Oh, the frustration! You’ve got spark, fuel, and compression and the engine still won’t start. Where do you go from here? Let’s take a look at no-start diagnostics when, by all accounts, the engine should be running fine. The laws of physics still apply so let’s think outside the box and solve that mystery no-start.
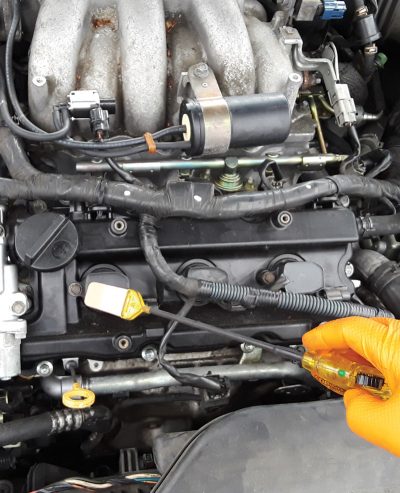
In nearly every no-start diagnostic that rolls into your shop, you’re going to find one of the big three is the cause of your customer’s problem. Fuel for the fire, spark to light the fire and compression so the fire can move the engine. Very rarely, an engine will seem to have all three and still refuse to start. The problem will always have a solution. The questions are, can you find it and can you fix it? As with any diagnostic, a solid understanding of how an engine works and how it is controlled are key to finding the fault. With these kinds of problems, you will have to add a bit of creativity to the mix and think about it from different angles.
The most frustrating situation with no-start diagnostics is when the test you did didn’t give you the correct result. Either you relied on a test that was not as thorough as it needed to be, or the test flat out gave you the wrong result.
Take spark for example. If you test a coil with an induction probe and see the coil fire, it’s usually safe to assume the spark is fine. It’s almost unthinkable, but it is possible that the spark isn’t getting all the way into the cylinder. Just a few possibilities might be: fouled spark plugs, oil in the spark plug tubes, broken spark plug insulators or even incorrect plug gap.
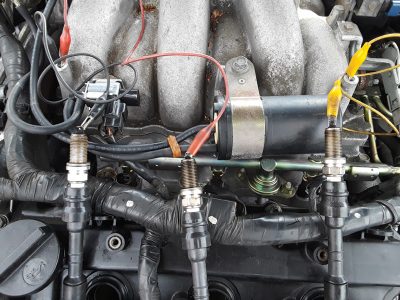
Knowing a history of how the no-start occurred can eliminate some of these possibilities. Consider that all it takes is one less than perfect, do-it-yourselfer to gum up the works. Perhaps someone thought they could save some money by changing their own spark plugs. They installed the new plugs with a standard 5/8†deep socket not knowing that spark plugs have insulators that can break, or perhaps they didn’t understand that the spark plug gap should be more than zero. Seeing the spark at the actual plug can alleviate these concerns. Even with coil on plug distributorless ignition you can test for integrity in the ignition system; it’s just a little trickier.
In the automotive world that just keeps advancing, it is interesting that these 2.4L and 3.3L vehicles with their distributors are still on the road. The primary method for ignition control for Nissan vehicles since the mid-2000s is the coil on plug distributorless ignition. It is so efficient, there don’t seem to be any changes coming anytime soon. All of the issues the distributor presented seem to have departed with it.
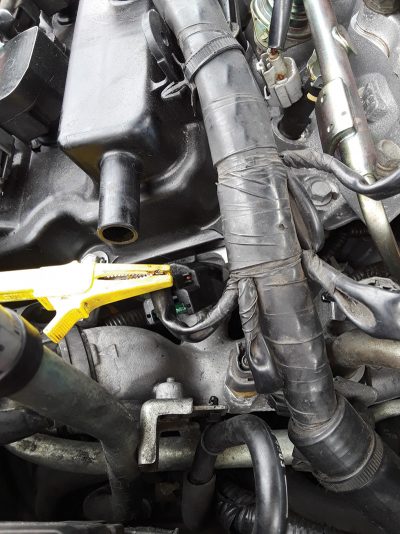
There is one notable exception and that’s the intermittent CMP sensor. It’s so common and can be so hard to pin down that it has been suggested that the first step in diagnosis is to replace the part and move on. This problem doesn’t seem, on the surface, to be related, as a CMP or CKP sensor failure will carry an obvious lack of spark and fuel injector pulse.
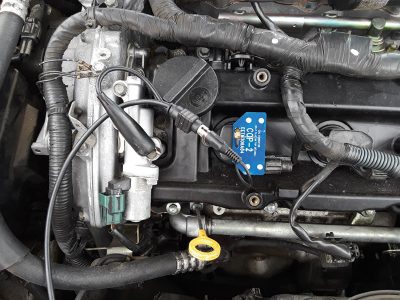
This is merely a cautionary message to be a little extra thorough. Rather than calling a fuel injector pulse good when you first see the noid light illuminate, watch it for a good 5-10 seconds. Any drop-outs in the rhythm of the noid light may indicate intermittent driver failure, intermittent CMP sensor failure, or poor power and ground connectivity to the ECM, all of which can cause a no-start condition. Don’t have a noid light? The same can be tested with an induction probe and lab scope watching the coil being triggered or even using the cowboy spark testing method of having an entire bank of coils with spark plugs connected to ground. The rhythm should be steady as the engine cranks. If it’s not, find out why.
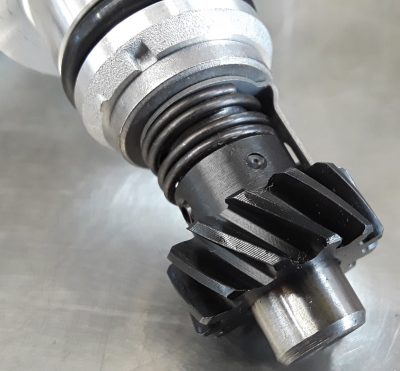
There is an exception to the fuel, fire, compression triangle and that’s in the timing. The internal combustion engine is basically a way to take the energy from an explosion and turn it into movement then repeat the process several hundred to several thousand times per minute. Using an explosion to make movement is easy, but making it repeatable requires precise timing. The pistons must move to exactly the right place and, at the same time, the valves have to open and close at the precise moment they are designed to. This gives you compression. Add in electronically controlled fuel and spark at exactly the right time and we have a functioning engine. Timing that is off a little can cause poor runnability and misfire. Timing that is off a lot will cause a no-start. Timing that changes while the engine is running will cause a no-start that is very difficult to diagnose.
When ignition timing is off enough to cause a no-start it usually gives itself away while the engine is cranking. Backfiring in the exhaust or intake manifolds is often a solid sign your timing is off. If the engine was being worked on prior to the no-start, looking at what repairs might have been related to the ignition system will likely be a short cut to your answer.
Take the 3.3L you might find in an early 2000s Xterra, Frontier or Pathfinder. The distributor is gear driven off the bank 2 (left) camshaft. A very simple mistake in replacing the distributor can lead to an engine that will crank and crank without starting. To confirm the distributor is clocked correctly, turn the engine to top dead center on the compression stroke. Remembering the crankshaft has a TDC position in both the exhaust stroke and the compression stroke, use a compression whistle to make sure you are on the compression stroke.
Install the whistle in place of the number 1 spark plug and turn the engine until it goes through a long whistle. As soon as the whistle stops align your timing mark on the crankshaft to TDC and you’re ready to roll. Remove the cap and double check that the rotor is pointed at the spark plug wire that goes to cylinder number 1 (right bank, first spark plug). Even very experienced technicians have been known to make this simple mistake.
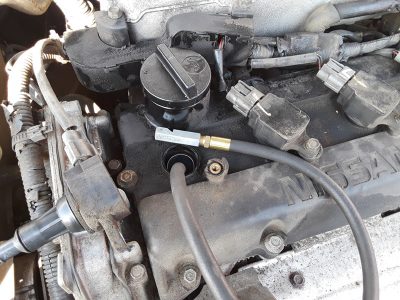
At this point, even if the rest of the cylinders are in the wrong firing order, you should get cylinder 1 to fire. Then simply confirm the firing order is correct (1-2-3-4-5-6 in the case of the 3.3L) and more importantly in the right direction, counter-clockwise. Putting the wires in order but clockwise will cause an interesting and possibly exciting failure to start.
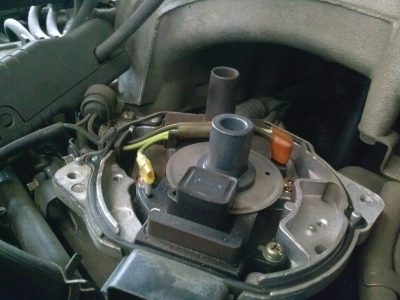
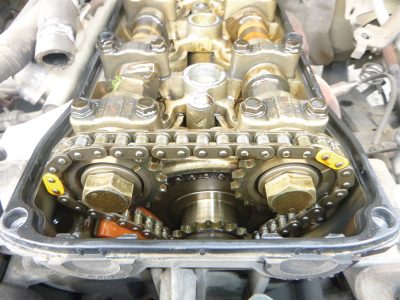
Distributors are quickly becoming a thing of the past. Is it still possible to have a timing-related no-start with distributorless ignition? The answer is not likely. Significant hard parts damage would have to occur that would more likely lead to a no spark condition. CMP and CKP sensors can’t be out of adjustment as there is no adjustment to be out of. Since most Nissan applications use hard parts like the actual camshaft or crankshaft to trigger the sensors any failure in these parts would be more catastrophic than a simple no-start.
Valve timing can cause a no-start condition. With confirmed good compression however, it is unlikely to be the cause. Incorrect valve timing as a cause of a no-start condition is more likely to be noticed by the complete lack of compression as the engine is cranking. Other symptoms might be backfiring out of the exhaust or intake manifolds as valves, being open at the wrong time, allow the fire to escape. If valve timing is suspected, even a little, stop and check. The difference between “far enough out of time to cause a no start†and “far enough to cause valve damage†is very small with our most popular Nissan powerplants being interference engines.
It’s also important to realize that too little gasoline isn’t the only fuel problem that can cause a no-start. Even in a modern fuel injected engine, too much fuel can flood the engine and foul the spark plugs. A failing fuel pressure regulator or leaking injectors allowing too much fuel can effectively short out the spark plugs inside the engine.
There is a provision in the ECM software to help deal with excess fuel in the cylinders. If the throttle is pushed to wide open while cranking, the fuel injectors are shut off, preventing any further fuel from entering the cylinders. So long as fuel isn’t being provided by an alternative method, this should allow the cranking engine to blow the excess fuel out the exhaust and resolve the flooded condition.
Since a single badly leaking injector isn’t likely in the first place, there is almost no possibility of all 8, 6, or even 4 injectors being at fault. Of course, fuel injectors aren’t the only possible failure that can cause extra fuel in the intake manifold. Fuel pressure regulators that are vacuum actuated, as in many pre-2000 Nissan engines, can be a place to investigate. Typically, this will result in a very rich running engine with misfiring and bad, gassy smells. If it’s ignored by the driver long enough it can get to the point that fuel is puddling in the intake manifold and flooding the engine during cranking. This failure has a “tell†in that you will likely smell the excess fuel by just walking up to the vehicle.
Being a professional automotive technician, of course, we know that if you smell raw fuel, cranking the engine isn’t a safe option. When excess fuel is suspected, simply remove the vacuum hose and check for raw fuel. Any liquid in the vacuum hose means a fuel pressure regulator is in your future. Most Nissan engines after about 2000 have a return-less fuel system and the fuel pressure is regulated by the fuel pump in the tank. If the engine is old enough to be carbureted, a leaking needle seat or sunken float will have the same effect.
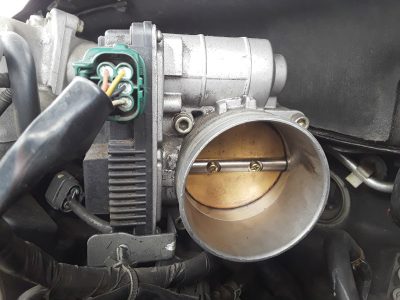
There is another side of the fuel situation that is sometimes taken for granted, and that’s the air side. It doesn’t mater how hot your spark is, without air you have no fire. In older engines with a throttle cable, a stuck or plugged idle air control solenoid could actually be the cause of a no-start condition. Often this failure would present with the firing of a couple of cylinders then a quick stall. Simply raising the throttle off idle slightly would easily identify there was a problem present in the idle circuit.
With Nissan’s adoption of the “fly-by-wire†electronic throttle bodies in the mid-2000s, the throttle control side of the equation has become more involved. Since an electronic motor controls the throttle plate, there is no need for an Idle Air Control solenoid (IAC) as the ECM can simply open the throttle plate directly. Failures in these throttle bodies are rare, but when they do happen a no-start condition can be one of the results.
Most often you will find a stored code as the ECM constantly monitors the throttle body’s performance with redundant throttle position sensors and a functional test when the key is turned on. A failure without codes is still possible in that the throttle position sensors only monitor the actual throttle plate. With enough carbon buildup around the throttle it can act just like a clogged IAC. If this is the case, simply depress the accelerator a little to see if the engine will start. Better still, inspect the throttle plate for signs of trouble.
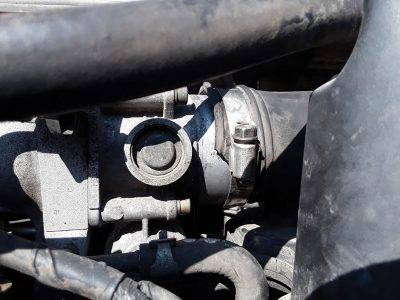
Another consideration in the area of air flow is the ECM thinking the air flow is greater or less than it actually is. Something as simple as a torn intake air tube can prevent the engine from starting and, in some cases, can cause intermittent stalling.
The way it works is the opening in the air tube, after the MAF, allows air in without passing through the MAF, then the ECM sees much less air entering the throttle body. The ECM then drastically modifies the fuel flow preventing starting. After multiple attempts to start the engine the ECM will override the MAF reading and start the engine with default values. If the leak is in such a position that the air flow changes back and forth, the ECM can stay confused, resulting in a no-start condition.
Another situation to consider is the triggering of the NATS immobilizer system. Typically, the no-start will be accompanied by a flashing or steady security light. It’s the light that looks like the outline of a car with a key inside it. Check for codes first. A dead battery in a key fob may be the core of the issue.
There are specific issues that affect all Nissan vehicles equipped with the system from 2005-2008. A TSB has been issued, NTB10-107. What can happen is a no-start situation that appears to be a security immobilization. The actual cause is a failed battery reducing the voltage to the ECM while cranking. The battery may even test good with a non-load type tester. Before getting too deep in any no-start or even engine performance diagnostic, be sure to confirm that your battery is good with a load test and your grounds are solid.
0 Comments