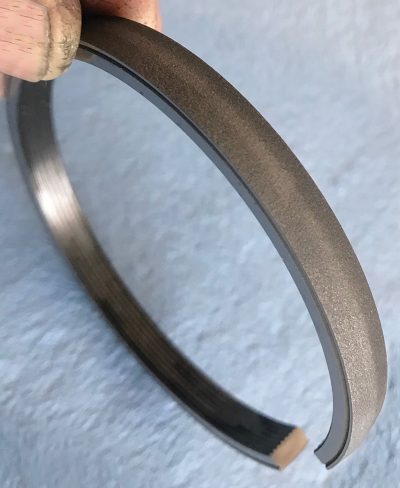
When Porsche first started building their own brand of vehicles, they relied on many components which had already been engineered and put into production for Volkswagen. In fact, Porsche’s original concept was to build sports cars using Volkswagen components. As Porsche grew as a brand, it began to engineer and produce many of its own proprietary components for use in the first 356 models.
Leopold F. Schmidt was a transmission designer for Porsche and was tasked with designing and producing a unique style of synchronization specifically for their new transmissions. This new design concept was to replace the Borg Warner style synchronizer which utilized a cone shaped dog gear. The new Porsche system was innovative but also a bit more complex than the cone-style synchronizer, and therein lie some of its more problematic idiosyncrasies.
As with many of its designs like their transmission synchronizer system, Porsche had a tendency to stay with a concept and develop it as opposed to throwing it out altogether and starting fresh. The Porsche-designed synchronization was found in its first 911s, 912s and 914s models, as well as in several of its race cars including the 904 and 906. This early version transmission, from 1965 through 1976 had the internal factory designation “901.â€
To be clear, the Porsche “transmission†should be referred to as a “transaxle†as it incorporates the final drive assembly; ring gear, pinion gear and differential, in the same main housing as the transmission itself. As the 911 became more powerful, the 901 transaxle needed to be beefed up to handle this additional power and the 915 transaxle was produced. The most notable difference to the driver was that the shift arrangement of the five speed 915 had reverse gear in the same gate as fifth gear, where reverse gear in the 901 transaxle shared its gate with first gear.
Other internal differences included larger gears and shafts, as well as a stronger case. The 914 gearbox was simply a 901 transmission that had been adapted to working in a mid-engine application by flipping the ring gear and re-working the linkage to accommodate the shifter.
Overhaul of either the 901 or 915 transmission requires a certain number of special tools, some of which are imperative to have, others can be worked around. Many of these tools are available in the aftermarket at relatively low cost, while others can be purchased only through Porsche at significant expense. The tooling to set up the relationship of the ring and pinion gears (pinion depth, side bearing pre-load and ring gear backlash), for example, are not available through aftermarket suppliers and must be purchased directly from Porsche or sourced used from a technician selling off tools.
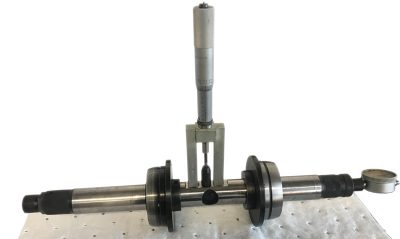
Some or all of the adjustments to the ring and pinion gears may not be necessary if certain components affecting the relationship of the gears are not replaced or serviced. The components devoted to servicing the transmission portion of the transaxle do not require a daunting investment and are the areas which are more prone to require repair and rebuilding. Do not, however, attempt to overhaul a Porsche transaxle without a workshop manual or a reasonable facsimile sourced through one of the several repair information providers to our industry.
The Porsche/Schmidt style of synchronizer incorporates five main components; a brake band, an anchor, a stop, a friction ring and “dog teeth.â€
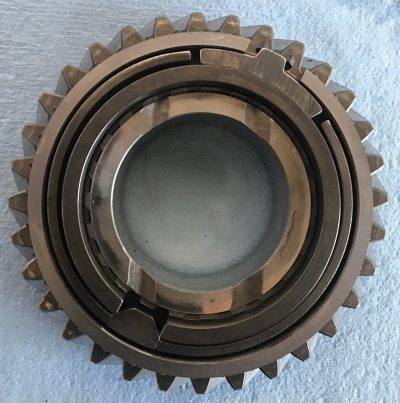
An operating sleeve, which is fixed to its respective shaft, first contacts the friction ring which has a surface that has a rough spatter coating. As the operating sleeve grabs the synchronizer, it turns until it hits the stop. The stop, in turn, then energizes the brake band, which then applies more tension on the synchronizer ring. This action is all to either speed up, (in the case of downshifting), or slow down, (in the case of upshifting) the gear that is going to be engaged. As the gear speed matches the spinning shaft, pointed “dog teeth†allow the operating sleeve to lock the selected gear to the shaft. All of this is happening in split seconds and the integrity of the individual components is key if a clash-free gear shift is to occur.
The system is effective only if the key components are working properly and not worn. If the operator misses a shift, or doesn’t fully de-clutch when moving the shift lever, stress is put on one or more of these components. The rough coating on the synchronizers eventually can be worn smooth with normal use, which then can cause the dog teeth and operating sleeve to clash and wear down the points which are there to assure clean engagement.
The effect of improper use, or a missed shift, will begin a “snowballing†effect as wear on one component compromises others. This is why it is key during an overhaul to carefully assess each component for wear or damage due to past use. If the transmission is relatively high in miles, all synchronizer rings should be replaced as a matter of course, as these are the front line of the entire shifting process. Always pay close attention to the dog teeth as well as the teeth on the operating sleeve.
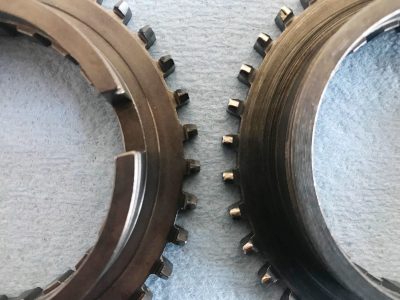
Slight wear or evidence of minor contact to the teeth are okay, but the points of the engagement dog teeth should be distinct and relatively sound. The operational caution here is: if in doubt, replace it.
Porsche does not sell the dog teeth portion of its gears separately. As one can imagine, replacing a gear set, whether through Porsche or one of the several aftermarket suppliers, can be an expensive proposition. Fortunately, there are suppliers who make the dog teeth separately and they can be purchased for a fraction of what a gear set will cost.
The replacement of the dog teeth requires the use of some very special tooling. While this equipment is not cheap, the tools will easily pay for themselves after a very few uses and they add tremendous value to the cost of a rebuild. It is vital to pay attention and follow the tool manufacturer’s procedures for a proper job.
The replacement dog teeth gears are relatively thin and can be easily damaged during installation. It is also a good idea to utilize a high strength locking fluid to assure a reliable repair. This procedure, while not condoned by Porsche, has been done countless times by professional Porsche technicians and proves to be a perfectly reliable fix if performed professionally and conscientiously.
On both the 901 and 915 transaxles there are internal adjustments to the shift rails.
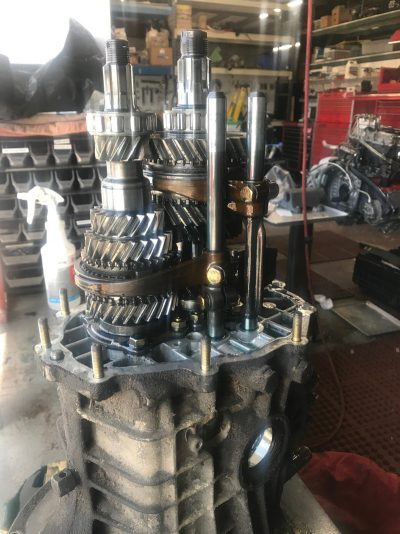
The procedures for this must be followed very carefully as per the factory repair manuals. The shift rails and linkages are adjustable on two planes; fore and aft, as well as their relationship to one another, side to side. Failure to get this part of the repair done properly might necessitate a complete disassembly to access the pinch bolts on the shift rails that facilitate the adjustments. It is a great idea to engage gears while they are exposed prior to installing the housing and observe the movement of the shift rails to assure that they are properly adjusted.
The fluid that lubricates a Porsche transaxle is subjected to two major challenges. It must be highly shear stable to provide protection and wear of the heavy loads of the ring and pinion gears, and it also needs to be light enough to allow the synchronizers to function properly. Modern synthetics are far superior to what came before and there are several products to choose from.
One stickler that requires consideration is the fact that most synthetic oils lubricate a little too well to allow the synchronizers to perform their duties. Lubricant manufacturers have become aware of this and have blended “synthetic†oils that actually allow the synchros to operate by not being too slippery while providing the shear stable characteristics of a heavier 75W-90 hypoid oil that the ring and pinion requires. A popular synthetic oil provider actually has an “NS†designation for “Non-Slippery†transmission oil that addresses this very issue.
The differential service components include ring and pinion gears, pinion carrier bearings and the differential itself. All are addressed as a separate unit even though they share the housing with the transmission. The setup of a ring gear is only necessary when a new ring and pinion or a new differential has been installed. The relationship between ring and pinion gears is critical to the longevity of the components as well as quiet running of the gears.
While there is nothing new about what is measured in a Porsche ring and pinion gear setup, how they are measured is quite unique. Specifically pinion gear depth, one of the most critical dimensions to achieve, requires highly specialized tooling, and there is no way to make the proper adjustments without them.
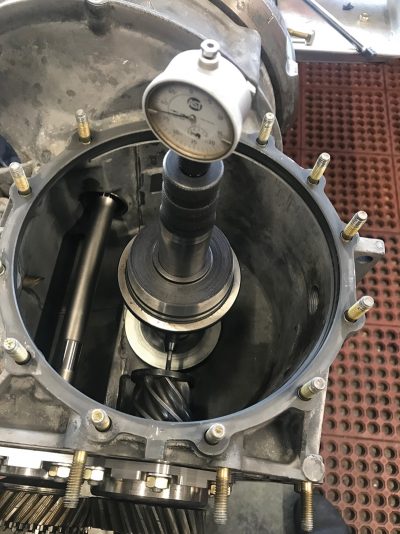
Each ring and pinion set is matched to one another and the pair should never be mixed with a different set. There is an “r†value assigned to every pinion gear after it has been finally machined and matched to its respective ring gear. This “r†value is a small deviation from the depth specification and must be factored into the adjustment.
The method for setting pinion depth is accomplished by putting shims behind the pinion shaft bearing, and this can be measured only with the factory designed equipment. This cannot be “fudged†or estimated or even set up with the original shim selection in the hope that it will work. The tapered roller bearings on each side of the differential housing can often be replaced without upsetting the ring gear adjustment, but checking the differential pre-load, ring gear backlash and gear patterns are all standard operating procedures after replacement and can be accomplished using more generic or even locally fabricated equipment.
In 1987 Porsche solved many of its gear shifting issues by switching to a Borg-Warner cone style synchronizer ring. This device, which is used widely in the industry now, has far fewer parts than its Porsche-engineered counterpart and is extremely effective and reliable. Porsche started using this with the 3.2 liter 911’s and has stayed with it through the 964, 993, and 996 models.
The dog teeth on the cone-style synchronizer are shaped much like those on the Porsche style counterpart. The friction component, however, is on the inside of the synchronizer cone and it is pushed by an operating sleeve directly onto a corresponding cone on the gear that is about to be engaged. As the friction does its magic, the gear about to be engaged is either sped up or slowed in order to match the shaft speed before the dog teeth of the synchronizer locks onto the dog of the gear itself. Wear is much more easily measured on the cone rings, as there is a specification for the distance between the synchronizer ring and the face of the dog teeth on the gear.
The later, water-cooled Porsche models 996 were fitted with the G96 transmission. This too utilized the cone style synchronizers as did the G50 transaxle. The biggest difference internally is the use of larger gears and bearings to handle the additional power to be delivered through the gearbox.
An unusual twist is the use of sealed bearings inside these newer style transmissions. Porsche utilized a sealed bearing internally on the intermediate shaft of the early Boxster engines with disastrous results. The use of sealed bearings seems puzzling but they seems to work reliably on these transmissions. Due in part to its larger gears and shafts, the G96 transmission has components requiring much greater press force to assemble and disassemble the gears and bearings from the shafts. Prior to tackling one of these newer transaxles a smart technician should be certain that a press capable of up to 25 tons of pressure is available for use.
From the onset of the G50 trans to contemporary transmissions, internal adjustments have been removed from the hand of the servicing technicians as now the accuracy of manufacturing has become precise enough that adjustment is no longer necessary. Instead of the shift forks clamping to the shift shaft via a pinch bolt, the forks are now secured in the proper position via a set of roll pins that do not permit any adjustment error.
This, however, does not mean that things can’t go awry. Always check the internal shift rods for straightness and replace any if you find them bent. Pay attention to the position and movement of any detents or gear lockout pins as well, as these can either block a shift rail or allow two gears to be engaged simultaneously if not in their correct positions.
Both the pinion shaft and the mainshaft, also referred to as the input shaft, are supported by three bearings each. There are two roller bearings and one “four-point†bearing, which is essentially just a ball style bearing with the center race split into two components. The roller bearings support the shafts and control lateral play in the shaft and the four point bearings control fore and aft movement of the shaft.
Special attention must be paid to all the bearings during inspection, but the four point bearings require especially close scrutiny. The ring and pinion gears carry a lot of load and forces are constantly trying to push them apart. It is the duty of the four point bearing to control the forces trying to push the pinion shaft away from the ring gear. Likewise, the differential carrier tapered roller bearings control the loads on the ring gear and they are subjected to extreme pressure and consequently higher wear than many of the other bearings in the transaxle assembly.
Inspection of these as well as the roller bearings on the pinion and mainshafts is a bit tricky as there is almost always what appears to be slight degradation of the surface of the bearing races. Some of this degradation occurs very quickly and is normal. Consider the expense and the role each bearing plays and consider how long the vehicle might be in service. A classic Porsche that is driven only a few thousand miles lightly each year might be given very different consideration than one that is driven year round or dedicated to track events only at high performance driver education events.
With each job it is vital to review any technical service bulletins pertinent to the transaxle that is being serviced or overhauled. Porsche is known for updating older components with redesigned parts which often cure a known defect or make the transmission stronger. It would be tantamount to negligence to not take advantage of an upgraded part or a modified procedure.
A discussion with the customer is extremely critical as well. Expectations have to be laid out carefully and the customer needs to understand the idiosyncrasies these Porsche transmissions, especially when it comes to the 901 and 915 models. Best practice is to drive the vehicle with the owner before and after repairs. Take time to notice proper driving habits and diplomatically correct them if you notice the owner inadvertently misusing his or her transmission.
It is absolutely critical for the clutch to be fully disengaged (foot right down to the floorboard) before attempting to move the shift lever. Each time a gear is clashed or a synchronizer is disengaged with power still being applied, components suffer and become compromised.
Inspection of the clutch itself is also imperative, as a dragging clutch, one not fully disengaging, will cause synchronizers to clash or be overworked. Installing a new clutch assembly along with any transmission work is considered standard operating procedure unless the clutch assembly has a service record of having been replaced or looks and measures to new specifications.
Transmission work can seem daunting at first to the uninitiated. Any job undertaken for the first time requires research, care and diligence. With thoughtful self-training, however, this area of repair can be conquered with minimal pain to a conscientious technician. Transmission repair work is an area of service that has become more common as the classic Porsche models age. The rewards for taking on this type of work and developing expertise will eventually pay off in the form of significant revenue enhancements.
Download PDF
0 Comments