You may be thinking a big radiator and an auxiliary fan, but there’s more to this challenge than that.
One of the more common complaints that owners of vintage cars and hot rods have is that their car’s engine runs too hot in warm weather. Perhaps the stock cooling system was marginal to begin with, or the installation of a larger, more powerful engine has sent it over the edge. They have already replaced the radiator and the water pump, and added a pusher electric radiator fan to help the stock fan, but none of that seems to be helping. The main questions they have are, “Why is the engine running so hot,” and, “What can be done to solve the overheating problem?”
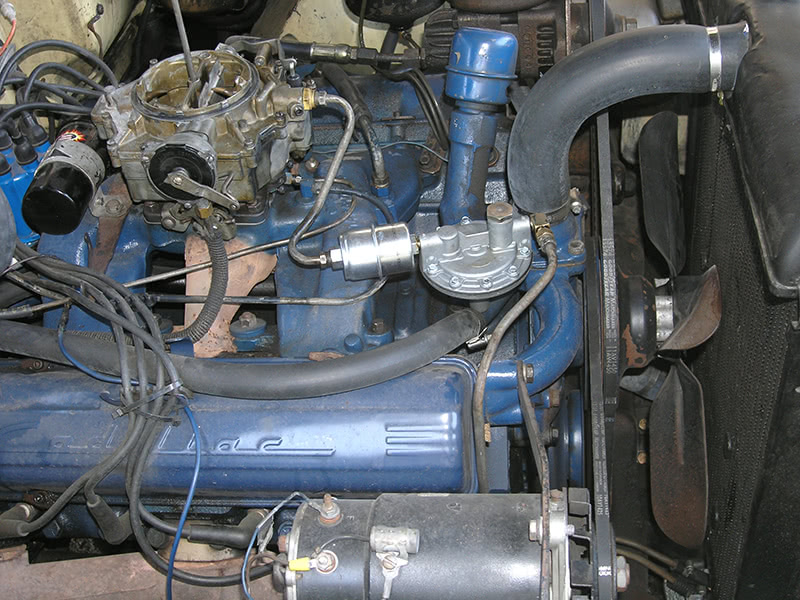
The stock cooling fan did an adequate job back when this 1956 Cadillac was burning leaded gasoline, but in recent times the engine started overheating whenever the weather got warm.
Among the many issues we’ve found in our shop are such things as an electric fan blowing the wrong way, a bad thermostatic fan clutch, a faulty radiator cap, or large air gaps around the radiator that allow the cooling air to go around, not through. Also, when a vehicle is overheating and everything in the cooling system is functioning as it should, the problem may not be due to shortcomings in the cooling system, but is more likely because the engine is creating too much heat in the first place. Perhaps the air/fuel mixture and/or the amount of ignition spark advance isn’t right for the application.
Btu removal
An internal combustion engine burns gasoline to create motive power, but only maybe 25% of the energy that is in the fuel is actually converted into the power that moves the vehicle down the road. The rest of the energy in the gasoline becomes the heat that is dissipated from the surface of the engine, is pumped out with the exhaust, or goes into the cooling system and is thus wasted.
The basic rule operating here is that any cooling system seeks thermal equilibrium. The first law of thermodynamics (a function of the conservation of energy principle) states that a high-temperature medium (coolant) will transfer heat to a cooler medium (air flowing through the radiator’s fins and tubes), and this transfer will continue until equilibrium is achieved.
Depending on the temperature and speed of the outside air flowing through it, the radiator should remove about 25 to 50 deg. F. of heat from the coolant. One way of checking to be sure the radiator is doing its job is to use a non-contact infrared pyrometer to measure the temperature at both the inlet (at the top) and the outlet of the radiator. If the inlet temperature is 185 deg. F., the outlet should read in the 135 to 160 deg. F. range.
Assuming the radiator is in good shape, if it’s not removing enough heat from the coolant you should be sure that the air flow over its fins and tubes is adequate. Any gaps around the radiator that would allow air to flow around instead of through the radiator should be sealed so that the movement of the relatively cool outside air from the vehicle being driven and the action of the cooling fan will do the most good. We have also worked on vehicles where the air flow through the radiator is good, but the engine compartment is so crowded that the air cannot flow out sufficiently and is trapped. In a case like this, you could try driving the car without the hood. If the engine run cooler then, you may need to consider louvering the hood or wheel wells to allow the hot air to escape, facilitating the breeze through the radiator.
The flow of coolant must also be unimpeded. The only purpose of a thermostat is to promote the achievement of normal operating temperature as quickly as possible, to maintain it, then to get out of the way. There’s a persistent myth left over from the Ford flathead days that if the liquid medium moves through the radiator too fast, it won’t have enough time to give off its heat sufficiently, but a little thought explodes it. It’s in a closed system, after all, so in an ideal world the temperature would be the same throughout. Since nothing’s 100% efficient, however, that’s never going to happen. Temperatures vary dramatically in the various passages, chambers, and tubes.
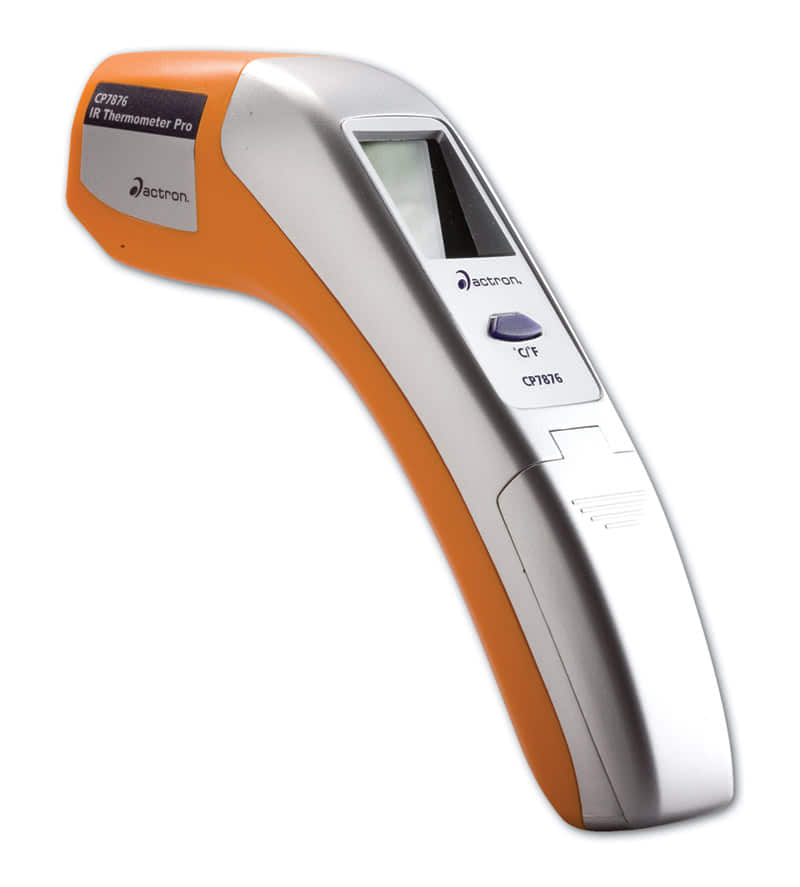
A non-contact infrared thermometer/pyrometer allows you to find out whether or not the radiator is removing enough heat from the coolant.
If you restrict flow, the coolant will stay in the radiator longer and will indeed get cooler than that in the water jacket and heads, but that means it will also move more slowly through the engine causing hot spots to develop, possibly to the point of boiling and even to internal damage. In the old high-capacity (typically 22 qts.!), low-pressure (four to seven psi) flathead, at high rpm the twin water pumps would often overcome the radiator cap’s rating and water would be forced out leaving the system low and causing overheating. Also, some added backpressure in the block helped control localized boiling. That ancient history, however, doesn’t apply to engines produced in the last six decades or so.
The radiator cap is used to increase the pressure in the cooling system — every psi increase adds an additional three deg. F. to the boiling point. So, a 15 psi cap increases the boiling point of the coolant by 45 deg. over that of a system that’s open to the atmosphere.
By the way, always use distilled or deionized water to mix with the antifreeze because tap water contains minerals and often chlorine that can cause deposits and corrosion in the cooling system. A 50/50 mixture of water and antifreeze concentrate works the best for transporting heat and increasing the boiling point. Of course, it also lowers the freezing point. A water “wetter” agent added to the coolant can also help it remove heat because it keeps air bubbles from forming.
Spark timing and air/fuel mixture
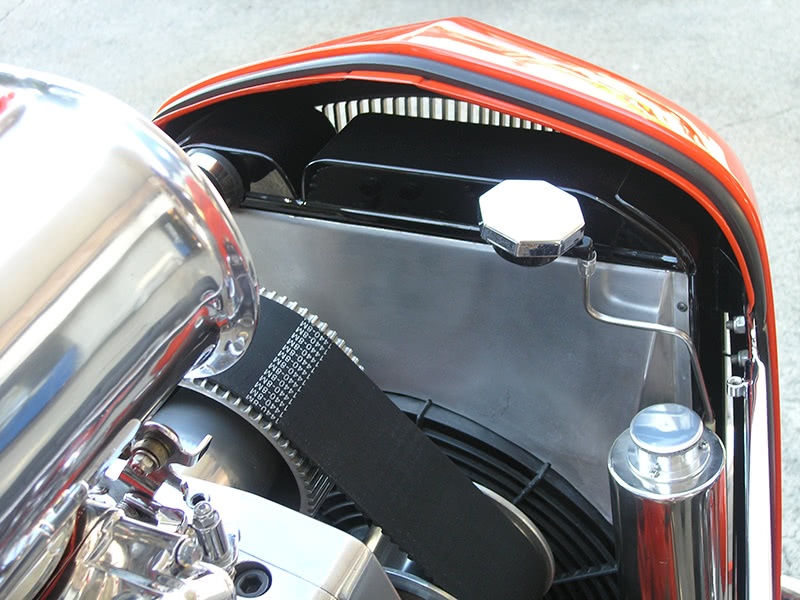
The air gap above the radiator of this supercharged street rod is allowing cool air to flow around the radiator instead of through it.
Also important for cool running is the correct ignition spark advance curve and the proper air/fuel mixture for all the load conditions the engine will see. A primary rule in performance tuning is to tune the spark timing before you tackle the air/fuel ratio.
The ideal spark timing will cause the engine to have maximum cylinder pressure when each piston is at about 12 degrees after top dead center, which will allow the engine to operate at maximum efficiency. This ideal spark timing will vary with engine speed and load, and as the air/fuel mixture changes. If the spark occurs too soon, the engine will fight against the pressure in the cylinder creating extra heat and possibly cause “pinging” that may do internal damage. If the spark occurs too late, maximum cylinder pressure will occur too late also with the result that less of the gasoline will be converted into useful work, and more will be wasted as heat that the cooling system must get rid of. So, if ignition timing is incorrect, not only will the engine run too hot, it won’t have the power it should either.
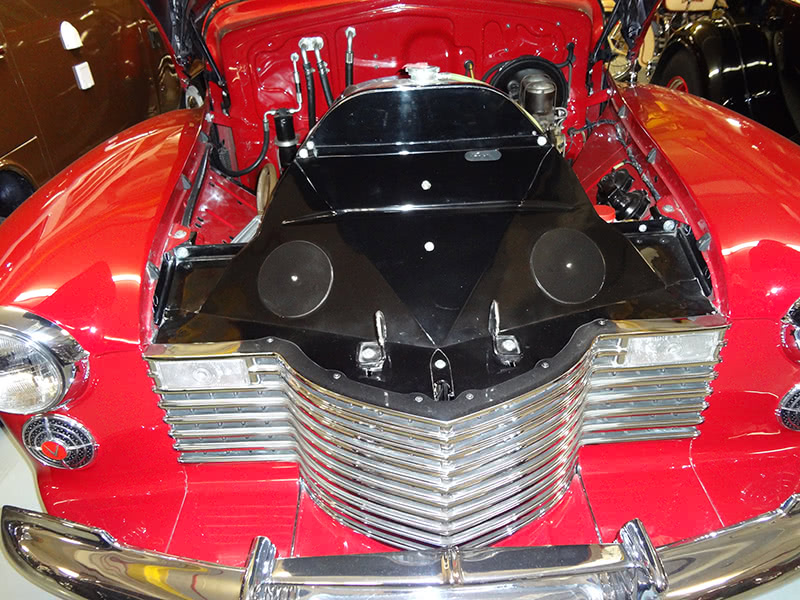
Once the access holes in the radiator supports of this 1941 Cadillac were covered, the engine ran cooler at highway speeds.
When an engine is operating with an air/fuel mixture that’s too lean for current needs, it will in many cases cause overheating problems. Typically, richer air/fuel mixtures will take some of the heat load off the cooling system, but not for the reasons many people believe. Actually, the highest combustion-chamber temperatures are obtained right at stoichiometry (that is, a 14.7:1 air-to-fuel ratio by weight) — going leaner won’t make the burn any hotter. As Performance Technician’s tech editor puts it, “You can’t make the fire in your woodstove hotter by putting fewer logs in it.” But there’s more going on here than is obvious. One of the things that happens is that a lean blend burns more slowly than a rich mix, so there’s still combustion going on when the piston approaches the bottom of its stroke. Thus, more of the cylinder, hence more of the water jacket, is exposed to the fire. Also, lean burning results in a different set of gases than rich: CO2 and N2 instead of CO and HC, and the former have lower specific heat capacities. Since the gases left over from a lean burn can’t “hold†as much heat, it’s radiated out into the cylinder wall raising water jacket temperatures. On the other hand, the CO and HC that go along with rich running carry more of the heat out with the spent charge.
Mechanical and vacuum curves
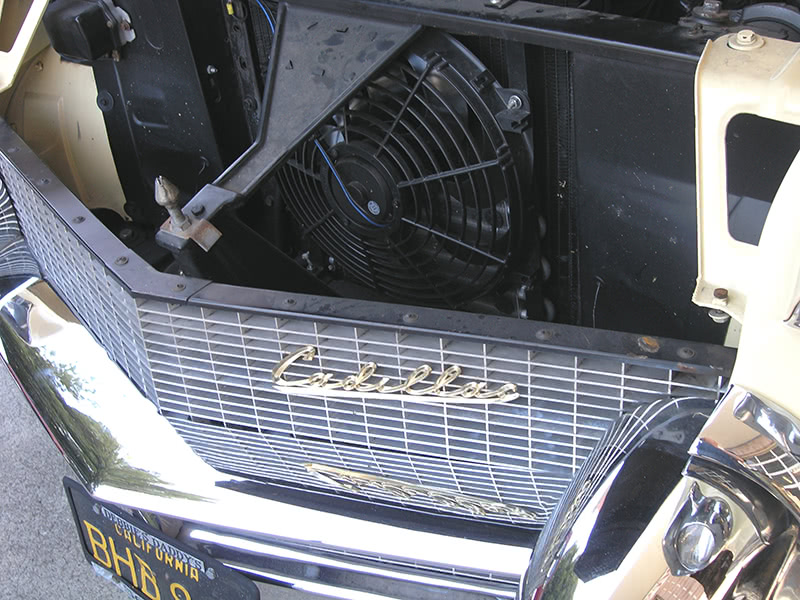
The electric pusher fan on this 1956 Cadillac helped cool the engine, but it still tended to run hot. Plus, it lacked the power it had had in the days of leaded gas.
Proper ignition timing involves more than just the initial setting. Even more important if you expect the engine to perform its best and not overheat is the amount and rate of both the mechanical and vacuum advance systems. Any original equipment or performance replacement distributor should have the mechanical and vacuum advance mechanisms checked to be sure they are properly tuned to match the engine/vehicle combination and the gasoline bing burned. The stock distributor that came with a vintage carburetor-equipped engine was engineered for a blend of gasoline that no longer exists, so it will need to be tuned for today’s reformulated unleaded gasoline. If the engine has a more modern aftermarket performance replacement distributor, you should be aware that many of these come with a very slow mechanical advance curve, it being assumed that the customer will recurve with the correct advance springs and limiting bushings to match the needs of the engine.
The vacuum advance can help cool a hot-running engine by giving it a little extra ignition timing lead under light load conditions that then goes away under higher loads. In most cases when you are using a “hot-rod†mechanical advance curve along with a vacuum advance, the amount of additional advance from the vacuum mechanism should not exceed 10 degrees when the engine vacuum is above 10 to 14 in. Hg. When you get too much advance at too low an engine vacuum, you may get pinging at light throttle.
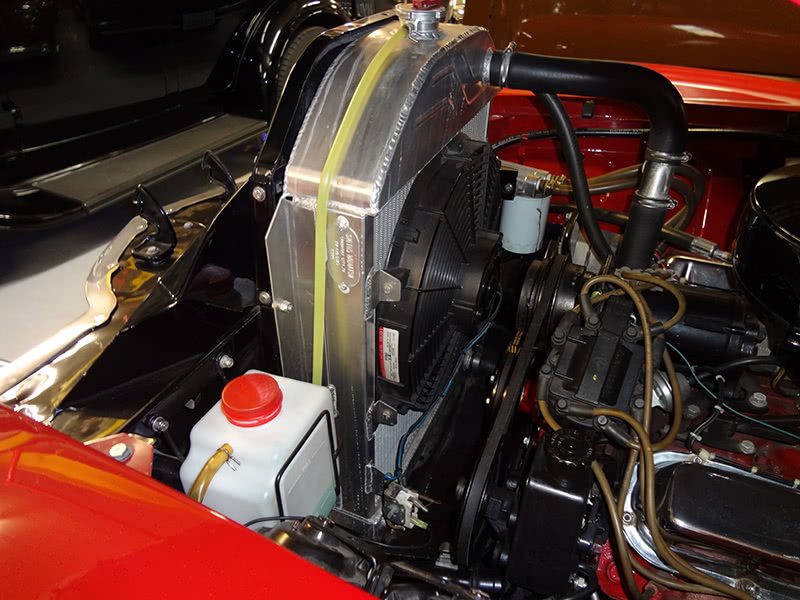
Even with an electric fan and aluminum radiator this 500 cubic inch Cadillac engine in this ’41 Caddy tended to overheat every time the weather got warm.
The vacuum source we like for advance is ported (no vacuum at idle) unless the mechanism has been matched to the engine vacuum at idle with the transmission in gear. The reason for this is to avoid any change in the spark timing as the vacuum drops when a vehicle with an automatic transmission is put into drive or reverse. Such a change in timing will affect idle quality and speed when the car is put into gear, especially if the engine has a hot cam. In gear, vacuum is lower and therefore there is less advance from a manifold-referenced system, which lowers idle speed.
The mixture effect
Once the advance curves are correct, it is time to check the jetting or air/fuel mixture. It is also very important to be sure that the fuel pump can supply enough fuel volume and pressure, even at high demand. The fuel pressure we use most is 5.5 to 6 lbs. at all speeds, and this must be maintained even at maximum load. Fuel tank venting issues can cause the pressure to drop under high fuel demand conditions — as vacuum builds up in the tank the pump will not be able to “pull” the fuel out. If the fuel pressure drops at high loads, the mixture will go lean and create a heat problem. An engine that is jetted too lean will produce more heat than an engine that has the correct air/fuel ratio. On the other hand, if the jetting is too rich, the mixture may still be burning in the headers and exhaust system, again creating more heat. Many of the overheating problems we have seen are due to a lean-at-part-throttle situation that is very common with both original equipment and aftermarket carburetors, and this can lead to overheating at light throttle.
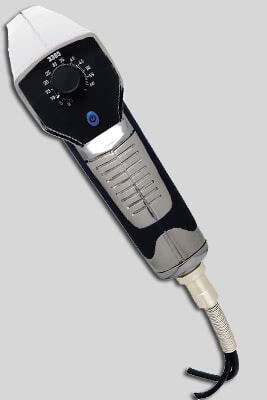
This #3365 OTC Tools dial-back timing light lets you check the total spark advance an engine is getting from the distributor’s mechanical and vacuum advance systems.
Also, modern reformulated gasoline can shift the air/fuel mixture lean by about 2.7%, which has brought on many lean mix problems. If this occurs during any driving condition, the engine will create even more heat for the cooling system to dissipate.
The easiest and most accurate means of checking the mixture (jetting) is by observing the CO reading from an exhaust gas analyzer, such as the Performance Gas unit we use from Bosch/OTC Tools. All you have to do is place the sample probe in the tailpipe and the analyzer will tell you the air/fuel ratio the engine is burning.
The mixture that works best for a stock engine produces an idle CO reading of 1 to 3%, or a 13.4-14.1:1 air/fuel ratio, along with a 3,000 rpm cruise mixture CO reading of .75 to 1.25%, or a 14.2-14.0:1 air/fuel ratio. A high-performance engine may need a richer cruise mixture of 3% CO, or a 13.4:1 ratio. If any readings are leaner than the target mixtures, excessive heat may be created as the engine fights to make the power needed to move the vehicle down the road.
The air/fuel mixture available from the carburetor’s power circuit should also be checked to be sure it’s adequate for high-load operating conditions. Most vintage engines use a power mixture of 6.6% CO, or a 12:1 air/fuel mixture, while an engine with more modern fast-burn cylinder heads may operate best with a 13.2:1 power ratio. If the mixtures are richer than the targets mentioned, the engine may not run too hot, but it may foul spark plugs and the vehicle will not go as far on a gallon of gas as it would if it were properly tuned.
Cooling a pair of vintage Cadillacs
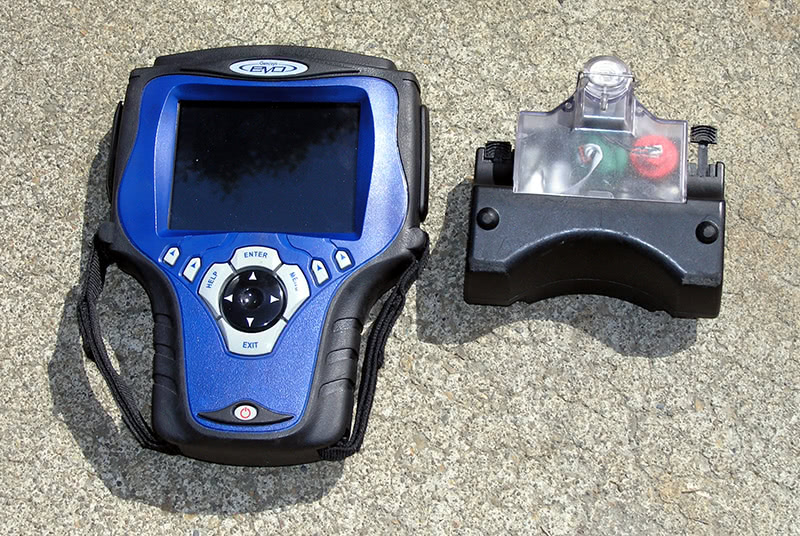
A portable exhaust gas analyzer such as this OTC Tools Performance Gas unit gives you the capability of reading the air/fuel mixture an engine is burning even while the car is being driven.
We will use two different vintage Cadillacs to illustrate how we diagnosed, then cured the overheating, driveability, and low-performance problems both of these cars were suffering from. The first example is a stock 1956 Cadillac El Dorado. The owner had installed an aftermarket electric fan mounted in front of the radiator to help the stock mechanical fan keep things cool. The aftermarket fan helped, but during hot weather the engine still ran too hot.
We first checked the exhaust gas with our OTC analyzer, and we observed that the idle and cruise mixtures were very lean. We then checked the mechanical and vacuum advance systems with a dial-back timing light. We saw that the mechanical system was advancing very slowly and was not providing the amount of spark lead that the factory built into the distributor. Plus, the vacuum advance system was not working properly.
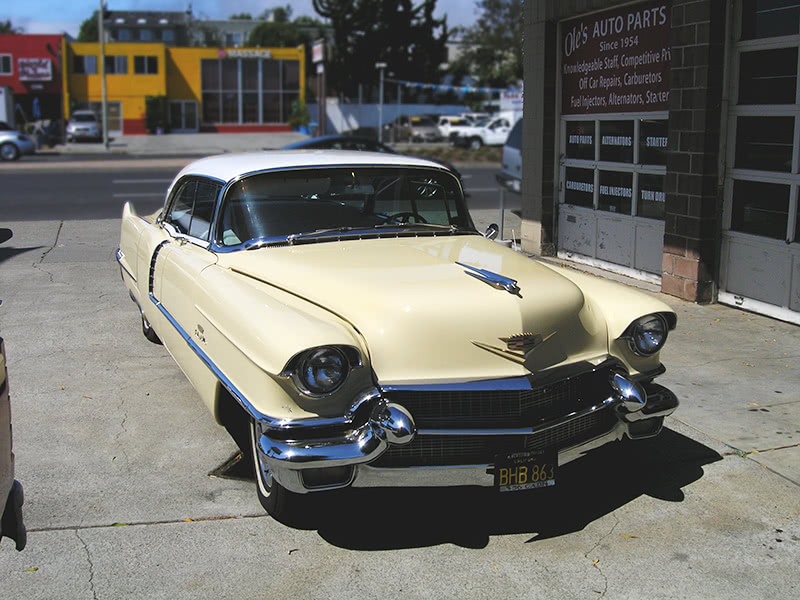
Once the engine in this 1956 Cadillac had its spark advance and air/fuel mixture curves tuned for today’s gasoline, it performed as it always should have, plus it ran cool even in hot weather.
The mechanical system was not advancing as it was designed to because the lube on the weights had tuned into a gummy substance that prevented free movement. The vacuum system wasn’t working, either. After repairing the distributor, we checked the air/fuel mixture the engine was getting from the stock four-barrel Rochester 4GC carburetor. The idle blend was very lean, and so was the cruise mixture. After modifying the idle and off-idle systems to provide more fuel, and increasing the main jets by FIVE sizes, we had the correct air/fuel mixture. After a test drive, the customer said that not only had the overheating problem gone away, but the car had never run so good.

The 500 cubic engine in this 1941 Cadillac now performs very well indeed, and it never overheats. The cures were routing all the air flow through the radiator, and proper tuning.
The second Cadillac was a 1941 with a 500 cubic inch V8 from a 1971 Eldo. This car had major overheating issues, plus it did not perform nearly as well as it should have with all that displacement. It turned out that the radiator supports on both sides had several large gaps that were allowing the air to bypass the radiator, so the first thing we did was seal them. We then checked the spark advance curve and found that the amount of mechanical advance was less than half of what it should have been. Plus, the vacuum advance was bad. After repairing the distributor advance systems, we checked the air/fuel mixture the engine was getting from the stock Rochester Quadrajet. The idle readings we observed on the OTC exhaust gas analyzer were very lean even with the idle mixture screws adjusted all the way out, and the cruise mixture was also very lean. We modified the idle and off-idle systems, plus increased the size of the main jets. The customer commented after taking the car for a test drive that the engine was no longer running hot, and now performed as he had always hoped it would.
The cool results
Now that both of these Cadillacs have had their fuel and ignition systems properly tuned along with having their cooling systems in proper working order, they are ready to be driven anywhere without the worry of overheating. Any vintage carburetor-equipped engine will both perform at its best and run cool when it is operating with the correct air/fuel mixtures and ignition spark timing curves properly tuned for today’s reformulated gasoline.
0 Comments