by Kerry Jonnson
When it comes to racing, initially large chunks of horsepower are made and lap times drop quickly on that first day at the track. By day three, the improvements have dropped to 0.1 second if you’re lucky. Will lightening your flywheel give better lap times — or just another 0.1 second? And will the car still be “streetable†after this mod?
You might be wondering what you can do next to your engine to pick up faster laps. You have already installed high-performance camshafts, and maybe free-flowing intake and exhaust to improve breathing. You may have even fitted high-ratio rockers with double and triple valve springs. Pretty exciting stuff, but how about putting that power into the driveline and on the ground?
Whatever you envision as your next step, we strongly recommend you make gradual improvements to the entire system, rather than wholesale individual changes, to avoid any unintended consequences that might not sit well with your all-important power plant.
Let’s take a look at the engine when it’s out of the car. Perhaps you’re thinking the next modification is going to be the clutch and maybe the flywheel — say, your clutch just went, and, besides, you just did the engine over. Whatever the reason, you’re thinking about racing clutches with multiple “pucks,†high-pressure pressure plates, and of course, a new throw-out bearing. Yes, it is important to apply all the horsepower the engine can make to the ground, and it has to pass through the driveline. Here, we’ll look into getting the right clutch, and maybe lightening the flywheel.
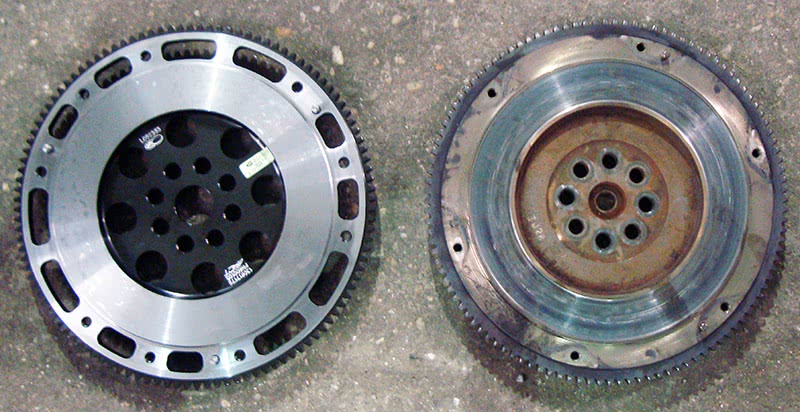
Will the huge reduction in rotating mass represented by the installation of that high-performance flywheel have negative driveability consequenses? After all, the one on the left weighs about 75% less than the stock unit on the right.
You’ve done your research and settled on a high-performance clutch, but in your research you see you can also upgrade to a light-weight flywheel. What will that do for you? There are many myths spread around by people who just don’t know the physics behind a high-performance engine and drive train. We will try here to dispel most of these myths, but you must keep in mind that a lot of what you feel as you drive your car is your own personal interpretation. What is “streetable†to you may be an awful commute in traffic for someone else. So, we’ll take a look at the pros and cons of these modifications.
While researching a stronger clutch and possibly a light-weight flywheel, you’ve seen advertisements for Stage 1, Stage 2, and Stage 3 mods, maybe even a Stage 3+. Sounds alluring, but what are the realistic options for a light flywheel? You have probably read that this can increase horsepower, but can make the car very difficult to drive in traffic.
Light Flywheel Equals No Boost for Horsepower
Well, truth be told, a lighter flywheel will not increase horsepower — we repeat, a lighter flywheel will not increase horsepower! It may change your horsepower curve slightly, but the peak horsepower will remain the same.
Think of your engine as an air pump. The more air it can move through the cylinders, the more power it is capable of making. If you can keep air intake velocity up, get the ignition curve to match airflow, and get rid of the spent gases as fast as possible, you can produce large amounts of horsepower, but the weight of the rotating mass won’t affect it as long as it’s within reason.
Lightening the load, however, does have its advantages. A lighter crankshaft will contribute to quicker crankshaft acceleration, and also reduce the load put on the rear main bearing and seal. The job of a flywheel is to dampen pulses that occur between cylinder firings, and smoothness is a big concern with production engines. A robust crankshaft makes for smoother power delivery and smoother shifts in a vehicle equipped with an automatic transmission — this is important to most commuters, but chances are if you’re just commuting you’re not reading this anyway.
The weight of a stock flywheel is typically something like 36 pounds. There are outfits that will re-machine an existing flywheel to make it lighter, and you might want to consider this and save the expense of replacing it. We decided to see what would happen if we went to an ACT XACT Prolite light-weight flywheel that weighs only 8.7 pounds, roughly only 24 percent of the stock flywheel. Sounds like a drastic change, but if you calculate the weight of the entire rotating and reciprocating mass of crankshaft, connecting rods and pistons the percentage is smaller.
Allows Crankshaft to Spool Quickly
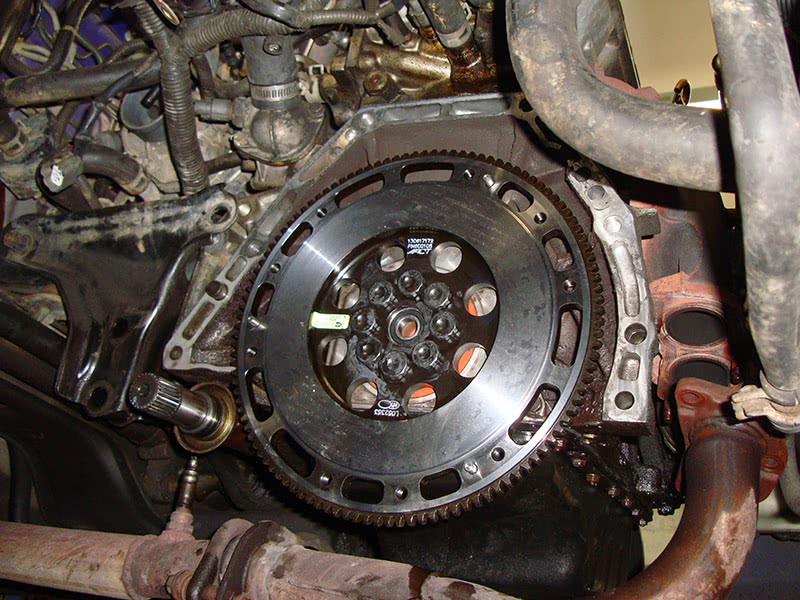
Here, new ARP bolts are being used to secure the flywheel to the crankshaft. These should be torqued down to ARP specs. The company also supplies a thread lubricant to ensure proper torque. You also might notice the new rear crank seal hiding behind the flywheel (orange).
Lightening the load of our rotating mass will allow the crankshaft to spool up quicker, and this means you are going to notice the improvement mainly while under hard acceleration. Look at the type of driving you do and how much WOT you do. It can be argued that if it is drag racing, or just street performance driving, you are doing, this does not involve enough time accelerating to make lightening the flywheel a cost-effective performance improvement.
It will be difficult for all but the most dedicated racing enthusiasts to quantify the performance gained from a lighter flywheel. Conventional theory and common sense tell us there will be an improvement, but it is probably something you will only notice on a stop watch during timed laps at a racetrack. We’re not saying it’s a waste of money, we’re just warning you that you may only notice a small change in performance. On a racetrack with many opportunities to accelerate out of a corner, for instance, the effect will be cumulative and you should be able to decrease lap times.
Mounting Bolts Distribute Shock Load
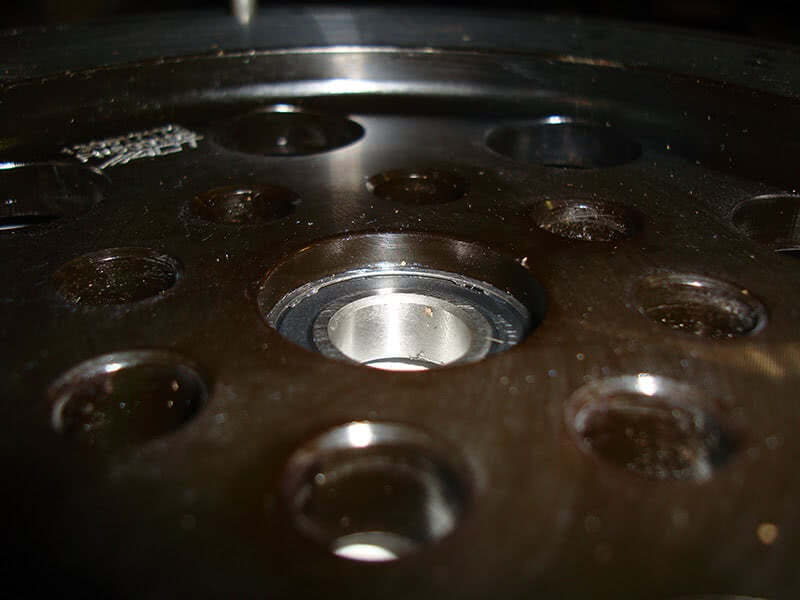
The clutch kit purchased comes with everything but the Prolite flywheel. Make sure to install or press the pilot bearing all the way in until it is fully seated up against the lip of the new flywheel.
The stock flywheel uses only six mounting bolts to mount the clutch to the flywheel. The Prolite flywheel we installed upgrades this to nine mounting bolts. This helps distribute the shock load. We went with ARP high-grade bolt kits for both the flywheel and clutch to feel confident in the strength of our fasteners. ARP makes an eight-bolt kit for the flywheel and a nine-bolt kit just for the clutch upgrade. You can find new torque specs on the website.
With our new flywheel, we of course installed a new pilot bearing. No sense having your input shaft wobbling around under hard acceleration stressing out the input shaft bearings. The pilot bearing is pressed into the flywheel, and make sure you have pressed it in all the way and it is fully seated up against the lip. Whether you are using a bearing driver kit or a hydraulic press make sure your tool is only applying pressure to the outside bearing race to avoid stressing the bearing.
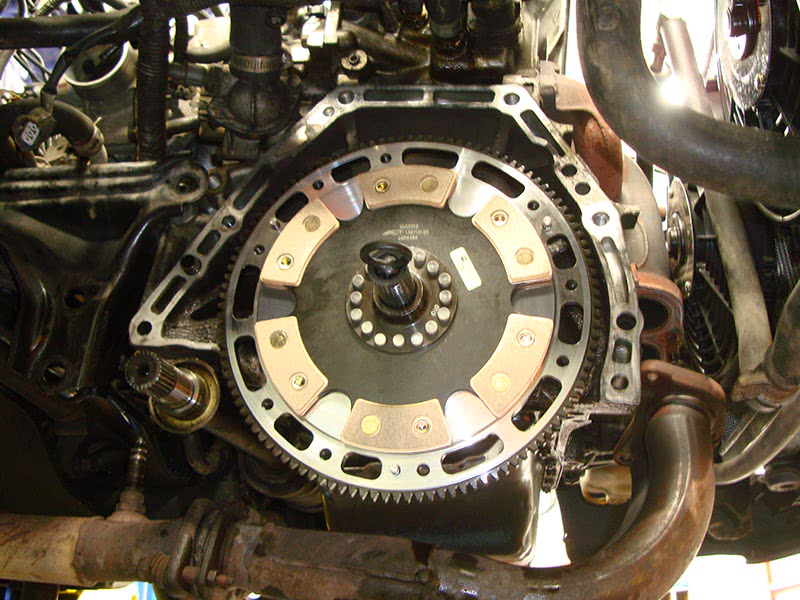
The kit comes with the tool to center the clutch ceramic element plate. The six ceramic pucks means this clutch is going to grab quickly and is not make to “slip†in. Make sure you have cleaned the metal surface of the flywheel before installing the clutch plate, then clean the surface of the pressure plate before you install it.
We noticed no significant difference in drivability with the Prolite light flywheel during regular driving — the clutch had a much bigger effect on drivability. Of course, we also upgraded the clutch at the same time we did the flywheel, opting for an ACT Sport/Race Ridge six-puck unit with ceramic friction material. This may seem like overkill on what at this point is a fairly mild engine, but we are just starting to make powertrain upgrades and the car needed a clutch anyway.
ACT does not recommend using these rigid-ceramic-puck design clutch discs for spirited street driving. The engagement point, with a thinner design pedal, will feel lower and the ceramic pucks with a harder material will also be harsh — this can definitely change your commute. Also, the rigid clutch does not have a spring set to protect the transmission input shaft from the shock of acceleration, and the entire driveline is going to absorb that shock. You can purchase a four- or six-puck ceramic friction clutch assembly with shock absorbing springs from the manufacturer to counter this.
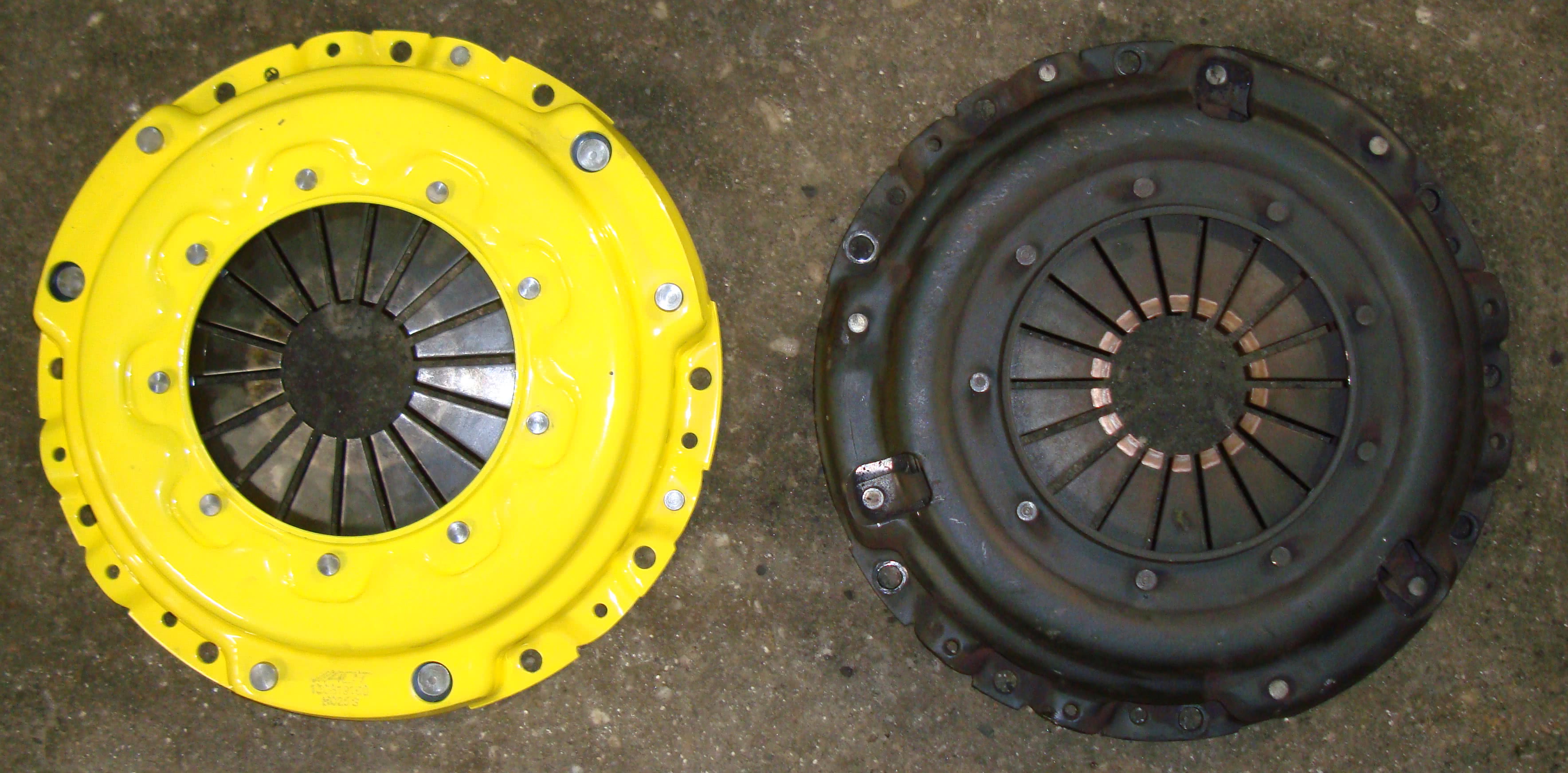
This is what makes a clutch a clutch. The spring pressure provides the clamping force to transfer the power from the crankshaft to the gearbox input shaft. We opted for the rigid disc with a torque capacity of 280 ft. lbs., this for the moment is more than the engine produces. As far as weight goes, ACT states its clutch assembly weighs about the same as the stock unit.
Pressure Plate Clamping Ability Crucial
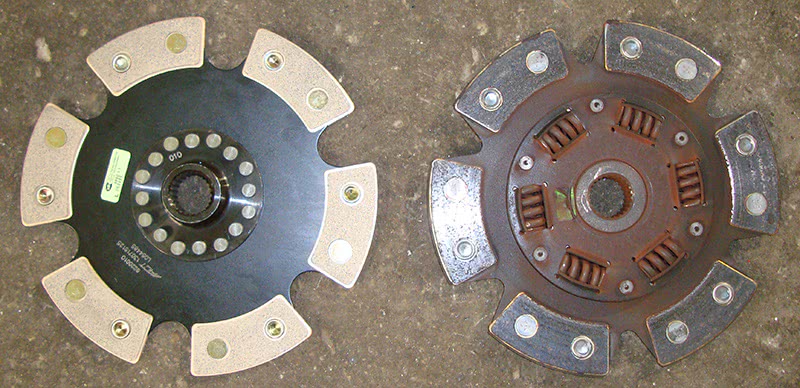
Although an upgraded six-puck clutch plate had been previously installed in the vehicle, we opted for the rigid design this time. The old clutch had springs to absorb some of the shock to the driveline when the clutch engages, which changes the weight of this part of the clutch assembly. This is more of a racing set up, and you will notice this during clutch engagement.
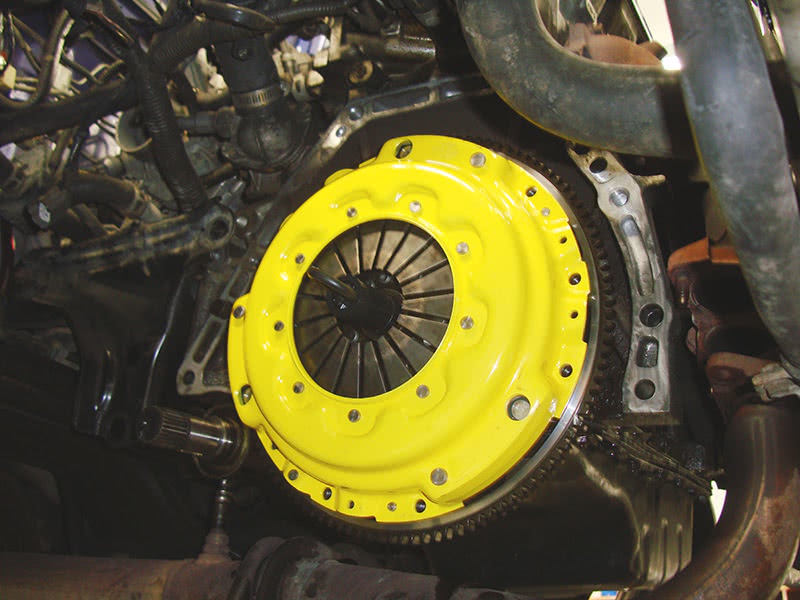
Our new flywheel and clutch combination fits flawlessly, but something we did not anticipate is that the new flywheel and clutch use nine mounting bolts to hold it together, three sets of three 120 degrees apart. The stock set up used only six. You could use the six bolts and leave each middle bolt hole empty in the set of three to maintain the balance, but that is simply out of the question. The whole idea of staying with the same manufacturer was to save time and money on balancing the whole package together.
Just as important as the friction clutch disc is the pressure plate. Most manufacturers supply a wide range of clamping abilities. ACT, for example, offers pressure plates with clamping forces that can handle anywhere from 175 to 1,010 ft. lbs. of torque for single plate clutch designs, and up to 1,500 ft. lbs. for dual-plate clutches. The one we installed here is the A14-SPRsix, which is rated for 280 ft. lbs., way more than we really need at this point in our engine’s transformation. Remember, with a rigid clutch plate, engagement is going to be harsh to begin with, and the increased clamping force needed to handle more horsepower also requires more spring pressure and therefore increased pedal effort — a clutch with clamping force capable of handling up to 1,500 ft. lbs. would be a bear to drive in traffic.
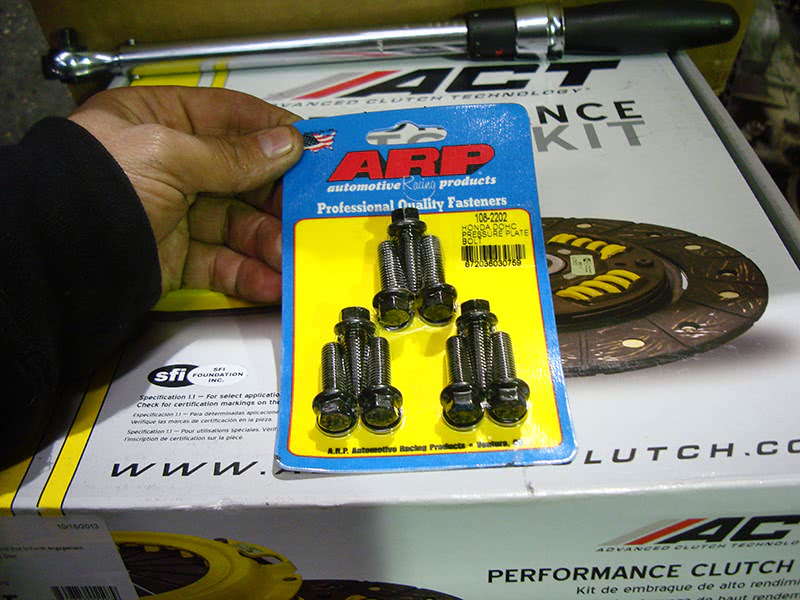
ARP makes the perfect bolt kit because most upgrades use nine bolts to secure the clutch pressure plate to the upgraded nine bolt flywheel. High-grade bolts will do a much better job of securing the clutch pressure plate under heavy acceleration.
We wanted the clutch kit to match the flywheel. Both the flywheel and the clutch are balanced and we felt we might be able to save a step and not need to have the clutch and flywheel balanced together. If you are mixing and matching clutch components, or just replacing the clutch disc, you should have everything balanced together — especially if you are dealing with a small-displacement, high-rpm engine.
You don’t need us to tell you that out of balance components will cause vibration and excessive wear, and could even lead to total failure. Installing a lightweight flywheel will be more noticeable on the track than in street performance driving. The type of clutch material and spring pressure (torque capacity) used will have a much greater effect on drivability, if you use your car both as a driver and an occasional strip/race machine.
Â
0 Comments