In this final article of a series designed to improve understanding of Nissan camshaft control systems, we’ll take an in-depth look into the system that controls variable valve timing in Nissan engines, including sensors and solenoids, and how to diagnose problems with them.
For a review of the two previous articles on Nissan camshaft controls, you can read the first article; Timing is Everything in the Summer, 2015 issue of Nissan TechNews and Understanding Camshaft Control Systems Part II: Servicing Timing Chains & Sprockets in the Fall, 2015 issue. Both can be viewed on the Nissan TechNews website at NissanTechNews.com. |
In this article, we’ll discuss Nissan valve timing systems and how they work, with a focus on the QR25 engine in the 2015 Nissan Altima. We’ll learn what camshaft phasing is, and why it is beneficial. Then we’ll look at the sensors that are used by the ECM to monitor variable valve timing, and explain how the ECM controls solenoids to achieve proper camshaft timing. Once we understand how all the different parts of the system work, we’ll look at common failures and how they affect drivability, and discuss how to diagnose and repair these failures.
Camshaft phasing refers to the change in timing of the camshafts in relation to the crankshaft, and to each other. It’s important to understand that the duration and lift of valve opening remain unchanged during phasing. Phasing is beneficial for a few reasons. Power and torque can be maximized at high rpm, while still maintaining drivability at low rpm. Emissions can be reduced by controlling the amount of exhaust gas that remains in the cylinder. Fuel can be conserved by reducing pumping losses. Now let’s take a look at some examples of the camshaft phasing implemented on the QR25.
Minimum phasing, also referred to as static timing, takes place when there is no Variable Camshaft Timing (VTC) action. The intake valve opens 5° after TDC, when the piston has just begun traveling downwards in the cylinder. The intake valve closes 69° after BDC, when the piston has already traveled over a third of the way back up the cylinder on the compression stroke.
After the compression stroke, the exhaust valve opens 41° before BDC, when the piston is three quarters of the way down the cylinder on the power stroke. The exhaust valve closes 3° after TDC, when the piston has just begun traveling down on the intake stroke. There is no valve overlap under minimum phasing, as the exhaust valve closes 2° before the intake valve opens. Under light load, this reduces pumping losses and emissions without sacrificing torque.
Maximum phasing takes place when the VTC system is active. Intake valve timing is advanced and exhaust valve timing is retarded. The intake valve opens 35° before TDC, while the piston is still traveling upwards on the exhaust stroke. The intake valve closes 29° after BDC, when the piston is on its way up on the compression stroke.
The exhaust valve opens 4° after BDC, just after the power stroke as the piston begins to travel up on the exhaust stroke. It closes 48° after TDC, when the piston is a quarter of the way down the cylinder on the intake stroke. Under maximum phasing the valve overlap is 83°. This increases power under high load by improving flow through the combustion chamber.
Whenever the engine is turned off, the intake camshaft sprocket will become fixed in intermediate lock by the engagement of two lock keys located inside of the sprocket. If the engine is started with a coolant temperature of less than 140°F, the intake camshaft will remain locked in intermediate phase until the coolant reaches operating temperature. In this phase the intake valve opens 5° before TDC, near the end of the exhaust stroke. It closes 59° after BDC, as the piston moves upwards on the compression stroke. This phase has 8° of valve overlap, which is ideal for reducing emissions when the engine is cold.
The PCM requires a means of determining the engine’s position and speed. This is achieved through the use of two sensors. The crankshaft position sensor (POS) and the camshaft position sensor (PHASE). Both are Hall Effect sensors mounted facing a toothed ring called a signal plate. As the engine rotates, and the teeth of the signal plate pass the sensor, the magnetic field in the sensor changes. The change in magnetic field causes a change in the output voltage of the sensor, which is monitored by the PCM.
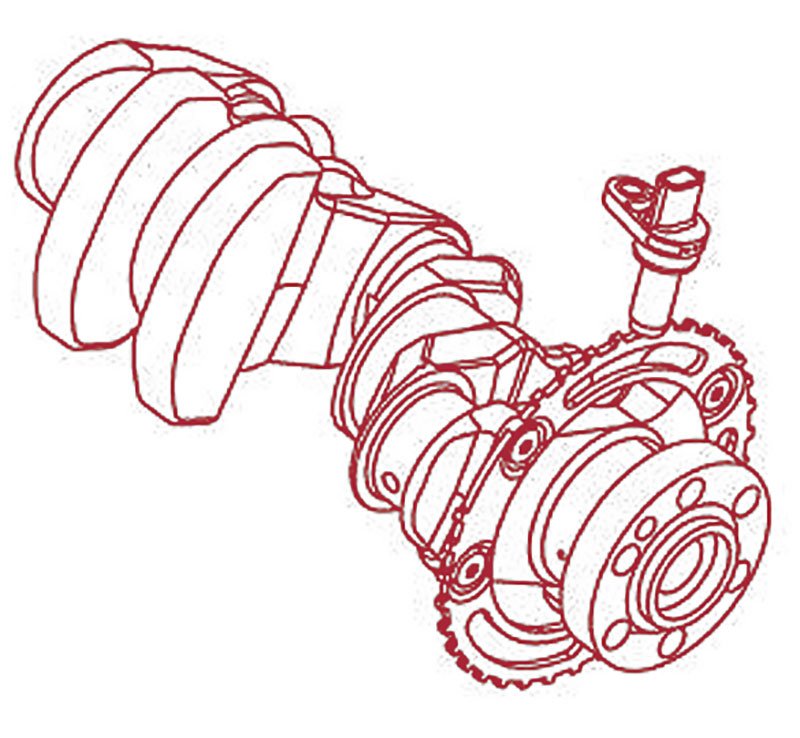
Here we see the how the POS is oriented facing the signal plate on the rear of the crankshaft. The signal plate has teeth equally spaced, with two larger gaps 180° apart that represent pistons at TDC.
Crankshaft Position Sensor (POS)
The POS is mounted towards the rear of the engine oil pan facing a signal plate that is mounted on the engine crankshaft. This sensor is used to detect crankshaft speed, position, and fluctuation. The PCM can determine engine speed and fluctuation from the frequency of the voltage pulses, and engine position from the location of the larger gaps in the signal.
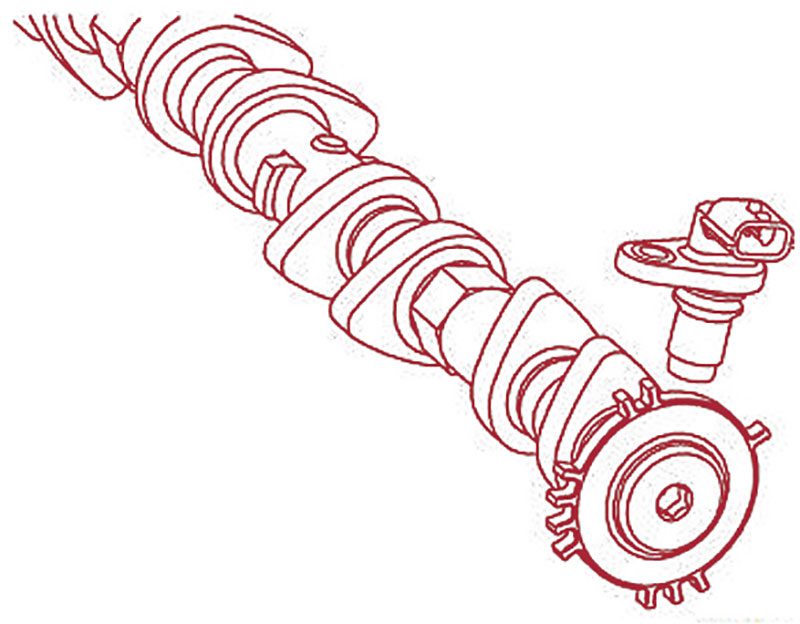
The PHASE is mounted facing the signal plate on the intake camshaft. The four sets of teeth each on the signal plate each correspond with a cylinder at TDC compression.
Camshaft Position Sensor (PHASE)
The PHASE is mounted on the camshaft position sensor bracket, located just rear of the rocker cover, facing a signal plate mounted on the rear of the intake camshaft. This sensor is used for cylinder identification, and produces a unique pulse for each cylinder. Failure of this sensor can result in hard start/no start condition, rough idle, or misfire.
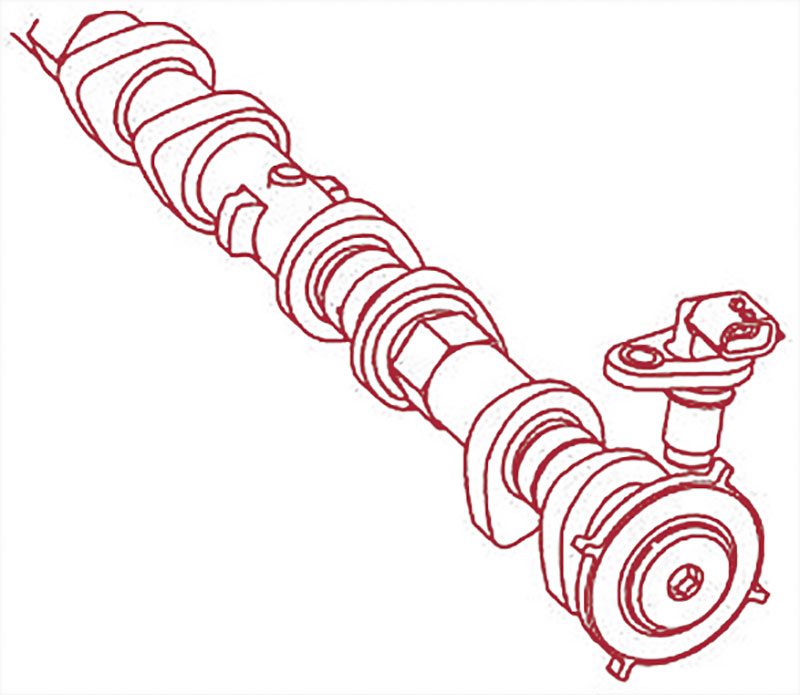
This is the Exhaust Valve Timing Control Position Sensor and its signal plate mounted on the rear of the exhaust camshaft. The signal plate has four teeth equally spaced.
Exhaust Valve Timing Control Position Sensor
This additional Hall Effect sensor is mounted next to the PHASE sensor, facing a signal plate on the rear of the exhaust camshaft. It is used to monitor the position of the exhaust camshaft, and confirm commanded changes to exhaust valve timing.
Solenoids
The PCM controls solenoids to implement desired changes in valve timing. These solenoids divert oil pressure to the proper chambers in the camshaft sprockets. The QR25 engine uses three solenoids for valve timing control. The intake valve timing control solenoid and the exhaust valve timing control solenoid are three position solenoids controlled by on/off pulse duty signals generated by the PCM. A duty cycle of less than 50% will retard the camshaft, while a duty cycle greater than 50% will advance the camshaft. A duty cycle of exactly 50% will maintain current camshaft timing. The intake valve intermediate lock control solenoid is a two position solenoid. When commanded on, it drains oil pressure from the intermediate lock keyways. When commanded off, it blocks oil pressure allowing the lock keys to release.
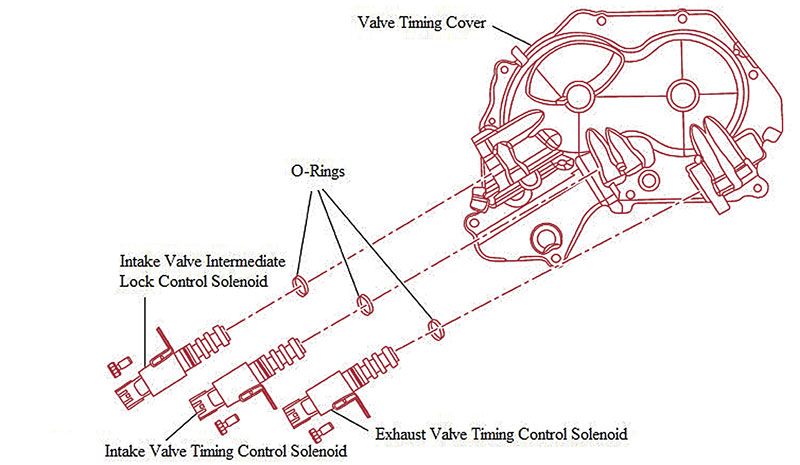
Here we can see where the three valve timing control solenoids mounted in the valve timing cover, located in front of the camshaft sprockets. Be sure to replace the O-rings when the solenoids are removed.
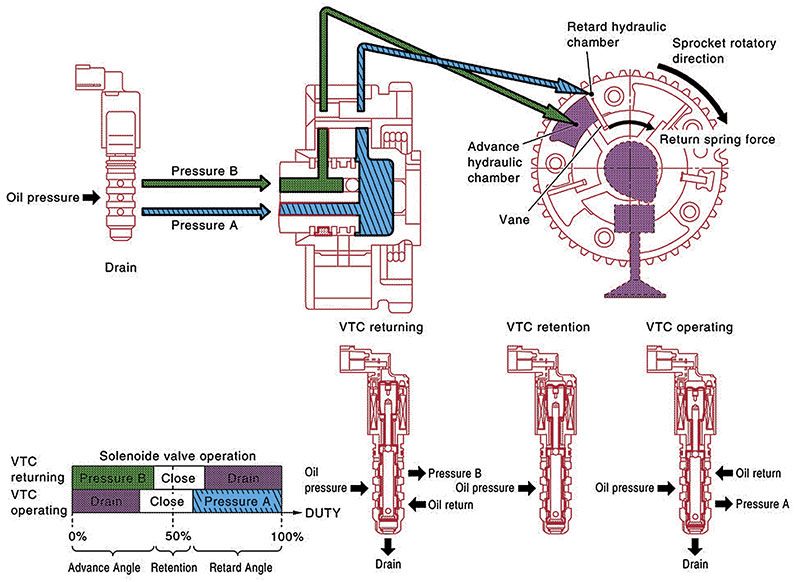
Here we can see how the exhaust valve timing solenoid works. The exhaust camshaft sprocket is held fully advanced by spring tension until the VTC activates to adjust valve timing.
Valve Timing Control DTCs
The DTCs that we will focus on involve the valve timing control system of the QR25. They are:
- P0011 IVT control
- P0014 EVT control
- P0075 Intake Valve Timing Control
- P0078 EVT Control Solenoid Valve
- P0335 CKP sensor
- P0340 CMP sensor
- P052A/P052B Intake Valve Timing Control
- P1078 EVT Control Position sensor
- P0643 Sensor Power Supply.
The first step in any DTC diagnosis is always a confirmation procedure. These differ, depending on the conditions under which the DTC was set. In the case of electrical faults, the procedure may be as simple as starting the engine and letting it idle for five seconds. For faults that only occur under certain driving conditions, there may multiple steps to the confirmation procedure. The first step usually involves looking for a 1st trip DTC with the vehicle stationary, and engine running at a specific rpm. If no DTC is set, the next steps usually involve attempting to recreate the conditions in the freeze frame data. Although it may be difficult to recreate every condition exactly, it is important that vehicle speed is within 6 mph, engine speed is within 400 rpm, and coolant temperature is within 20°F. Regardless of procedure, the goal is the same. To ensure the problem is present, so it can be diagnosed accurately and efficiently.
Once the fault is confirmed, diagnosis can proceed. Remember to always check for TSBs first. Also keep in mind that many of these faults can be caused by low oil pressure, almost always due to low engine oil. Access to a CONSULT III plus can be invaluable, as monitoring live data can be more useful than certain diagnostic procedures. When faced with multiple codes, usually one of the codes will pertain to the actual fault in the system, while the others are just secondary consequences of it. For example, if P0011, P0075, and P0300 are set, we know that intake phase angle is incorrect and we have a random misfire. But the likely cause of the problem is in the intake valve solenoid electrical circuit, so we should begin diagnosis with P0075.
P0643
P0643 will generally be set in addition to other codes, and it should always be addressed first. The PCM sends a 5V reference voltage to many sensors throughout the vehicle. These reference voltage circuits are divided into two groups, each containing half of the sensors. Therefore, if a short circuit develops in one of these circuits, all sensors on that circuit will be affected simultaneously. Procedures for diagnosing this code mainly involve checking for voltage and continuity along various circuits.
P0075 & P0078
When the PCM detects an abnormal voltage in either the intake valve control solenoid, or the intermediate lock solenoid circuit, P0075 is set. P0078 is set when improper voltage is sent the PCM from the exhaust valve timing control solenoid. Despite these codes being phrased differently, they both imply the same thing. There is an open or short somewhere in their respective circuit. The diagnostic procedure for the two is identical, except for the specific solenoids and wiring to be tested.
The procedure involves testing each circuit for power and ground. If the circuit is working properly, the individual solenoids must be tested. The first test is a check for continuity between certain terminals, and then measuring the resistance of the solenoids coil. Resistance specifications vary, but generally should be between 7 and 8 ohms at 68°F. If the solenoid passes the electrical tests, check movement of its plunger. Briefly apply 12V to the solenoid, and then interrupt it. This will cause the solenoid’s plunger to move back and forth. Be sure that it moves through its entire range and doesn’t bind at any point in its travel. Power should never be applied to the solenoid for more than 5 seconds, or its coil may be damaged.
P0011, P052A, P052B, & P0014
These codes are set when there is a gap between the target angle and the measured angle of the camshaft. P0011 is set when the intake camshaft is out of phase at operating temperature, and P0014 is set when the exhaust camshaft is out of phase. P052A is set when the intake camshaft is over-advanced at cold start, and P052B is set when the intake camshaft is over-retarded at cold start. Possible causes include faulty sensors or solenoids, clogged oil passages or filters, problems with signal plate, and even a stretched or misaligned timing chain. The diagnostic procedures for each of these codes are basically identical.
Diagnosis begins with a check of the appropriate solenoids as outlined in the P0075 diagnostic procedure. If the solenoids are within specifications, the POS and PHASE sensors must be tested. The procedure, as detailed in the service manual, consists of a visual check for any obvious external damage to the sensor or its signal plate, and a resistance measurement across the sensors terminals. These tests are certain to identify a completely failed sensor, but an intermittently failing sensor may pass these tests and still be faulty. The dual trace oscilloscope function of the CONSULT III plus is very useful, and can be used to monitor the signal from both the POS and PHASE and pinpoint fluctuations caused by an intermittently failing sensor.
If none of these tests yield a failed component, the final things to be inspected are the timing chain and the lubrication system. The service manual procedure states that checking static timing should only proceed if any recent repairs may have caused timing chain misalignment. However, the timing chain may be stretched, so static timing should be checked regardless of repair history. The procedure is covered in detail in the previous article of this series, but the two best methods for checking static timing involve either checking the alignment of the POS and PHASE signals on an oscilloscope, or removing valve covers and visually checking alignment marks.
Checking the lubrication circuit begins with removing the three timing control solenoids, and disabling the fuel injectors. Then crank the engine and observe whether oil is produced at the oil holes in the valve timing control cover. If no oil is observed, some disassembly of the timing cover may be required to locate the source of the blockage. Small oil filter screens installed in the timing cover are a good place to start.
Intermittent Incident
If no faults are found at the end of any of these diagnostic procedures, we move to intermittent incident diagnosis. This is detailed in the general information section of the repair manual. All of the procedures are designed to simulate the conditions or environment present when the fault occurred. They include lightly tugging on wires to check for loose connections or internally damage, disconnecting connectors to inspect for corrosion, heating or cooling certain components, checking components for water intrusion, or turning on all electrical loads. Every situation is unique, so let the known facts guide you when determining which of these tests are appropriate.
Now that we understand how camshaft phasing works, and how to diagnose and repair faults that may occur, we can service these vehicles confidently and competently. Bear in mind that components can fail without setting a DTC, so always consider failures in this system when diagnosing drivability problems that don’t set a code. And remember to always follow procedures listed in the service manual to avoid damaging components or causing injuries.
0 Comments