Welding: It’s a matter of focus and staying relevant.
Like almost everything else on a BMW vehicle, mechanical service and collision repair are constantly evolving. In addition, what was once a clear division between mechanical and collision service has blurred.
Electronic systems — modules, sensors, cameras, and other hardware — are often situated in the very same areas that welding may impact, so awareness and taking precautionary measures do matter. 

As BMW vehicle construction technology advances, the repair procedures, equipment, tools, supplies, and other resources required to provide customers with a complete and safe repair that returns the vehicle to its original specifications and safety ratings march in step. BMW increasingly recommends the use of bonding and rivet joining technology for newer models, rather than conventional welding, such as MIG (Metal Inert Gas) or STRSW (Squeeze-Type Resistance Spot Welding). Examples include the replacement of both steel and aluminum exterior body panels, structural parts, and sectioning specific locations in conjunction with VIN-specific repair procedures. [Note: Bonding and riveting was covered in the June, 2012 edition of the bimmer pub in an article titled “Bonding Ramps Up.â€]

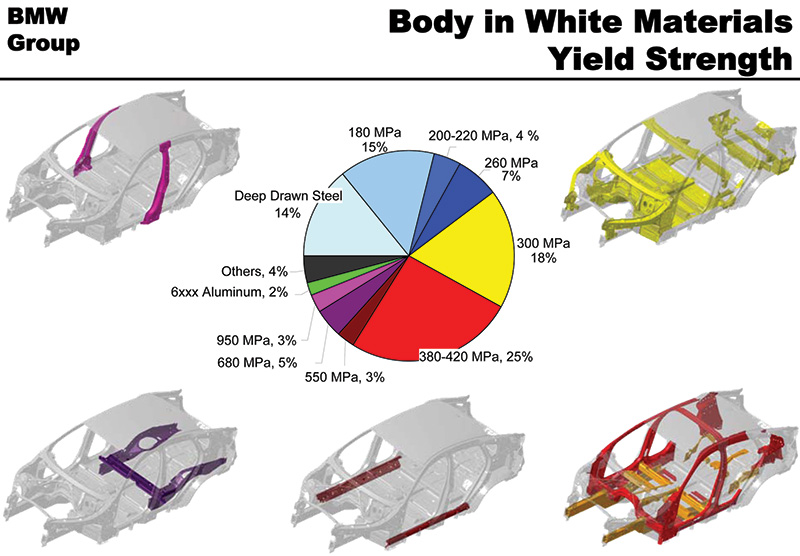
BMW “Body in White” color-coded schematics delineate the mix and location of AHSS, UHHS, aluminum, and other materials that comprise its models. For the BMW X6 shown above, BMW calls for several different joining technologies — MIG welding and brazing, spot welding, bonding, riveting and others — depending on the part being repaired. Consult ISTA for details.
One of the main reasons is the increasing use of heat-sensitive advanced higher strength steels (AHSS), ultra high strength steels (UHSS), aluminum, magnesium, and alloys. Heat generally weakens these new metals, while bonding and riveting allows their inherent strength to be retained. Another reason is that BMW offers a 12-year corrosion warranty; bonding and riveting provides increased corrosion resistance of the repair joints compared to conventional technologies.
However, while conventional welding techniques and processes are becoming the secondary method for newer models, they still remain a primary method for the collision repair of older models and associated parts, components, and assemblies. But times have changed. The challenge for collision facilities and technicians who repair BMW vehicles is clear: They must embrace and develop competencies for new joining technologies while also preserving the same for conventional welding attachment methods.
For welding, there is no substitute for authentic BMW resources
The choices that collision facilities make matter; being cheap or extravagant both have their consequences. Low quality, sometimes incomplete, repairs can result in expensive comebacks that are not offset by revenue. If an improper prior repair is determined to be at fault in damage or injury in a future accident, consequences can be even more serious.
And when customers have a sour brand experience due to a poor collision repair, it impacts everyone: BMW, the dealership, and the collision facility. Consulting genuine BMW resources should therefore always be the first step in the repair process, so that a welding-related repair isn’t compromised from the beginning.
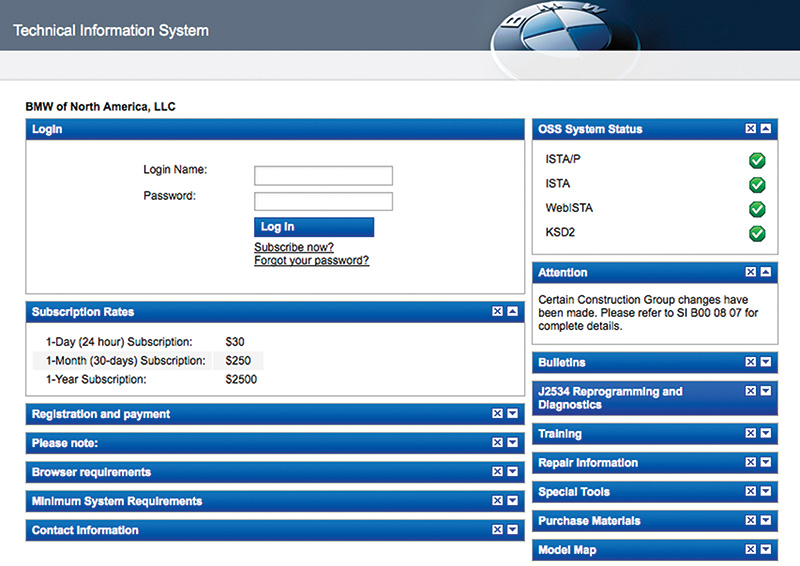
Keep your collision repairs correct, complete, and current. Always consult the BMW Technical Information System (ISTA) application at www.bmwtechinfo.com before beginning repairs. ISTA provides detailed repair information and procedures, special tools and equipment, technical service bulletins, wiring diagrams, and other VIN-specific data.
BMW’s Technical Information System (ISTA) application is the most authentic, complete and up-to-date source for collision and technical information. Visit www.bmwtechinfo.com and choose from several fee-based subscription terms to access this resource. For collision repairs, and welding in particular, ISTA provides VIN-specific repair procedures; “body in white†diagrams that show where various types and strengths of metals that comprise components and parts are located, as well as the most current associated procedures, tools, and equipment required to effect repair.
“I’ve seen numerous cases where BMW schematics were the key to making the correct and complete repair,†says Peter Orlando, a technician and owner of Automotive Training Technologies. “For example, in contrast to BMW schematics, third party service information providers typically ‘edit down’ diagrams in an attempt to maintain a uniform appearance across different brands. The missing detail makes the difference in the time spent and completeness of the repair.â€
BMW-approved welding equipment, tools, and supplies also make a difference in restoring a vehicle as close as possible to its original condition and safety ratings. BMW makes these lists readily available on its website. In addition to welding resources, collision professionals increasingly need to use scan tools to diagnose and repair wiring and damage to electronic components incurred during accidents. Welders and associated supplies are one example. The choice of diagnostic and reprogramming scan tool is another.
“Factory tooling matters, especially when lives are on the line,†Orlando explains. “Without the BMW iTool, you are never going to be able to totally fix cars with just a generic aftermarket scan tool. For example, the Bosch Mastertech M-VCI aftermarket scan tool is an excellent tool that provides independent repair facilities with full access to ISTA diagnostic and reprogramming functionality via an SAE J-2535 pass-through device, but it does not enable access to all of the other functionality that is also essential for modern collision repair.â€
“Training, equipment, and parts sourcing are three other critical resources essential to full and safe collision repair,†notes Tim Morgan, a welding expert who serves voluntarily as the chairman of the Equipment and Tool Institute (ETI) Collision Repair Group.
Body shops must commit to ongoing training to remain relevant
“The ETI Collision Repair Group comprises automakers, equipment manufacturers, scan and hand tool makers, material suppliers, educators, and others. We work closely with BMW and others to ensure we are aware of inbound changes to vehicles before they enter the marketplace so that we can then help the collision industry be service-ready,†says Morgan. He is a leading collision industry authority on welding procedures, processes, and practices, having worked for a number of collision industry equipment manufacturers that include Car-O-Liner, Chief Automotive Technologies, ELEKTRON Bremen GmbH, and Spanesi Americas. In addition, Morgan was also instrumental in identifying and recruiting trainers for consideration by BMW of North America (BMWNA) when it was developing its network of nationwide training facilities.
“BMWNA today is one of a very small number of automakers that provides both mechanical and collision training,†he says. “This training is available to both dealer-owned certified collision repair facilities and independent facilities that are sponsored by a BMW dealer. BMWNA also works closely with ETI, the Inter-Industry Conference on Auto Collision Repair (I-CAR), and other industry educators to ensure currency with BMW technology and repair methodology. That combination is a rarity.â€
“There are practical benefits in utilizing the BMW-approved equipment, tool, and supply vendors listed on the website,†he adds. “Besides meeting the criteria that BMW requires for its vehicles, many approved suppliers also provide training in how to set up and use their products, as well as continuing training to help technicians stay current with innovation and changing technology. Changes in welding and other joining technology, procedures, and safety guidelines are constant; continuing education keeps professionals on the leading edge of the learning curve over time.â€
“Committing to ongoing training is critical,†Morgan emphasizes. “The materials used in BMW’s vehicle construction mix are dynamic; the mix evolves over time as innovation is integrated into vehicle design and manufacture. Also, many collision facilities have a high staff turnover rate. One-time training isn’t enough; be sure to negotiate with your suppliers, not only at initial purchase and setup, but also for ongoing training. It keeps you fresh and it keeps you relevant.â€
Morgan adds a caution. “When it comes to welding with replacement parts: Use genuine BMW parts. Aftermarket parts (if they even exist) and reused salvage parts are both problematic. For example, cutting and removing pre-existing welds on salvage replacement parts can be a tedious, time-consuming chore that can eat up technician time, drive up costs, and erode profit. When welding is a necessary process for a repair, genuine BMW parts provide better form and fit, typically require less labor to position properly and then attach. The result is a safer, quicker, more economical, and better quality repair.â€
“I-CAR believes that welding practices within the collision industry are inconsistent and inadequate,†states Jeff Peevy, I-CAR director of Field Operations. “Our recent 2012 I-CAR research study tells us that over 90 percent of collision industry technicians who weld lack competency in advanced high-strength steel welding procedures and other techniques. In addition, 69% of collision facilities nationwide have no consistent welding-related training.â€
That is disturbing. According to Peevy, the I-CAR research identified three primary issues related to infrastructure, shop practices, and training:
- Amperage supply at many body shops was too low to support modern welding equipment.
- In far too many cases, welding equipment was unable to perform properly due to poor or little maintenance.
- Improper welding techniques were increasingly common when producing the basic welds that are prevalent within the industry.
To help resolve welding competency gaps, Peevy says I-CAR has revamped its welding courses for both MIG and STRSW, and also has launched new Weld Qualification tests for each that require technicians to demonstrate basic welding techniques and the ability to perform basic weld types. Visit www.i-car.com for more details.
But here’s the good news: When asked specifically about BMWNA, his response was appreciative and his praise stark. “BMWNA gets it. It not only acknowledges that certain minimum ‘welding qualification’ standards are needed, it has alsoincorporated them into BMWNA training provided to technicians in BMW dealer-owned certified body shops or independent dealer-sponsored body shops and also shared that training with industry organizations like us. The industry needs more of this.â€
The primary welding trend is “focused intense heatâ€
When you look at the history of automotive welding, the evolutionary trend has been on improving the focus of the heat source to lay down a precise and appropriate type of weld. Keeping as small a heat-affected zone as possible and minimizing the amount of heat transferred into the metals being welded conserves the inherent strength of the materials being repaired.
In the distant past, welding by blacksmiths involved heating metals in a forge, then hammering them together to form a weld. A very large area had to be heated to red hot to get a weld area hot enough to join. The invention of the gas welding torch produced more focused heat to actually melt metal in a smaller area to form a weld. Arc welding in turn produced even more intense focused heat.
The advent of TIG (Tungsten Inert Gas) welding provided more heat and enabled smaller, more precise welds to be performed. Pinpointing more intense heat was further facilitated by MIG (Metal Inert Gas) welding and later, Squeeze-Type Resistance Spot Welding (STRSW). Today, at the manufacturing level, BMW employs more intense and precise pulsed laser welding using robots to create very precise welds where necessary, with minimal heating of the metals involved.
In cases where conventional welding is called for by BMW on late models, generally either MIG (also known as GMA or Gas Metal Arc) welding or “spot welding†(STRSW) is specified. Be sure, however, to check BMW VIN-specific repair information to ascertain the welding and procedures required.
“MIG welding provides a narrow, focused heat that is appropriate for aluminum, mild steels, and some higher strength steels,†Morgan tells us. “Driven by material shifts toward stronger steels, aluminum and other alloys, spot welding is generally more frequently specified than MIG welding,†Morgan says. “It also requires less preparation and labor during a collision repair. For example, less grinding down is needed.â€
BMWNA explains that STRSW has other advantages compared to MIG welding. These include:
- MIG plug welds require lots of finishing, while spot welds need a little rubbing with an abrasive pad.
- Spot welds are cleaner looking and less invasive. The zinc coating on BMW finishes will actually flow around a spot weld, and not have the nodule-sized nuggets that MIG plug welding can create.
- Spot welds also have a much smaller heat-affect zone. This minimizes the risk of corrosion and also maintains the structural integrity of AHSS, UHSS and other metals. This translates into less materials being consumed — no welding wire, no welding gas, and no abrasive to grind with.
Tips that matter
“In today’s collision environment, facilities would be well-positioned if they used a pulse-type MIG welder,†Morgan advises. “Typically, two different torches should be provided, one for use with 100% argon shielding gas, the other with an easier-to-work-with 80% argon/20% carbon dioxide shielding gas mix.â€
“Cleanliness is essential; don’t compromise your repair. MIG welding new panels or structural parts on a vehicle is probably the most critical process during the repair. If all aspects of site preparation and MIG welding are not virtually perfect, the vehicle may be unsafe when returned to the road. It’s ironic that the most common MIG welding flaw seen in body shops is an incomplete MIG plug weld, which just happens to be the most utilized weld as well. An unclean weld site is a primary cause of this; poor visibility is the other.â€
“For STRSW applications, a spot welder must deliver 14,000 amps at the tip on a consistent basis throughout operation,†Morgan says. “To do that a 220V three-phase power supply to the facility is necessary. Note also that top-quality spot welders have a built-in inverter to monitor and regulate power from the plug to the tip of the torch. Also, make sure the spot welder arm and cables allow the technician to get the gun into the tighter workspaces in vehicles today.â€
“Before taking on spot welding, facilities must also be aware that they need to ensure adequate power supply not only to the shop, but to the spot welder as well. When doing your electrical power supply survey, ensure there is a minimum of 60 amps available at any plug outlet where the spot welder will be used. Also, be sure to use copper, not aluminum, wire between incoming power and the plug outlet. Copper wire has better electrical conductivity and won’t suffer the power loss over distances that aluminum wire does. Finally, plan on shorter cable runs where possible to conserve the energy delivered to the plug outlet.â€
“One last piece of advice: Invest in an aluminum-only room. Plan on it being about the size of a paint booth; it can be walled-in or well curtained. This is because it is essential when welding aluminum to keep shop contaminants out. Facilities will also require separate extraction gear and repair equipment. Admittedly, this investment is expensive. But a poor collision repair due to substandard body shop practices, or turning away repair opportunities because a body shop doesn’t keep pace with repair trends are costly too.â€
It all comes down to the choices made.
Do it Right: Consult ISTA
The 2004 BMW 5-Series is built with both aluminum and a variety of steels. The front end from the firewall forward is aluminum with the passenger compartment and rear section constructed from various steels. From an equipment viewpoint, BMWNA currently has approved the use of a Car-O-Liner bench fitted with a Car-O-Flex fixturing system and a Car-O-Tronic measuring system. However, the repair procedures required for aluminum parts are much different from those of the steel parts.
According to BMWNA, the only acceptable repair for the 2004 5-Series aluminum front end parts is complete replacement. Pulling of the front end is not allowed, nor is any heat, such as welding, to be applied to the front end structure. To make the aluminum repair, specific bond and riveting steps must be taken to replace the damaged front end with new aluminum parts.
For repairs to the various steels that comprise the cabin compartment and rear end, BMWNA specifies both MIG and/or spot welding procedures and outlines steps for each. The procedures vary depending on the type, strength, and thickness of the steels in certain locations. In addition, special steps for parts that are made with different steels are required (e.g. AHSS on the visible outboard side is reinforced with UHSS on the backside).
Unlike most automakers, BMWNA, in certain cases, stipulates that when attaching a third outer panel to an originally weld-bonded interior panel, technicians must use the original weld locations and not use adhesives. BMWNA says technicians should fit and clamp the third panel without using adhesive, then use resistance spot welding at those locations to join the panels. BMWNA also typically requires applying more spot welds when replacing a weld-bonded joint. To be certain, technicians should check with ISTA for model-specific instructions before starting repair.
An almost universal rule when squeeze-type resistance spot welding is called for as the attachment method for three-layered weld-bonded panel repairs is to not make a repair spot weld over an original spot weld. However, BMW is the exception to this rule when it comes to certain weld-bonded panels.
The rear end assembly of the BMW 7-Series is a conventional structure, for which BMWNA specifies conventional welding. But the B-pillar on the side frame and the sill are made of boron, a UHSS. UHSS when damaged must be totally replaced; no welding is allowed. Beyond the boron, as shown by the section lines, conventional welding attachment procedures are permitted.
0 Comments