Johnny Lightning makes great cars and trucks even better
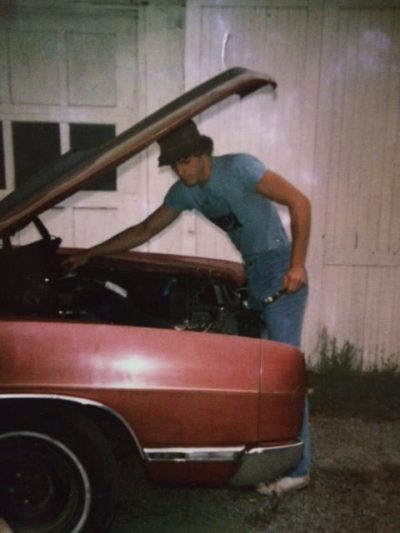
It’s all a very familiar story. Boy comes of age. Boy works with his teen-age buddies. Boy’s father is a sheet metal mechanic. Boy learns fabrication with teen-age buddies. Boy combines fab skills with technical skills learned in friends’ garages.
The story continues from there. John Wiker, Jr., a/k/a Johnny Lightning, grew up this way, and did the things so many young boys do. He developed an interest in Hot Wheels cars and slot car racing. He took auto shop in school. He built up kits with gasoline-powered cars and ran them in circles using a hand-held controller connected to the cars by strings. He pretty much built and developed every kind of automotive model that he could find. And he usually found a way to make them faster.
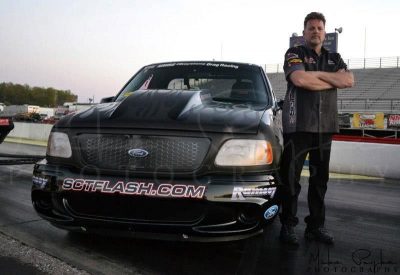
As you would expect, the next step up was a real car, which he received as a gift from his stepmother, Sandy Wiker, when he was just 17. It was a 1969 Ford Galaxie with a 390 and an automatic — not exactly a barn-burner, but at least it was something with some grunt, and something to work with. He paid his dues with many trips down the lanes at Strato Rods Dragway at Maguire Air Force Base in New Jersey.
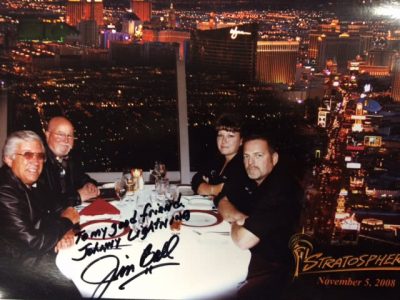
He knew breathing would help the big Ford FE motor, and a big Holley carb helped, but fate would have him fabricate a ram air setup using the sheet metal skills he learned working for his father, John Wiker Sr.
And with that first ram air setup, the die was cast for a career and fame with special expertise in the performance induction arena.
Some successes with the Galaxie led him to trade off a case of beer for a junkyard 390, and shortly thereafter he bought a wrecked 69 Mustang GT fastback, which received a transplant of the newly-rebuilt junkyard engine, which powered the Mustang to many podium finishes.
Fast-forward to several years of working with his father in the sheet metal fabrication shop, and then as a welder and fabricator, all to fund his part-time racing effort. Strange as it may seem, fate would then have him work for several years as a grower of shiitake mushrooms with his father in their business, Lancaster County Exotics, in a region nationally known for mushroom cultivation. This experience allowed him to pursue his racing while learning valuable business and customer relations skills.
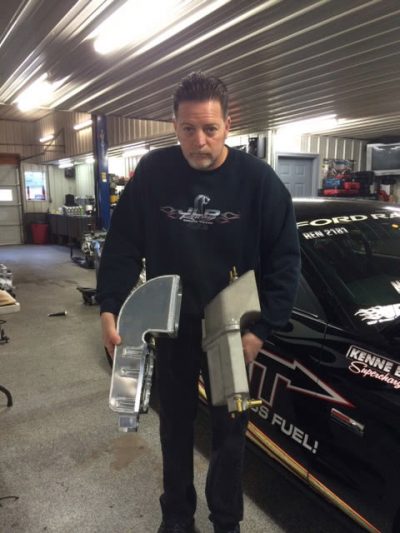
All the while he focused his engine performance work on induction systems, learning all the nuances of fluid dynamics, and applying them to increasingly sophisticated powerplants, most of them Ford products, an outgrowth of his first Ford Galaxie. He ran a 1984 5.0 Mustang, then a 1990 Mustang GT wearing a Vortec supercharger. In 1993 he stuffed a Vortec supercharger on top of a Mustang Cobra SVT/R and broke the 10-second barrier in the quarter-mile.
When the Ford Gen 2 Lightning pickup truck package was introduced in 1999, he just knew he had to have one, bought one and did some dyno testing and tuning including a hand-made ram air box setup. His first major race happened to be the first-ever Modular Motor Shootout, and Johnny won the event with a 12.90, becoming the first-ever Lightning pilot to break into the 12’s. Owners of some of the other 30 or so Lightning trucks there immediately wanted to know his secrets and buy parts from him.
And with that, John Wiker, Jr. became “Johnny Lightning,†and he founded Johnny Lightning Performance.
Much of what Johnny learned along the way had to do with induction systems. He labored on minimizing restrictions to air flow, with the understanding that the lowest cfm component in the induction system dictates the final air flow into the engine. He also focused on reducing air inlet temperature, since every ten degree increase in inlet air temperature tends to reduce horsepower by about one percent.
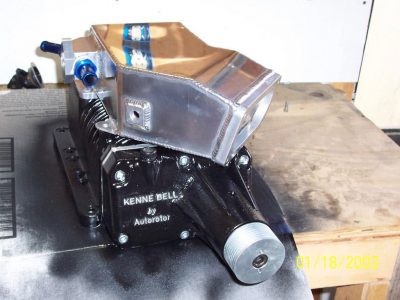
Johnny’s work led to his development of low restriction, high efficiency induction systems, which he offered initially for Ford models, and then expanded to other makes and models. But it also led him into developing a family of products for supercharged engines.
His fabrication skills led him to prototyping inlet ducting and plenums, but he also was wise enough to recognize that it would be impractical to make a massive investment in engineering, manufacturing, and testing the products he was developing. So he reached out to Jim Bell, a principal in Kenne Bell, a company well-established in the development and manufacture of superchargers and related products. Bell, a modern-day hot-rodder in his own right, readily accepted the partnership.
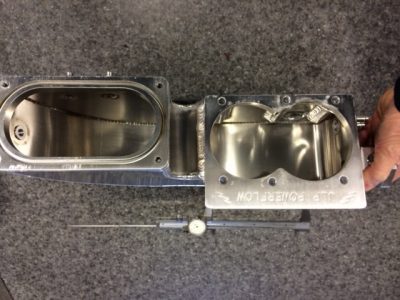
The two made for a perfect team, with Johnny’s ingenuity and ability to tailor induction systems to individual engines’ needs, and Jim’s existing superchargers and interest in volume production for the retail market.
Most readers of PT are familiar with the role of a supercharger. It uses a belt-driven pulley to compress the incoming fuel/air charge, filling each cylinder with more fuel, and therefore making more power. A turbocharger performs the same function, except that it is driven by exhaust gases passing over a turbine wheel rather than being belt-driven. Most racers prefer the supercharger arrangement because it responds instantly, rather than displaying the “turbo lag†of exhaust gases having to build up to power a turbocharger.
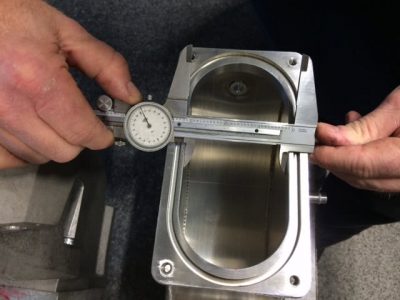
Key to the efficiency of a boosted engine is an inlet plenum with as little restriction as possible, so as to not limit the availability of incoming air in a fuel-injected engine, or the incoming fuel/air mixture in a carbureted engine. Designing these plenums is one of Johnny’s greatest strengths, and precision is critical for optimal performance.
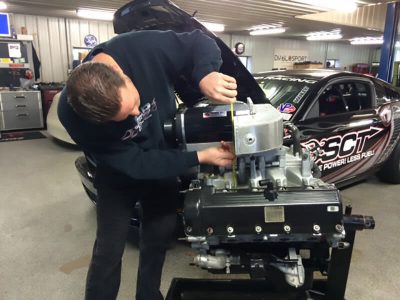
Many supercharged engines also make use of an intercooler. Here’s why. A supercharger does a very good job of compressing air or a fuel/air mixture. But science tells us that compressing a gaseous mixture, by definition, makes it hotter. And we all know that a cooler fuel/air mixture generates more power. An intercooler makes up for this by cooling the mixture as it exits the supercharger.
And here’s the key point: By lowering the temperature of the fuel/air charge, the engine is able to run on lower octane fuel, avoiding engine-damaging detonation. So the intercooler doesn’t directly increase power; rather, it optimizes conditions for making the most power from the highest octane fuel available or allowable.
Here’s where the math comes in.
- Every pound of boost from the supercharger increases the temperature of the fuel/air charge by about 10 degrees F.
- Pressure is necessarily lost through the intercooler. A very efficient intercooler can lose as little as 1.1 psi. A very inefficient intercooler can lose much more.
- Each psi of loss of boost costs about 20 horsepower in a high-end race-prepared V-8 engine.
- Incoming volume as measured in cfm is calculated by multiplying maximum horsepower possible times 1.5. So, for instance, a 1,000 horsepower engine requires 1,500 cfm of incoming fuel/air charge.
As you analyze all of these factors, we can reach some defining conclusions:
- Higher pressures in the cylinders provides more horsepower, up to the limits of the available fuel.
- There is necessarily some pressure drop through the intercooler.
- Supercharger output can be varied to compensate for pressure loss through the intercooler.
- A precise combination of pressure, volume, and temperature can optimize engine performance.
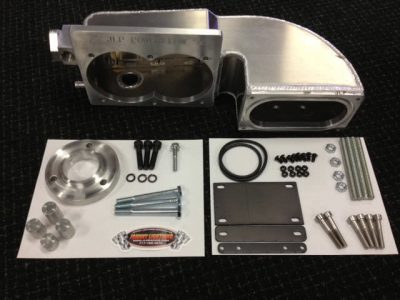
Given all of these facts, here’s how Johnny and Jim collaborate to produce complete forced induction systems. Johnny designs and builds engines to meet specific customer requirements or class rules, determining the maximum power possible while naturally aspirated. He also custom-designs an intake plenum to be as efficient as possible for the space limitations of the particular application and the octane of the fuel to be used.
Johnny and Jim then collaborate to spec out the supercharger and intercooler that provide the maximum cylinder pressure that the fuel will tolerate. So, for instance, if there’s a 2 psi pressure loss through the intercooler, they re-design the intercooler and manifold to eliminate the 2 psi loss. Otherwise, the loss of 2 psi would translate into a loss of 40 horsepower.
The partnership brings benefits to both parties. Johnny hand-builds intake plenums for custom applications and adds Kenne Bell supercharger and intercooler components so he can offer complete one-off engines and boost systems for each individual customer. Jim, in turn, is able to take Johnny’s custom-made plenums and adapt them for volume production, so he can offer complete Kenne Bell forced induction systems with the most efficient plenums possible. Each party can offer the best product to their customers.
In a way, the whole process is about loss prevention —preventing loss of pressurization, loss of power through unintended higher fuel/air temperatures, loss of intake volume due to poorly-designed intake plenums and inefficient intercoolers, and other factors. Johnny Lightning’s skills, coupled with Jim Bell’s testing and manufacturing facilities, allow individual racers as well as retail customers, buy the boost system that best suits their needs.
In order to extract maximum power from a performance engine, especially a boosted engine, precise tuning is a must. With virtually all vehicles built in the last dozen years or so, engine management is controlled electronically, So engine tuning must likewise be done electronically. Johnny uses exclusively software from SCT, a leading supplier of performance tuning hardware and software. This advanced equipment offers standard packages for mildly-modified engines, plus a sophisticated computerized system for individual custom tuning. With this advanced system, Johnny can set shift points, change transmission shift pressures during shifts, provide fuel and ignition curves for optimal performance, set rev limits, and even adjust for different size fuel injectors. The use of the SCT programming allows Johnny to program and calibrate each individual engine to match customers’ needs.
In the meantime, Johnny has built on his years of experience to expand his package of offerings to include a wide variety of performance products for Fords and other makes, including exhaust systems, suspension upgrades, cooling system products, interior accessories and, of course, complete engine assemblies.
Johnny is just one more example of today’s innovators that carry the hot-rodding spirit to the next level, developing tomorrow’s technology today. He’s living proof that Lightning can strike more than once…
Loss Prevention is the Key
Flow benches measure pressure/boost loss through the throttle body, inlet manifold, intercooler, and discharge manifold, in that order. The goal is to minimize the pressure/boost loss through these components. Johnny and Jim pursue improved efficiency through more efficient flow, and therefore less boost loss through the induction system. As restrictions are engineered out, more boost and cfm translate into more horsepower.
While boost can be increased with the use of a smaller supercharger pulley, that option is often not possible due to space restrictions. So the next best choice is to optimize flow through the induction system with the least restriction possible. Remember, that every additional psi that enters the combustion chamber makes about 20 additional horsepower in a high end race engine. So it is critical to maximize flow from air intake to combustion chamber. And while you could simply change the pulley drive to achieve an additional psi and the 20 ponies it brings with it, the change in pulley drive will bring with it parasitic loss through the supercharger drive system.
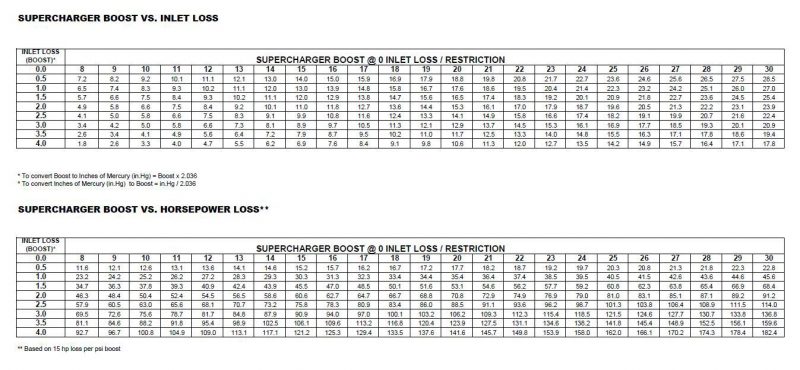
0 Comments