Creative work, indeed, and if tempered by these tips, profitable, safe, and pleasurable.
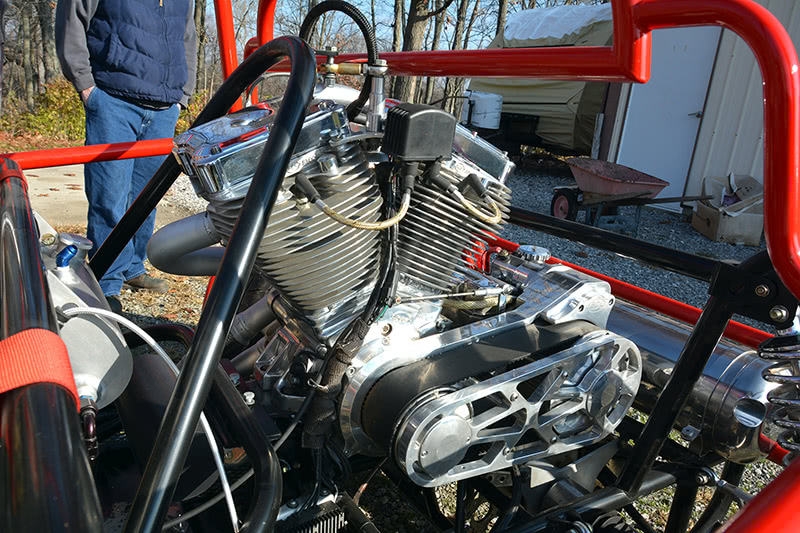
Left: This is a truly unique build in that it uses a large-displacement S and S-based Harley-Davidson engine. Custom parts were fabricated to transfer the power, in addition to the parts that make up the car itself. One unforeseen problem: The engine vibrates so badly that at some points in the rpm band the car isn’t a lot of fun to drive. After several very creative attempts to dampen it out, the decision has been made to change powerplants — which is why it’s back at Advanced Chassis.
Between racing, various projects, and the holidays, we finally got to sit down and discuss the last bits for this article. My last question for Dan Bowers was, “What things have you learned — the hard way — that you wish you had known, or had a better understanding of, when you first got started?†His responses might surprise you!
“Centerlines, centerlines, centerlines, he tells Performance Technician. “Centerlines are one of the most important things to find and lay out so you can start your work from the same reference points every time. I always like to start all of my layouts from a center line (X-axis and Y-axis both, if possible). All of your jigs should have accurate centerlines scribed into them in as many places as possible. We do all of our measuring from the axle centerline (X-axis) forward and back, and all other measuring from the longitudinal centerline out (Y-axis).
Next, he says, “If it spins, it will hurt you — and in most cases you’ll get to take an ambulance ride if you get into a spinning tool. I have seen this and I’ve seen the damage done from a lack of respect for things that spin. Even if it’s not a powerful tool, the inertia from the spinning tool can be enough to really screw up your day.
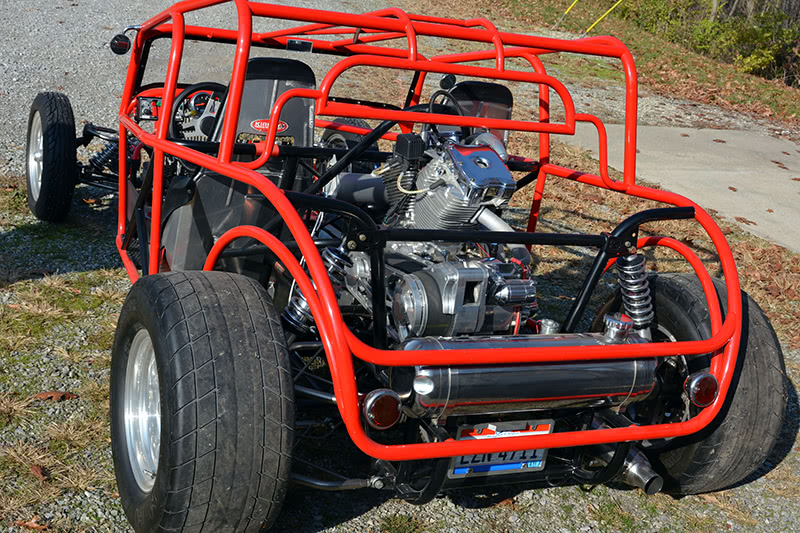
The body outline in red is your classic ’32 Ford and those parts that don’t contribute to the look of the car are blacked out and just disappear into the background. It’s a very clever treatment designed to enhance the look of the ’32 while providing sufficient structure to make the car safe and functional.
“If you ever want to see a great example of just how this works, grab a ratchet tie-down strap and see what happens when you get a single wrap around that little metal bar. You can move a 4,000 lb. car forward with a four-inch lever! This is exactly what happens when your shirt or glove touches something spinning, one wrap and it’s all over (except for the ambulance ride!). Keep sleeves, gloves, watches, rings, and all loose clothing way, way away from spinning tooling.
“While we’re talking safety, wear your safety glasses. Or, both glasses and a face shield if you’re really making swarf. While they can pull ferrous metal out of your eye with a magnet in most cases, non-ferrous metals like aluminum, brass, or copper has to be dug out. I can think of a lot of things I don’t like very much and having someone dig around in my eyeball ranks right up near the top of that list. I really don’t care if they make you look like a dork, and I don’t care if you don’t like them. Wear them.
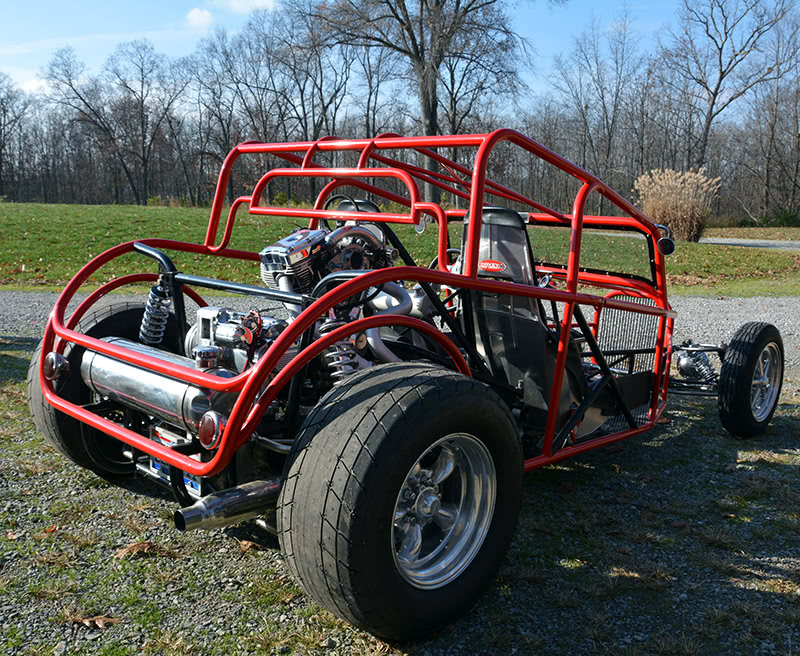
Dan describes this as his favorite build. The tubing forms the outline that becomes a 1932 Ford, chopped, channeled, and rodded.
“Other things to remember are to keep your wits about you as you do hot work — use sleeves, coats, gloves, and eye protection — use hearing protection if you’re in an area where the noise levels exceed 85 dB or so. Fab shops can be dangerous — THINK!
Dan continues with some helpful tips. “Have you ever had a bearing race or some other part pressed into a blind hole and later found that it needed to be removed for repair or replacement?†he says. “In the past, we were stuck using blind hole bearing pullers, using a Dremel to cut the race into pieces, or drilling into the part behind the race to get punch access so that the part could be driven out. But here’s a neat trick: If you weld around the inside diameter of the race that’s down in a blind hole the process of welding it will make it shrink and fall out! Wish I’d figured that one out sooner…
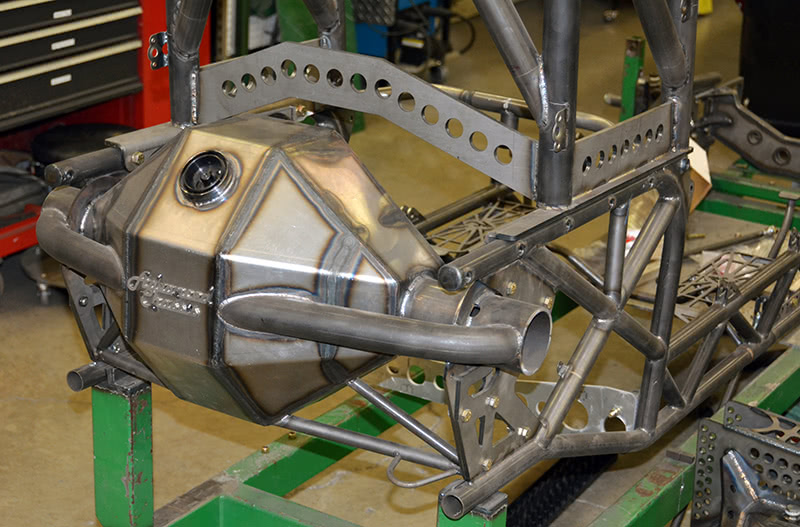
This gives you a good idea of what talent with a welder can get done. This Mini-mod pulling tractor frame is going together with a custom-fabricated rear axle housing.
“Working metal really accelerates the rusting process. Grinding or heating removes all of the inhibitors applied during manufacture. A mixture of transmission fluid and WD-40 sprayed onto tubing (especially after you weld) will keep it rust-free for a long time. If there’s a paint shop you use, you may or may not want to divulge this little secret formula because WD-40 contains silicone, which causes fisheyes in the paint. It depends on how understanding your painter is to YOUR needs and processes. Rust can compromise tube strength, so it’s critical to keep the corrosion off of your work, but if you’re going to get yelled at every time you drop off a job for painting, well, use you own judgment.
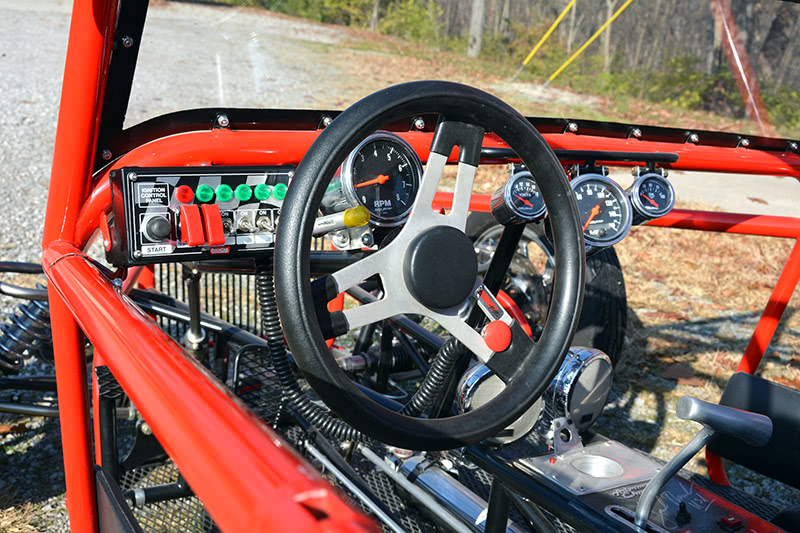
It’s all the little details that impress you — the neat layout, the hidden wiring and controls — we didn’t have enough time to take it all in, but you can see just how much meticulous planning and thought went into this project.
“Take the time to get to know your customer. Racing is done because it’s fun and we like doing it, but it’s all done out of discretionary income. Taking a little bit of time at the beginning of your new relationship will save you huge headaches down the road.
“I like to take a little more time than maybe I should with customers, especially on the first visit. A little time up front will save you tons of time later. I will talk about their families, their shop at home, and their pets along with the obvious conversations about the work we are going to be doing. These little conversations will reveal a lot about your newest boss, and who doesn’t like to make a favorable impression with a new boss when the opportunity presents itself? This is when you begin to help them manage their expectations. Customers tend to believe that the work is easier than it really is, that it will take less time than what it will really take, and that it will somehow be cheaper than what it ends up being. You will also likely find out what others have done in the past that disappointed your new customer, so you can avoid doing those things. Two good side effects: One, you get to spread your network into this guy’s circle, and, two, you might just make a new friend who shares your passion.
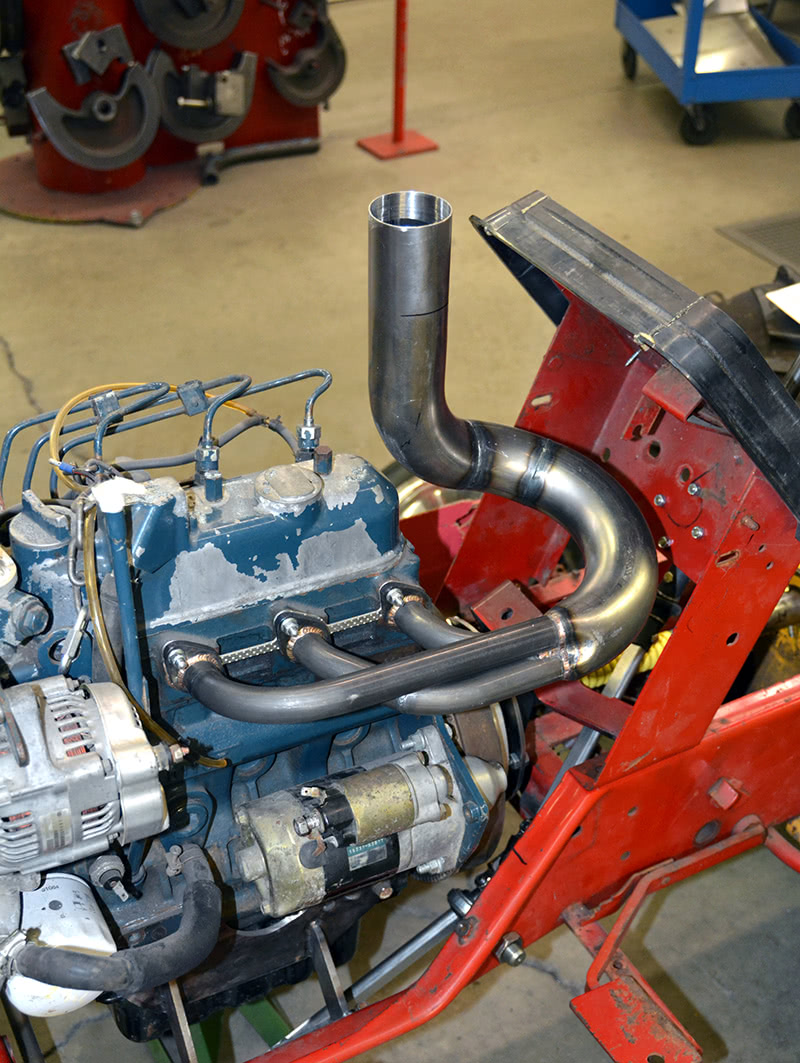
We were wandering around the shop, upsetting the work flow (again), and talking to the crew when we spotted this little project. We don’t know a thing about these little tractor pullers, but we’re going to have to go and check it out this summer. Look at that header design! It’s a thing of beauty.
“Organization — I’ll admit it, when I got started in this business with my Dad 20 years ago I was a slob. It didn’t take long to realize that it wasn’t my Dad being overzealous about putting stuff away, it was stupid not to. If you don’t put it back you spend half your day hunting tools! As you will see in our pictures, we color-code all of the common tools in our shop. All are laid out and hung nearly identically on peg board at or near each work station, and there is a place for everything. Every station has everything needed to do all common work, and all specialty tools are kept in one tool box that is labeled on the outside of the box. I spend nearly every weekend in the winter cleaning and organizing my shop to try to get the efficiency as high as possible. It is hard enough to make a profit in this line of work without making it harder than it has to be.
“Cleanliness and organization has one terrific side effect: Everyone talks about your shop, and how they don’t take their cars to a competitor because he’s a slob. Believe me, this happens all the time and the more professional you come off, the better off you’ll be. I like to use aspiring fabricators from the local high school for my clean-up and organizational crews. With a little guidance, they do a good job and I can meet potential future employees that I might hire as the business expands.â€
Most PT readers will do some amount of fabrication at some point in their careers, but if you should want to get into this satisfying creative activity in a professional way, or if you just want to communicate better with a fabricator who’d doing jobs for you, Dan’s advice will prove to be very valuable. Thank you, Dan and company!
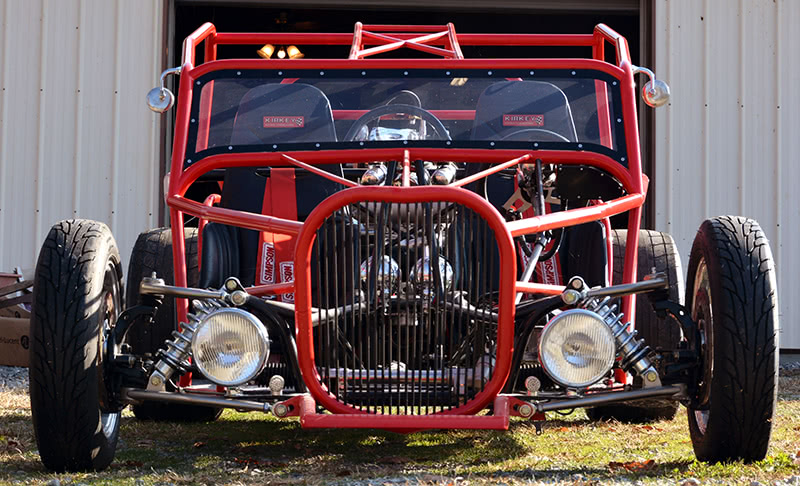
Check out the front end of the Harley car. It incorporates all of the key features of the hot rods of that era, and does it all in outline. With low, raked coil-overs, it has the right kind of look all done by suggestion, since there’s not really a body here at all!
0 Comments