History
Turbocharging may seem synonymous with Porsche cars to many of the folks reading this article, but like so much automotive technology it was preceded long before it had been made popular by Porsche. Dugald Clerk was the man who originally obtained a patent for supercharging He got the idea of shoving fuel and air into an engine by means of a Roots style blower, as opposed to just allowing the engine’s vacuum to suck it in, and there was a moment in automotive history genius.
The very idea of force-feeding an internal combustion engine must have caused heads to spin with all the potential of that technology. Then along came the Swiss engineer, Alfred Buchi, who figured out that you could drive a supercharger by using an exhaust driven turbine that captured the untapped power of the heat and velocity of previously wasted exhaust gases. Turbocharging, while being extremely innovative, is nothing more than an exhaust driven supercharger.
Porsche rocked the sports car world when they introduced their 930 Turbo model in 1976. Porsche engineers had turned to turbocharging as a means of competing with cars using larger engines and creating more horsepower than the 3.0 liter, air cooled, horizontally opposed, aluminum engine could produce.
The impetus behind building a street legal version of the 911 using turbocharging was to meet homologation requirements for racing sanctioning bodies. Homologation requirements state that a certain number of cars built by a manufacturer had to be produced and sold to the general public in order to qualify for a specific race class. This was to prevent the manufacturers from building a radical one-off car that was not representative of a vehicle that could be sold for public consumption.
By today’s standards this 3.0 liter engine, producing 260 horsepower, seems unremarkable, but modified and massaged for racing, this car was indeed very remarkable. The street legal 930 Turbo utilized a compression ratio of only 6.5:1 but, with the addition of 12 psi boost, the car accelerated like a rocket when the turbocharger came to life. It wasn’t long before Porsche, as well as many other auto manufacturers, began to add turbocharging to other cars in its lineup.
Over the years Porsche produced many models that utilized turbocharging, and most of these were modified and raced by both factory entries as well as private entrants. In addition to the 930 Turbo, Porsche eventually adapted turbocharging systems to most of its lineup, including the 924, 944 , 964, 993, 996, 997 and 991 models. Because of the advantages that turbocharging provides with emissions as well as horsepower, it is now suggested that most, if not all Porsche models will eventually receive forced induction via turbocharging. Proof of this is the new horizontally opposed, four cylinder engines finding their way into the new Boxster and Cayman models.
As the iconic horizontally opposed six cylinder models evolved, so did improved turbocharging. The models 993, 996 and 997 all benefitted from using two, smaller turbochargers, which greatly reduced the turbo lag issues as well as dramatically increasing horsepower output. Some of the more exclusive models such as the GT2 and GT2RS would produce horsepower in excess of 600.
Nothing, especially horsepower, comes without a price tag. In addition to spending extra dollars to purchase one of these turbocharged models, there is added complexity when it comes to servicing as well. Lack of space in the engine bay of turbocharged models adds challenges when service becomes necessary. Many of the supporting components to these engines, such as intercoolers and exhaust components, have to be removed before other vital components can become accessible.
The basic designs of the actual turbocharger unit vary but there are more similarities than differences. Each unit has two separate housings; a “hot†side that the engine’s exiting exhaust gases use to spin an impeller, and a “cold†side that houses the impeller which creates pressure in the intake manifold. The two impellers are joined together via a common shaft. This shaft must float in a bearing with an excellent supply of oil provided from the engine’s normal lubrication system.
Due to the extremely high rpm the shaft between the hot and cold side impellers must turn, in excess of 100,000 rpm (even higher in some applications), even a momentary loss of lubrication can be fatal. Balance is also critical as the extremely high rpm leaves little room for error. The clearances at this bearing are greater than you might see at a conventional bearing on the inside of an engine. This increased clearance allows the impeller shaft to literally float in a cushion of oil. It is not hard to imagine what 100,000 rpm can do to a bearing and shaft if lubrication is disrupted even momentarily.
Lubrication is one of the areas where many, if not most, turbo failures occur. Turbos run at exceedingly hot temperatures, sometimes in excess of 1875 degrees F. When an engine is shut down, especially on a hot day, that heat has nowhere to go. In fact, temperatures from exhaust components can cause an increase in localized temperatures within a turbocharger unit. These higher temperatures cause oil to break down and form coking deposits, which then restrict oil passages that will then create loss of oil volume and pressure to the turbo’s bearings.
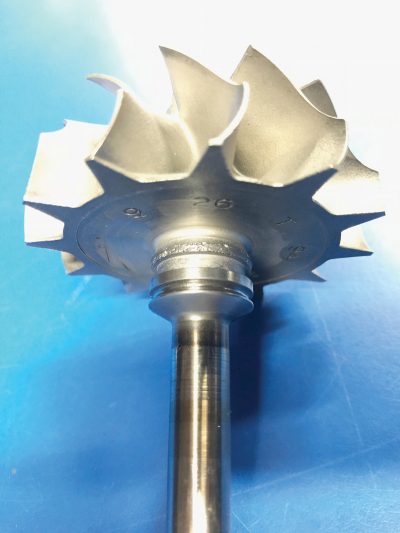
Allowing a hot, turbocharged engine to idle for a minute or two, especially on a hot day, is a great idea. This allows the cooling system to take away some of the excess heat and gives time for fresh oil to circulate and cool the turbo to some degree. It also assures that the turbocharger has plenty of time to spool down from running at 100,000 rpm.
All turbochargers are over-engineered to deliver more boost (overkill) than will ultimately be required by the engine. This is in a large part to address some of the inherent turbo lag issues, having more power available sooner. Additionally, the nature of turbocharging can be compared to a snowball rolling down a hill. The more boost generated at the beginning of the process as it spools up increases the exhaust volume that then spins the turbine faster, increasing boost even more.
To regulate this runaway boost a wastegate is used. This is a very simple device, nothing more than a valve very similar to the valves found in a cylinder head. As the boost increases, the valve, which is controlled electrically or by using a pressure line from the intake manifold, is lifted and exhaust gases that normally go to spin the turbine wheel of the turbocharger are dumped back into the exhaust or simply dumped out to the atmosphere.
The closer a turbocharger’s location is to the exhaust exiting the cylinder head, the better or more efficiently the turbo will run. The expanding of hot exhaust gases increases the flow of exhaust leaving an engine. Directly after the combustion process has ended, the hot exhaust gases are expanding at their highest rate. A properly placed turbocharger will take advantage of these expanding gases by locating the unit as close as possible to the cylinder head.
While this makes sense in terms of efficiency, it creates challenges due to location as it often makes getting rid of the external heat difficult. The more heat added to an already cramped and relatively hot engine compartment, the more problems could arise. The cast iron “hot housing†will glow like an ember when these engines are pushed to the limits. Gaskets, rubber seals, different rates of thermal expansion of various materials are all issues that need to be dealt with when turbocharging is introduced to an engine. It isn’t an uncommon sight to see an older turbocharged Porsche hemorrhaging oil due to various heat-worn seals and gaskets finally giving up.
Intercoolers are often used to maximize the effect of turbocharging. The act of compressing air actually has the effect of raising the temperature. By cooling the incoming air to a turbocharged engine, the density is increased and further power is achieved. This also has the effect of cooling the combustion chamber temperatures as well, which helps control the damaging effects of detonation.
There are essentially two types of intercoolers; air-to-air and water-to-air. The air-to-air are the more common types as they utilize the air in an already accessible stream rather than a separate, cool water supply. These appear to look much like a radiator and they function in a very similar way to a radiator. As the incoming air is forced into the intake manifold, it is drawn through a series of pipes just as water is forced through the pipes of a radiator. The pipes have light fins attached to them that allow heat dissipation to the atmosphere. Thus the air charge is cooled just prior to entering the engine.
Porsches use air-to-air intercoolers on virtually all their cars with turbochargers. The bigger the better and it is all about location. On the air-cooled cars the intercoolers generally live just below the intake air grille on the engine compartment lid. With the water-cooled versions they are often placed in the rear fender well where air is then ducted to them.
“Turbo lag†is a common term used to describe the most apparent driving challenge that is inherent in turbocharged engines, especially with the earlier versions. As one might imagine, the process of exhaust spinning a turbine wheel, coupled with the compressor side building up pressure, there is a significant time delay. This lag time can feel like waiting for a snail to cross a road when a driver is trying to accelerate out of a corner. When the boost finally does kick in, the rush of power is quite exhilarating.
The early turbocharged Porsche 911s used a relatively large turbocharger and lowered the compression ratio of the engine to a very low 6.5:1. The lower compression ratio allowed the engine to pull smoothly under hard acceleration and low rpms. Smooth, however, did not mean strong. When the boost finally does decide to develop, around 4,500 engine rpm, it comes on like gangbusters and the car feels like a rocket. Drivers had to learn to mash on the gas pedal much earlier than with normally aspirated race cars in order to take advantage of the huge power when it does arrive.

The earliest street-going Porsches made a relatively modest 265 horsepower, but their sudden development of power made it feel like much more. The bred-for-racing cousin of the street legal Porsche 930, designated the 935, had water cooled heads and produced around 750 horsepower out of a 3.2 liter engine. Just imagine what the rush of 750 horsepower might feel like as it arrives almost all at once!
Turbo lag was a big reason that Porsche engineers went to the use of two, smaller turbochargers in later versions of the 911. The Porsche 993 had two turbos; one small unit for each bank of three cylinders. The smaller turbos did not require as much exhaust flow to get them spinning, and turbo lag was all but eliminated. These new turbocharged 911 models produced slightly over 400 hp, a significant increase over the more modest 265 hp of the earliest versions.
Porsche provided other goodies to help keep the car planted firmly in concert with the extra power — larger brakes, modified suspension, a wider stance and improved aero bodywork to name a few. Twin turbocharging also gave the opportunity to position the turbos in an ideal location; close to the engine’s exhaust ports and directly under the heads where they can receive the greatest benefit from the expanding exhaust gases, but also with the ability to stay cooler by being closer to air flow under the car. Another notable change was an enormous intercooler that mounted over the top of the engine. This was a simple air-to-air unit, but was essentially all you could see when the engine lid was lifted as it takes up every available square inch of top-side real estate in the already cramped engine compartment.
It was a sad day among Porsche fans when the air-cooled models were discontinued. While the early, water-cooled 996 models were received with a certain level of tepidness, they were actually superior to the air-cooled versions as the heat could be controlled better.
The basic layout of the water-cooled engine was so similar to that of its air-cooled cousin that some of the internal components, such as the crankshaft and connecting rods, were interchangeable. The liquid-cooled engines still benefitted from a dry sump lubrication system while the normally aspirated 996 models had a completely different engine block and did not enjoy dry sump lubrication. Water cooling also resulted in greater power and less turbo lag as these units became more efficient. Redesigned body work and lack of need to accommodate airflow to the actual engine permitted the use of huge intercoolers located in the flared rear fender wells of the 996 as well.
The other Porsche models to receive turbocharging were the four cylinder, entry-level models introduced in the late 1970s and through the 1980s. Porsche’s popular line of four cylinder, water-cooled models, the 924 and 944, were praised for their handling and ergonomics but not for their power.
It was no surprise then that the 924 and 944 models both received help in the form of turbochargers. One might argue that the 924 was the worst Porsche ever built and you would be on some pretty solid ground. Turbocharging added some much-needed punch for the 924, but it only made a reluctant engine slightly more acceptable. The 944, on the other hand, was transformed by forced induction into something beyond acceptable, all the way to extraordinary, and it became one of the best entry level cars Porsche ever made.
Turbocharging added a level of complexity to the servicing of these vehicles, which some folks already considered to be difficult to service. Accessing the valve covers and adjusting the valves of a 930 Turbo, a normal mileage-based maintenance item, required additional disassembly and added easily another three or more hours to the operation. Some of the inherent problems with these engines like cylinder head stud breakage and various gasket ruptures would occur at an earlier time than in the normally aspirated 911. It wasn’t unusual for a routine maintenance visit to a repair facility to turn into a major overhaul if broken head studs and excess oil leakage were discovered.
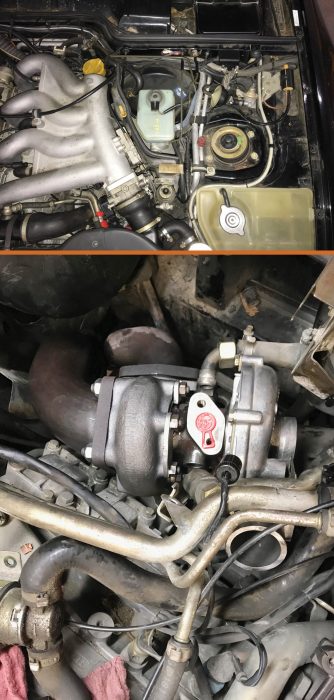
Accessibility of many components, including the turbo itself, was one of the more vexing problems confronting a technician when attempting to replace one of these units on an earlier 930 or, worse yet, a 944 Turbo car. The air-cooled 930 positioned its turbo where it was relatively easy to access once the rear bumper and its trimmings were removed. The 944 Turbo was a very different challenge. To access the turbocharger on one of these models it was necessary to disassemble the entire intake manifold, loosen up the steering rack and remove many difficult to access heat shields and supporting brackets. Being something of a contortionist and possessing many universal sockets and extensions was necessary for replacing these units. Luckily, the turbochargers were reasonably reliable and the need to replace one of these units on either the 930 Turbo or the 944 Turbo was relatively rare.
Additional horsepower was well within reach simply by turning up the boost, which could be done by means of regulating the wastegate. The early 930 Turbo cars and the 944 Turbos had wastegates that were controlled by pressure being applied to a diaphragm on top of a valve. As the boost increased, the pressure on the diaphragm lifted the valve and allowed boost to bypass the hot side of the turbocharger.
The application of the pressure was partially regulated through the fuel management system on the 944 models but the system applied to the 930 was completely mechanical in the sense that the pressure to the wastegate was not controlled by any electrical means. Many savvy tuners would create mechanisms that allowed the boost to be adjusted by means of a simple knob on the dashboard.
There was an over-boost cut-out feature that would shut the fuel pumps off at a certain level, about 14 psi. This safety device would have to be bypassed when modifications to the boost were made. Increasing the boost on the 930 without assuring that there was sufficient fuel being delivered and no over boost protection could have catastrophic results. Engines running lean under extreme turbocharging pressures would cause piston melt-down in a hurry. Contrary to some folks’ belief, a lean engine at wide open throttle will not necessarily run poorly or give the operator warning that something is amiss. Even if it did, the catastrophic meltdown occurs so suddenly that it is unlikely that it would occur without damage even if an astute driver did become aware that something was wrong.
The 944 Turbos often had their boost modified by utilizing a slightly different strategy of restricting the pressure line signaling the wastegate and internal modifications to the EPROMs controlling the fuel and ignition management. The resulting significant increase in power would often be followed by a head gasket failure as the pressures in the combustion chambers were too much for the stock configuration. An updated, improved head gasket that utilized a much wider fire ring would help mitigate this problem.
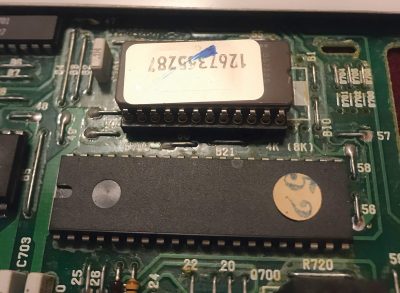
Further reliability could be achieved by machining a small, circular groove cut into the cylinder head that would interface with the middle of the fire ring. A stainless steel wire, which stood about 0.010†higher out of the groove, would then be carefully installed into this groove. The effect of this cylinder head o-ringing process would be that the stainless steel wire would bite into the fire ring of the gasket slightly and help retain its position and strength under higher combustion pressures. This modification was very effective and most head gasket problems could be eliminated even under relatively extreme boost conditions.
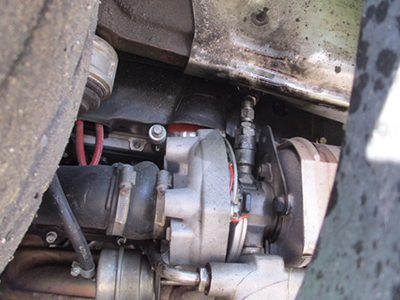
Internal repairs to turbochargers are best left to specialists. Just swapping out bearings and seals is the easiest part of the job as a turbocharger is not that complex a device. What is absolutely critical is the balancing procedure after repairs have been completed. The tiniest little wobble in a shaft or imbalance in an impeller can have catastrophic results. At 100,000 rpm things happen very quickly and self-destruction will not be pretty.
It has been predicted by many astute observers that one day all Porsche models will be turbocharged. The development of the new four cylinder, turbocharged Cayman and Boxster engines would seem to bear this out. Smaller engines create fewer pollutants by weight than larger engines. Turbocharging allows high horsepower yields out of smaller engines, resulting in fewer overall emissions. This is a win for both auto enthusiasts as well as those of us dedicated to preserving our environment.
Download PDF
0 Comments