Painters must account for humidity levels when planning a waterborne refinish job. With a little help from the experts at BASF, we’ve collected tips about how ambient temperature and humidity affect your options of additives, spray application techniques, and drying methods.
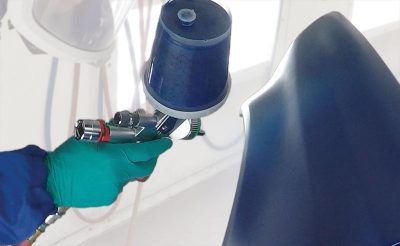
Differences in ambient humidity levels have a major impact on the evaporation rate of waterborne basecoats. Professional painters compensate by choosing the additives recommended by the paint manufacturer for ambient conditions at spraying time, adjusting gun setup, increasing or decreasing how wet they spray each coat, and creating turbulent airflow in the booth during the drying process. Once you learn these key procedural differences versus solvent-borne paints, you will find that use of waterborne basecoats offers faster cycle time and easier color match with OEM coatings.
Coating System Components Are Not Mix and Match
Different manufacturers may use very different technologies to produce waterborne coatings that offer the desired color match and durability. Use of incompatible primers, reducers, basecoats, clearcoats and other products may alter application procedures and color match or finish durability. All of the tips in this article are based on products from BASF Glasurit and R-M Onyx paint systems.
FACT: A higher amount of reducer will produce a thinner paint film.
TIP: In high humidity climates, BASF trainers recommend that technicians adjust the amount of reducer added to waterborne basecoats up to between 70 and 80. Water will evaporate faster from the resulting thinner film, and you will get faster flash times between coats.
FACT: The 50 overlap that is typical of solvent-borne coatings results in less hiding if used with waterborne basecoats.
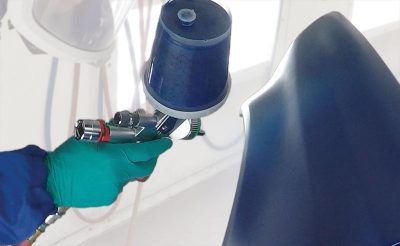
TIP: If you reduce the paint 70-80, and also spray using a 50 overlap, your coverage will be disappointing. Some painters attempt to compensate by spraying wetter, or by spraying more coats. Either way, drying time and cycle time go up as a result.
The better solution is to increase overlap to 70 – 80. You will get a tighter pattern and better coverage, all in fewer coats than if you sprayed using 50 overlap.
FACT: Waterborne basecoats contain 20 pigment in their metallic or pearl formulations, one-third more than the 15 pigment content in solvent-borne basecoats.
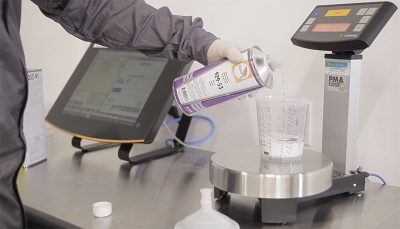
TIP: Thanks to the higher hiding ability of waterborne basecoats you can spray fewer coats and still get the same coverage. BASF waterborne basecoats usually require 2 medium wet coats plus an effect coat to achieve hiding for most colors and to match the selected ColorMax® color chip. Whether you are spraying metallic, pearl, tri-color or some other waterborne coating type, 2 medium wet coats plus an effect (or mist) coat will dry faster than the same color sprayed in 3 medium wet coats.
FACT: In a hot, low humidity climate such as in Nevada, for example, waterborne basecoat may dry faster than desirable. Pigment flakes may not have enough time to settle at the proper depth and angle in the paint film.
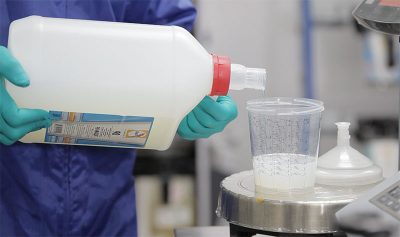
TIP: On a 95 degree F day in Las Vegas, the ambient temperature may be within the normal range for the paint system you are using, but the humidity may be at or below 20 percent in the afternoon (35 percent in the morning). If you are spraying during afternoon hours, the BASF tech data sheet for your paint product may suggest use of a larger gun tip to compensate for the low humidity. This will result in a wetter application, allowing proper settling of pigment flakes during the drying process, and better blending into the panel.
On that same 95 degree F day in Florida or Georgia where you have both high heat and high humidity, you may be advised to use a smaller than normal tip on your spray gun. You’ll get a less wet film on the surface, resulting in a faster flashover than if you had used a larger tip.
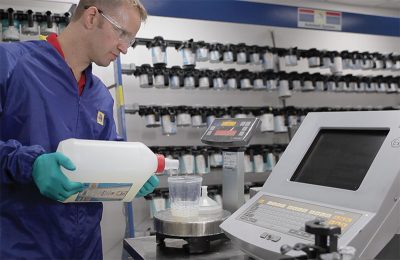
FACT: Without turbulent air movement, waterborne basecoats take longer to dry. The standard laminar (downflow) air in a paint booth follows the contour of the vehicle or parts being painted. As laminar air flows around the vehicle or part, it creates a boundary layer of slow moving air close to the painted surface, even though air that is further away is moving faster. As water evaporates from a waterborne basecoat, this slower moving boundary air layer quickly becomes saturated with water. The saturated layer blocks and reduces the rate of evaporation of additional water from the paint film.
TIP: Use turbulent air flow to eliminate the effects of a boundary layer. Turbulent airflow provides increased air velocity and multi-directional air movement. Air moving in different directions around the part breaks up the boundary layer, encouraging faster evaporation. In a downflow booth, turbulent air flow can be achieved by adding air movement devices that push air horizontally toward the vehicle or part being painted. These can include stationary mounted devices, portable or hand held devices, and ceiling fans mounted at different angles.
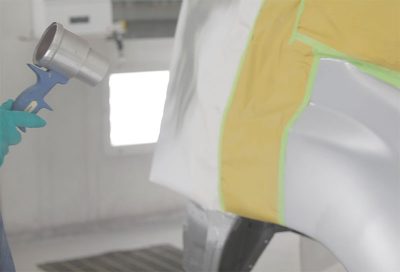
Whether you use a hand-held blower or a fan on a portable stand to create turbulent airflow, always point at a 45 degree angle rather than dead-on (90 degrees) to the panel. Pointing the blower straight at the panel pushes water back into the paint film. Blowing at a 45 degree angle increases evaporation.
If your prep includes blowing dirt off of the vehicle, then cleaning and tacking it, you needn’t worry much about turbulent air depositing dirt onto the freshly-painted panel. When blow drying side panels, keep your 45 degree angle to the panel horizontal. Pointing down may stir up dirt from the floor.
FACT: It is difficult to gauge visually whether or not a waterborne basecoat has completely flashed off in order to apply an additional coat.
TIP: Applying clearcoat over basecoat that is not completely flashed off results in die-back (loss of gloss) in the clearcoat. One very effective and inexpensive tool to assist you is a hand-held digital thermometer. After spraying each coat, point the thermometer first to the just-sprayed panel, then to an adjacent factory-finished panel, and compare the two temperature readings. If the just-sprayed panel is cooler than the OEM painted panel, it is still wet. Like a splash of water on a hot summer day cools your skin, water in the paint cools the painted panel.
Training Assistance
When you convert from solvent to waterborne paint, either a BASF technical trainer, a technician from your coatings distributor, or your coatings account manager is there to provide hands-on instruction. In two to three days of real world practice, they will walk your technicians through best practices for paint prep, gun setup, spray application and other process tips.
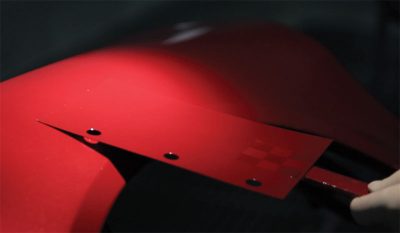
Humidity Adjustment Additives for
| ||
High Temp / High Humidity |
High Temp / Low Humidity | |
Glasurit 90-Line Waterborne Basecoat | 90-M4 Normal Mixing Clear 93-E3S Slow Reducer | 90-M4EDT (Extended Dry Time) Mixing Clear 93-E3S Slow Reducer You may also add M5 Waterborne Blending Clear at a ratio of 2:1 to a mixed color for blending of a difficult color. |
R-M Onyx HD Waterborne Basecoat | 90-HB002 Hydrobase Normal HB040 Hydromix Slow Reducer | 90-HB005 EDT (Extended Dry Time) Hydrobase HB040 Hydromix Slow Reducer You may also add HB055 Waterborne Blending Clear at a ratio of 2:1 to a mixed color for blending of difficult colors. |
0 Comments