Spark generation has gone high-tech
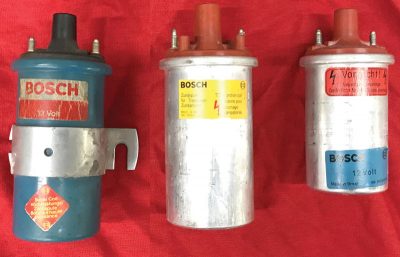
Porsches, it can be argued, are a highly sophisticated and quality car. They are unique in many ways when compared to the everyday “grocery-getters†that many of us drive on a daily basis, but all vehicles share certain requirements. Among these requirements is a high voltage, properly timed spark to ignite the fuel and air mixture in the combustion chamber.
Many of us can remember the days when an automobile engine had only one ignition coil. Occasionally one might have seen a system using two coils if the engine had more than eight cylinders, but that was rare. The good old oil filled, cylindrical ignition coil of the past was an extremely reliable component. So reliable, that it was often overlooked as a possible problem when mechanics were attempting to troubleshoot a performance problem. Oh how things have changed!
No moving parts
The beauty of a coil it that there are no moving parts to break down. Using the principle of electromagnetic induction, a 12 volt current is applied to a relatively small winding around a core of fine wire made up of many more windings. The low voltage windings create a magnetic field and when that field is collapsed, by interrupting power to it, a much higher voltage output is induced in the secondary windings. This increased voltage, often in excess of 50,000 volts, is what is delivered to the spark plugs to ignite the fuel and air mixture.
Challenges
The drawback to having only one coil serve multiple cylinder engines is that a coil’s effectiveness is limited to the amount of time the magnetic field has to build up. This time is referred to as “dwell,†also called “coil saturation,†and it is necessary in order to have a strong magnetic field so that the output of the coil is at its maximum capacity.
Count the number of sparks necessary to run a typical four-stroke V-8 engine. Each cylinder is fired after two complete revolutions of the engine, so four spark plugs must be fired every single rotation. That means the coil has to build up its magnetic field and collapse four times per revolution. At 5,000 rpm the single ignition coil needs to fire 20,000 times a minute! That is a lot of magnetic field buildup and collapsing going on in a very short time span.
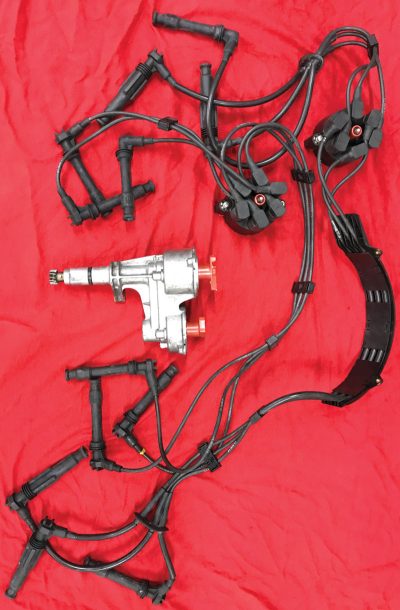
The other drawback is that the single coil ignition system requires an elaborate spark delivery system. Ignition distributors, distributor caps, ignition rotors, and high-tension spark plug wires are all required paraphernalia when using only a single coil. With a system this elaborate, there are lots of potential areas for failure.
Many of us are all too familiar with the common pattern failures in early ignition systems; carbon tracking in distributor caps, spark plug wires leaking to ground and ignition cross-firing, just to name a few. High voltages in ignition wiring can also create a lot of electromagnetic interference (EMI), which is a disturbance generated by all that high voltage current running through ignition wiring, distributor caps and the like. EMI can affect the very sensitive low voltage circuits in a fuel injection system, and can even shut some systems down entirely.
Evolution
It’s no wonder that automobile engineers wanted to get rid of the single coil system. Early efforts brought about a coil system that fired two plugs simultaneously, referred to as “waste spark.â€
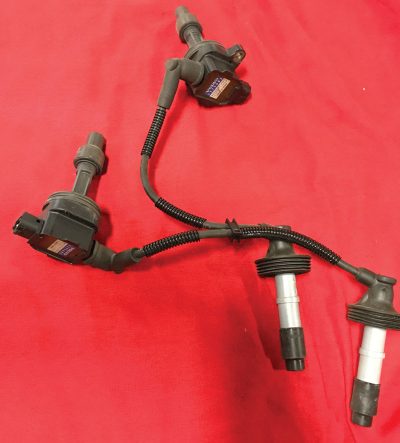
The idea is that a single coil can serve two cylinders. This coil fires two spark plugs serving companion cylinders simultaneously. One spark plug is igniting the fuel air mixture for the cylinder that is on its compression stroke while the other plug is just firing needlessly on the companion cylinder’s overlap stroke.
The reason for firing two plugs at the same time was two-fold: It simplified the triggering of the coil and, by firing two spark plugs at once, it allowed the coil to fire in one direction. That is, the secondary current would flow only in one direction, so the spark would jump from positive to negative on one cylinder while its companion would jump from negative to positive. This can be evidenced by examining spark plug wear.
The plug receiving the “negative†spark would wear out the grounding electrode, whereas the plug receiving the “positive†spark would wear out the center electrode on its spark plug. While the waste spark system does away with the ignition distributor, cap and rotor, it still requires the use of high-tension spark plug wires.
Coil on Plug
The most recent innovation is what most technicians refer to as “coil on plug†systems. Taking the waste spark system to its next logical step, this system assigns a single coil to each spark plug of each cylinder.
Porsche cars, like most modern vehicles, utilize an ignition system that is controlled by the same central processor that orchestrates the fuel delivery to the engine. By controlling both the spark event and the fuel delivery simultaneously, things can be controlled much more precisely and emissions can be kept to a minimum while performance is enhanced.
Modern fuel and ignition management systems are also incredibly fast, so fast that the system has the capacity to change the timing of each cylinder as it progresses through the firing order.
By precisely controlling the ignition event, timing can be altered not only to optimize efficiency and performance, but also to protect the engine from detonation-damaging events. This is especially important for engines with forced induction in the form of supercharging or turbocharging, where detonation is more common. Feedback from knock sensors informs the control unit when to dial back the timing to mitigate the effects of detonation.
Another advantage to coil on plug systems is that the coil now has much more time to build up its magnetic field in the primary windings.
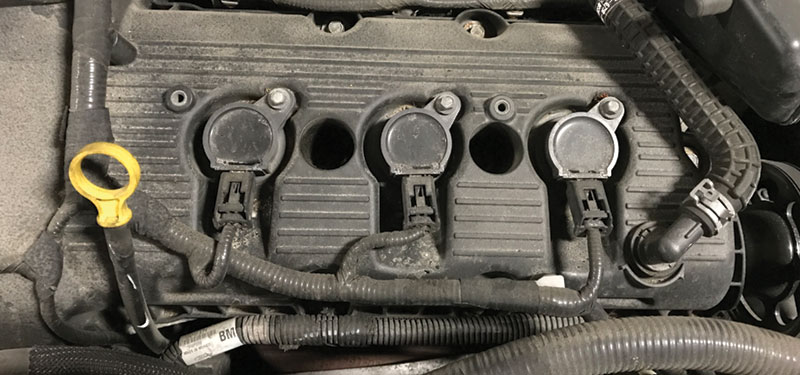
Instead of firing a coil four times a revolution on our V-8 example, a single coil has two full revolutions of the engine to fully saturate the primary windings of the coil, allowing for maximum buildup of spark. This also allows the coils to be manufactured using fewer windings, making them smaller and lighter. The compact design also allows them to be able to fit into relatively small areas, such as on top of the valve or camshaft covers.
Gone are the spark plug wires, distributor caps and rotors. A typical coil on plug design has the coil bolted to the valve or camshaft cover with an electrical suppressor end that attaches to the coil, runs
down a long tunnel through the cylinder head and attaches to the spark plug. This location may seem to be ideal, but there are some significant drawbacks; heat, vibration and that pesky tunnel that the suppressor has to span.
Porsche engines, at least the engines in their sports models, utilize a horizontally opposed layout. Among many other advantages, this layout provides a low profile and low center of gravity. It also provides a challenge for coil on plug ignition systems in that the location of the coil exposes it to not only heat from the exhaust, but all the elements; rain, snow and road grime.
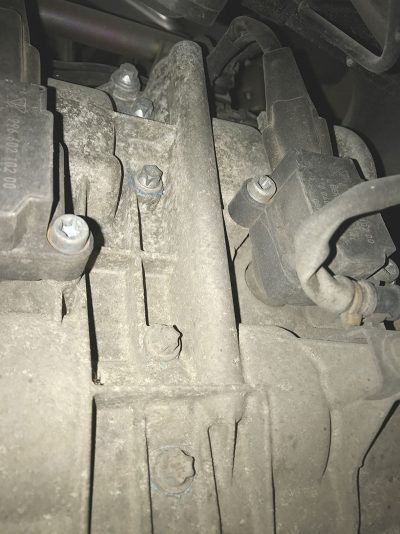
It is especially important to inspect these coils on Porsche engines for damage as a result of rust and corrosion from living in this highly hostile environment.
Ignition coils by nature generate a significant amount of heat due to the constant flow of electrical current. By locating them on the top of a valve or camshaft cover (their more common location) the heat issue is made more problematic. The constant heating and cooling of any component causes breakdown of materials and can be attributed to shortening the lifespan, especially for a component that is relatively fragile to begin with. Now add some vibration in the form of a reciprocating engine sitting underneath it and you’re exposing these poor coils to a double-whammy.
The suppressor connector running down that tunnel to the spark plug also adds some additional challenges for modern ignition systems. The valve cover gaskets can eventually leak into that tunnel and allow oil to pool up around the base of the spark plug and the suppressor connector. While oil is a decent insulator, it can contaminate the connection point and generally make a mess when it is time to change the spark plugs.
Now visualize that suppressor connector running down that tunnel through the cylinder head. Just like a spark plug wire can leak voltage and arc to anything metal, the same voltage can leak through the insulation on the suppressor and arc to ground rather than jump the gap at the spark plug. The only difference is that you can’t see the problem like you often can with external spark plug wires. So it can be difficult to tell if a dead cylinder is a problem with a coil or the suppressor.
Servicing spark plugs on a horizontally opposed Porsche engine presents a few more challenges than a “normal†engine layout as heat shields are often in the way and accessibility is not very convenient.
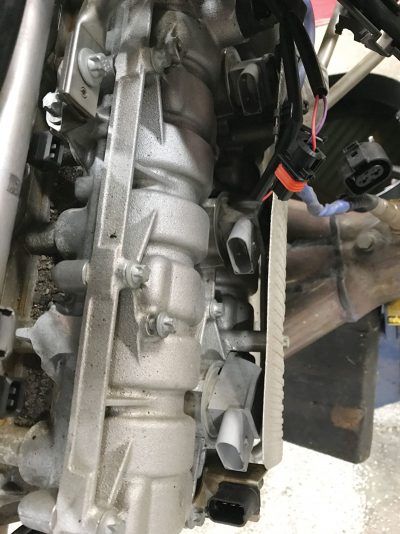
It is important in these situations to carefully evaluate the ignition coils you must remove to access the spark plug. A technician must ask him or herself whether the coils will last as long as the new spark plugs that are being installed.
We all hate comebacks, and conscientious technicians are often concerned about replacing parts that may not seem to be necessary. None of us wants to leave our customers feeling as though we have tried to gouge them by running up a repair bill needlessly. That’s why this is an issue that needs to be dealt with delicately when spark plug replacement becomes necessary.
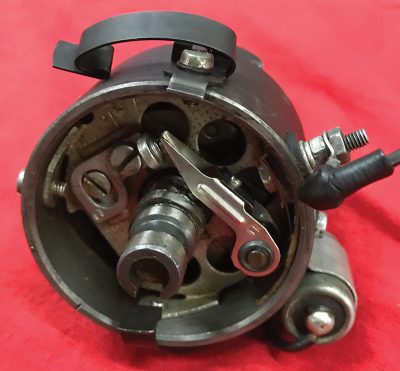
Spark plug replacement intervals are rarely less than 60,000 miles these days. It is impossible to guarantee that your ignition coils and suppressors will outlast two spark plug changes over the course of 120,000 miles. If you, in the spirit of saving a customer some money, re-use the coils and suppressors, who do you think the customer is going to point the finger at if a coil or suppressor fails shortly after the coils have been removed and reinstalled? The random misfire problem following shortly after a spark plug service is, in the customer’s mind, going to point a finger directly back at the technician who performed the service.
Communication is one of the most important and sometimes difficult aspects of the business of auto repair. Establishing a relationship based on trust is the essential first step. By communicating clearly to your customer the pitfalls of re-using parts that may fail in the near future you will be taking steps to build a relationship based on trust.
Download PDF
0 Comments