the future of electric cars. It has a distinctive body design not based on any other platform in the Nissan fleet, giving it a road presence unlike any other compact car. Prominent LED headlights and a long LED cluster tail light, coupled with blue-chrome accents make the LEAF impossible to confuse with other vehicles. Plus, once you pop the hood, nearly the only thing that looks normal is the faux “valve cover.†Let’s take a closer look at the features of the new LEAF to try to strip away some of the mystery.
Overview
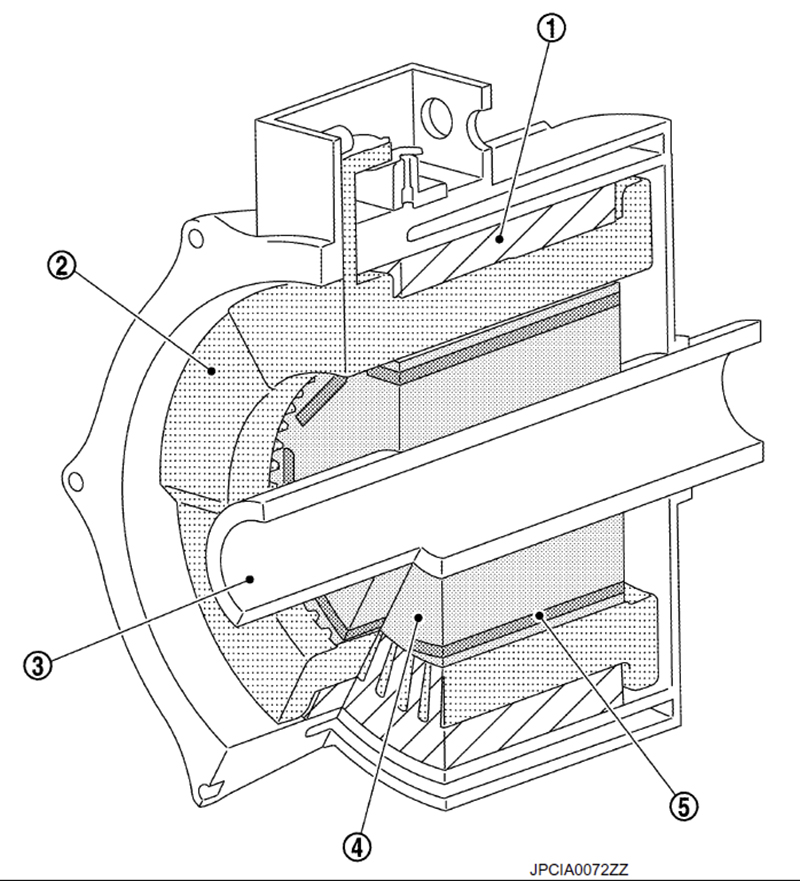
The traction motor consists of the stator core (1), coil windings (2), output shaft (3), rotor core (4) and permanent magnet (5).
The LEAF is a front-wheel drive car, utilizing an all-electric three-phase traction motor and reduction gear to drive the CV axles. The motor gets its power from a lithium-ion battery pack composed of 48 modules in series, each containing four cells laid flat to produce a total of 403V. A water-cooled inverter changes battery power as necessary from DC to AC to drive the motor, and, likewise, from motor-generated AC (from regenerative braking) to DC to charge the battery pack. Regenerative battery charging is achieved by converting the kinetic energy of the already moving car into power through induction within the traction motor. The suspension is independent MacPherson struts in the front, and a solid I-beam in the rear with shocks. Steering input is rack and pinion, with an electronically-controlled electric power steering rack. It’s equipped with standard ABS using front-wheel discs and rear drums. Vehicle Dynamic Control (VDC) is standard, and enhances safety and handling.
The instrument panel has two separate displays for the driver, showcasing unique LED styling for electric power consumption, and Nissan’s usual dot-matrix information screen. An integrated navigation unit comes standard, using GPS and telematics to show the vehicle’s estimated range and nearby quick charge locations.
Powertrain
The first description of the LEAF is invariably that it’s “an electric car,†so we should begin with how it works without an internal combustion engine.
The traction motor takes the place of a conventional engine, and generates torque from precisely-controlled electromagnetic fields. The motor is basically two primary components: the permanent magnet rotor, and the coil windings of the stator. Information about temperature or speed sensor locations, cooling tubes, and high-voltage connections, or other specific components can be found in the service manual.
When three-phase AC current is applied to the stator coil windings, a controlled electromagnetic field is generated. This field pulls on the permanent magnet inside the rotor, causing the rotor to chase the generated field. The Vehicle Control Module (VCM) can create a constantly rotating electromagnetic field using a rotor position (angle) sensor, much as an internal combustion engine regulates ignition and fuel using crank and cam sensors. The torque generated by the electric motor is approximately proportional to the amperage of the current, whose frequency (or pulse timing) affects the rotational velocity. Current application is controlled by the VCM monitoring position with the traction motor resolver and current flow from a sensor within the motor.
Some DTCs (Diagnostic Trouble Codes) will limit the rotor rotational speed, the torque output of the motor, or both as a precaution. A P3240 “Drive Motor Current Control Malfunction†may set if the VCM does not see expected changes in current application due to sensor error or an internal problem. The LEAF requires a CONSULT-III PLUS for diagnosis and repair.
Like an internal combustion engine that performs differently according to changes in the intake charge and timing, an electric motor is dependent upon the frequency and amperage of the supplied current. It is the job of the VCM and the inverter to create the equivalent of an intake charge for the traction motor. It does this by adjusting voltage based on two calculated values: target force, and motor torque request signal. Because the resistance within the system is constant, changes in voltage affect amperage proportionally – think Ohm’s Law.
Target force is based upon sensor input from the accelerator pedal position, vehicle speed, and shift position. Other systems like ABS or VDC will send torque-down signals to the VCM to reduce motor torque output. Once determined, the VCM will command the inverter to convert DC from the battery pack into AC of the specific amperage (torque) and frequency (rotational speed). Thanks to thermodynamics, this conversion work also generates heat which is transferred into the cooling system and dissipated by the radiator in a traditional manner.
The LEAF also charges the battery by working in the reverse of the above method. Instead of creating synchronous electromagnetic fields, during regeneration the outer field is maintained stationary. The rotor magnet moves through the field creating a current flow by the electrical property of induction. This AC current is captured by the inverter, converted to DC, and stored in the battery pack. The VCM performs the regenerative charge constantly at deceleration, effectively slowing the vehicle. In ECO mode, the LEAF will regenerate more aggressively; however, in both modes, when the battery is at the fully charged state, no regeneration is performed. This is to protect the battery from overcharging.
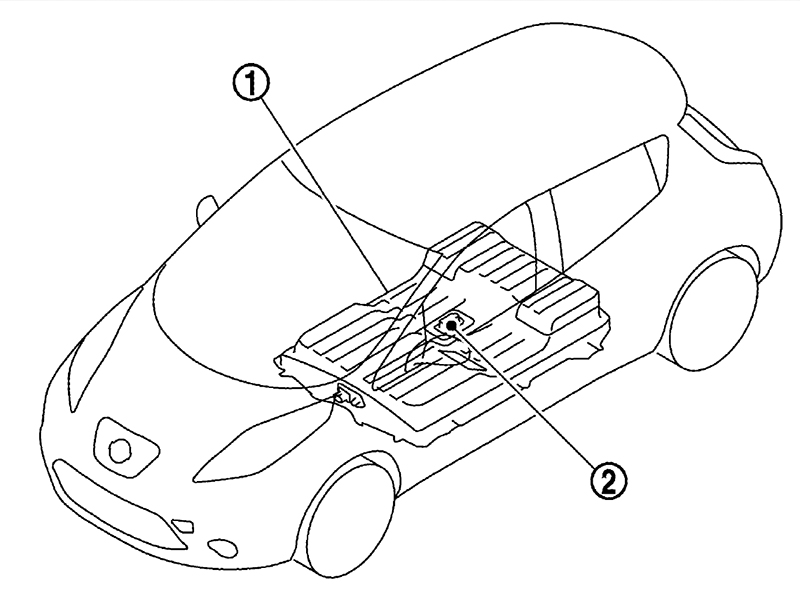
This diagram indicates the location of the 403V lithium-ion battery pack (1) and the service plug (2).
The heart of the powertrain is the 403V Li-Ion battery pack, arranged beneath the floor of the leaf. Every cell of the 48 modules is monitored, and the CONSULT-III PLUS can display many relevant PIDs for the battery pack, such as module voltages, total voltages, charging/discharging voltage differences, and the four battery temperature sensor signals. Yes, if there is a battery cell malfunction, a DTC will point directly at the problem cell. Considering the pack weighs a total 648 lbs., we should be thankful that any one of the modules can be replaced in the event of failure.
The LEAF comes standard with two ways of charging the battery pack at home using domestic AC. The “Normal Charge†method requires professional installation of a 240V source at home, and achieving a full charge will take approximately six hours. The “Trickle Charge†method will allow 120V household electricity to fully charge the battery in approximately 21 hours. The trickle charge method is not recommended for normal use according to the Owner’s Manual, but can be useful when at a friend’s house. This charging method may use power a bit erratically, charging and discharging capacitors for example, that may trip household breakers or cause other leaks to ground. Anecdotally, it appears that the trickle charge is not recommended due to its unreliability. Using the trickle charge method will not cause damage to the vehicle. It is best to follow Nissan’s recommendation.
An optional “Quick Charge†port can be installed in the LEAF, allowing a zero to 80% State of Charge (SOC) in about 30 minutes. These high-powered stations are available in some locations, and can be found using the LEAF’s navigational unit. However, repeated Quick Charging may shorten the lifespan of the battery pack.
Every 12 months, regardless of mileage, Nissan requires the annual Battery Usage Report for warranty purposes. This must be done with the CONSULT-III PLUS. We will discuss the report below in the maintenance section.
Transmission and Drivetrain
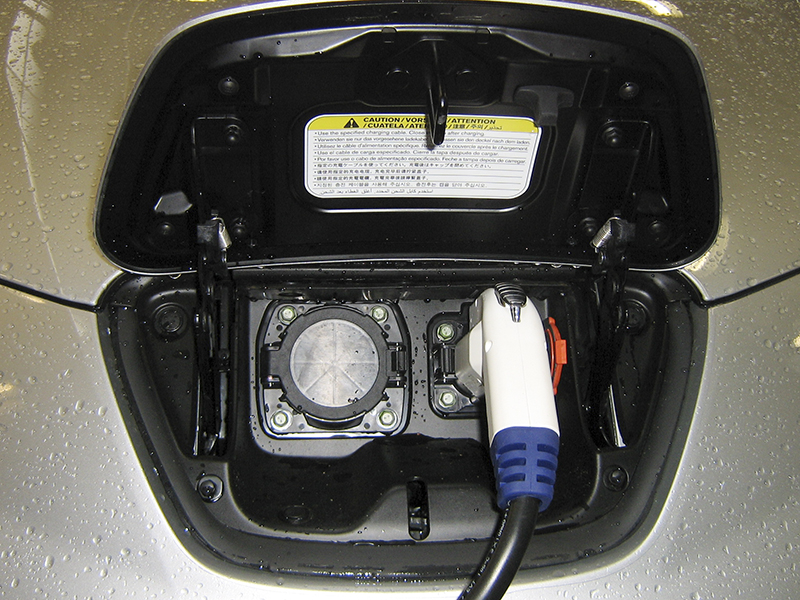
The port on the left is for quick charge. Shown here, the LEAF is using the shop’s 240V to get a little charge while in for service.
The LEAF does not have a CVT or planetary gear transmission, but rather a reduction gear that looks much like the gears in a shop roll-up gate. The electric motor output speed and torque can be precisely controlled so there is no need for a conventional transmission’s changing gear ratios. On top of the reduction gear housing is where the electronic brake actuator lives, and a parking pawl is found inside the case. The LEAF uses a unique parking feature, which can be set with a single button press on top of the shift lever. Once set, the BCM transmits the ON/OFF command to the electronic shift control module. The shift control module alerts the VCM of the signal, then commands the parking actuator to operate, which will lock and unlock the parking pawl appropriately. When it’s time to drive, the LEAF will automatically disengage the parking pawl without driver input so long as the driver seat belt buckle is engaged, the shift selector is in D/ECO or Reverse, and the accelerator pedal is pressed. The LEAF cannot be shifted while in OFF or ACC modes.
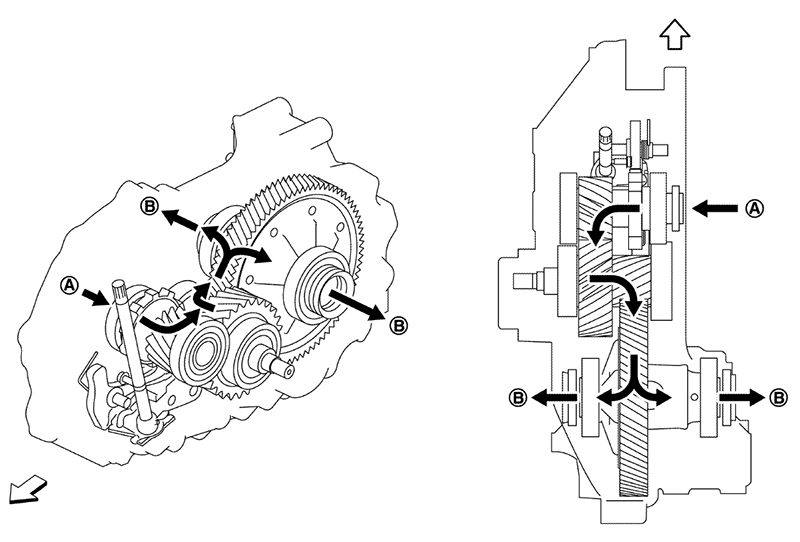
The RE1F61A reduction gear input gear has 17 teeth, connected to a 31-tooth main gear, which outputs through another 17-tooth gear to the large, 74-tooth final drive gear. The final gear ratio is 7.937. In this diagram, (A) indicates the power input direction and (B) indicates the power output flow.
The LEAF utilizes standard CV axles, so periodic inspection and repair of the boots as necessary will ensure long axle life.
Brake and Steering Systems
The basics of the LEAF’s brakes are what you already know and understand from many other vehicles: front disc brakes using hydraulic caliper pistons, and rear drums and shoes. However, Nissan introduces an electronically-driven Intelligent Brake Unit (IBU) that integrates the brake control module with the master cylinder and an electronic brake booster.
Because the VCM can switch the role of the traction motor into a generator when not accelerating, the LEAF must account for this behavior in braking. When you try to separate two magnets, it requires effort; the same force also occurs during the induction process within the electric motor, effectively slowing the vehicle down. This is called regenerative braking, and it can be used cooperatively with the friction brakes to stop the car. The VCM can measure the exact stopping power of the regeneration process by monitoring the AC generated – simply the inverse of how it calculates target motor speed and torque.
Here’s how the LEAF comes to a stop. First, the Stroke Sensor in the brake pedal assembly measures the pedal travel (driver input) and gives this information to the IBU control module. From this input, and with data from CAN communications about the vehicle speed, available cooperative regeneration slowing force, and wheel speed sensors, the VDC module calculates necessary fluid pressure for the friction brake components. This calculation is sent back to the IBU, where the electronic brake booster uses an internal motor to generate the commanded amount of fluid pressure within the brake master cylinder. Fluid pressure is then passed through the ABS actuator onward to the brake calipers and wheel cylinders.
In the event of an emergency power outage, the LEAF can still provide friction braking. The IBU fail-safe feature allows physical master cylinder control with the brake pedal. When the LEAF has no power, solenoids that would otherwise be energized default to a position that allows the pedal to directly interface with the master cylinder. For this reason, it is necessary to power off the LEAF during brake fluid flush maintenance in order to bleed the lines.
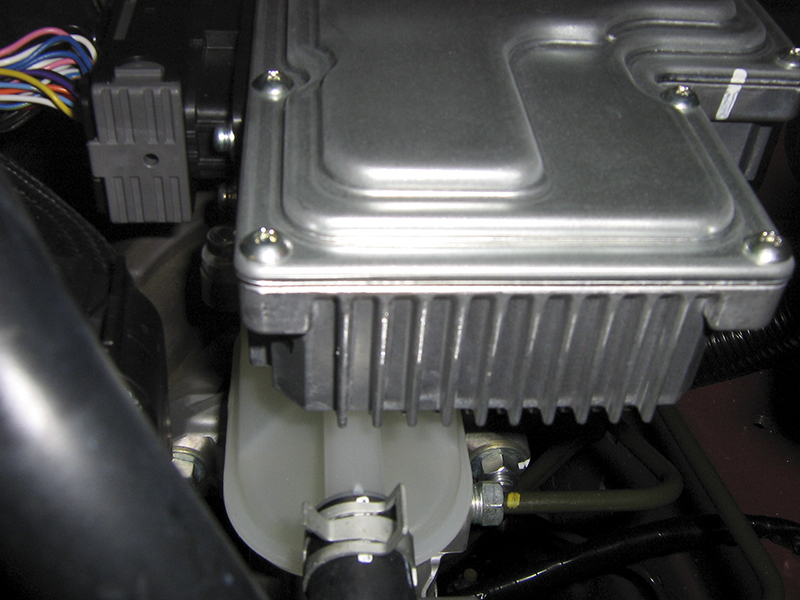
The Intelligent Brake Unit is not independently serviceable, but is monitored completely by the VCM and will report any malfunction using the MIL and dedicated bulb indicators.
The LEAF’s Electric Power Assist System (EPS) generates optimal power assist torque based on the load on the front wheels, steering wheel turning torque, and vehicle speed. The EPS unit is attached to the steering column, and its output shaft connects to a standard rack and pinion. During operation, sensors detect the motion and torque of the steering column (driver input) and the EPS module calculates the necessary assistive power using an electric motor within the EPS unit. Therefore, the motor can provide a varying amount of assist based on steering input: the greater the steering input, the greater the amount of current supplied to the EPS motor for assist. Since electricity is only required when assist is needed, the total draw on the Li-Ion battery is reduced. The EPS employs a reduction gear to properly transmit output torque into the rack assembly.
Diagnosis and repair of braking and steering systems must be done with the CONSULT-III PLUS. After component replacement, it is often necessary to indicate the change to the VCM. For example: a zero-point calibration can be performed for the EPS so the return-home position is learned.
Restraint System and Miscellaneous Accessories
The LEAF is equipped with many of the safety features modern consumers have come to expect: driver, passenger, side, and curtain air bags. The Supplemental Restraint Systems (SRS) are controlled in a conventional fashion, utilizing G-sensors, yaw sensors, and crash sensors to logically determine whether a crash has occurred, from what direction, and with what severity. Repairing the LEAF after a collision requires more diligence than normal due to the presence of high voltage. Follow the service manual guidelines for properly disabling 12V and high voltage prior to working on SRS components.
Air conditioning is controlled electronically by what Nissan terms the “A/C Auto Amp.†The electric A/C compressor uses high voltage input to power a three-phase motor in an identical manner to that of the main traction motor. The driver can determine his or her desired level of cooling, and the A/C Auto Amp will electronically control the A/C compressor speed to generate the target output temperature. Because the compressor can be controlled independently of engine speed, the system is inherently more efficient than a belt-driven unit on a conventional car. As the compressor draws power from the high-voltage battery, it will decrease the overall range of the LEAF and should be taken into account when discussing the Battery Usage Report. ECO mode will automatically decrease the power available to the A/C compressor.
An “alternator†is simulated by using an onboard DC to DC charger, which lives in the DC/DC junction box. The high-voltage battery pack will automatically supply power to charge the on-board 12V battery as necessary. When the vehicle is stored OFF for an extended time, the VCM will periodically charge the 12V battery for five minutes every few days. Nissan cautions LEAF owners not to leave the HV battery SOC above 80% when storing the vehicle as it can affect the longevity of the battery pack.
High-voltage components generate heat, which is handled using an aluminum core radiator and electric fans. Two electric water pumps are controlled by the VCM and set in series to operate together for redundancy. The VCM can control the amount of cooling by directly operating the water pump duty cycle. Sensors within the DC/DC junction box, traction motor, inverter, and on the battery modules will report operating temperatures to the VCM. Use only Nissan genuine pre-mixed coolant (blue), and never use stop-leak additives because they can damage the electrical components.
Maintenance and Driver Conveniences
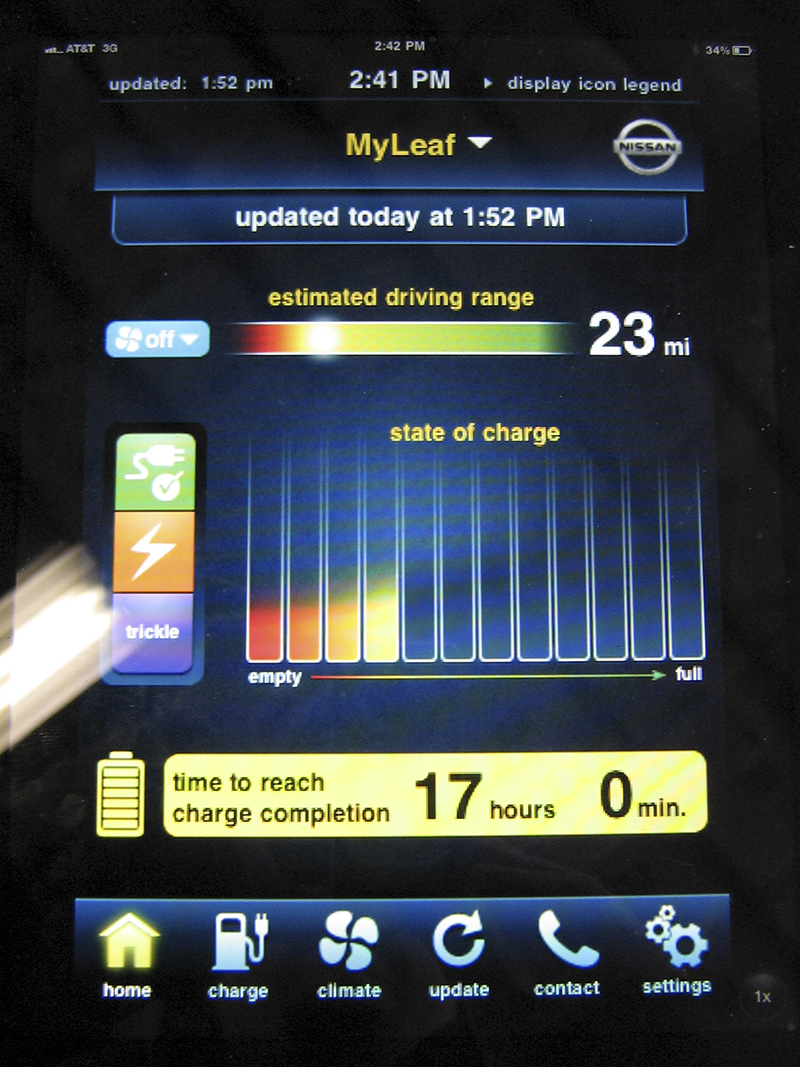
Communicate with the LEAF remotely using SMS on a cell phone, or the internet and a support device. Shown here is the Apple iPad app.
The LEAF is equipped with cellular telemetry for navigation, live updates, and remote control. This system is called CARWINGS. The telematics control unit (TCU) lives under the dash, near the right passenger kick panel. Nissan cautions service personnel who rely on cardiac pacemakers or other life-support systems to be mindful of the interference that the telematics antenna can cause. The LEAF is capable of using both Simple Message System (SMS; colloquially called text messaging) and internet connectivity to provide drivers with basic status information and bi-directional control of some systems. Once owners have registered their username and password, they can use a supported device such as an iPad to check battery SOC, control at-home charging, or even begin cabin conditioning using the HVAC.
Due to FCC controls and regulations, a unique VIN and International Mobile Equipment Identifier (IMEI) must be registered to any TCU. Therefore, it is not possible to perform diagnosis or repair with a known-good TCU or a recycled part. Furthermore, a replacement TCU can only be registered using the CONSULT-III PLUS after any replacement. The work support function provides the necessary registration steps.
CARWINGS will allow users to locate nearby charging stations while traveling without having to install GPS update DVDs. The navigation computer can be configured to approximate the vehicle’s range, and display quick charge stations if toggled.
A LEAF high-voltage Lithium Ion battery that is nearly discharged will begin to limit power distribution to the traction motor and A/C systems to increase range. The charge limitation indicator (“turtle lightâ€) will turn on to alert the driver that the LEAF will no longer accelerate at the same rate. The Owner’s Manual warranty supplement will include emergency contacts for road-side charging or towing. Towing a LEAF must be done with a flat-bed, or by trailing the rear wheels. If a LEAF is towed with the front wheels trailing, the traction motor may generate electricity and cause damage to the EV components.
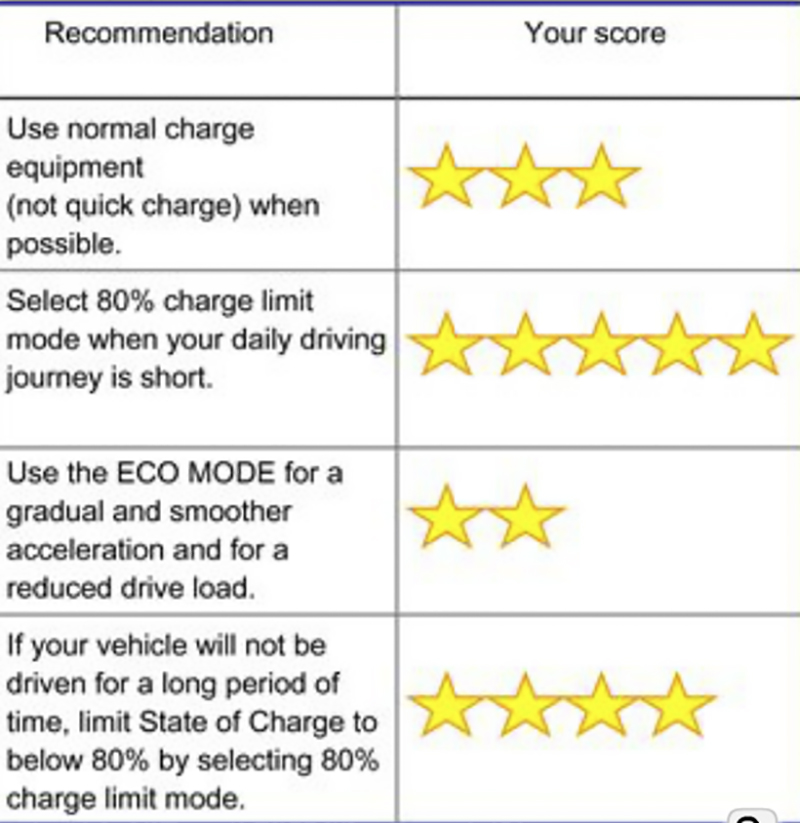
This LEAF driver may be a bit too aggressive in driving or usage habits. The Battery Usage Report can help your customers improve their range.
The LEAF still requires periodic maintenance. Nissan recommends changing the brake fluid and cabin filter every 15K, along with inspections. The reduction gear uses Nissan Matic-S for lubrication. Every 12 months regardless of mileage, the EV component warranty requires a Battery Usage Report. This report is generated on a CONSULT-III PLUS, under the maintenance section EV tab.
The Battery Usage Report is a table designed to illustrate the projected health of the battery under current usage. In the graphic, the driver does not stress the high-voltage battery with repeated quick charges, fast acceleration, frequent ACC-only “idling,†or continual use of the A/C. Nissan states that the HV battery is expected to perform at approximately 80% of its original performance after five years of average use. In other words, an owner who started out with 100-mile range should expect his or her range to be 80 miles after a few years.
Springtime for Electric Vehicles
The electric vehicle movement is gathering support and momentum, and will require an additional level of expertise. Shops that train and familiarize themselves with hybrid and electric vehicles will be able to retain their customers who eventually shift away from their conventional gasoline vehicles. The Nissan LEAF is very popular, and will show up in your shop. Will you be prepared?
0 Comments