This ingenious sensor has been in general use for over three decades, and it’s proved itself to be extremely dependable. That is, if you maintain its living conditions and avoid cheap air filters.
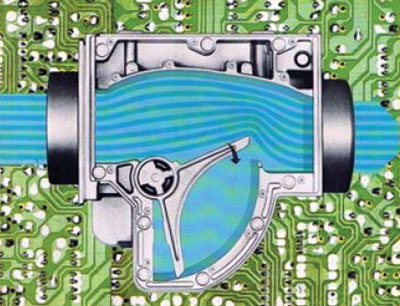
Although you probably haven’t seen one in decades, the VAF (Vane Air Flow) meter was an ingenious Robert Bosch invention — the rotating flap turned a variable resistor to provide a signal to the computer. It’s just not accurate enough for modern requirements, however.
Diagnosing MAF (Mass Air Flow) sensor faults on Mercedes-Benz vehicles requires that you obtain as much information as possible from the customer as to the nature of the problem. Does it have a Check Engine light (MIL) on? Is there poor performance? Hesitation? Fast or uneven idle? A test drive of the vehicle to verify the complaint and then a proper scan for trouble codes is, of course, another prliminary. A trouble code of 2646 may turn up indicating a fault with the left MAF sensor if you’re working on a 164 chassis. Any number of other fault codes may show up that may be related to this important input to the PCM (Powertrain Control Module, the standardized SAE term that replaces ECU and ECM).
Overview
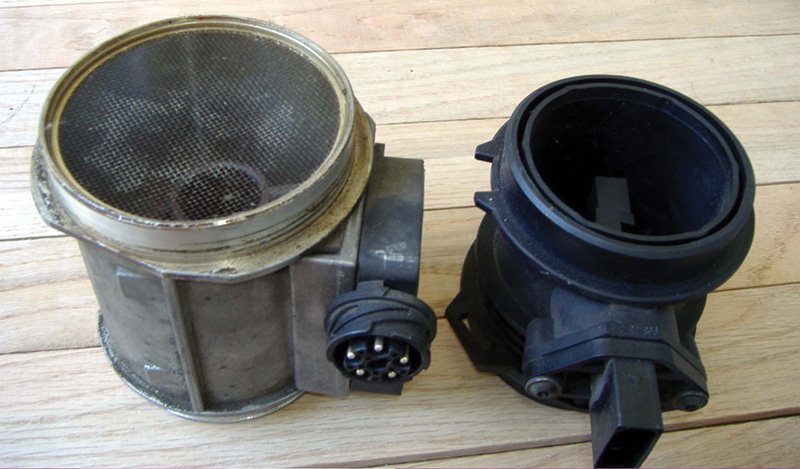
Whether hot wire or hot film, the principle of measuring actual mass, instead of just volume, is the same.
A full understanding of how the MAF sensor operates will definitely help you in fault-finding. An internal-combustion engine is basically a sophisticated air compressor. Air comes in, gets compressed, oxidizes the injected fuel, and whatever may be left exits through the exhaust system. The amount of air coming in needs to be measured accurately for the PCM to be able to produce the proper air/fuel mixture for combustion to happen efficiently.
Some historical perspective is appropriate here. In 1968, mankind was preparing to visit the moon, the environmental movement was becoming big news, and Robert Bosch produced the first popular electronic fuel injection system. That original D Jetronic EFI used a vacuum sensor (the “D†is for “Druck,†which means “pressure†in German) to inform the electronics about the intake situation.
Six years later, the air flow meter showed up on L Jetronic (the “L†stands for the German word “Luftmengenmessung,†meaning “air quantity measurementâ€), also known as AFC (Air Flow Controlled) fuel injection. At the time, we thought the concept was ingenious: A vane rotated against spring pressure according to the volume of air the engine was ingesting, and this movement turned the shaft of a variable resistor, thus changing the 5V reference signal before it returns to the computer. Simple, and much more accurate than anything else previously conceived.
We should mention the older-style speed-density EFI systems that used computer power to calculate the mass of intake air from input on rpm, vacuum, throttle position, and the signal from the intake air temperature sensor. They reached a pretty high state of development, especially among Asian brands, and worked quite well. One of the requirements of OBD II (mandated in 1996), however, was that a MAF must be present in all passenger cars and light trucks sold in the U.S.
Since air/fuel ratios are by weight (stoichiometric is 14.7 units of air to one unit of gasoline — by volume, it would be about 2,000 to one), measuring mass makes more sense anyway. So, LH-Jetronic (to continue our foreign language lesson, the “H†stands for “Heiss,†German for “hotâ€) with its hot wire sensor was introduced in 1984. Why is measuring mass better than measuring volume? Because air changes its density — the number of O2 molecules per cubic unit — as it expands and contracts with temperature and pressure. In automotive applications, air density varies with ambient temperature, altitude, and the use of forced induction, which makes MAF sensors more appropriate than volumetric sensors for determining the quantity of intake air (hence oxygen) that’s entering the engine, upon which (among other things) the PCM bases the pulse width of the injectors.
Wire to film
There are two types of MAF sensors: the early hot wire variety, and the other, now much more common, hot film sensor, or HFM. The theory of operation of the hot wire sensor is similar to that of an anemometer (which determines air velocity). Measurement is achieved by heating a wire suspended in the engine’s intake air stream — like a toaster’s resistance wire — with either a constant voltage over the wire or a constant current through the wire. The wire’s electrical resistance increases as its temperature increases, which varies the electrical current flowing through the circuit, according to Ohm’s Law. When air flows over the wire, it cools it, decreasing its resistance, which in turn allows more current to flow through the circuit since the supply voltage is a constant. As more current flows, the wire’s temperature increases until the resistance reaches equilibrium again. The current increase or decrease is proportional to the mass of air flowing past the wire, not the volume. The integrated electronic circuit converts the proportional measurement into a calibrated signal, which is then sent to the PCM.
The hot film MAF works on the same principle, but is more robust and less prone to problems from contamination.
For any MAF, volume and pressure are not important, only the weight of the air entering the engine is. That is why it is called a Mass Air Flow sensor, using the scientific definition for mass: The property of a physical object that measures the amount of matter it contains. Mass is also what causes an object to have weight in the presence of gravity.
Keeping it hot
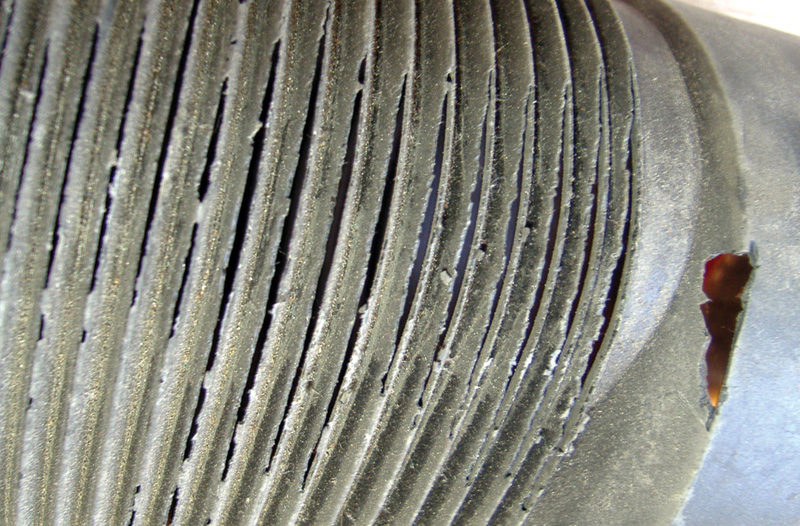
Damage and perforation of the duct between the MAF and the throttle body may have caused many perfectly good sensors to be mistakenly replaced. Better materials and construction are gradually eliminating the problem.
A MAF sensor has some other advantages besides its ability to account for density: no moving parts, restrictions, or compensating sensors. An early MAF’s wire element is kept heated to a specified temperature above ambient (82 deg. C, or 180 deg. F. in a typical unit) and is exposed to intake air. Through a Wheatstone bridge circuit and dedicated electronics, the amount of current required to maintain that temperature becomes the signal to the computer. High air flow obviously has a greater cooling effect than low, but so does the denser air of cold days and low altitudes, so the engine management computer gets the true data on mass it needs to provide the proper injector pulse width for efficient combustion.
At idle, the low airflow level requires little additional current to maintain MAF temperature and the signal to the computer is typically about 0.6V. At wide open throttle, the rush of air requires a much greater current to maintain film temperature, and the signal to the computer can be more than 4V.
Complaints
Problems with a MAF typically generate consumer complaints of low power, stumble or hesitation, rough idle, both cold and hot hard starting, and possibly stalling. Of course, the symptoms you may want to blame on a bad MAF can also be caused by other defects. So, always check the basics first: ignition, compression, fuel pressure and volume, etc.
Always do a through visual inspection for an air leak downstream of the MAF. Unmetered air, commonly called “false air,†entering the engine behind the MAF isn’t accounted for by the computer as it sets injector “on†time. The resulting lean condition causes all kinds of drivability complaints. Leaks from deteriorating air ducts, PCV hoses, etc. can be hard to find, so do an eyes and hands inspection — look closely at the ducts and hoses and squeeze them to detect cracks, holes or mushiness.
Where there’s smoke there’s a leak!
The use of a smoke machine is one of the best ways a technician can confirm the integrity of the intake ducting. Of course, the engine needs to be off in order to use this leak-detecting device. Find a place in the intake system where you can introduce the smoke. A vacuum port is ideal, but most smoke machines will have adapters that you can use to put the smoke where you want it. Be sure to block off the ductwork where outside air is pulled in. Simply look for smoke — you’ll often be surprised at where it’s coming from.
Sealing problems between the air filter housing and throttle body can cause faulty readings in air flow numbers. The intake air line upstream of the air filter and the clean air line between the air filter and the turbocharger are places to inspect. Check the intake air lines for leaks. Visually inspect all connections for leaks, cracks, incorrect assembly and correct as needed. Check the charge air system (green seal ring between turbocharger and charge air line to noise damper, seal rings at the connections between the charge air hoses and the Henn couplings). Visually inspect all of the connections for oil leakage, cracks, incorrect assembly, and pinched or damaged O-rings on the charge air hoses.
There is one somewhat dramatic approach to MAF testing you can use, especially when engine performance is really raggedy. With the key off, unplug the MAF harness, and start the engine. If performance is noticeably better in the resultant “limp -in†or “fail-safe†mode, it’s time for a new MAF.
No MAF can do its job if it isn’t getting power. There are two power feeds to a MAF. One is the OBD II input voltage, and the other is the current feed to heat the wire or film. If either feed is missing, the MAF won’t work, but the problem is somewhere in the wiring, not in the MAF itself. You can check MAF output voltage with a digital voltmeter or a lab scope. You should see a smooth, linear change in output voltage to the PCM as engine speed changes. Some technicians blow shop air into the MAF when testing to see if the voltage increases. In addition to a smooth change in voltage, compare output readings at different engine speeds to the Mercedes-Benz specs for the model and engine you are working on.
If output voltage shifts are jerky, not smooth, or if the readings don’t match specifications, it’s time to replace the unit with a new MAF from Mercedes-Benz. Make sure the output voltages match the Mercedes-Benz specs. On some systems, close isn’t good enough. A variance of as little as 250 millivolts from spec can be enough to cause problems.
OBD II continually examines the MAF, looking for out-of-range signals. OBD II also compares the actual MAF output signals received by the computer to expected values based on rpm, manifold absolute pressure, throttle position, and intake air temperature. If there is a discrepancy between actual and expected MAF readings, a trouble code will be set.
A word of caution: Blind faith in codes can get you into trouble. Consider DTCs as guideposts, not as the absolute word on what’s wrong. Do basic testing and rely on your experience before you accept a code as the final verdict on what is wrong.
Dirty
With no moving parts, a MAF won’t break or wear out, but things can still go wrong. One problem is MAF contamination that insulates the hot wire or film, so air movement doesn’t have the same cooling effect. The MAF signal will be sluggish and the value won’t accurately reflect the true mass of the air going by. Contamination typically is caused by a faulty air filter that releases fibers, an air filter long overdue for replacement, aftermarket filters that use any type of oil coating, and prolonged driving in extremely dusty conditions.
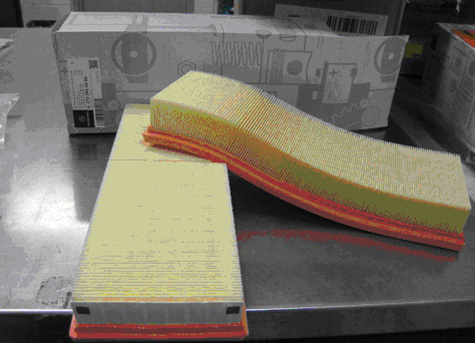
Before you start thinking about replacing a MAF sensor you’re dubious about, look into the filter situation. If it’s not a genuine Mercedes-Benz part, that could be the whole trouble.
If the MAF is contaminated, you have to do two things: Replace the MAF with a new Genuine Mercedes-Benz unit AND solve the source of the contamination—replace the defective air filter, recommend more frequent maintenance service, remove an aftermarket filter that uses oil and replace it with a Mercedes-Benz OE filter, etc.
Genuine article
Why is it important to use genuine Mercedes-Benz air filters? Because aftermarket filters aren’t engineered, tested, or manufactured with anything like the care that goes into the genuine articles. They will probably have different flow characteristics, which can set DTCs. And the real thing will not break down — loose fibers are the main culprits in MAF contamination.
In models with two air filters, make sure each is on the correct side. Be sure to check all the ducting for particles of broken-down filters if an aftermarket unit has been used. When it’s time to replace an air filter, there are some adaptive values that need to be relearned. With your XENTRY or other scan tool, access the CDI engine control unit and follow the path to “Control Unit Adaptations.†Both “Reset Air Filter Learned Values†and “Reset Values for HFM Drift Compensation†have to be performed to ensure proper function of airflow volume calculations in the engine control unit. In many cases, a change of air filters and resetting these adaptives will solve any problems you may have uncovered.
All air filters are not created equal
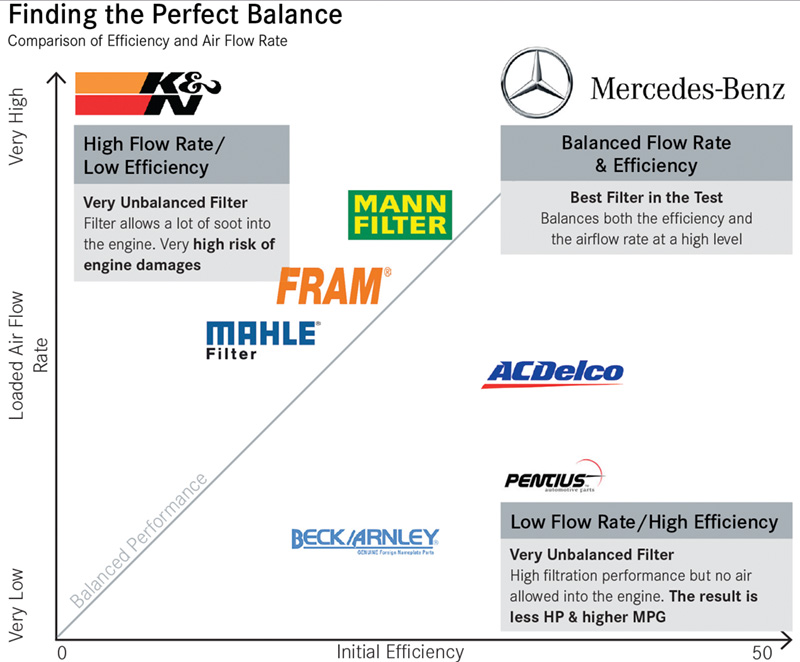
Rigorous testing proves that no aftermarket brand comes up to the quality of genuine Mercedes-Benz air filters.
Why is it that simply replacing the air filter is the answer to solving some of the HFM issues you might encounter? Even after only 18,000 miles, the filter element can become clogged enough to cause trouble. What are we measuring, after all? Airflow, of course, in the form of air density. Another reason is that all air filters are not created equal. A well-designed and manufactured air filter has a good balance between a high airflow rate and filtration performance. Airflow significantly affects a vehicle’s performance (hp) and fuel consumption (mpg). Proper air filtration protects the internal engine components from damage. In a recent test, Genuine Mercedes-Benz air filters scored highest in five categories:
- Filter pleat count
- Dust capacity
- Quantity of particulates filtered
- Filter efficiency (in percent)
- Airflow Rate (pressure drop)
You can see from the exhaustive testing done that using anything but genuine filters can cause you frustration in servicing the HFM systems in Mercedes-Benz vehicles. According to Star Bulletin #S-B-09.10/30, an improperly installed air filter assembly can cause the MAF element to receive turbulent, instead of laminar, airflow due to air leakage at the sealing ring. This in turn can cause 0745, 0749, 2091, or 2095 ME fault codes. Take the time to make sure you’ve installed the filter correctly.
Note: While some technicians may attempt to clean MAF elements with alcohol and a cotton swab, that’s more likely to cause damage and comebacks than it is to cure a problem.
Bottom line
In any case of a possible MAF sensor fault, one of the most important steps will be to consult a Mercedes-Benz service manual and any possible technical service bulletins associated with electronic engine management. There are many good sources and publications both on-line and in print to help with proper service and diagnosis. Working the proper steps and troubleshooting diagram for the particular system you’re working with will save you time, thus help your bottom line.
0 Comments