The “I can’t fix it if it ain’t broke†dilemma.
What can we do when the customer’s complaint doesn’t show itself? Let’s look into the intermittent issues, hidden faults and the misunderstandings that plague our industry. Â
Automotive diagnostics are hard enough. Trying to find a small EVAP leak or a module that is causing a communication code can be frustrating to say the least. Then it gets worse. A customer comes in terrified that her car won’t start, yet she drove it in and it hasn’t had a problem for over a week. Of course, the car starts every time in the shop. Or worse yet, a very sensitive customer insists that his new car has something wrong with the engine, because it makes a lot more noise than his last car. Is something wrong or is it just different? When a problem refuses to show itself you may be tempted to throw in the towel, but don’t give up too quickly. There are techniques you may be able to use to find a solution.
- There are some possibilities to consider with any diagnostic job that comes through the door:
- The problem is real, and present, and you can find it and solve it.
- The problem is real but not present, so you have to figure out how to make it misbehave.
- And the last, most unpleasant option; there is nothing wrong and you are wasting your time.
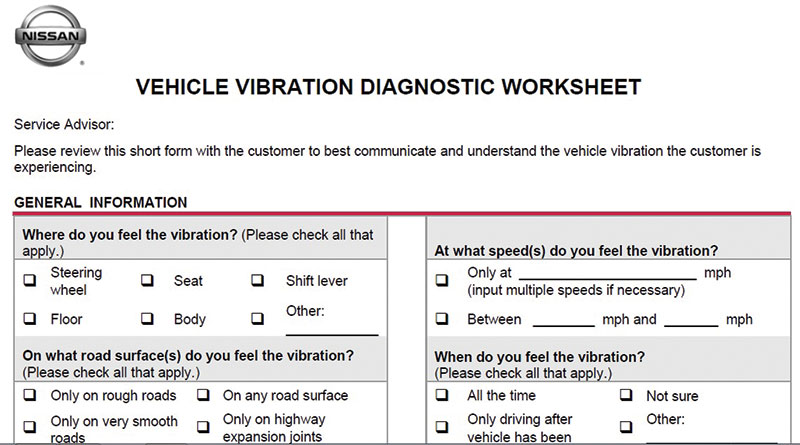
Print page 2 of TSB NTB12-020 and ask your service writer to use it when a customer has a noise or vibration complaint.
This last situation should be extraordinarily rare and will usually involve the owner’s not understanding how some feature of their car works. Think about the “shifting†complaints when CVTs were first introduced. Good communication with your customer will help to prevent most simple misunderstandings.
The first step in any diagnostic procedure is to record the mileage, because your service writer will need that information later and you may forget. But immediately after that you need to verify the customer complaint. How you go about that will depend on the nature of the complaint. Keep an open mind when listening to the customer’s concerns. A very small misunderstanding about what is actually concerning them can make a big difference in where you will look for the problem. Words like clunk, click, bang and stall may mean something completely different to the customer than what you think it means. Getting them to tell the whole story will give you context as to what the words mean to them.
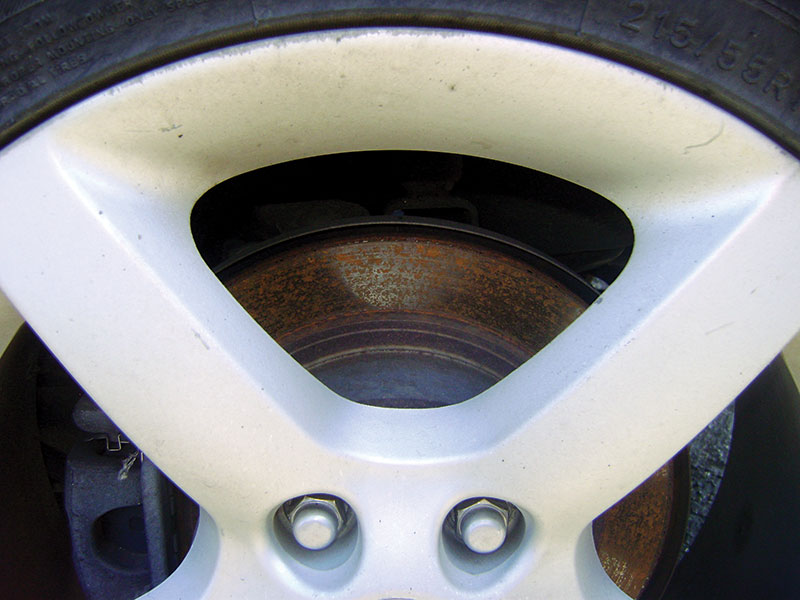
Rust on the rotors means this car hasn’t been driven in a long while. If nothing is obviously broken you may want to put some miles on it before you try to diagnose suspension noises.
A very common area of confusion is in vibration diagnostics. Even if you feel or hear a vibration that concerns you it may not be the same one that the customer is concerned about. TSB NTB12-020 is one of the broadest TSBs put out by Nissan. It applies to all Nissan vehicles and basically consists of a checklist for the customer to fill out that will help you pin down what they are feeling.
Short of actually riding with the customer this may be your best bet in getting to the heart of their concern. If you have the opportunity, you should absolutely take a drive with the customer. Not only will it give you a much better understanding of what their concern is, but it will also give them more confidence in you as a technician. People appreciate that you care enough to take the time to really understand their problem.
Noise diagnostics is really in the same field, as you will seldom have a noise without an accompanying vibration and vice versa. Just listening for any noise may get you into a repair that isn’t what the customer was actually worried about. If a person has been driving their car for years they may not notice a wheel bearing that has been slowly getting louder over the years, but will be very aware of a new buzz in their stereo system. Although you know the wheel bearing is much more important and must be brought to their attention, it’s important to be sure and address the customer’s concern first. You may fix the bearing and still have an angry customer because of a buzzing radio.
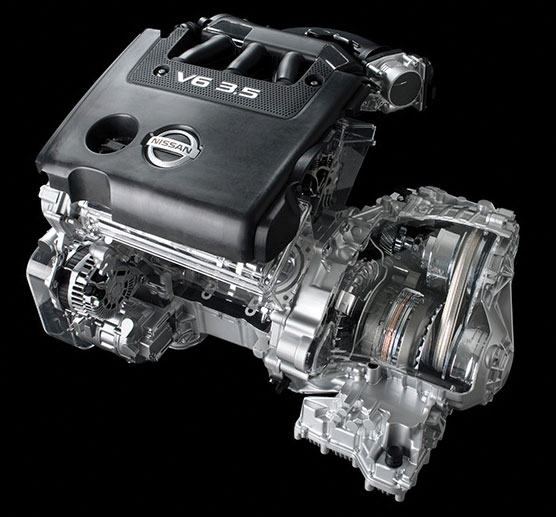
On the outside this may look like your average transmission, but inside it is an entirely different machine. Don’t expect it to work or sound just like a regular transmission.
Where this becomes more difficult is if your service writer doesn’t know to ask the right questions. They may hand you a work order that states, “Customer hears a humming noise.†Being a focused technician you, of course, go for a test drive. An exhaust leak may get your attention, all the while not realizing the customer has, for the first time, noticed a faint road noise from the tires due to a new road surface in his neighborhood. The questionnaire from the TSB may help eliminate such mistakes.
These examples are fine if the vehicle has an actual problem. Often people will be concerned about noises that are part of the normal operation of the vehicle. Being familiar with normal sounds comes with time and experience. Just because you can hear something doesn’t mean it has failed. There has been a recurring issue with CVT transmissions being replaced from technicians hearing noise and condemning the transmission. TSB NTB16-109 addresses this and applies to any Nissan with a CVT transmission. There are a number of examples in the TSB of common noises that a CVT will make, and how to differentiate between CVT noises and other front end noises. The moral of this story is you need to know what the car is supposed to sound like. Comparing a CVT transmission to a non-CVT transmission, in regards to noise, can lead to a serious misdiagnosis.
Although noise and vibrations are very common examples of difficult-to-define problems, intermittent failures can also cause big headaches. Let’s examine an example of a customer that may complain that their 2009 Altima will not start and the customer has diagnosed it to be a failed starter. You may be tempted to just change the starter. Go through all the variables first.
Does this customer know what he’s doing in “diagnosing†a failed starter? Does he even know where the starter is? If his vehicle has the option of a push button starting system, how confident is he that it isn’t a problem with the vehicle’s security system?
Regardless of whether the customer is qualified to make any diagnosis, it will still be bad customer service to change a part if it’s not the problem. Although the cost of a proper diagnosis may make the customer wince, it’s really the best way to protect the customer and yourself. The cost of diagnosing after a new starter doesn’t fix the problem will make him wince much harder.
So you’ve got the customer’s OK to diagnose the no-crank situation. The car is now in your service bay and starting every time. This is the beginning of the first step in diagnostics. Verify the complaint. Just because the vehicle isn’t failing to start doesn’t mean it isn’t having a problem that you can identify. Testing the various systems involved in engaging the starter motor may reveal your culprit.
A graphing multimeter and an inductive amp probe clamped onto the battery cable going to the starter may reveal irregularities in the cranking pattern that would indicate a starter nearing failure. Checking the steering lock for proper operation may also lead you to your solution as these have known issues and happen to control the starter function. In today’s age of aftermarket modifications, looking for an aftermarket alarm or remote start system may lead you to your solution.
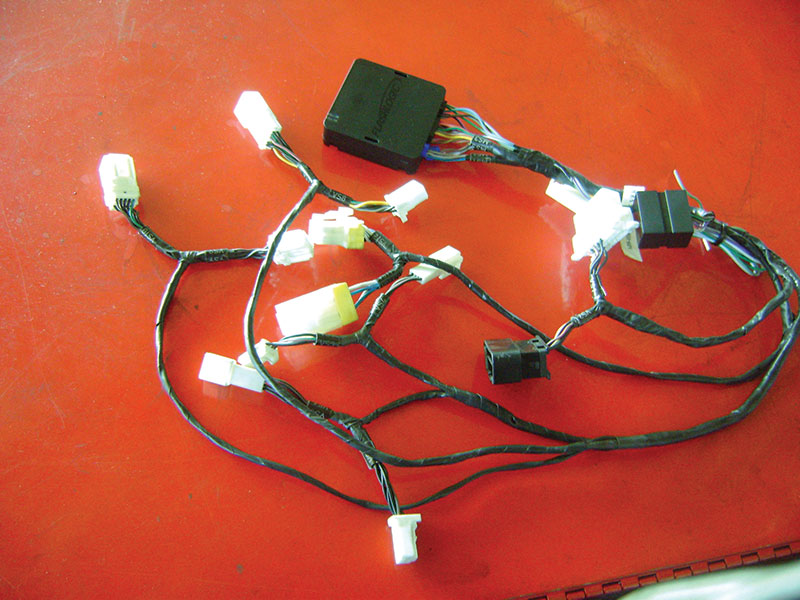
It looks like it belongs, but a keen eye will spot the aftermarket device. Wired in with the push button start on a 2009 Altima, this device was causing a very intermittent no crank. What’s worse is that the customer bought the car used and never even knew it was there.
Intermittent failures can be very frustrating but even worse than that is the customer’s insistence that their car has a certain failure every time they drive. And yet, it won’t misbehave when you go for a test drive. Driving with the customer will often reveal some very weird habits that you may not even consider.
A great example of this is a driver who has developed the habit of braking with the left foot, or more specifically, resting their left foot on the brake pedal while driving. With the ECM-controlled throttle body the car will not allow proper acceleration if it senses the brake pedal is engaged.
Nissan has addressed this in a TSB: NTB14-107, “Check if the driver is resting their left foot on the brake pedal while accelerating. Advise the customer not to rest their foot on the brake while accelerating.†Of course the same problem could be caused by any situation in which the ECM sees the signal that the brake pedal is engaged, but driver error is an easy one to miss as it won’t be reproduced on your test drive unless you take a ride with the customer.
Since 1996 and the implementation of OBDII, ECMs have been monitoring vehicles’ systems for anything that might increase their output of harmful emissions. And certain markets have requirements that vehicles must pass periodic emissions tests. The government has left it up to each state as to how they will enforce their emissions standards, but a common theme in all of them is the vehicle will have to pass all of the OBDII monitors. The idea is that normal driving on surface streets and the highway will allow the vehicle to test all of its systems.
A fairly common way cars fail is when they don’t complete the monitors for some reason. Of course it could be something simple, like the customer thought he could cheat the system and clear his codes right before taking the test, or perhaps the car was parked for 6 months before the test and had a dead battery.
This can be a frustrating problem to diagnose because, in a certain sense, there isn’t a problem. The vehicle runs well and there are no warning lights on the dash. A customer can drive for years with the monitors incomplete without any idea there’s a problem until they fail inspection.
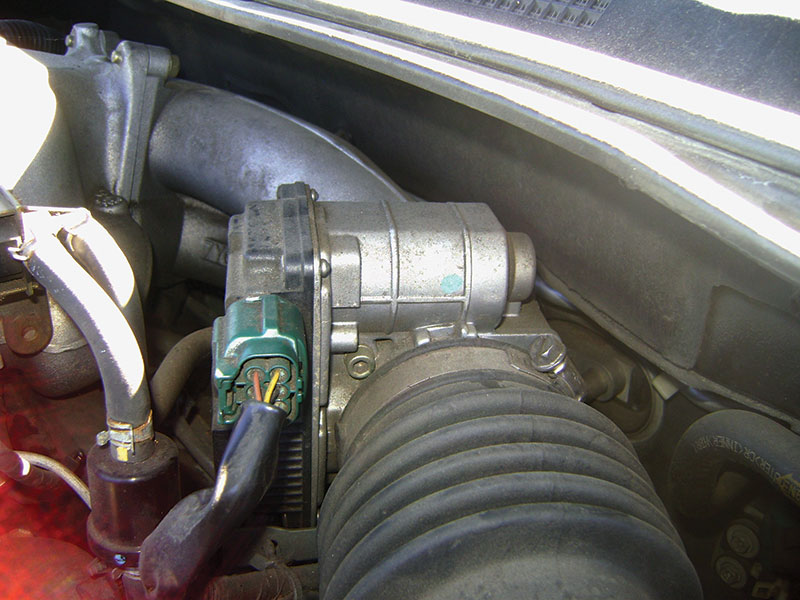
If the computer uses logic to control the throttle and the driver doesn’t, the vehicle might not work the way the customer expects it to.
Getting a vehicle to pass all the monitors is fairly straightforward. System readiness test (SRT) drive patterns are the absolute shortest route to passing the monitors. The standard is different for each manufacturer of course. It’s also different for most models. There is a lovely TSB, NTB98-018g, that covers all 1996 and 1997 Nissan models as well as some good information about general procedures for newer cars. For example, a drive cycle will complete much faster if you have less than half a tank of fuel since the EVAP monitor runs slower on a full tank. The TSB also lists each 1996 and 1997 vehicle by the last 5 digits of the ECM part number and gives a graphic and text description of what the SRT will look like as well as how many trips are required.
If you are trying to get a vehicle to complete all its monitors, be sure to take a quick look at your data stream before you start. For example fuel trims near or over 10 (positive or negative) may not have set a code yet, but clearly indicate that something isn’t working the way it should. MAP, MAF, ECT, IAT, and the rest of the common PIDs should be looked at to see if something is out of place.
If it’s 80 degrees F outside and the data stream for your IAT is at -20 you will have a problem soon even if a code hasn’t set yet. Unfortunately most drive cycles are going to take you about half an hour. When you factor in that many will require two trips, it doesn’t leave much time in the standard one-hour diagnostic time to figure out a problem if you do find one. Making sure your customer is aware of this diagnostic time ahead of time can save an uncomfortable conversation later.
Once in a while you will come across a vehicle that never seems to have completed its monitors. Be aware that loss of battery voltage will cause this to happen. Running a vehicle through its SRT only to have the customer take it home and fail the next day would be very disheartening. It is a good idea to be sure you know why it did not have its monitors complete.
Customers don’t always use their vehicles in the most logical ways. Some drivers are very well versed in jump starting their car as they have a tendency to leave the lights on or the doors open, killing the battery overnight. If you don’t know why the monitors are incomplete ask the customer if they have had a dead battery recently and stress the importance of trying to keep that from happening. Vehicles that are going to be parked for long periods of time may benefit from having a trickle charger installed to prevent battery drain.
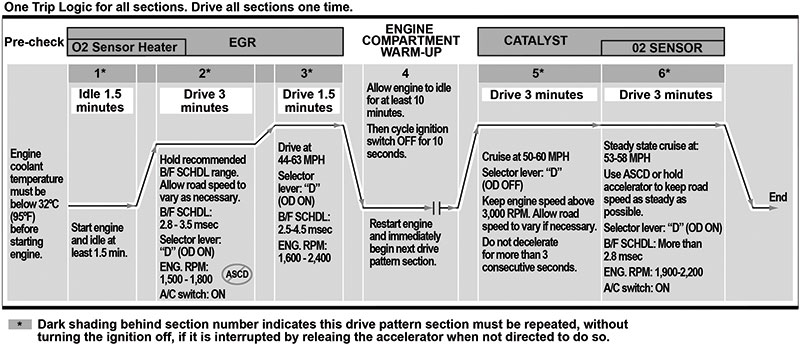
This pattern will lead you to the quickest completion of the OBDII monitors for a 1996 Pathfinder. Finding a road where you can drive these speeds for the time required is another matter.
When you have a case with an intermittent problem that isn’t presenting itself it can be tempting to tell the customer, “It will have to get worse before we will be able to diagnose it,†and send them on their way. Giving the customer more confidence may be better customer service. If you aren’t hearing the noise or feeling the shimmy the customer is complaining about it can feel like you are wasting your time. From the customer’s perspective they might be worried that they are going to break down on the highway and have a nervous breakdown right there in front of the whole world. But they are bringing it to you, the expert, to try and prevent that from happening.
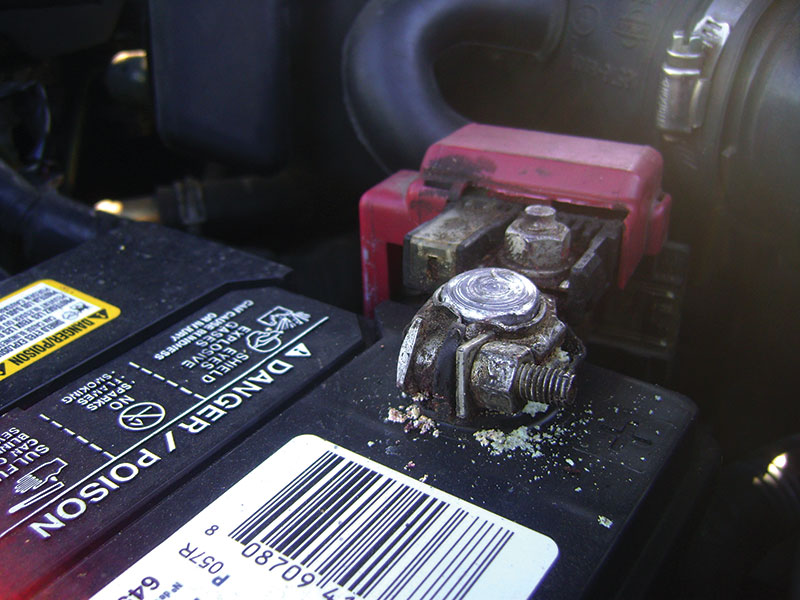
Customers may not be concerned about the things they should be concerned about. Having to frequently jump start their car because of a loose and corroded battery terminal wasn’t important until it caused them to fail their emissions inspection.
Taking a few minutes to inspect the rest of the vehicle, especially the safety equipment (brakes, steering, suspension and fluids) will go a long way in giving them confidence that you aren’t just brushing them off. Even from a strictly business perspective, sensitive customers are much better than apathetic customers who drive their car into the ground then want you to fix the absolute minimum to get them back on the road. Maybe this perspective can make this kind of frustrating job a little better.
You may be noticing a trend here. TSBs are excellent places to look when a problem, or lack thereof, has you stumped. There usually will be a solution; the question is, do you have the time to find it? Today’s Nissans have more technology than ever before. Be patient and open-minded. The brake noise and flashing brake light will sometimes be a parking brake left on, and the dash light not working will sometimes be the dimmer switch turned all the way down. Just roll with it and keep an eye out for something serious. You never know when the next intermittent shimmy might be a tie rod end about to fall off.
0 Comments