We’ve heard people who’ve been saved by ESP refer to it as “the hand of God†intervening for them, and the way it works can seem pretty miraculous. Understanding it doesn’t require divine inspiration, however.
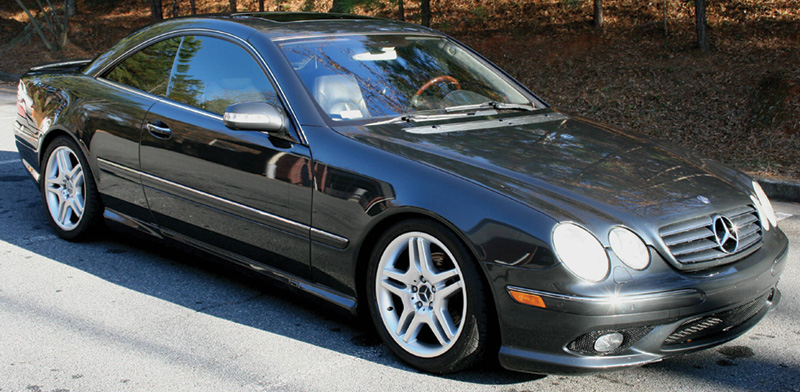
This CL500 has been lowered by altering the Air-Matic level sensors, dramatically reducing suspension travel. It’s likely that this kind of modification will adversely affect the way the ESP reacts in an emergency.
In 1959, Professor Fritz Nallinger, chief engineer and executive with Daimler-Benz AG, posed a question: Would it be possible to keep a vehicle’s wheels from spinning through a “control system†that could intervene by using the engine, transmission, and/or brakes to limit wheel slip? The idea was not feasible given the technology of the day, so the concept was patented and shelved until many years later. It wasn’t until the mid-1970s, some 10 years after Herr Nallinger’s retirement, that new developments would bring the idea back to life. New sensor and microcontroller technologies laid the foundation, leading the way to what may be the least known or understood safety system of the modern era.  Â
What’s in a name?
Elektronisches Stabilitätsprogramm — the English translation of that German name is Electronic Stability Program, commonly abbreviated to the clever “ESP†(which conjures up “extra-sensory perceptionâ€). It’s the trade name given to Mercedes-Benz’s electronic stability control system, which the company developed in partnership with Robert Bosch LLC. It’s been so successful that it represents a significant leap in automotive safety technology. By making such a definitive advance in safety, Mercedes-Benz yet again proves itself a pioneer and industry leader. Since 1996 (18 years ago!), ESP has been optional equipment on select Mercedes-Benz vehicles before becoming standard equipment across the line in 2000. Now as federally mandated safety equipment, it or its imitators is required on all new vehicles (less than 10,000 lbs.) sold in the United States since 2012.
Keeping Control
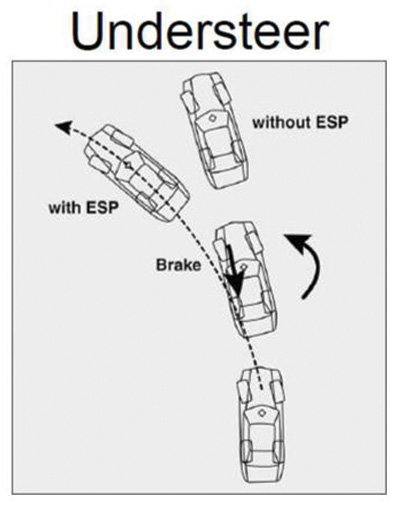
Under-steering is when you’re “plowing†through a curve. ESP applies the inside rear brake to help keep you from driving off the road.
What exactly is vehicle stability control or ESP? We already have a system in place to deal with wheel lock-up in the form of the Anti-Lock Braking System (ABS). Likewise, there is a system to deal with wheel spin known as Acceleration Slip Regulation (ASR). ESP was developed in an effort to provide safe directional stability in hazardous driving situations. These include braking, accelerating, coasting, and cornering. ESP working in concert with all other passive systems (passive meaning silently present in the background until needed) helps Mercedes-Benz produce some of the safest cars in the world.
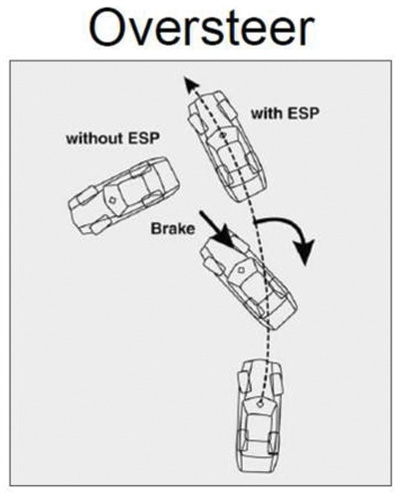
Over-steering is the rear of the car tending to overtake the front in the scary phenomenon commonly called “spinning out.†Braking the outside front wheel helps counteract this.
ESP is a safety program/system integrated into Mercedes-Benz vehicles that augments driver inputs. To help prevent loss of control from over-steer and/and under-steer, ESP will intervene in an attempt to assist the driver in maintaining control. Using various sensor input data, the stability control computer can sense when a vehicle is no longer traveling on its intended path or has reached the limits of controllability. Through a very sophisticated set of proprietary algorithms within the programming, the ESP controller calculates and implements the appropriate response. ESP gives this response in the form of braking individual wheels (and reducing engine power if necessary) all in an attempt to help the driver keep or regain directional stability.
The goal of ESP in the event of under-steer is to get the vehicle to actually turn in the direction the front wheels are being steered. An example of under-steer would be if you were sliding on ice with the front wheels completely turned, but momentum kept you sliding in a forward direction. The goal of ESP in the event of over-steer is to keep the rear of the vehicle from “stepping out,†or “swapping ends.†An example of over-steer would be if you were going too fast entering a curve with the steering wheel turned sharply, causing rear-end momentum to spin out the vehicle.Â
Control losses that ESP may respond to include:
- Wet or slippery (hydroplaning) driving conditions
- Icy roads, especially black ice
- Evasive maneuvers (swerving) to avoid obstacles
or accidents - Distracted driving that results in under-
or over-correction - Excessive cornering or turning speed
- Situations that would induce vehicle spin or skidding
Parts and Forces at play
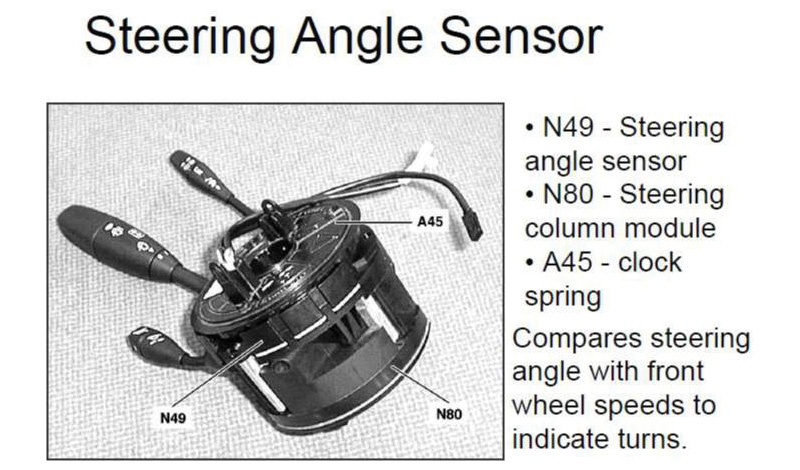
One critical ESP component is the Steering Angle Sensor, which is incorporated into the Steering Module Assembly.
ESP is heavily data dependent, relying on multiple sensors to provide the input the electronic logic requires to command the appropriate action. To accurately maintain this critical system, you, the Independent Service Provider (ISP), must realize the importance of all the parts involved.
Sensor inputs include:
- Wheel speed sensors located at each wheel hub relay accurate speed data.
- The steering angle sensor signal relays information on the driver’s intentions for steering direction
- Brake switch state input is used to determine when the driver’s foot is on the brake pedal
- The Brake Pressure Sensor accurately monitors the exact amount of brake pedal effort being applied
- The Accelerator Pedal Position Sensor is used to determine not only load position, but also to calculate the speed at which pedal pressure is released in relationship to the speed of the brake pedal being applied.
- The Yaw Rate Sensor is a critical component for ESP in that it measures rotational speed (turn rate) around a vertical axis (the Earth is a good example of yaw: The planet spins on an axis while moving in orbit)
- The Lateral Acceleration Sensor measures side load or cornering G-force and the speed at which the load occurs. If you have ever been pushed up against the door from taking a hairpin curve a little too fast, you have experienced lateral acceleration.
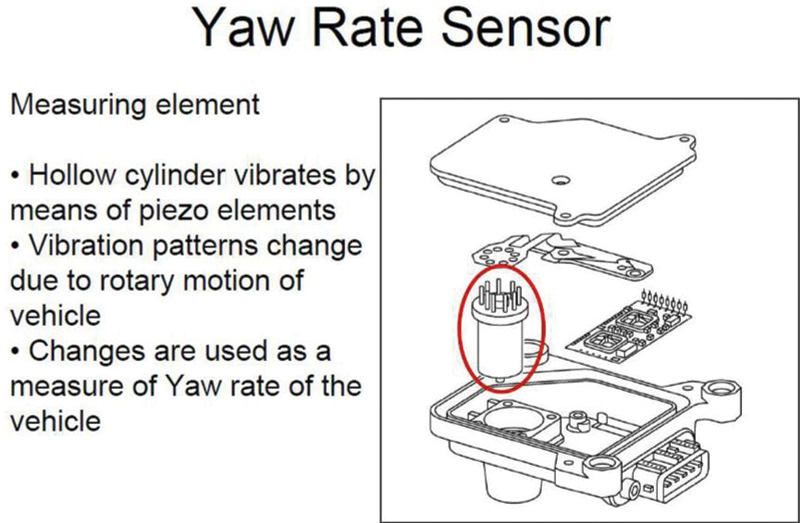
This stand-alone Yaw Rate Sensor makes use of piezo elements and vibration patterns to generate a signal that informs the ESP electronics of the vehicle’s rotation about a vertical axis.
The important ESP outputs and actuations are:
- The ABS pump, which is used to control braking at an individual wheel whenever the driver’s foot is applying brake pressure. This is the main multi-function actuator for all traction systems. Continued refinement in reaction speed and precise pressure control have allowed the ABS pump to take on multiple roles.
- Engine Control Unit is in the loop. If power (torque) reduction is needed, the ESP can direct the ECU to retard engine timing and close the electronic throttle. Once the target has been achieved and intervention is no longer needed, the ECU seamlessly resumes normal operation.Â
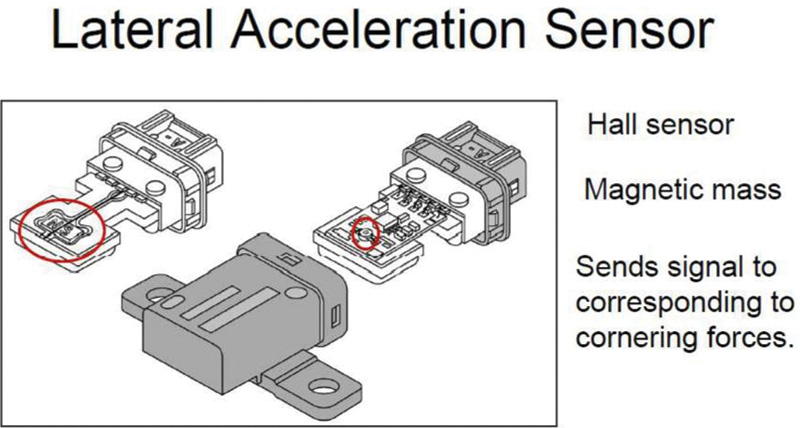
The dedicated Lateral Acceleration Sensor provides ESP input from a magnetic mass and Hall effect sensor.
Physical Limits
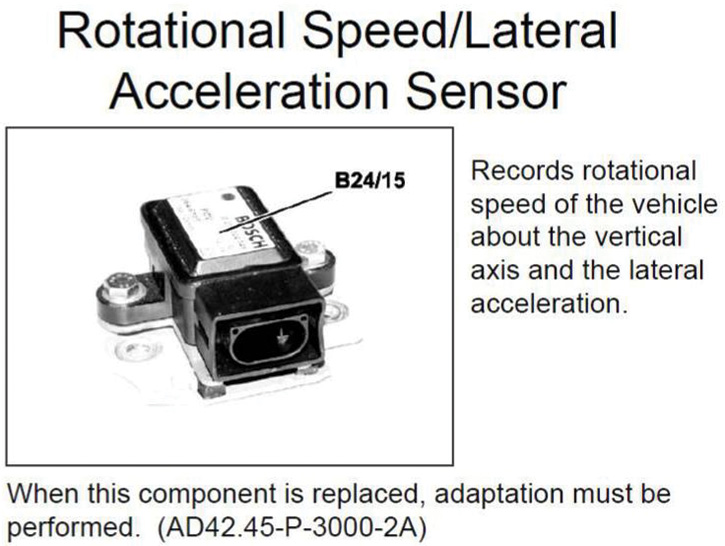
A combined Rotational Speed (“yawâ€) and Lateral Acceleration Sensor as found in later-production Mercedes-Benz vehicles is also referred to as a “sensor cluster.â€
Helping the driver to maintain control or recover from loss of control is a benefit to all on the road. There have been many world studies that prove the benefits of ESP. It has substantially reduced the number of accidents and fatalities since its inception. In some instances, ESP has even rivaled ABS as a stand-alone system in the number of avoided accidents. Because of their higher center of gravity and propensity to roll over, SUVs in general have shown the most notable reduction in accidents. As older cars are taken off the road and replaced with newer stability control-equipped vehicles, it stands to reason that the number of lives lost and accident rates will keep falling. Who knows — maybe the cost of insurance will go down, too (hey, one can dream). But as great as ESP is, it’s still bound by the laws of physics. ESP cannot overcome full hydroplaning on water or ice, and driving too fast for conditions is still driving too fast for conditions. Driver alertness is still paramount. The best accident prevention is common sense.Â
ESP in the shop
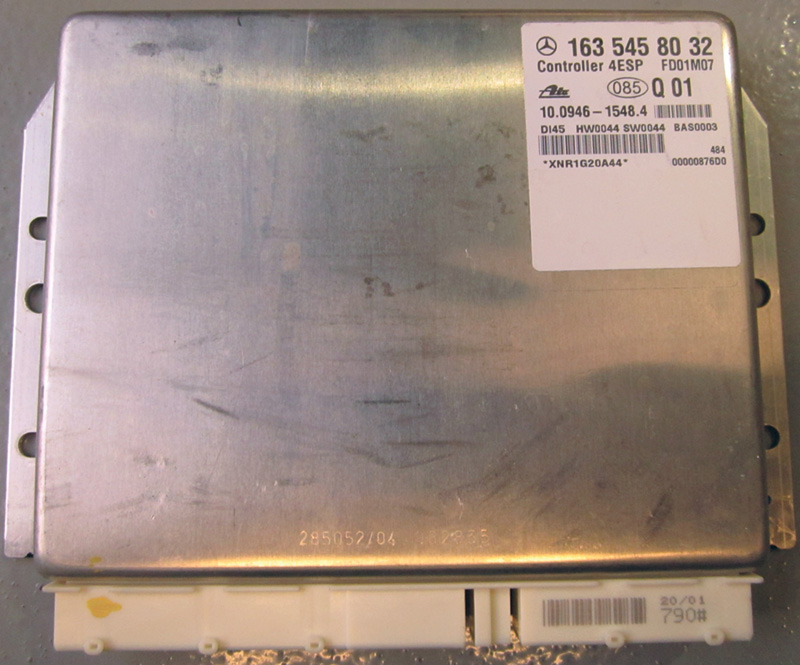
According to published Mercedes-Benz engineering data, a human can react in about 300 milliseconds (0.3 seconds), but the ESP controller a can make calculations and react in as little as 40 milliseconds (0.04 seconds).
From an ISP standpoint, Mercedes-Benz ESP has proven to be a very reliable system. Still, there are some key points to be made.
The first point is owner education. Most people aren’t aware that they have these safety systems built in. A common owner complaint is that the ESP is activated while driving and the owner misinterprets this as a malfunction. Being uneducated in the matter may cause the owner of the vehicle to bring it by the shop for an unnecessary reason.
The second point relates to assuring that the system continues to function as designed. As with all safety systems, we feel it’s the duty of the ISP whenever performing maintenance service to thoroughly inspect the actuating components of safety systems and make solid, knowledgeable recommendations on needed maintenance or repairs. You are the eyes that can recognize what the customer can’t see, and human life could be at stake if neglected parts fail. Ultimately, it’s up to the owner whether or not to follow through on repair recommendations, however.
Where ESP components are concerned, the only “maintenance†involved beyond brake fluid changes is regular inspection of those that have an influence on the operation of ESP. There are, however, some very important service-related points:
- Mercedes-Benz-approved wheels and tires. That means the proper size, speed rating, tread depth, inflation, and they should be within the industry age recommendation of less than six years old. ESP is engineered to work within very specific parameters. Aftermarket wheels or the use of wrong or neglected tires could upset the system’s proper function.
- Genuine Mercedes-Benz brake pads, rotors, and fluid. The braking system as a whole has to be maintained to a higher level than in the past. ESP’s foundation is brake-critical. Mercedes-Benz has formulated, engineered, and manufactured rotors and brake linings with specific compounds to provide the best possible stopping power. Excessively worn, over-worked, or aftermarket parts could all compromise safe actuation in an emergency situation.Â
Four-wheel alignment and suspension. ESP’s reliance on the steering angle sensor has brought suspension geometry into a more prominent role. Proper alignment is necessary to ensure that driver input or directional intention is transmitted to the front wheels accurately. Steering direction is verified by comparing front wheel speed sensor signals. When turning or cornering, the inside wheel spins more slowly than the outside wheel. This speed differential is compared with the steering angle input by the stability control computer to verify that the wheels are in fact turning in the intended direction. Worn suspension components or altered ride height that changes suspension travel could also have an adverse effect on ESP operation.
The third point is actual diagnosis. ESP is a refinement of ABS and many braking or related sensor problems can cause ESP to fault and shut down. The picture must be looked at as a whole, taking into account all faults in all systems. When dealing with ESP, we have found no substitute for the Mercedes-Benz factory DAS/SDS scan tool. Aftermarket tools seem to generate spotty information at best. If you, the ISP, do not have access to the proper diagnostic equipment, fault repair should be left to an ISP or authorized dealer who does. It’s a high stakes guessing game when you’re not equipped to deal with safety systems. Fortunately, problems with ESP are few and far between.
ESP complaints and failures
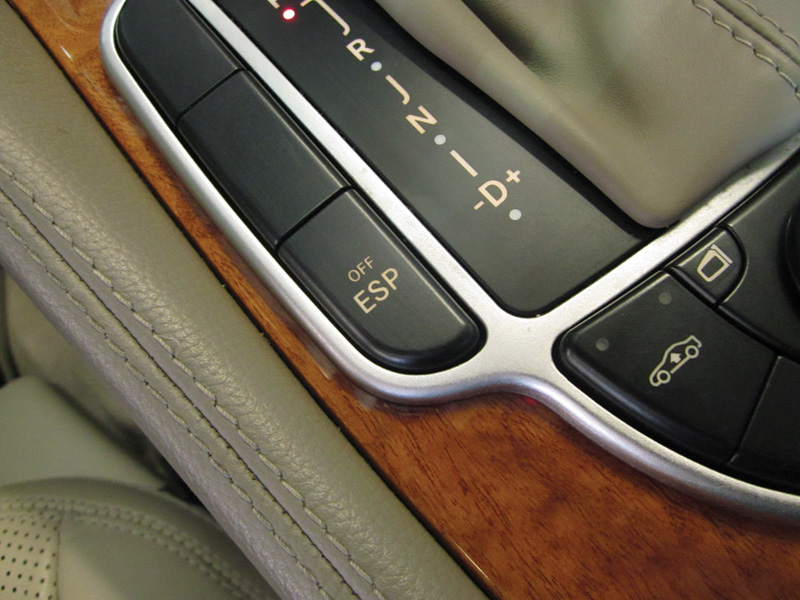
It’s a misconception that this switch completely disables ESP. The truth is it only disables the engine power reduction side of the programming. Braking function is always active except on a few special race-application AMG models. ESP can be completely eliminated for off-road (track) use only.
Still, some problems do occur in the harsh real world of motoring, to wit:
- Brake switch malfunction is by far the most common reason for ESP fault codes. The truth is that very few switches actually fail — most faults occur because of human interaction. Brake switches are designed to be self-adjusting to a point, but when installing a brake switch, proper gapping procedures must be followed. Documents explaining this can be found in Mercedes-Benz service literature. Failure to set the proper gap will, in certain circumstances, cause brake switch actuation to be out of sync with the internal brake booster travel switch. ESP uses both switches to determine brake actuation speed. Improper installation may generate Fault Code C1200 — S9/1 (stop lamp switch plausibility).
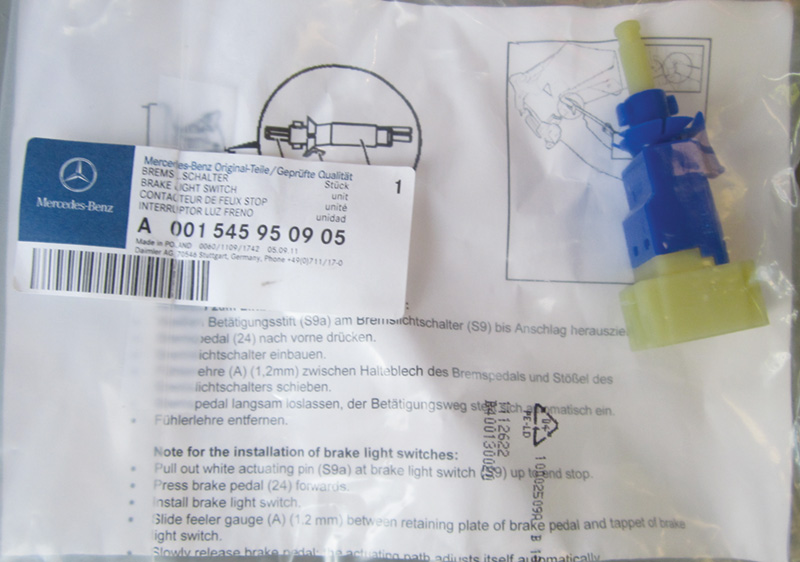
MBUSA’s Parts Division has made the technician’s life easier by including work instructions/procedures with some new brake switches.
Another common cause of brake switch codes is bad driver habits. Over the years, we’ve seen three common specific driver-induced problems. First are drivers that like to slip their foot off the brake pedal, which allows the full force of the return spring to slam the pedal against its stop. Over time, this repeated action drives the adjusting pin of the brake switch back into the housing. The second cause of brake switch codes results from drivers who like to put their foot under the brake pedal and pull it back. This results in the same situation as the first, driving the adjusting pin back inside the housing. And, third are drivers that use their left foot for braking and their right foot for accelerating. Under some circumstances, driving with your feet on both the brake and accelerator pedals at the same time can result in a plausibility error within the ESP control unit, which will cause the ESP system to enter limp-in mode.
- Pedal obstruction: Worn floor mats or multiple floor mats have been known to cause faults and limit travel when they have slid or become bunched up under the foot pedals. This is a very dangerous situation and should be checked for and noted during all routine service.
- Steer angle faults: Again, proper alignment comes into play. An off-center steering wheel may cause an ESP conflict, resulting in a fault code and illumination of the ESP light. Another common cause is spilled liquid (i.e. coffee, soda, tea) on the steering wheel so that it finds its way into the angle sensor and covers the optical sensors. Also, if the battery is disconnected, the steering angle sensor in some models will need to be re-initialized by turning the wheel lock to lock.
- Yaw and lateral sensor faults: On occasion, these sensors have failed. One of the most common mistakes is replacing the wrong sensor. On earlier systems that used both sensors independently, the fault language could be confusing, leading to technicians replacing the wrong component. It’s important to verify the fault with the guided tests in SDS and positively I.D. the correct component. These steps will help you avoid making a costly mistake. Â
- The mysterious stuck caliper: A vehicle comes into the shop with one seemingly stuck brake caliper. This could be severe enough to have burned the pads, rotor, and, in the worst case scenario, damaged the wheel bearing from the intense heat. Common sense might lead you to believe it’s solely a brake problem. That may indeed be the case, but with the addition of ESP, there might be a deeper problem. Because ESP can actuate each brake independently, false data from the yaw or lateral sensor (very rare, but it has happened) could keep one brake applied. Let us reiterate: When dealing with ESP, the brake system needs to be looked at as a whole.
- When component replacement is necessary, there is absolutely no substitute for the genuine Mercedes-Benz part. These critical components were manufactured and tested to meet Mercedes-Benz’s strict standards.   Â
What the future holdsÂ
Development of ESP hasn’t ceased. Mercedes-Benz has recently developed an enhanced version for its line of delivery trucks and vans with the capability to sense cargo load and account for it in emergency activation. Already implemented is ESP for tractor-trailer applications. This should greatly cut down on the number of large truck rollovers. It is to be hoped that these new systems will produce the same stellar numbers in accident reduction that the passenger car market is seeing.Â
0 Comments