So far we’ve looked at the components that supply the pinching force and the ones that spin off all that heat. Here we’ll talk about the interesting subject of lining “recipes” and what you should choose for your hot car or truck.
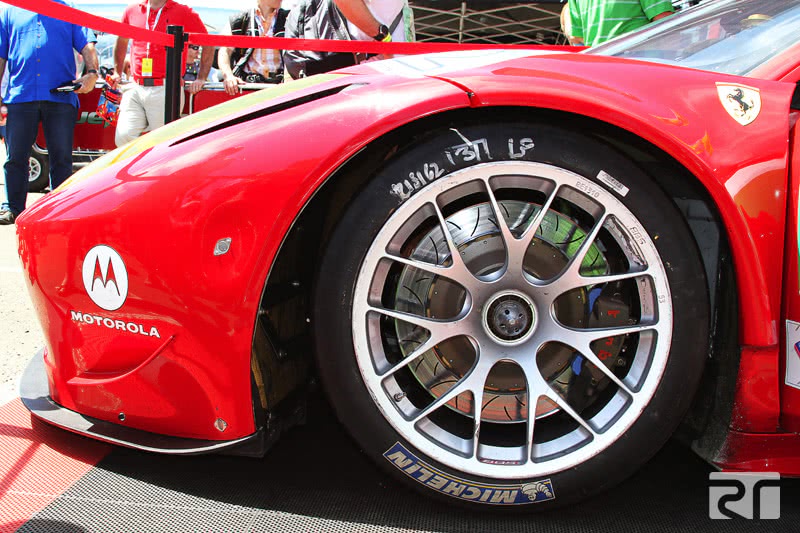
What’s in your caliper? You can bet the big Brembos on this Ferrari are loaded with pads that bear lining material exactly matched to the job (courtesy Brembo).
If you were around cars (or around at all) before the wholesale adoption of disc brakes in the mid-1960s, you might remember a couple of attempts at making drum brakes less apt to fade in heavy use. The first was sintered iron shoes (you could call them “full-mets”), which were used in some Corvettes, on highway police pursuit cars, and in racing. They handled heat quite well, but until they got warmed up you needed both feet on the pedal to stop at the end of your driveway. Then there were the expensive finned-aluminum drums with iron wear surfaces that appeared around 1960 on certain Buicks and Pontiacs. No amount of lining materials change or engineering, however, could overcome the basic drawback of the drum brake: It’s not good at shedding heat. After all, if you need to keep something hot you could hardly do better than to put it in what’s essentially a Dutch oven.
No, disc brakes represented the design departure that made safe deceleration from high speeds, especially repeatedly, a practical proposition. They had other advantages, too, such as much lower sensitivity to immersion in water, fewer pesky parts to deal with during a reline, and the pads in those heavy early multi-piston calipers seemed to last forever.
The resistance to this technological shift in the service business and among tradition-bound auto experts was almost humorous. It was said, for example, that only dealerships would be able to work on these new-fangled decelerators — independent garage “mechanics” simply couldn’t deal with them. Well, we don’t know about you, but we’ll race you any day hanging pads while you install new shoes and fiddle with all those springs, star wheels, levers, and cables.
For 15 years or so, however, disc brakes used the same old asbestos for lining material. Then, two things happened. First, the dust from that fibrous mineral whether in brake-component factories or service shops was linked to serious lung disease. Second, as brakes were lightened and downsized in the quest for fuel efficiency, and cars got overdrive and were made more aerodynamic so that they didn’t slow down as much when you took your foot off the gas, we needed a better material anyway to combat the dreaded fade.
Never-ending quest
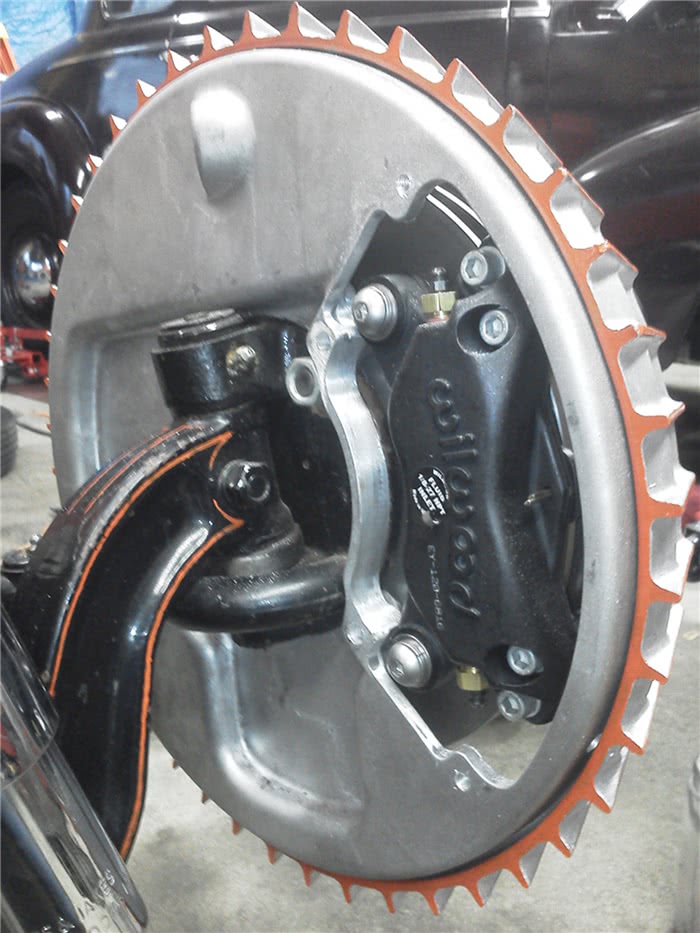
What the heck is this all about? This ’27 Model T rod looks like it has 1960-style Buick finned aluminum drums. But wait. There’s a Wilwood caliper sticking through the backing plate, and you can see a disc if you look closely. So, the fins are just very cool window dressing (courtesy Richard Rossi & Wilwood).
The history of the quest for the ideal friction material has been sort of like a drawn-out version of Thomas Edison’s search for a suitable light bulb filament. All kinds of things have been tried since the automotive era began 120 years or so ago. The spoon brakes used on the first cars usually had wooden blocks, but they were sometimes supplemented with a leather lining. External band‑type brakes were either metal‑to‑metal, or used wood or leather, too. The earliest drum stoppers (invented by Louis Renault in 1903) had iron shoes against steel, then some strange materials were used, such as the walrus hide linings of the English Wolseley.
The credit for first taking a scientific approach to friction materials goes to an Englishman, Herbert Frood, and Ferodo, the company he started early in the 20th century, which is still going strong as part of Federal-Mogul. Using a water wheel‑powered friction test machine, Frood experimented with numerous materials (even cotton!) and bonding agents in 1879 (no cars yet, but there were many potential industrial applications) . In 1902, he hit upon resin‑impregnated woven asbestos reinforced with brass wire, and the era of safer stopping began.
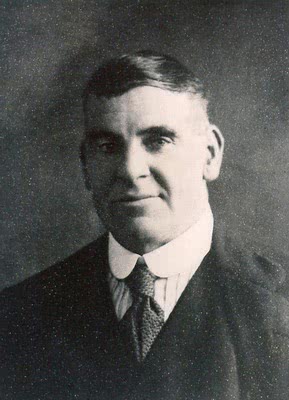
In 1873, Englishman Herbert Frood was the first to take a scientific approach to developing brake friction material (courtesy Ferodo).
We’d better get our terms straightened out before we go any further. In the brake business, asbestos linings were called “organic,” which is really a misnomer since only something derived from living organisms fits the dictionary definition of the word. It’s applied to asbestos because it occurs naturally. Now, with all kinds of unusual materials being used, organic has come to mean anything that’s not metallic or ceramic.
Semi‑mets were the first step. Basically, these are steel wool, iron powder, and other metal particles molded together with a phenolic resin binder. They’re very good at handling heat, but early recipes had big problems with noise and tended to eat rotors and drums.
As a spokesman for one of the major aftermarket brake parts manufacturers says, “The early replacements for asbestos were very aggressive on rotors, very noisy, and very challenging.†Those of us who were around then remember the distress all that caused very well.
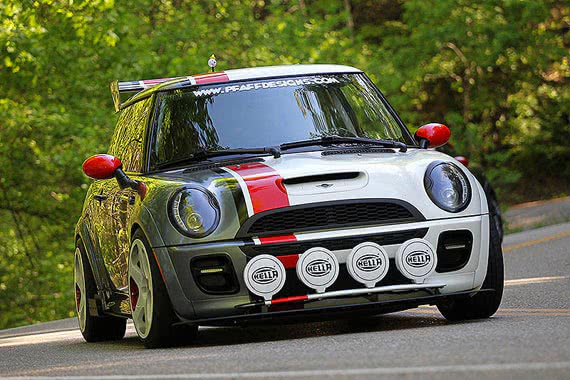
If you’re not exactly racing, but instead engaging in what the Brits call “sportive motoring” on challenging roadways such as the Tail of the Dragon in the Smoky Mountains, you’ll still appreciate the sense of security and the great feel of high-performance linings. This Mini Cooper has EBC Redstuff pads, which did great in all the tight curves and steep downgrades (courtesy EBC).
Then came non‑asbestos, non‑semi‑met linings, called “NAO” (Non‑Asbestos Organic ‑‑ there’s that term again). All kinds of mixtures containing such things as aramid/Kevlar, fiberglass, carbon fiber, nut shells, different kinds of metal wire and particles, etc. are used, the goals being long wear, good friction characteristics, preservation of rotors and drums, and quiet operation, which they accomplished to a greater or lesser extent.
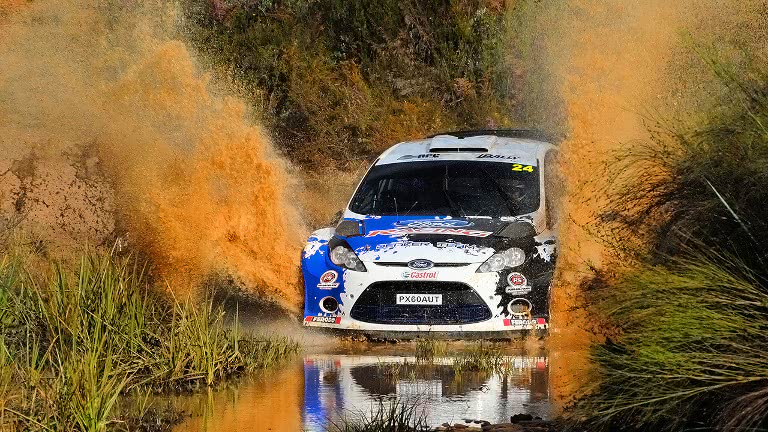
Frood’s company, Ferodo, is still going strong making O.E.-quality and premium performance linings, such as the ones on this rally car in South Africa (courtesy Ferodo).
Then something most of us would’ve considered far-fetched appeared: ceramic friction material. When we first heard of this back in the 1980s, we visualized bricks or chunks of concrete against the poor rotors, and wearing them down fast and relentlessly. We quickly learned, however, that ceramics have lots of positive benefits, enough so that most linings on the road today are on this material basis. They’re actually kind to rotors, very quiet, and make little dust to spoil the looks of those beautiful wheels. They contain a high percentage of ceramic fillers along with a non-ferrous metal, such as copper.
Now, regulations are appearing in Washington State and elsewhere that are forcing friction material makers to phase out copper and other metals — it’s said that they’re dangerous to fish! The manufacturers are making adjustments to meet the regs, and some have been successful already.
Fade is the most dangerous among many other factors
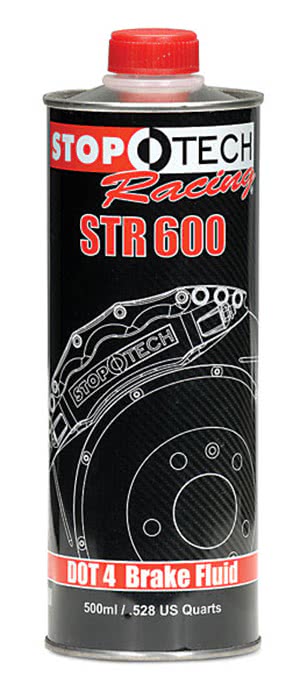
Since boiling fluid caused by overheated brakes will cause a truly terrifying type of fade, as in pedal to the floor and no decel, you can switch to something like this 600 deg. F.-rated DOT 4, and change it regularly (courtesy Stop Tech).
While we discussed fade in the last installment, it bears repeating. Normally, it won’t be a big issue in one instance of hard decel even with stock brakes. It can sure get scary, though, with more than that, or when trying to keep control on long downgrades, say in the mountains. When it occurs, even the strongest human leg muscles won’t stop you.
“Out-gassing” from the evaporation of the chemicals in the resins that hold lining materials together was implicated in the past — it made the linings “aquaplane” over the disc friction surface. That phenomenon, however, has been mitigated in modern high-performance pads from reputable manufacturers, and a proper “bedding-in” procedure (we’ll get to that a little later) also helps.
Still, you’ll be apt to experience less braking power and a pedal feel that doesn’t instill confidence if you’ve chosen linings that aren’t formulated for the kind of driving you’re doing, say road racing where rotor temps may exceed 1,000 deg. F. If you do manage to overheat your brakes, it can cause even high-quality, high-temp friction material to break down and “smear” onto the rotor
Boiling fluid is another likely cause of frightening fade during heavy-duty braking, as in pedal-to-the-floor fade. We have a feature planned on that topic for a future issue of HRP, so all we’ll say here is that you should change that hydraulic medium frequently. Why? Because at less than 4% water, the boiling point of regular DOT 4 drops over 130 deg. F. That may sound like a lot of moisture, but we’ve taken samples out of cars that were 40% water.
And so to bed
Perhaps because in the old days linings were supplied “green,” or “raw,” there are still plenty of fallacious opinions out there about how new linings should be bedded in. As one aftermarket brake expert puts it, “It’s not unusual to see a perfectly good brake job ruined in the first five minutes by improper break‑in.” Or, as Wilwood’s tech literature says,
“Remember, the proper break-in of pads and rotors is extremely important. Not doing it properly can cause permanent damage to rotors and adversely affect overall brake performance. Pads and rotors interact with each other to provide efficient brake performance. The break-in or bed-in procedure is done to condition the pad/rotor interface. Depending on the pad being used, more or less pad material is uniformly transferred onto the disc as a thin film. The resins and bonding agents in some pads need to be heat cycled to work properly as well. By not properly bedding in pads, uneven pad material deposits can occur that may cause a vibration. Improper wear characteristics may also show up on either the pads, or rotors, or both.”
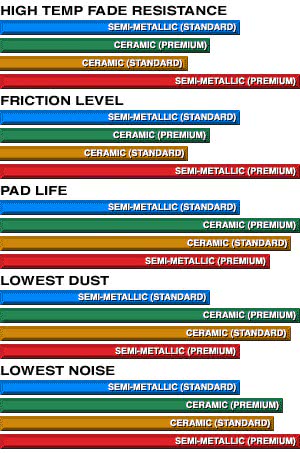
Here’s one brake parts company’s comparison of semi-mets to ceramics, both standard and premium. Others may disagree, but you get the idea (courtesy cquence).
Some high-perf linings are “scorched” before delivery, meaning they get a super-heating process that forces any uncured bonding agents and impurities out of the friction material and pre-burnishes the pads to accelerate break-in and enhance consistent performance, cold or hot. Others are given special coatings that are supposed to do the same thing, but neither is justification for neglecting a sensible bedding-in procedure, to wit:
- As long as it’s not deeply grooved and doesn’t have enough DTV (Disk Thickness Variation) to cause pulsation, a used rotor’s surface is the best thing to get new linings started on, believe it or not.
- After installing the new pads, you do always pump the pedal a few times before moving the car, right?
- Take it easy! Drive where there’s no traffic, and do a series of light decels — three to five seconds each, with maybe 10 seconds between — to generate the initial heat. A dozen or more of these is good.
- Follow that with numerous firm stops to continue heating the brakes. If you feel any fade, drive for a while at cruising speed without touching the pedal to cool things down.
- Get ‘er up to 60 mph or so, and brake hard down to 25. Speed back up to 60 and drive for at least 15 seconds before braking hard as above. Repeat this 10 times. Again, if you sense fade at any point, cruise for a few minutes.
- Park it and leave it alone.
NOTE: DO NOT sit stopped with the pedal applied at any time during this process as it may cause “pad imprinting” wherein a thin layer of lining material is transposed onto the discs. This can result in pulsation.
That last note brings up the fact that almost all linings are “adherent,” meaning they are formulated to transfer a layer of material evenly to the rotor’s wear surface. This layer provides optimum braking performance, and anything that interferes with its formation should be avoided.
Suppose you install high-performance pads, but you never drive aggressively enough to get them up to their optimum operating temperature. The proper transfer of material won’t occur and you’ll end up with bumpy braking and poor performance. Once again, correct bedding in for the chosen material is the answer.
Practical points
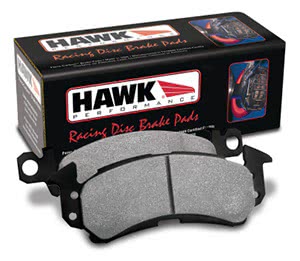
Reputation, reputation, reputation. If you choose high-performance pads from the selection offered by well-known and respected manufacturers, you’ll know their characteristics beforehand. One big problem: counterfeiting. Be very sure of your suppliers (courtesy Hawk).
So, what should you do? It all depends on the kind of driving you’re actually going to do. Get over any delusions of grandeur you may have — if you’re not really going racing, you don’t need (and shouldn’t even want) true racing pads. If you put them on your car, you’ll get a hard pedal, poor stopping when cold, and noise, and you’ll eat up those rotors. Plus, you will have spent too much money.
That doesn’t mean you shouldn’t upgrade to high-perf street linings. They’re great protection against fade, and you can live with them. They may do all you want without the need for a “big brake kit.”
The best advice we can give here is to research, research, research. Go to the sites of all the best-known performance brake manufacturers and read their tech literature, paying special attention to what’s suggested for the kind of use you intend for your vehicle — realistically.
Â
0 Comments