The mostly cast aluminum structural components of the 2016 AMG GT S cannot be repaired if damaged. Access to replacement aluminum structural parts will be restricted to only those technicians who have received Mercedes-Benz certified aluminum welding and other specialized repair training. Here are a few AMG GT S differences that will require aluminum and other advanced repair skills.
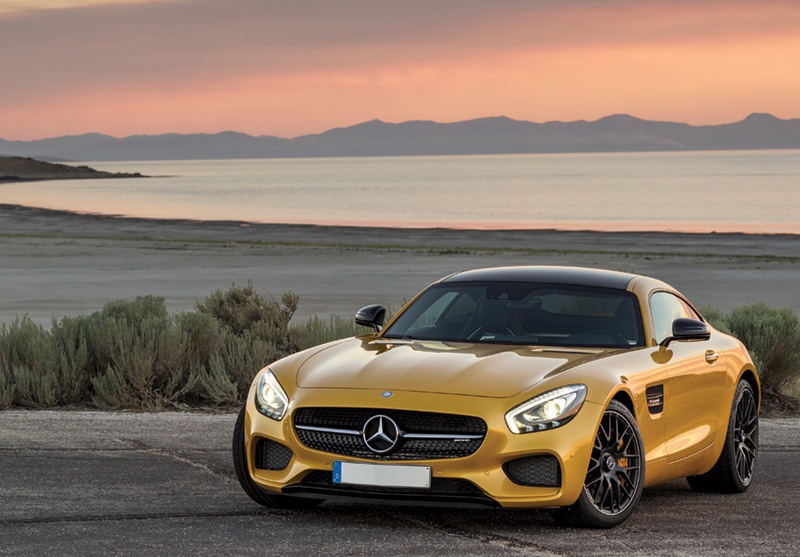
The 2016 Mercedes-Benz AMG GT S is a race-bred, pure sports car with a low-slung, aerodynamic aluminum spaceframe.
The 2016 AMG GT S from Mercedes-Benz is a race-bred supercar with a fire-breathing 4.0-litre dual-turbo V8 that kicks out a maximum torque of 650 Nm before it even reaches 1,800 rpm, and delivers 503 hp. It muscles from 0 to 60 mph in 3.6 seconds, on its way to a top speed of 192 mph. A front mid-engine fitted low in the body, a dual-clutch transmission mounted over the rear axle, and rear wheel drive work together to ensure optimum weight distribution for superb driving dynamics.
AMG gave the GT S a respectable fighting weight by using aluminum for over 90 percent of its body. A front cross-member of magnesium reduces weight ahead of the engine, which combined with the aluminum spaceframe and driveline layout helps give the GT S a 47/53 front-to-rear weight split. This slightly rear-tipped load distribution ensures that drive and suspension forces provide the best possible lateral and longitudinal dynamics, and cuts forward pitch during braking.
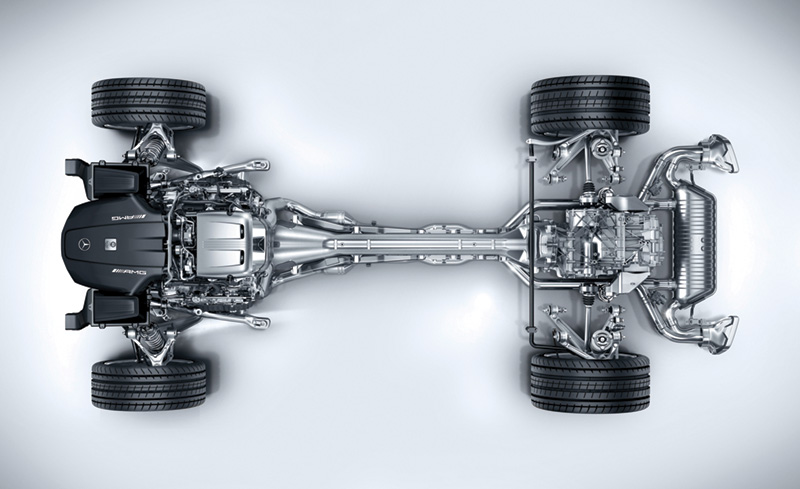
The 2016 AMG GT S with its aluminum spaceframe, front mid-engine, and dual-clutch transmission mounted over the rear axle has a 47/53 percent front-to-rear weight split, giving it the perfect load distribution for outstanding road-handling characteristics.
The aluminum-intensive body gives the AMG GT S both outstanding fuel economy and structural stability for better handling characteristics. It also means that we’ve gone far beyond just door panels and front hood, to where now almost all of the structural components of the body-in-white are made of aluminum. There are still bolt-on aluminum parts, including hood, front fender and door panels, for which collision repair is often a simple remove-and-replace procedure. With an aluminum-intensive vehicle such as the new AMG GT S, however, most structural components now require aluminum welding skills.
Aluminum: Different, but not more difficult than steel
Aluminum alloys melt at lower temperatures than steel. The range between the minimum amount of heat you must apply in order to begin reshaping aluminum and the maximum it can take without the metal being permanently weakened is narrow. Riveting and adhesive bonding are used extensively in aluminum repair as a way to minimize the risk of heat damaging a replacement part, or affecting adjacent components that may be heat-sensitive. These cold-joining techniques are also very useful when joining aluminum to polymers and other materials that have even lower melting points.
Aluminum is also a better thermal conductor than steel, so you must use lower heat settings and monitor the temperature in the heat-affect zone to avoid exceeding the limit, or overheating nearby components.
The untouchables: Cast or extruded structural components
Many structural components are made of cast aluminum. In addition to offering weight reduction and structural stability, cast aluminum components can be precisely tailored to handle load requirements of specific areas, and to dissipate high impact forces along designed paths. Strut towers and pillars are examples of cast aluminum parts. Attempts to cold straighten or heat cast aluminum parts can rearrange the internal structure of the metal, causing it to lose a significant amount of its original strength.
Longitudinal members (frame rails) that once were made of layers of metal welded together are today made by extrusion – pressing heated aluminum through dies to form multiple hollow internal cells for reduced weight, and rigid walls for strength and stiffness. Extruded parts cannot easily be straightened, and not without loss of integrity of their complex internal structure.
Different skills
MIG/MAG welding of aluminum involves different skills from those used to weld steel. The welding rate is significantly higher than that of steel. The welder must be held at an angle of approximately 75° to 80°. If held too flat, the heat and protective gas dissipates too quickly over the surface. This can lead to faulty welding results.
Mercedes-Benz collision repair is divided into four levels based on the skill level required to properly complete the repairs. Levels 1 and 2 are for bolt-on and adhesive bonded or riveted parts, respectively. Any technician with standard Mercedes-Benz training can perform Level 1 and Level 2 repairs.
Level 3 is for welded, non-structural parts, including sheet metal. Level 3+ covers repair of structural components that must be welded. Special training is required for technicians who perform Level 3 and Level 3+ repairs. Technicians that have not received training in Mercedes-Benz welding and aluminum repair procedures are not allowed to perform any Level 3 or 3+ repairs on Mercedes-Benz vehicles. Sales of welded structural repair components are restricted to Mercedes-Benz certified collision repair facilities.
Work-hardening: Greater risk in aluminum than steel
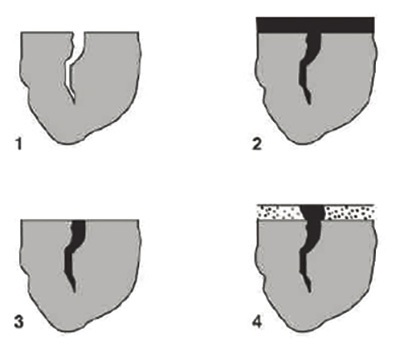
Aluminum stress cracks can be microscopic and difficult to see with the naked eye. Detection involves a four-step process using dye penetrant. First, clean the surface to remove debris, oils, and other contaminants that may hide fine cracks. Second, apply a dye penetrant. Keep wetting the surface for up to 30 minutes to allow penetration into microscopic openings. Third, wipe excess dye penetrant from the surface, leaving only dye that has penetrated into cracks. Fourth, apply a developer to draw the dye penetrant to the surface. This makes the crack visible by contrast of the dye penetrant against the developer material.
Work-hardening occurs when bending stress causes metal to become harder in the bent area. Some hardening is an intentional by-product of the panel forming process at the factory. Work hardening also occurs due to collision impact, and when damage is hammered out during the repair process. This can lead to an aluminum panel becoming brittle and forming cracks. It takes less bending stress to cause excess work-hardening in aluminum than in steel.
Hammer and heat
Re-straightening of Mercedes-Benz structural components is prohibited. Pulling operations increase the risk of cracking in cast or extruded aluminum components, and should be avoided if possible. Sheet aluminum used for hood and door outer panels may be reshaped using drawing-in and planishing.
Work-hardening makes cold-straightening aluminum a bit more difficult. You may be able to tap out minor dents, but for larger areas you must also add heat to soften the metal. To draw in a dent, Mercedes-Benz recommends applying heat between 150° C (300° F) to 450° C (840° F), then cooling the area down quickly. The rapid temperature change causes the surface to contract and the aluminum to resume its original shape.
Unlike working from the outside in when using planishing tools on steel, with aluminum you start tapping in the center of the dent. Press toward the outer edges of the damaged area. To avoid tearing or gouging soft aluminum surfaces, replace sharp-edged and hard steel repair tools with plastic, wood, or aluminum tools.
Thermal expansion within the heat affect zone must be limited. Use thermal pens, self-adhesive temperature measuring strips, or an infrared thermometer/pyrometer to monitor heat buildup. Follow manufacturer guidelines on the use of temperature checking tools.
They may look alike, but…
All aluminum materials are not the same in their composition, strength, and what is most important for collision technicians, response to heat and cold-working repair techniques.
Mercedes-Benz engineers have balanced a variety of chemical formulation factors, including tensile strength (how much the metal can stretch without breaking), ductility (the amount of bending a material can take without cracking), formability during manufacturing, compatibility with other materials in the vehicle, long-term corrosion resistance, and many more. This ability to fine-tune the chemical formulation of the alloy means that the aluminum used in a Mercedes-Benz vehicle may not only perform differently from that of other manufacturers, but may also require very different repair procedures. Even if you’ve had some aluminum repair training, there may be procedures that are specific to Mercedes-Benz that you are not already aware of. Always check in the Mercedes-Benz Workshop Information System (WIS) for specific procedures before finalizing your repair plan.
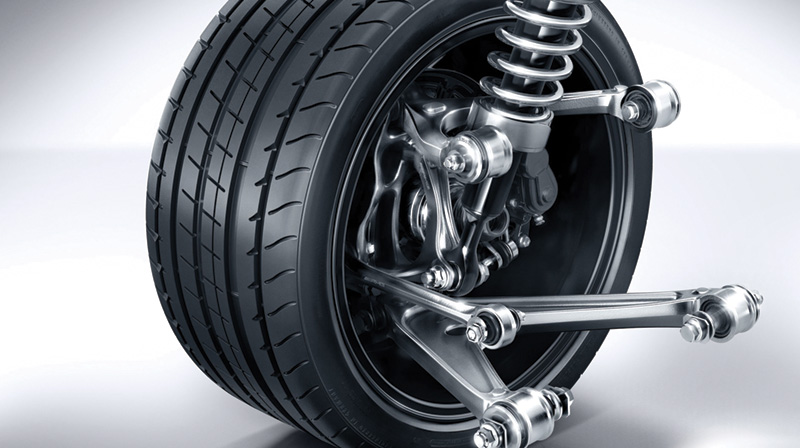
The 2016 AMG GT S uses forged aluminum double wishbones and hub carriers at all four wheels, giving its state-of-the-art Adaptive Suspension system the rigidity needed for excellent road-handling performance while also reducing unsprung weight.
For example, the cast aluminum used for many structural components on the AMG GT S is a proprietary formula that features enough plasticity that it can absorb a high amount of collision impact without breaking. Mercedes-Benz hands-on collision repair training includes a demonstration cast aluminum plate that is bent, then placed in a vise and bent back, all without cracking or breaking. This bend-but-don’t-break property is intended primarily to help protect vehicle occupants in a collision. Once it bends, work hardening occurs. This alters in unpredictable ways the future load-carrying capacity and impact resistance of the component. Even if you could straighten the component, which is highly unlikely, it is not safe for reuse.
It’s curtains for you
You’ll need a separate room or curtained-off area for conducting aluminum repairs. This “clean room†is required to prevent cross-contamination between aluminum and steel particles. If dust from grinding, welding, or sanding steel settles on aluminum, it reacts with moisture in the air to form galvanic corrosion, which degrades and eventually eats through the aluminum.
The clean room must have an explosion-proof exhaust system. This is to reduce the presence of aluminum dust particles, which, in the right proportions in the air, can explode violently if a spark or other ignition source is introduced.
Aluminum repair star
Aluminum repair training is part of the requirement to become a Mercedes-Benz certified collision repair facility. The equipment, tools, and training cost to become certified must be balanced against the potential repair volume in your market area.
The training goes beyond theory to provide extensive hands-on practice in real-world procedures. It will give you a great comfort level with how cold-straightening techniques and application of temperature should be handled differently for aluminum versus steel. You’ll learn how to assess damage to aluminum structural components, what can or cannot be repaired, and if and where sectioning is permitted. You’ll test different setup parameters for creating durable joints using computer-controlled MIG/MAG welding equipment. You’ll set up frame benches with model-specific, dedicated fixture sets for anchoring and component positioning.
After training, you’ll be an expert at obtaining the precise structural alignment necessary to restore the buttery smooth road-handling and industry-leading safety of a Mercedes-Benz vehicle. You’ll also be one of the few able to acquire the OEM parts required for structural repairs. Mercedes-Benz, like many OEMs, restricts sales of certain aluminum structural components to its certified collision centers only.
Materials and repair procedures can change frequently, even within the same model year for a given vehicle, so maintaining your expertise will require frequent training/certification. Always refer to the Workshop Information Systems (WIS) for the most up to date repair procedures.
Precious metal
Tightening fuel economy standards and significant technological advances in aluminum manufacturing encouraged Mercedes-Benz to increase its use of aluminum in recent years. The aluminum-intensive AMG GT S is a harbinger of things to come. Let it encourage you to increase your training in how to repair this precious metal.
0 Comments