Is your choice of diagnostic tooling in collision repair helping or limiting you?
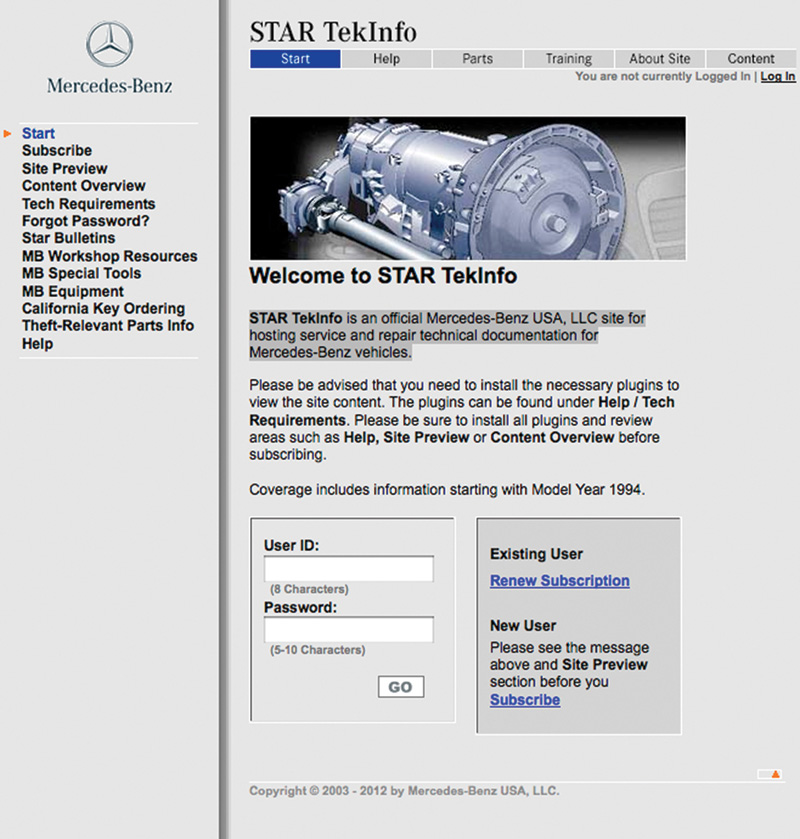
The STAR Tek Info website is the official Mercedes-Benz USA LLC (MBUSA) site for hosting service and repair technical documentation, bulletins, recommended tools and equipment, training, and other resources for Mercedes-Benz vehicles. Visit www.startekinfo.com for more information.
If you’re in the business of repairing Mercedes-Benz vehicles following an accident, you are now in the vehicle diagnostics business — like it or not. Like your mechanical brethren, being repair-ready and competitive in the marketplace today requires it. It’s that simple. But that doesn’t make it easy.
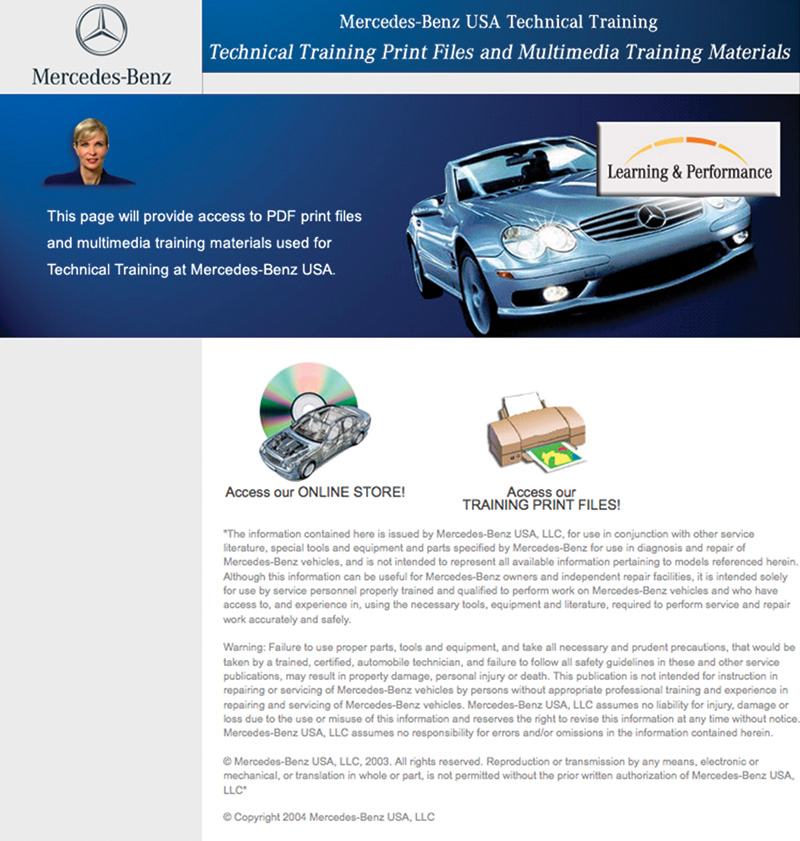
MBUSA also makes training information available at its Technical Training website. Visit www.mercedestechstore.com for a list of free model-specific PDFs or access to the Mercedes-Benz USA Online Store for model-specific CDs with more detailed information.
If you are not already using — or relying on someone who is — the M-B Star Diagnostic System (SDS), Xentry Diagnostics subscription-based software, and other factory-approved diagnostic tools during Mercedes-Benz collision repairs, the ability of your facility and technicians to provide customers with a complete job is limited, regardless of your experience and accumulated skillsets. Moreover, post-repair vehicle performance and occupant safety can be seriously compromised.
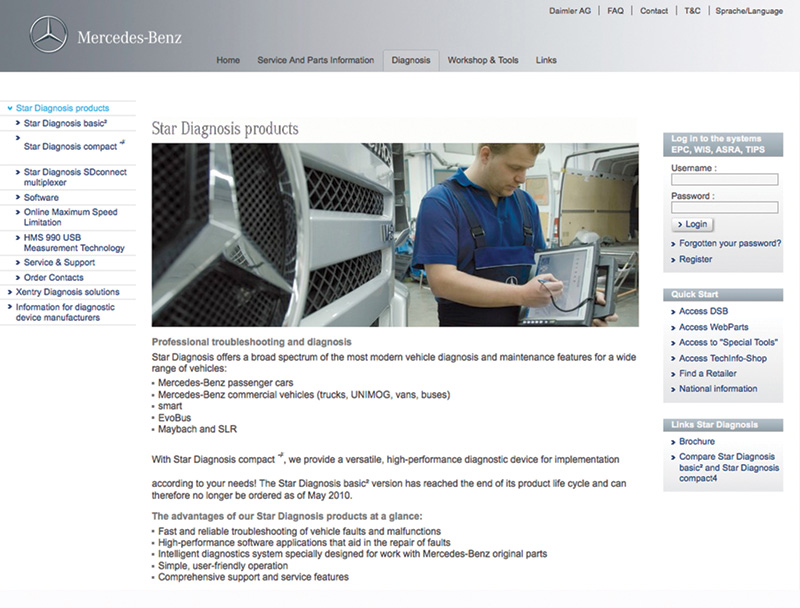
The Mercedes-Benz Portal describes various Mercedes-Benz Star Diagnostic System (SDS) hardware and software products, as well as the advantages provided to technicians. Visit , then click the “Diagnostics†tab to learn more. (Images —Mercedes-Benz USA LLC)
Let’s have a look at diagnostic scan tools basics, some Mercedes-Benz resources available and several case studies specific to the marque that will help collision facilities better understand why proper tooling is critical to their survival and future growth.
Electronic complexity drives scan tools into the collision repair process
Many aspects of modern collision repair of Mercedes-Benz vehicles require access to and the use of genuine resources for service information, training, collision repair procedures, equipment and tools are essential to effect a complete, safe repair. For example, recent changes in the mix of materials used to manufacture vehicle structures (e.g. advanced high-strength metals and carbon fiber-reinforced plastic) have resulted in Mercedes-Benz-specific changes in repair techniques, procedures, tools, and more.
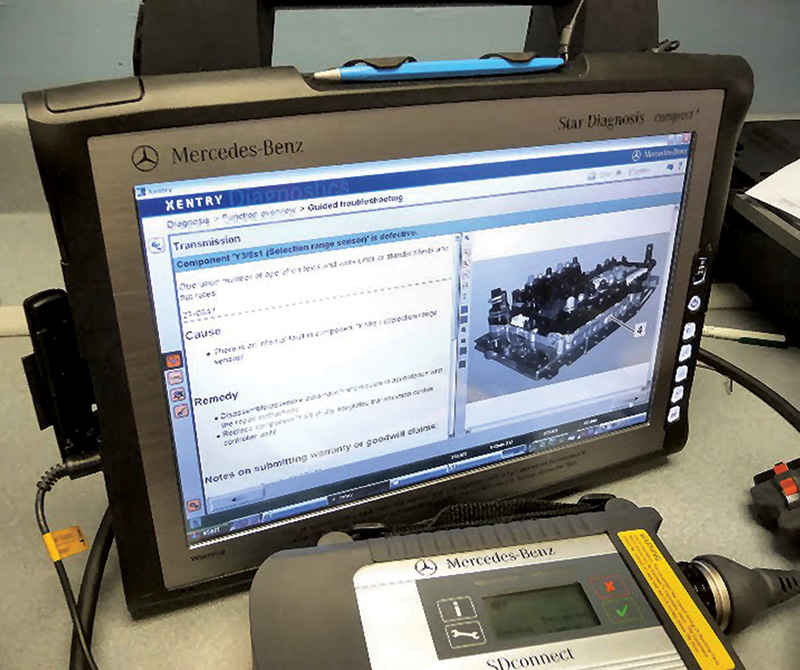
The Mercedes-Benz STAR Diagnostic System (SDS) Compact4 scan tool (above) along with SDS Flash subscriptions are essential to providing a complete collision repair. The Compact4 uses a vehicle’s VIN to register and verify vehicle-specific hardware and software data into Mercedes-Benz’s server, so that Mercedes-Benz knows exactly the configuration of each vehicle. This is crucial, since there are often various recall-based issues that require such knowledge and the company requires it of all electronic modules to provide recalibration, reprogramming, and other services. (Image — Continental Imports)
However, accelerating vehicle complexity is not just limited to structure. Vehicles just a decade ago were composed of mostly mild steel; they also contained only a few electronic control units (ECUs) — those computerized modules that control functionality of various vehicle systems. Today, however, it’s not uncommon for new Mercedes-Benz vehicles to have 50 or more electronic modules onboard; some high-end luxury models may even exceed 70 units. This proliferation of ECUs, as well as associated sensors, actuators, and other devices is driving the collision industry to join the scan tool revolution.
This trend is also gaining traction. Emerging electronic systems will continue to push the need for scan tools and other diagnostic equipment. Examples include engine management, passive and active safety, electrified drivetrains, electronic power steering, alignment, sophisticated communication networks, and other vehicle systems that may be damaged in an accident. Because these vehicle systems are interconnected, their proper operation and performance post-repair requires an early and accurate diagnosis for collision-induced damage to these systems.
But unlike replacing a structural part, even if an electronic part is properly diagnosed as being faulty, replaced, and properly positioned it will often require initialization, reprogramming, or some other specified procedure to complete the repair. This requires proper diagnostic equipment and software.
What’s in your scan tool?
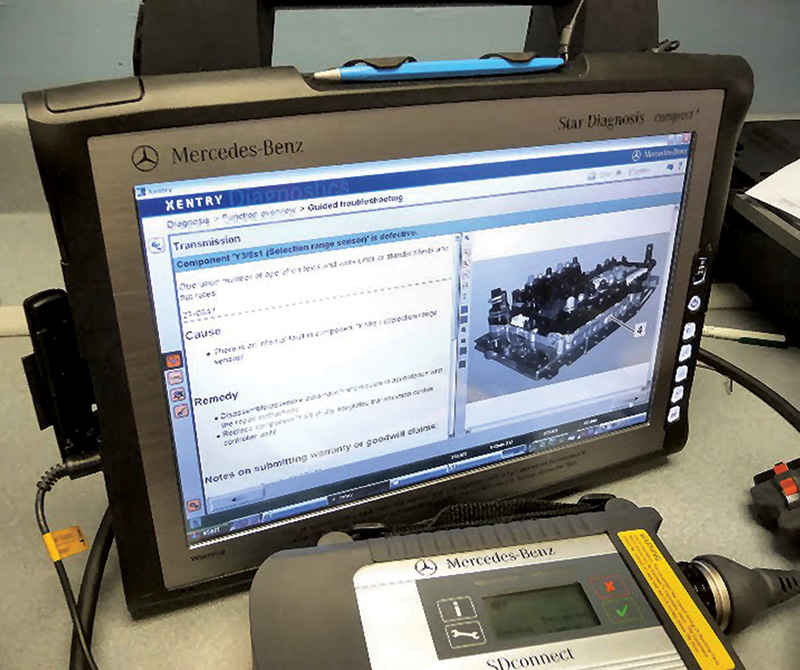
The Mercedes-Benz STAR Diagnostic System (SDS) Compact4 scan tool (above) along with SDS Flash subscriptions are essential to providing a complete collision repair. The Compact4 uses a vehicle’s VIN to register and verify vehicle-specific hardware and software data into Mercedes-Benz’s server, so that Mercedes-Benz knows exactly the configuration of each vehicle. This is crucial, since there are often various recall-based issues that require such knowledge and the company requires it of all electronic modules to provide recalibration, reprogramming, and other services. (Image — Continental Imports)
A recent survey by the Equipment and Tool Institute (ETI) reported that approximately two-thirds of all collision facilities own and use at least one scan tool. For those who don’t know ETI, it is the industry organization that communicates with Mercedes-Benz and other automakers to acquire and archive scan tool data — algorithms, protocol documents, parameter identifier matrices, diagnostic trouble codes, etc.
Aftermarket tool and equipment manufacturers pay a licensing fee or annual dues to ETI to use selected data to develop and build aftermarket electronic test equipment and other tools used for diagnostics and repair. When genuine gaps in scan tool information are discerned, ETI works with Mercedes-Benz, as it does with other automakers, to gather the data and pass it on.
“Be it Mercedes-Benz or any other OEM, factory scan tools are the most expensive diagnostic tools available, but they also have the most diagnostic and repair functionality for any automaker’s vehicles,†explains Charlie Gorman, ETI executive director. “In the case of Mercedes-Benz and some other automakers, subscription-based diagnostic software is also required in addition to the scan tool hardware. It’s often the software that needs to be fixed during a repair — whether by reinitializing, reprogramming or recalibrating functionality.
“With the advent of more ECUs on vehicles, the provision of scan tool information by automakers to the aftermarket has become a greater focus of what ETI does,†Gorman adds. “In the case of diagnostic scan tools, we’re talking about the computer data that needs to be integrated into an aftermarket scan tool so that technicians can talk to the vehicle and emulate an automaker’s factory tool.
It’s important that facilities and technicians understand that scan tool functionality is almost always the result of choices made by aftermarket manufacturers, not the lack of data being available from automakers,†he notes. “On rare occasions when bona fide data gaps are identified, ETI works with Mercedes-Benz to resolve them for everyone’s benefit.
“While aftermarket scan tool manufacturers all get access to the same data streams as the Mercedes-Benz factory tool uses, they cannot effectively replicate the full Mercedes-Benz tool and still be price-competitive. Instead, each manufacturer makes its own marketing decisions about what features, data, and functionality goes in their tools and what doesn’t — based on niche, price point, and other factors,†says Gorman.
“For example, some companies will build a generic scan tool that covers a wide range of OEMs for the most common fixes; some may offer slightly more comprehensive functionality for a narrower specific group of OEMs (European, Asian or domestic automakers); some will concentrate on a specific automaker and provide greater, although not complete, functionality; and others will focus on specific functions such as diagnostic tools for alignment or tire pressure monitoring systems.â€
Diagnostics at a Fraction of the CostBody shops and collision technicians can get bogged down by a lack of knowledge, technical resources, the time clock, and the customer. Typically, problematic vehicles are sent to a dealer or a mobile diagnostic service provider is called in. Both can add time and cost to the collision repair. “Remote diagnostics†is a new alternative that might be the right fit for collision facilities seeking to recapture the time and revenue lost by sending vehicles out to dealers or waiting for a mobile diagnostician to arrive. Robert Beckman, CEO of Blue Link Diagnostic Solutions Inc. says the “just in time†solution, developed in conjunction with IBM: Leverages J-2534 interface devices, which Mercedes-Benz supports, to connect Mercedes-Benz vehicles in your body shop digitally to Mercedes-Benz diagnostic tools, software and equipment at a remote location, at a fraction of the capital costs that tooling up to factory level capability would entail. Allows vehicles in a body shop to be diagnosed and repaired immediately onsite. Provides affordable access to genuine Mercedes-Benz service information and other resources. Utilizes the expertise of highly specialized technicians who have a thorough understanding of and experience using Mercedes-Benz service diagnostics. More information about this service can be found at www.bluelinkdiag.com. (Images — BlueLink Diagnostic Solutions Inc.) |
What’s a body shop to do?
 While a Mercedes-Benz factory scan tool and subscription-based software provide the most complete functionality for electronic-related collision repairs, not every facility can afford them. Given the high cost of factory versus aftermarket tooling, the purchase of a scan tool by a collision facility needs to fit the body shop’s business model. The challenge is for a collision facility to use the best scan tool strategy it can afford, then fill any collision service gaps with sources that have Mercedes-Benz factory diagnostic tools and software and the expertise to use them.
With respect to scan tools and diagnostics, collision facility scan tool practices generally fall into one of five broad categories. A body shop may:
- Own no scan tools, electing to farm all related work out to a nearby independent shops or dealers with the access to service information, tooling, training, and expertise.
- Own aftermarket scan tools only, but be unaware that certain functionality is missing, thus limiting the ability to make a complete repair.
- Own aftermarket scan tools only, but be aware of what specific functionality is lacking, and rely on “expert†mobile or remote diagnostic service providers to assist with more complex diagnostics and software programming. This enables a complete repair, but doesn’t provide a facility with direct control of its time or destiny.
- Own Mercedes-Benz tooling and software, but may not have mastered the full capability of the tools yet. Training from Mercedes-Benz can help grow expertise.
- Own Mercedes-Benz tooling and software, and acquired the expertise through Mercedes-Benz training to use the tooling to its full capability.
These scenarios prompt three questions. First, does a collision facility know what necessary functionality its aftermarket scan tool does not have before making repairs? Second, if an outside source for Mercedes-Benz tooling is used, does that source have the understanding, expertise, and access to software updates to make full use of the tools? Third, if no Mercedes-Benz tooling is used, either directly or indirectly, what hasn’t a collision facility fully repaired?
There is also a caveat to keep in mind: Using stop-gap measures may work for the short-term. However, in addition to giving up direct control, it does not diminish the full responsibility for a complete repair. In addition, because diagnostic-related repairs are not readily visible during the estimating stage, supplemental approvals for work and parts beyond the original estimate may be necessary, which may mean a delay in total repair time. For collision facilities and their technicians, it’s becoming increasingly critical to be able to not just make all structural repairs, but all electronic repairs as well.
“Radical change began in 1981 when the computer came onboard on every vehicle,†one senior trainer tells us. “Yet only 10 percent of body shops that I have surveyed recently actually use OEM factory tools; and just five percent of shops own and use a J-2534 interface tool to reflash electronic modules.â€
While the cost of Mercedes-Benz tooling is a serious consideration, the opportunities lost and the assumed risks of choosing not to invest in such tools to be fully competent and in direct control of one’s expertise should not be neglected, either. For example, outsourced expertise must be invoiced at face value, without any up-charge, But with in-house diagnostics, body shops can charge for diagnostic time and equipment, which can increase revenue.
The challenge for collision facilities is clear: Each must strive to be capable of providing customers with a complete and safe repair by employing the highest level of tools and expertise possible. And they must strive to gain more direct control and diagnostic expertise.
“Today and going forward, body shops and technicians are in for a really rough ride if they don’t embrace vehicle electronics and electrification as realities today, and then tool and train properly,†the trainer cautions. “Many aftermarket independent repair facilities are increasingly less productive today because they continue to farm out too many opportunities, rather than tool and train to manage change. Like a slippery slope, the refusal by some of these facilities to recognize, embrace, adapt, and prepare will ultimately seal their fate and pre-empt a sustainable, profitable future.â€
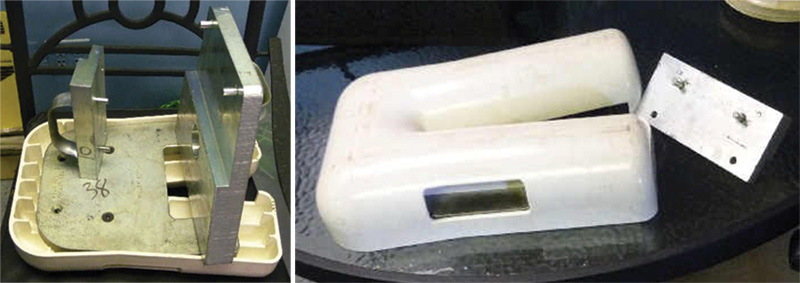
Configuring the deployment characteristics of new airbags installed during collision repair requires the use of WSS equipment, an SDS scanner and subscription-based diagnostic software. (Image — Continental Imports)
A few body shop examples
There are many examples of repairs in which Mercedes-Benz factory tooling and software capability, along with the expertise to use them, are essential to providing a full, safe collision repair. We talked with two expert technicians to provide a few examples to demonstrate this. They are:
- Robert Beckmann, who is the CEO of BlueLink Diagnostic Solutions, Inc. He also provides training in diagnosing and repairing Mercedes-Benz vehicles at various industry events and is well-versed in Mercedes-Benz diagnostics methodology and equipment for both regular and theft-related parts.
- Steve Brotherton, who owns Continental Imports, an independent shop located in Gainesville, Fla., that specializes in servicing Mercedes-Benz vehicles and several other brands. He owns OEM factory diagnostic tools and purchases service information subscriptions for each automaker that he services. In addition, he requires his Mercedes-Benz team of four technicians to complete Mercedes-Benz training and to use the Star Diagnostics System (SDS) Compact 4 diagnostic scan tool (above), software, and other Mercedes-Benz-approved tools. Besides his mechanical-based business, Continental Imports works with nearby collision facilities that recognize when they need the expertise his shop can provide.Â
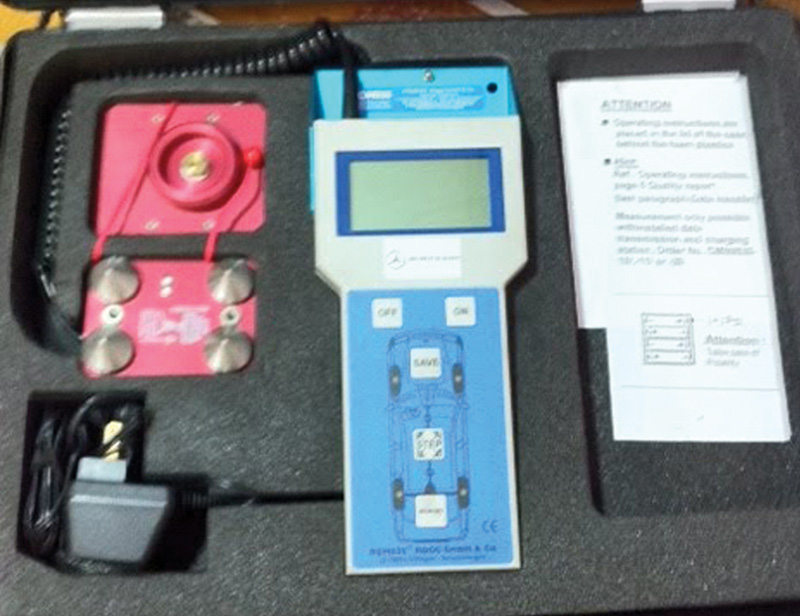
The Romess electronic inclinometer is a Mercedes-Benz-approved tool used to perform wheel alignments. (Image — Continental Imports)
“Mercedes-Benz has some of the most advanced safety equipment in the world, which makes the use of the company’s diagnostic equipment an essential part of most collision-related repairs today,†Beckmann says. “For example, many ECUs associated with vehicle safety systems are coded and configured to very specific applications. These include components such as seat weight sensing systems (WSS), electrically operated reversible seat belt tensioners, airbag control units, and others, all of which need programming after deployment or replacement.â€
“Collision professionals must be aware that these and other Mercedes-Benz safety-related components — especially if part of a vehicle’s Supplemental Restraint System (SRS) — need to be properly programmed and configured after deployment or replacement for them to operate correctly. Because they are part of most collision-related repairs today, the failure to do so may cause unsafe or unpredictable operation post-repair.â€
Beckmann cites a number of reasons why tooling and proper software programming is essential for safe predictable operation post-repair. Among others, these include the following:
- Many ECUs are VIN-locked (vehicle identification number) within the SRS system. Aftermarket scan tools simply cannot do all that the Mercedes-Benz scan tool can.
- Mercedes-Benz diagnostic equipment maintains log files and provides traceability into how things were programmed and coded.
- Accountability is provided by a login system that identifies who did the programming of any ECU.
- The information provided by Mercedes-Benz resources that support factory diagnostic tooling includes guidance that enables a level of repair aftermarket tools may not be able to provide.
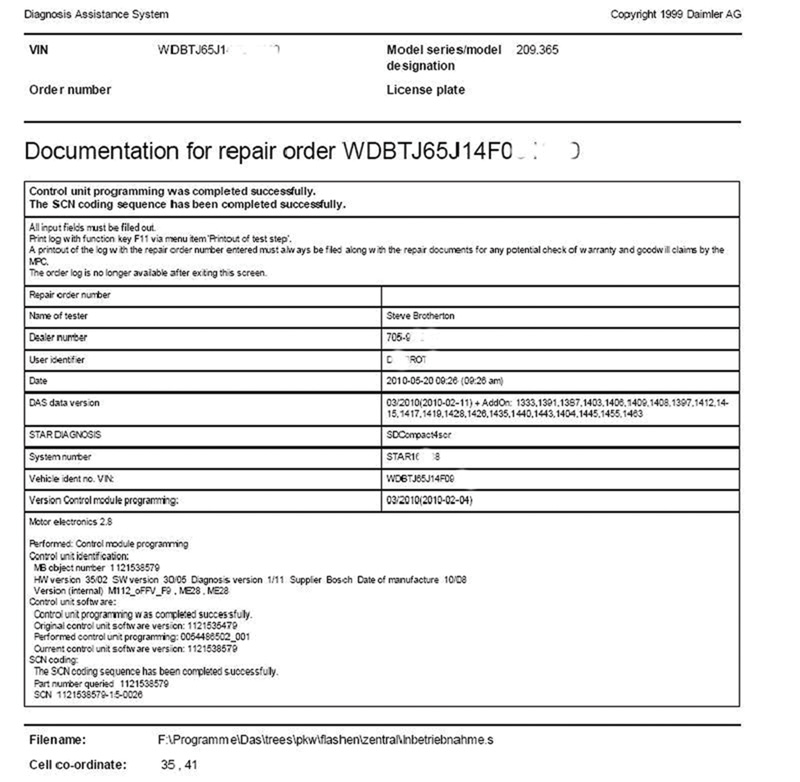
Mercedes-Benz requires SCN coding whenever ECUs are serviced. The coding provides the automaker, technicians, and vehicle owners with a secure means to identify, verify, and update the calibration and programming when servicing electronic modules. (Image — Continental Imports)
“For example, PDFs are available from STARTek Info that provide schematic diagrams and configuration instructions for the restraint and other safety systems,†Beckmann tells us. “In particular, these resources denote the data for items that need coding. The use of Mercedes-Benz scan tools and software is essential to taking advantage of this data to properly configure Supplemental Restraint Systems (SRS) and other safety systems. It’s part of performing a complete collision repair for your customers.â€
“The WSS is used to continuously monitor the passenger seat for the size and weight of the occupant and then configure the deployment characteristics of the airbag in the event of an accident,†notes Brotherton. â€The WSS involves three weights and requires a calibration process that can only be done completely using the SDS scan tool and subscription-based diagnostic software.â€
“When a wheel alignment needs to be performed as part of a collision repair, Mercedes-Benz requires the use of a certain approved tools and procedures,†Brotherton explains. “Any Mercedes-Benz model, but especially those with Airmatic and Active Body Control (ABC) systems, requires the use of the approved Romess tool, which is an electronic inclinometer.â€
“The concept of the tool is to gauge and calibrate ride height,†Brotherton continues. “Romess data is used to establish proper alignment specs. In the case of Airmatic or ABC, the suspension height must be calibrated before the alignment is performed. This is done by first adjusting the height with the SDS scan tool until it is the right Romess angle specification, and then entering those numbers (representing each corner of vehicle) to set the calibration.
“Mercedes-Benz also employs SCN coding when servicing modules,†Brotherton says. “The concept of SCN is for the tech to program a module and then hook to the Mercedes-Benz server located in Germany. The VIN, hardware and software numbers are verified and basically a calibration ID is performed. It also registers new software and hardware into the server for the car so the company knows exactly the configuration of each. In addition, there could be various recall-based issues that require such knowledge, and Mercedes-Benz requires it of all modules that get programming. The complete function by its very nature makes a Mercedes-Benz tool and SDS Flash subscription necessary, if a collision facility truly wants to be able to provide complete repairs.
Clearly, it is neither easy nor cheap to tool-up for diagnostic service as part of a collision repair. Improving vehicle serviceability means that OEMs and the aftermarket need to collaborate meaningfully. Mercedes-Benz does that, notably through its involvement with ETI, the National Automotive Service Task Force, and other organizations. That cooperation helps tool and equipment makers build the stuff that technicians want to use.
But collision facilities must be cognizant that when factory-level diagnostics are needed, nothing beats OEM diagnostic tooling. At the end of the day, it is the shop owners, technicians, and service advisors who customers identify as the human interface when it comes to collision repair. So, ask yourself one acid-test question: “Is my choice of diagnostic tooling in collision repair helping me or limiting me in growing my business?â€Â
0 Comments