Since the wholesale transition to EFI, some of us have forgotten about vapor lock and the subtleties of intake manifold design with carburetors, but many (most?) hot-rod and racing engines still breathe through the mechanical mixture maker.
One of the most common complaints we hear from our friends and customers who own and drive carburetor-equipped vehicles is that their engines are often hard to start after they sit for 20 to 30 minutes subsequent to the vehicle having been driven on a warm day. The engine acts as if the carburetor has flooded and will only start if the throttle is held wide-open. This problem is most often referred to as vapor lock or fuel percolation, and is caused by gasoline boiling in the fuel lines and in the carburetor bowl from exposure to the heat from the engine. Hard starting occurs because the engine is loaded up with the raw gasoline and thick vapors that were boiled out of the carburetor bowl.
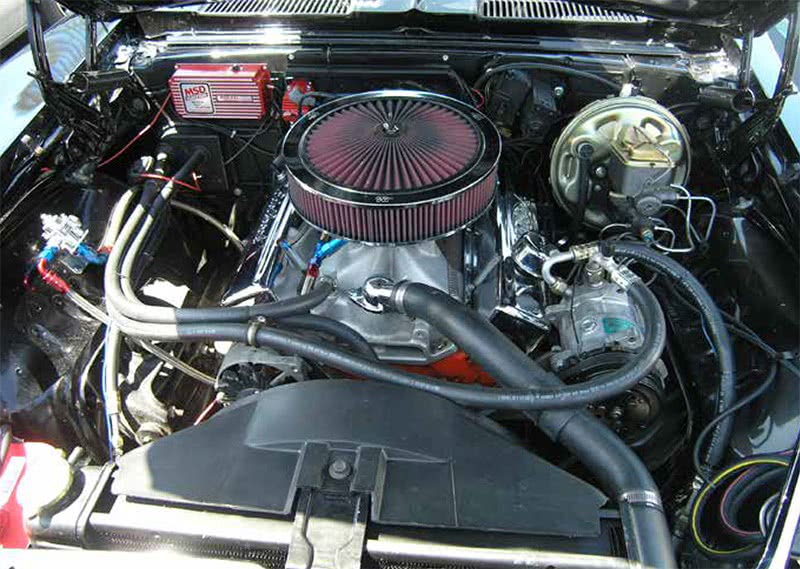
This open-element air cleaner may look very sporty, but it also allows hot air from the engine compartment into the intake, thus reducing the engine’s power.
The heat radiating from the engine and exhaust system can cause underhood temperatures to reach 300+ deg. F during hot soak after shut-down. Gasoline is a mixture of hundreds of different hydrocarbons, which vaporize/boil at a wide range of temperatures. The lighter fractions will begin to vaporize at about 80 to 100 deg. F., and all portions of the fuel should be fully vaporized at about 400 deg. F. This wide range of vaporization temperatures of the gasoline are what makes it a very good fuel for an internal combustion engine. The downside is that when it is in a carburetor that is exposed to high underhood temperatures it will tend to boil, causing the troubles mentioned.
Vapor lock has always been a concern with carburetor-equipped vehicles (especially with an engine-mounted mechanical fuel pump), but it seems to have become more of an issue with today’s reformulated gasoline. Modern fuel-injected engines have very few vapor lock-related problems mainly because the fuel pressure is higher and the gasoline is under pressure all the way from the tank-mounted pump to the injectors. A typical port injection system runs at a pressure of 40 psi or so, while most carburetors receive only about six psi. This higher pressure raises the boiling point of the gasoline — a one psi increase equals about a 3 deg. F. increase in the boiling point.
New blends of unleaded gasoline in many parts of the country contain ethanol, which can often cause swelling issues with the rubber components that are used in the fuel systems of most vintage carburetor-equipped vehicles. Heat only makes this worse, and troublesome and dangerous leaks can result. As we said, when a carburetor is exposed to high temperatures, the fuel in it will vaporize/boil out into the intake manifold and out through the bowl vents, perhaps even dripping down onto the outside of the manifold in the engine compartment. This unburned fuel will not only flood the engine, thus making it hard to start, but any that evaporates under the hood will also become a fire hazard that could be ignited by any flame source, such as natural gas- or propane-fired water heater in a garage.
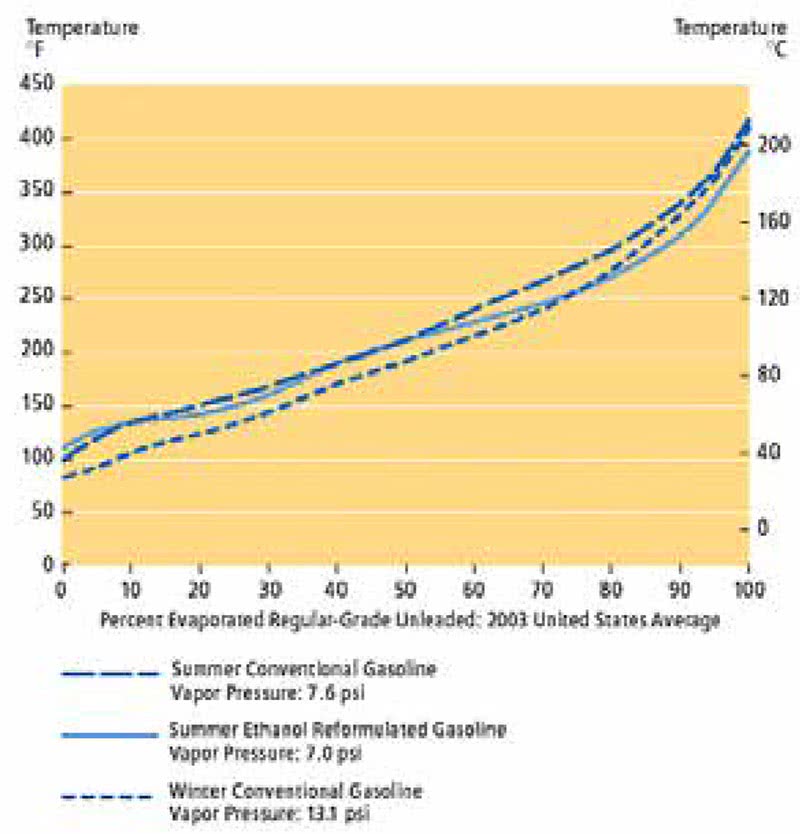
This chart from Chevron shows the percentage of gasoline that evaporates as the temperature increases.
The amount of heat determines how quickly the rubber and plastic compounds used in the fuel system will degrade because the rate of this reaction doubles for every 50 deg. F. rise in temperature. It is always wise to insulate the fuel lines and route them as far away as possible from any heat source such as radiator hoses and the exhaust system to avoid heating the fuel.
Contrary to what you may think, liquid gasoline does not actually burn. It is only the vaporized portions of the gasoline or the vapors that are above a pool of gasoline that can catch fire. EFI engines use exhaust heat routed through the intake manifold to help turn the mist that is sprayed from the injectors into the vapors that the engine can turn into power. The fuel that comes out of a carburetor is in the form of bigger gasoline droplets that need to be changed into vapor so they can burn. The heat, vacuum, and turbulence inside the intake manifold all conspire to do that as the air/fuel mixture is directed to each of the engine’s cylinders. The design of the intake manifold determines both how well the fuel will change from liquid into vapor, and the rpm range at which the manifold will operate best.
So, a carburetor-equipped engine needs enough heat in the intake manifold to convert the fuel droplets it gets into vapor form before the air/fuel mixture enters the cylinders. This need for heat is the reason most original-equipment intake manifolds are heated by the exhaust gasses being chanelled near the intake runners, but if the manifold gets too hot vapor lock problems may occur. There are intake manifolds, such as the Edelbrock AIR-GAP series, that are designed to reduce the heat in the ports, but if they get too cold the gasoline may not be fully vaporized at lower engine speeds.
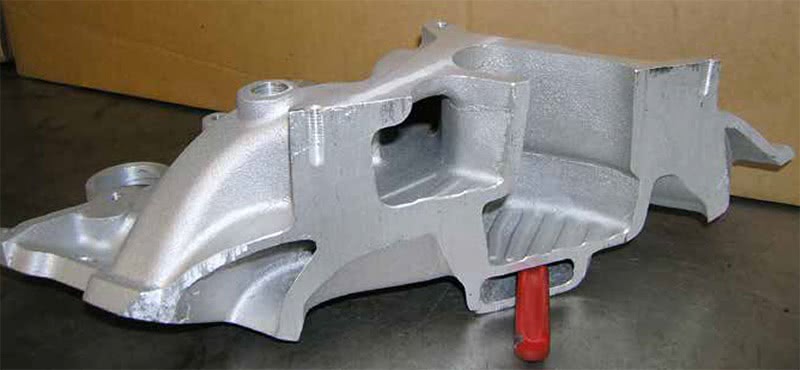
This cutaway of an Edelbrock dual-plane intake manifold shows the exhaust crossover passage that’s used to aid in fuel vaporization.
Manifolds
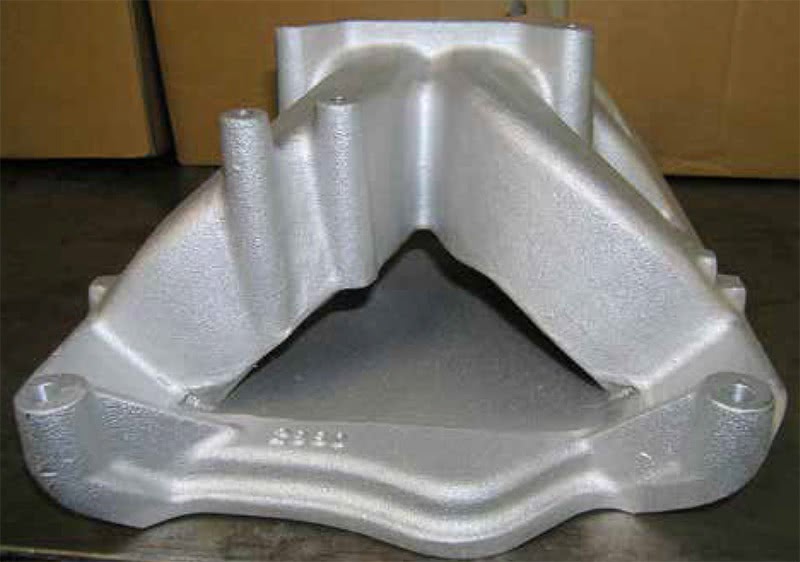
This Edelbrock Air-Gap intake manifold will help the engine make maximum power at high rpm operating conditions.
The main job of an intake manifold is to direct the air/fuel charge from the carburetor equally to each cylinder. The intake manifold and the vacuum created by the engine also have the job of converting gasoline that is still in liquid form (droplets) into a vapor that the engine can properly burn. The factory designed the intake manifold to operate at a wide range of conditions — the engine is expected to perform properly for very conservative driving, and also when maximum performance is required, resulting in compromises. This means that there may well be a fair amount of engine power that can be unlocked if you install a high-performance manifold.
There are quite a few options when it comes to selecting a single-carburetor intake manifold. First, do you want single-plane or dual plane? Then, you need to decide if you want a manifold with an exhaust crossover, or should you try a high performance manifold such as the afore-mentioned Edelbrock AIR-GAP? The dual-plane design is better for lower engine rpm operating conditions, but there are also dual-plane manifolds that are designed for higher rpm operating conditions. Most single-planes are designed for maximum power at high-rpm operating conditions. If maximum power is the goal, the AIR-GAP or equivalent design can offer a power advantage since it helps keep the incoming air charge cooler with the intake runners isolated from engine’s heat. The plenum and runners can become so cool, however, that the gasoline may not be fully vaporized at lower engine rpm and low-load operating conditions.
Vaporization
On the other hand, if the intake manifold to get too hot the engine may experience vapor lock problems, and the heat will also lower the density of the air, which will have a negative effect on the engine’s power and efficiency at higher engine load. It is necessary to vaporize the fuel before it can be expected to burn, plus it is much easier for the intake manifold to properly distribute fully-vaporized gasoline than it is to distribute an air/fuel mixture that contains liquid or non-vaporized fuel. The equal cylinder-to-cylinder distribution of properly vaporized charge is essential for the engine to be able to provide the user with the best possible power, driveability, and fuel efficiency.
If an engine’s air/fuel mixture is not fully vaporized, some of the cylinders may get a certain amount of liquid gasoline, which will not burn properly, while other cylinders will get a charge that does not contain enough fuel, thus is too lean for the needs of the engine. Whenever an air/fuel mixture that is too rich or too lean, or if the fuel is not fully vaporized, the engine will not perform as it should and the exhaust emissions will be relatively high. When the fuel is not properly vaporized, it will not properly burn in the cylinders and it will then go out through the exhaust system as wasted energy and air pollution (unburned hydrocarbons). The conditions that can cause the fuel not to be properly vaporized occur when the air/fuel mixture is traveling at low air velocity (low rpm), low manifold vacuum levels at low rpm (bogging the engine), an intake manifold with large runners (at low rpm operating conditions), a carburetor that is too large (CFMwise) for the operating conditions, or summer fuel blends used during winter conditions.
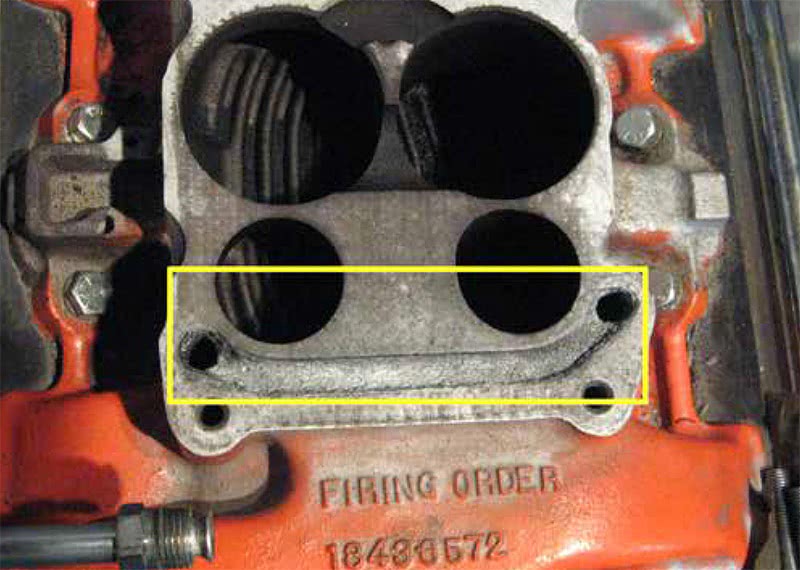
General Motors used exhaust gases to aid in fuel vaporization, but this tended to overheat the carburetor and led to vapor lock problems.
In the 1950s and 1960s, General Motors designed many of its V8 intake manifolds with exhaust gasses that passed across the base of the carburetor to prevent carburetor icing and to help vaporize the fuel, but since today’s gasoline is designed mainly for fuel-injected engines, it may be advisable to consider blocking off the exhaust passages that pass by the base plate of a carburetor, and, in some cases, reduce the exhaust flow thru the intake manifold’s exhaust crossover. Blocking the exhaust crossover of an intake manifold, or the use of an AIR-GAP-style manifold can cause engine warm-up problems and reduce the fuel’s vaporization during chilly weather conditions, which can reduce an engine’s driveability, thus making the vehicle miserable to live with.
Chrysler, Ford, and GM all started using thicker base gaskets and/or heat shields under the carburetor to help reduce the fuel temperature on their carburetor-equipped engines starting in the late 1960s. The use of a plastic or phenolic carburetor spacers to help keep the carburetor cool is also a good idea to consider as long as you have the hood clearance to allow it. Carburetors spacers can also be used as a tuning aid to move the torque and powerband down to where it is more usable. A four-hole carburetor spacer (four individual holes — one under each barrel) will increase your throttle response and acceleration because it will allow more time for the fuel to mix with the air before it has to make the turn toward each cylinder’s intake runner. The use of this kind of spacer in most cases will improve the engine’s torque and power in the lower rpm ranges. An open carburetor spacer (one big hole under the carburetor) will move the torque and power-band up in the rpm range by increasing the plenum area of the intake manifold.
Density
The density of the air is a very important factor in both how much power an engine will make and the jetting package an engine will need to perform at its best. The computer or PCM of a modern fuel-injected engine uses the data it gets from the air temperature and mass air flow sensors to calculate the density of the air, then it goes to its look-up tables to determine what ignition timing and fuel injector pulse-width command should be used for the engine load and rpm at which the engine is being operated. Serious racers or tuners of carbureted engines should have a competition weather station such as the Computech Race Air Pro to help them tune engines for changes in temperature, humidity, altitude, and air density. Most carbureted engines get their air from under the hood, but those air temperatures are not ideal for maximum engine power and efficiency because the air has been heated as it passes through the radiator and over the hot engine components. A typical engine will experience a 1% loss in engine power for every 11 deg. F. the intake temperature increases.
The larger the carburetor venturi size, or the larger the size of the intake manifold runners, the lower the velocity of the air/fuel mixture. This can cause a loss of engine power because the fuel will not be fully atomized/vaporized and/or properly mixed with the air charge as it enters the cylinder heads and combustion chambers at lower rpm operating conditions. High performance (long duration) camshafts and cylinder heads with large runners (race heads) will also add to the problem.
Driving an engine on the street that has been built for maximum power at high rpm is not for everyone — the engine may stumble and stall when driven “normally,†plus it will most likely lack power at lower rpm, but will have tons of power in the higher rpm band. When you select or build an engine for the way it will be driven most of the time, the vehicle’s driver will be a lot happier than he or she would be if the engine only ran good at wide-open throttle!
by Henry P. Olsen
Good, accurate information given in this article. I have experimented with carbs and intake manifolds and find the facts stated here to be spot-on! luckyuhaul.