Are you repair-ready for chemical bonding?
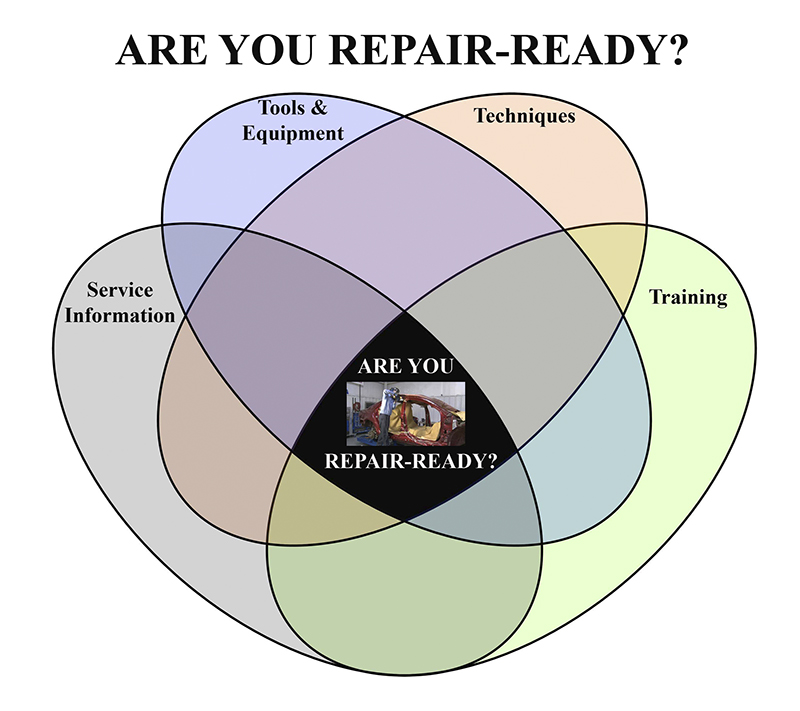
Collision professionals must remain current in the four key resource areas shown above. Only then can they be fully competent to perform complete, safe repairs for customers (courtesy ManicMedia LLC).
Hot on the heels of advanced high-strength steels and alloys, vehicle structures are now incorporating more thermoplastic, carbon fiber and other composite materials. The ongoing quest for lighter vehicle weight, performance without compromise, improved safety and lower manufacturing costs is driving the shift to these new materials. Nissan customers are already driving vehicles made in part from these new materials and more are on their way. Consequently, chemical bonding using structural adhesives is often the preferred and recommended joining method, rather than welding or riveting.
Professionals must ensure they are up-to-date with the latest service and repair information, invest in the required tooling, and seek effective training to learn and assimilate modern bonding-related repairs. Keeping competencies current is not only the difference between a cosmetic versus a complete repair, it’s also driving opportunity to properly-prepared collision facilities.
Bonding is the “New Normal”
Bonding with adhesives is a more complicated process than in the past. No longer is it a matter of just slathering on some glue and clamping the parts together. While structural adhesives have been used for more than 25 years in the automobile industry, early adhesives were predominantly single-component varieties, which at that time were sufficient for some repairs involving conventional mild strength steels.
The transition to repairing newer materials necessitated a shift to two-component (a resin and a catalyst) adhesive formulations that provided improved bonding properties and allowed more working time during repair.
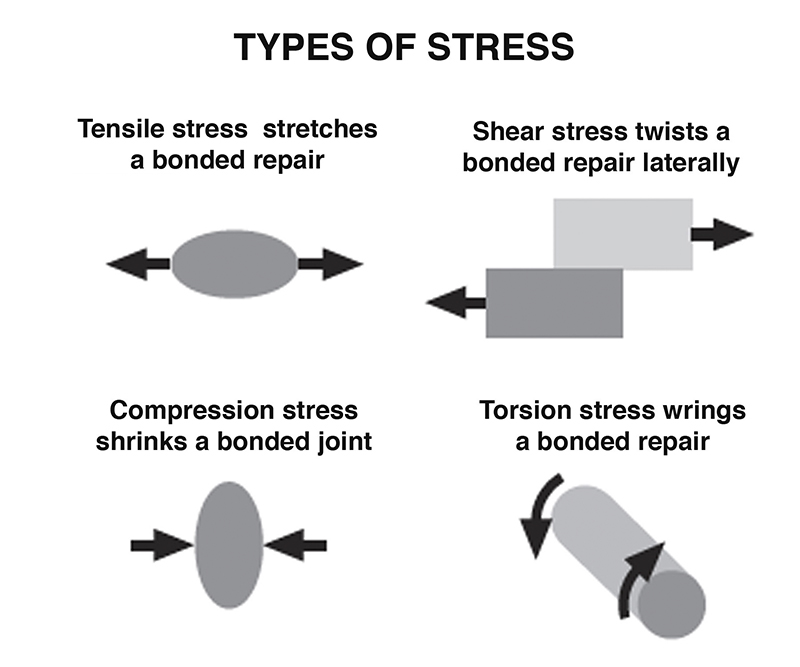
Chemical bonding, alone or in conjunction with other techniques, is an effective joining process for managing the above types of stress (courtesy Dow Automotive Systems).
When combined during a repair, the catalyst initiates a chemical reaction in the resin. Expect to feel the bonded parts heating up as the resin develops its bonding properties as the mixture cures. Note that the curing ability that is built into an adhesive can vary from minutes to days, which affects a technician’s working time. In addition, baking, ultraviolet light, hot air welding, or other procedures involving applied heat may be required.
Managing the types of stresses that a vehicle will encounter post-repair is also essential. This requires matching the right adhesive to the expected stresses and following more intricate bonding procedures. It’s the new normal.
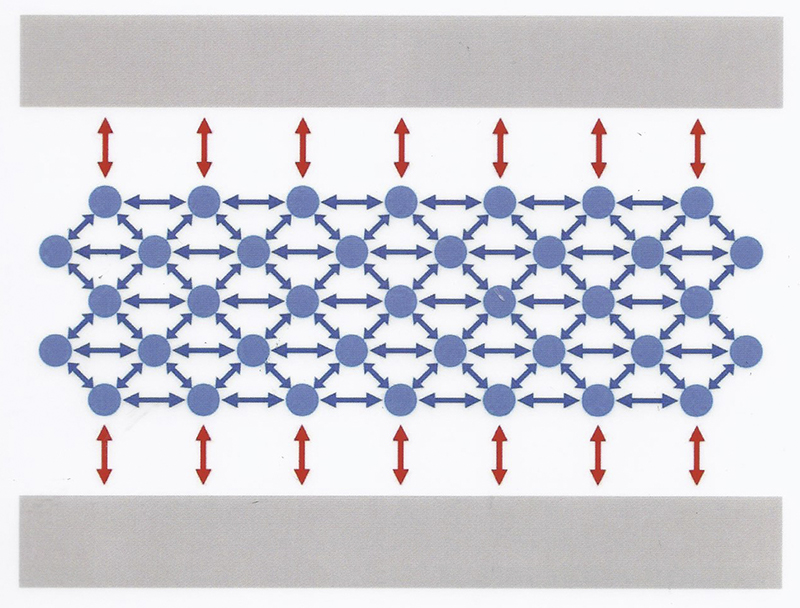
Adhesion and cohesion are the two fundamental properties of adhesives used in bonding materials. Adhesion (red arrows) is the attraction between the materials being bonded and the adhesive. Cohesion (blue arrows) is the attraction between the molecules of the adhesive itself, which occurs as the adhesive cures (courtesty 3M).
For example, bonding with structural adhesives is particularly effective in instances where the primary stress forces are either compression, or shear – where the force tries to slide the joined surfaces against one another, like pressing your hands together and trying to slide them apart. Conversely, bonding is not as effective in locations where tensile or torsion stress forces are in play. In cases where the tensile stress acting on the joint would pull the two pieces apart (peeling),or the torsion stress could bend or twist the joint, collision repair procedures often specify that adhesives be used together with rivets (rivet-bonding), or in conjunction with certain techniques, such as spot-welding.
The two-stage structural adhesives in use today include polyurethane epoxies, glassy matrix epoxies, which have glass beads embedded in the resin, and rubber-based epoxies. Glassy matrix epoxies, for example, are extremely strong and rigid, and they resist shearing stress at very high force levels. Polyurethane epoxies are more flexible and provide a better fit for some components, but they break under shearing forces at much lower force levels than glassy matrix epoxies. Newer rubber-based adhesives contain additives that allow synergistic rubber toughening of adhesives to provide high-strength epoxies with greater flexibility – a hybrid of the earlier formulations.
Chemical Bonding Offers Significant Advantages
Similar to higher-strength metals, newer plastics and other inbound composites come in different grades, which impacts how each material performs under various stresses during normal operation and during a collision.
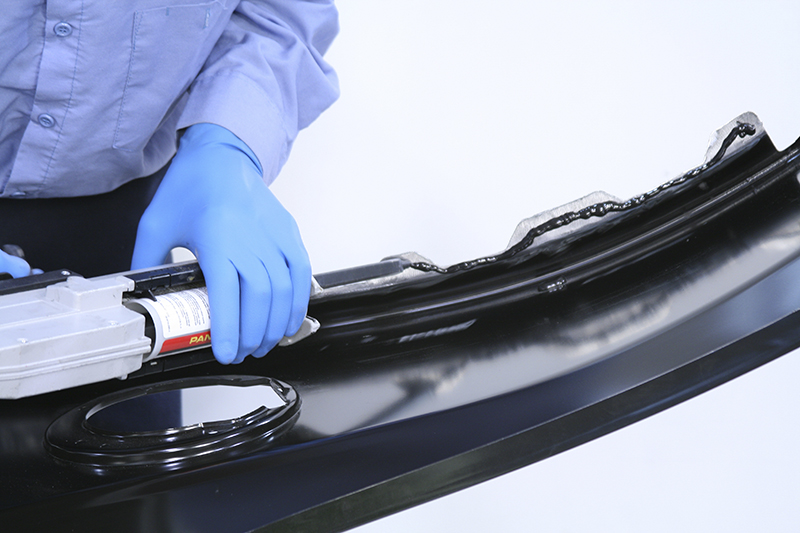
In some cases, Nissan requires procedures where adhesives are used along with other fastening methods. For example, proper repair of the GT-R requires the use of adhesives in the bonded and bolted joint where the aluminum rail attaches to the front steel structure, and also where the aluminum bulkhead attaches to the rear bulkhead. Adhesives are also used on the wheelhouse-to-quarter panel hem-flange joint (courtesy I-CAR).
Adhesive manufacturers 3M and Dow Automotive Systems say that the proper use of modern adhesives in bonding repairs:
- Provides more durable and stronger repairs with less corrosion risk than just welds. In fact, adhesives usually form a bond stronger than the materials they’re bonding together.
- Reduces the number of welds that would have otherwise been required. For example, OEM rivets and OEM structural adhesive are used in areas that squeeze-type resistance spot welding (STRSW) arms cannot access.
- Helps resolve problems with cracks around spot welds occurring as a result of fatigue loads. In addition, adhesives also enable hybrid sandwich construction to be employed in manufacturing.
- Optimizes the energy flow of the various stresses during normal vehicle operation, or a collision. These forces can be more evenly distributed across a region that is joined with adhesives, when compared to those joined only by welds, rivets, or other joining methods.
- Improves noise, vibration, and harshness (NVH) by dampening airborne noise distribution and minimizing body vibrations.
- Increases structural integrity and acts as an isolator between the dissimilar metals, preventing galvanic corrosion.
- Empowers the future introduction of lighter weight carbon fiber roofs and other non-steel and non-alloy components without compromising strength, performance, safety or durability.
Because different bonding adhesives have unique properties to provide acceptable or improved elasticity and flexibility, in addition to better stress management for the materials being bonded, collision repair facilities and technicians must be vigilant. The use of the wrong adhesive and/or incorrect bonding repair procedure – whether from ignorance or negligence – compromises everyone.
Rivet-Bonding is on the Rise
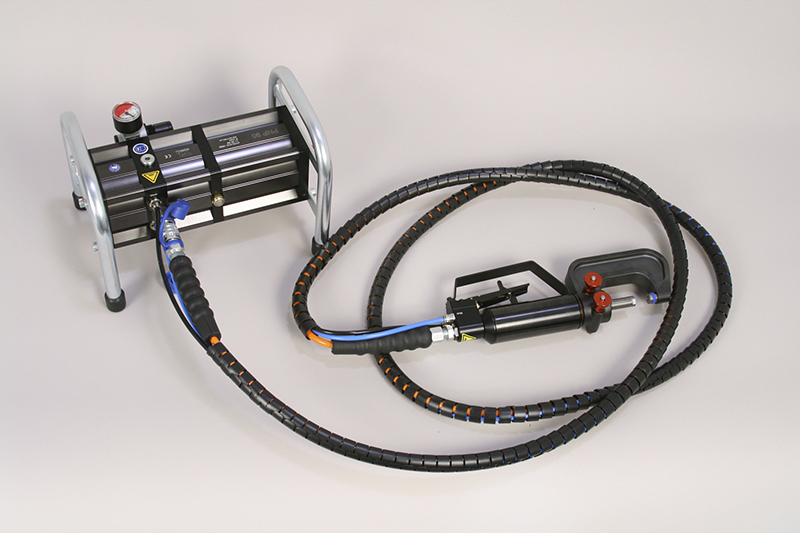
Consult TECH-MATE for Nissan-approved equipment, tools and supplies required to perform chemical bonding repairs. Examples include the fixture equipment and rivet bonding guns (courtesy I-CAR).
New vehicle construction techniques mean new procedures in collision repair are needed to maintain the integrity of a vehicle in the case of any following accidents. Consider the Nissan GT-R that uses a multi-material design of high-strength steels, aluminum, and carbon fiber.
While high-strength steel is used for most of the GT-R structure, cast aluminum is used for the GT-R front strut towers, door shells, and rear bulkhead. The front strut towers and rear bulkhead are attached to the steel structure using an adhesive, which increases structural integrity and acts as an anti-corrosive isolator. Carbon fiber panels, along with plastic and sheet-molded compound panels, are used to completely close out the GT-R underbody.
Attaching vehicle parts that are of two different types of materials should only be done by following the repair procedures approved by Nissan. Standard welding methods cannot be used to join these many new metals, because welding could deform them, and the interaction between the metals may lead to premature corrosion beneath repainted finishes. Likewise, welding would destroy newer nonmetallic materials. In these instances, chemical bonding may provide a viable alternative.
Some repairs to Nissan vehicles may only require a two-stage adhesive. Others may require the use of adhesives in conjunction with other fastening methods, such as bolts or rivets. Others may even require the addition of specialized welding procedures.
Should rivet-bonding be required, here are several key considerations that will help conserve limited working time and perform a complete, safe repair:
- Technicians must know the composition of what they are going to cut into beforehand.
- Before using an adhesive, application instructions and repair procedures must be understood.
- The use of approved parts, tools, fasteners and adhesives is essential. In particular, this new method requires the use of a punch riveting tool.
- Avoid cross-contamination by working on the separate metals in different areas and with different tools.
- Clean surfaces are required for proper bonding. It is also important that bare metal be bonded to bare metal and not to painted surfaces.
- When rivet-bonding, be sure to bevel the drill holes so that panels can be compressed snugly together. Technicians should also note if rivets are involved, repairs involving aluminum should use aluminum rivets, while those involving steel should use steel rivets. A coating of zinc dust to prevent corrosion may also be required.
- During the final assembly, ensure that the new panel aligns properly to where it will be attached and check for gaps. A specified reinforcement plate may be required.
Following Nissan Requirements and Recommendations is Essential
Nissan provides a number of resources for making complete, safe repairs for new lightweight materials.
For example:
- As a starting point, consult the Nissan or Infiniti service information websites (www.nissan-techinfo.com or www.infiniti-techinfo.com). In addition to other data, these sites provide critical information regarding the location of various construction materials within a vehicle.
- Then visit the Nissan TECH-MATE website (www.nissantechmate.com) for lists of required or approved tools, equipment and supplies. For example, Nissan requires Celette frame racks and fixture equipment, as well as certain adhesives, such as 3M DP420 or 3M 8115.
- Nissan has partnered with I-CAR for collision training. “Currently, collision program training for Nissan certified collision facilities is an I-CAR focused training program,” advises Mark Zoba, Nissan manager for Collision Parts, Service Sales and Marketing. ” To be a Nissan certified, facilities must attain I-Car Gold status. Full requirements to acquire Gold status can be found at the I-CAR website (www.i-car.com). We’ve already developed a GT-R course and are looking at adding additional Infiniti and Nissan specific courses in the future.”
Chemical bonding adhesives have proven to be ideally suited to modern vehicle bodywork repairs when high-strength metals, plastics, carbon fiber and emerging composites are present. Compared to more traditional joining technologies for new lightweight materials, modern two-component adhesive formulations and chemical bonding repair procedures allow all the properties of the repaired components to be more closely returned to their original state.
0 Comments