I-CAR’s knowledge assessment process rules out any courses you don’t need so you can acquire more repair skills while sitting in fewer classes.
Train to survive and thrive
Training is critical both to survival in this environment of rapidly evolving automotive technology and to the ability to succeed in the face of pressures from competitors and other market forces.
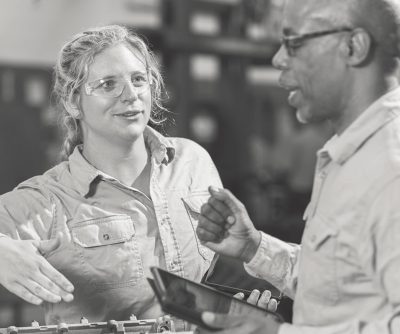
New body materials require repair procedures that often differ from those of traditional steels. Faster, more precise response to driving conditions and engine load require real-time inputs from many more vehicle systems than in the past. New sensor and other information input technologies require post-repair reset or calibration to communicate with control modules. This need may often be due not to damage to the sensor, but because it is part of a circuit that the technician disconnected from power during a repair that, in the past, would have been considered unrelated. And much of this new technology is mounted near the vehicle perimeter, or is networked through wiring connections in areas that are vulnerable to collision impact. As I-CAR® CEO and President John Van Alstyne has said, “If you are not training on new technologies, you are falling behind.â€
Eliminate training redundancies
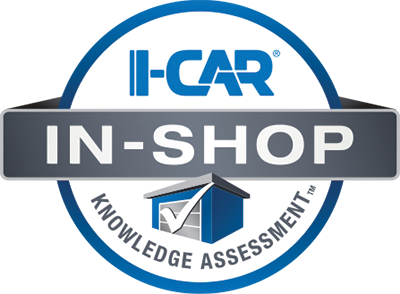
The I-CAR In-Shop Knowledge Assessmentâ„¢ program reduces the time required to learn by using competency testing to determine which classes a technician needs. The testing eliminates class requirements in all technological areas in which the technician demonstrates that he or she already has adequate knowledge.
That knowledge can come from experience, OEM training, or other sources, according to Gary Tench, Body Shop Manager at Jeffrey Automotive Group, a multi-brand new car dealership near Detroit. “For example, we’ve received the Nissan training on distance monitoring and safety sensor technology, and have already purchased related tools and begun repairing those systems. We know enough to pass assessment tests on those skills. We can focus on additional advanced training available from I-CAR.â€
“The Knowledge Assessment program allowed my technicians to test out of some classes that would otherwise have been required for them to achieve I-CAR Gold Class certification,†said Kathleen Walters, Body Shop Manager at Lisle Auto Plaza, a multi-brand suburban Chicago area new car dealership. “It cut our shop’s total training cost almost in half.â€
Test and train in your shop
All assessments and much of the subsequent training is done in your shop, to eliminate travel time and reduce expenses. Most training can be done after hours or scheduled to avoid significant lost technician productivity.
Instructors base assessments on oral interviews. Not using written tests reduces the potential for reading comprehension problems or English as a second language to slow the assessment process. “The In-House Assessment instructor asked questions and my technicians answered verbally, not in writing,†said Walters. “At times they went into the shop for hands-on experiences.â€
The instructor provides an assessment results report to shop management. It identifies knowledge gaps and becomes the basis for developing a training plan for each technician.
Fast track to certification
Body shops can reach or maintain I-CAR Gold Class® status by having technicians that are certified at least I-CAR Platinum™ 1 in four
functional areas: estimating, non-structural collision repair, structural repair, and refinishing.
Using the knowledge assessment process is like switching from sandlot baseball to a professional sports team.
With a completed assessment in hand, shop management and the technician together develop a training schedule. The training plan shows the quickest path for each technician to become Platinum certified. Shops that participate in the I-CAR In-Shop Knowledge Assessment program achieve Gold Class status in about one-quarter of the time, compared to the average non-participating shop.
“We combined the Knowledge Assessment with in-shop classes, all in a three-day period, for fast-track to I-CAR Gold Class certification for our entire shop,†explained Walters. “I-CAR instructors led live, hands-on classes after closing time in our shop.â€
“On-going classes are required to keep your certification up,†said Tench. “I-CAR classes help us maintain our Gold Class status.â€
Gold Class marketing
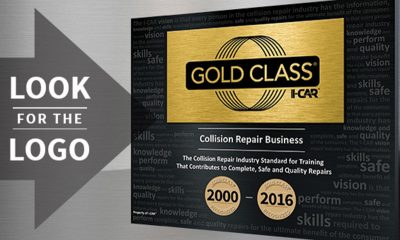
Once the shop is Gold Class certified, I-CAR lists it on GoldClass.com, a site used by vehicle owners when they are in the market for collision repairs. Insurers and OEM network program administrators also visit the website to ensure that shops they are using are current with Gold Class status.
Increase productivity and job stability
The training teaches technicians how to use the proper tools, equipment, and repair information. “Old-school, trial-and-error body work doesn’t cut it with today’s vehicles,†said Walters. “I see my technicians following OEM-recommended repair procedures and getting reduced cycle times, and that is partly the result of I-CAR training.â€
Nissan support
“I am filling out applications right now to a program offered by Infiniti to cover 50 percent of the cost to send a few of my technicians to I-CAR collision repair classes,†said Walters. “We pay, with help from Nissan, for our techs to take I-CAR classes,†agreed Tench.
“Every time we offer training support to our technicians, they are very excited about it,†said Tench. “They see it as the shop investing in their future,†said Walters.
The hottest ticket in town
I-CAR Knowledge Assessment points technicians to opportunities to learn about the latest tools, equipment, and repair procedures. “My techs understand that the grass is not greener on the other side,†said Walters. “They tell me that we’ve got the hottest ticket in town.â€
0 Comments