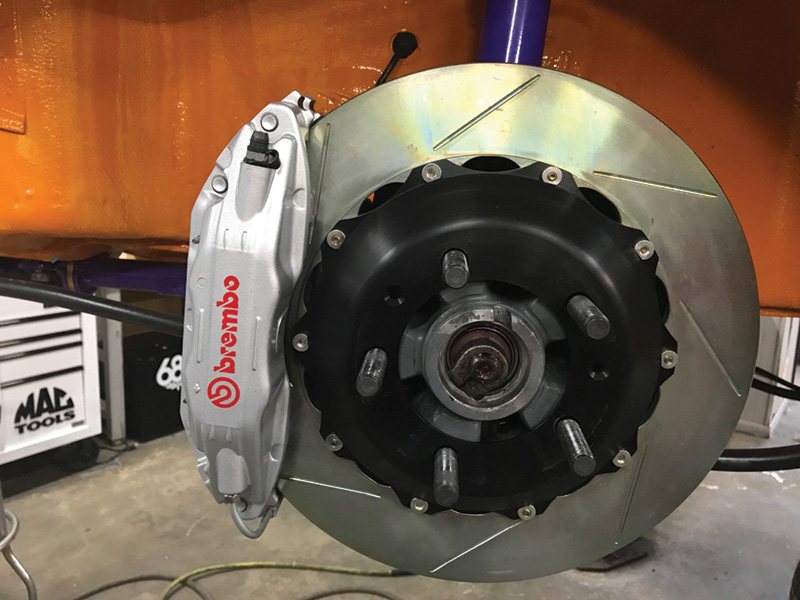
Does any road going 911 need this much braking? Doubtful, but sometimes the upgrades are as much for appearance as they are for functionality.
When the earliest Porsche sports cars hit the shores of the United States, there were a few features that made them stand out. Air-cooling was perhaps the most noteworthy, but overall the cars were noted for their small size, light weight, relatively low horsepower, rear engine layout and big brakes. The low horsepower feature, was certainly not something that you would add to the “plus†column with a performance sports car. This meant that Porsche had to work on other areas of their unique vehicle to be able to maintain competitiveness with the muscle cars being produced in The U.S. The lightweight feature of the vehicles only made the huge braking systems more effective for the so-called “giant killer†known simply as the “356.â€
Early braking systems were confined to drum type brakes. The 356 had what was considered a massive drum even by today’s standards when compared to the size and weight of the vehicle. Big often means heavy, and brakes are a particularly sensitive area to add to a vehicle’s weight because brakes are “unsprung†weight, not being carried by the car’s suspension.
Porsche used a finned, aluminum brake drum with a steel liner which helped considerably with weight and cooling issues. While these drums can be machined, having been built with a certain tolerance for wear, most shops are not equipped to machine them correctly. If the drum’s diameter is over the maximum permissible machine limit, the steel liner or entire brake drum needs to be replaced. This requires not only a deft and experienced hand, but specialized machine tooling in order to get it right. Should brake drum machining become necessary while servicing a 356 with a drum brake system, it’s best to leave it to the specialist who has done this before and possesses the proper equipment to assure a good outcome.
In the late 1960s, the heat limitations of drum style brakes gave way to disc brakes during the last few years of 356 construction. By today’s standards the rotors, calipers and pads were tiny, but they represented a huge technological advance for that time. Regardless of their size, the improved cooling effect that disc brakes provide by nature of their design, represented a significant improvement.
The other advantage that the new disc brakes provided was better serviceability. Rotors were far easier to machine than the old steel lined aluminum drums, and pads were more readily accessed than the conventional drum brake shoes. This provided a significant improvement as pads were easily replaced during endurance races, a venue of interest for the Porsche factory.
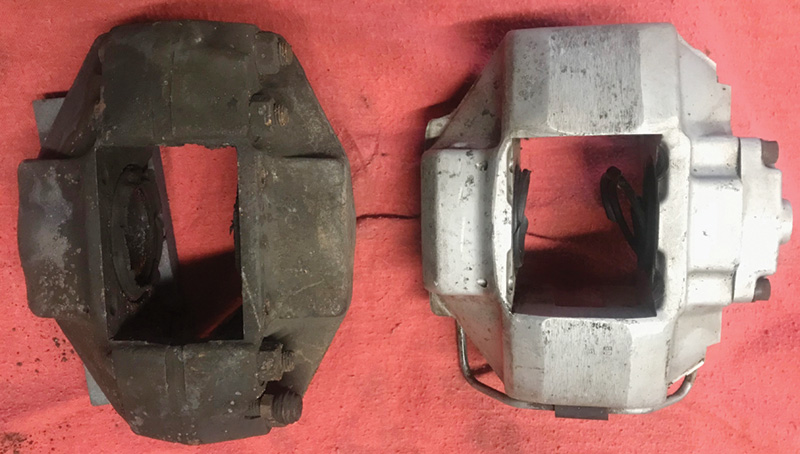
Aluminum is prettier than cast iron but weight reduction was the engineering principle behind the expensive S caliper option. As was Porsche’s custom, brakes could be upgraded throughout the various Porsche 911 line rather easily. Picky customers could also order virtually any braking caliper offered on any model directly from the factory.
Porsche continued with disc braking systems, as did virtually the entire sports car community, from their first rollout until contemporary time. The “new†911 model came equipped with disc brakes at all four corners, taking over where the 356 left off. The flagship 911 model offered different options for the front calipers depending on the level of tuning a given model received. The 911S was delivered with aluminum front calipers that utilized pads with a larger swept area. The front rotors were considered massive for their time and cooling was aided by ventilation through the center of the rotor.
While the light alloy calipers helped with the unsprung weight issue, they were considered a bit problematic due the softer alloy allowing the body of the caliper to flex as the pads were applied, rendering the feel of the brake pedal spongy. This was helped to an extent by re-designing the caliper to be made from one piece as opposed to two halves which were bolted together. While this helped with the soft pedal issue, the aluminum calipers were ultimately abandoned and replaced by cast iron units of the same size specifications.
While most of the automotive world was adding power assist to their cars produced with disc brakes, Porsche was reticent to do so. It wasn’t until 1979 that the 911 model received a vacuum assisted braking system. The 924 and 928 models, in contrast to the 911 models, had come out with power assisted brakes from the onset of their introduction. These water cooled Porsches used a layout virtually identical to most front engine cars of that day, with the master cylinder and boost unit in the engine compartment just beyond the firewall from the driver.
The 911, however, presented a bit of an engineering challenge when it came to adding on a conventional vacuum booster. The source of the vacuum, being the engine, had to come all the way from the rear of the car (where the engine lives) up to the front trunk area, close to the pedal assembly. There wasn’t much room for this brake assist unit as the front trunk was already quite small.
Instead, a rather complex linkage system was run at an angle up from the pedals to the booster through the floor of the front trunk. This booster and master cylinder assembly had to be mounted backwards from a more conventional layout. Replacing the master cylinder provides a bit of a challenge as space is at a premium in this area.
The system was successful, however, and the power assist greatly reduced the pedal effort while maintaining good feedback from the road, allowing for a “feel†that could inform the driver as to how the brakes were functioning.
Antilock braking systems, an expensive addition to any vehicle, were added to the Porsche lineup in 1987. The 944 turbo, a model already a recipient of much development, was the first model to get ABS brakes. While these are an important innovation in the automotive world, many sports car enthusiasts did not initially embrace ABS. There was often a misunderstanding of what exactly their function was supposed to achieve. Drivers lost much of that aforementioned “feel†when the car was on the threshold of brake lockup because that is the moment that ABS would take over, pulsing the pressure at the calipers to avoid a lockup situation.
Another popular misconception was that most people thought that ABS brakes were to allow a driver to stop faster, when the actual intent was to allow a driver to maintain steering control while achieving maximum braking at the same time. Purists were disappointed to learn that in many cases ABS systems increased stopping distances slightly.
Braking systems are an area where bigger can be better. The larger the brake calipers and rotors, the harder they can be used without overheating. As the Porsche models evolved, disc brake systems got larger and more pistons were added to the caliper, giving huge amounts of braking power to their most powerful models. All this was made possible largely due to innovations in materials. Now a monstrous, six-piston caliper can be as light as a much smaller, cast iron, two-piston unit found when disc brakes were first introduced.
Ceramic brake rotors were offered on the high horsepower GT3, GT2 and Twin Turbo models that are currently being produced. As with most braking system innovations, the ceramic brakes were offered to save weight and be able to deal with extreme heat conditions. While the ceramic rotors meet this challenge, they come at a significant cost. Ceramic rotors cannot be machined in the field, and replacement rotors and pads can run thousands of dollars if and when service becomes necessary.
Aside from the ceramic brakes and some accessibility issues with boosters and ABS components, Porsche braking systems offer few other challenges when it comes to servicing. Special care needs to be taken with any braking system, since the results of a mistake can be catastrophic, especially at a race track. Most conventional rotor machining lathes, found in the majority of shops are not sophisticated devices. The finish these lathes leave on a rotor are often inferior to the non-directional, swirl finish left by a stone grinder that was used when the rotor was constructed. The micro-grooved surface left by a rotor lathe will often result in a longer wear-in time and some potential for noise as the rotor and pad surfaces come to know each other better.
Download PDF
0 Comments