Mercedes-Benz chemical engineers and metallurgists have worked out the fine points of this, and would not be overjoyed to know you’ve been putting something non-specified in your customer’s vehicles.
The dictionary definition of antifreeze is, “Any substance that lowers the freezing point of water, protecting a system from the ill effects of ice formation.†That alone tells us that automotive engineers needed to develop something with the proper characteristics to work in automobile cooling systems beyond plain water. Water, of course, has great cooling and heat transfer properties, but aside from the freezing problem there are other concerns with using strictly water. Here, we’ll take a look at coolant/antifreeze combinations and the history of their development.
Antifreeze in its simplest form
The term “engine coolant†is widely used in the automotive industry, which covers its primary function of convective heat transfer, but doesn’t hint at lowering the freezing point. When used in an automotive context, corrosion inhibitors are added to help protect vehicles’ radiators, water pumps, cylinder heads, and blocks. As mentioned earlier, water is a great heat dissipater and is what the first designers of the internal combustion engines would have used except for two properties that were deal-breakers. One is its freezing point of 32 deg. F./0 deg. C. Water expands with great force when it freezes, and in a closed cooling system something has to give. That’s going to be some critical component such as a cylinder head or block.
The second problem with water is the corrosion factor. Obviously, water and iron are a recipe for rust. Iron swiftly oxidizes. In other words, it rusts in the presence of moisture and oxygen. Later engines use aluminum components combined with iron parts. Initially, aluminum doesn’t react with water, but the properties of that metal rapidly develop a thin layer of aluminum oxide a few microns thick that prevent it from further reacting with water. When this layer begins to corrode, a reaction develops that releases highly-flammable hydrogen gas. Aluminum chloride hydrolyzes in water making a mist when it comes into contact with air because hydrochloric acid drops form during the reaction with water vapor. This is where the corrosion occurs in aluminum.
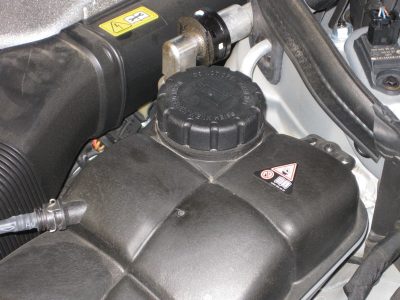
Early engine antifreeze was simply methanol, otherwise known as methyl alcohol. Since radiator caps were vented, as opposed to sealed, the methanol was soon lost to evaporation, requiring frequent replenishment to avoid freezing. Methanol also accelerates the corrosion of the metals, especially aluminum, used in most engine and cooling systems. It’s a weak acid that attacks the oxide coating that normally protects aluminum from corrosion. Ethylene glycol was developed, and replaced methanol as an engine cooling system antifreeze. It has very low volatility compared to methanol and water. Before the 1950s, cooling systems were unpressurized and the engine typically ran cooler than modern versions do. It should be noted that ethylene glycol also has a much higher boiling point than water at 387 deg. F./198 deg. C. By pressurizing the cooling system with a radiator cap, the boiling point of the fluid is increased further, permitting higher engine temperatures and better fuel efficiency. Pressurized systems do not appreciably change the freezing point. Later, propylene glycol was introduced due to its more-benign environmental characteristics, but its use has been limited mainly to the food industries, although it has seen some automotive use.
Dynamite!
Ethylene glycol is a colorless, odorless, viscous dihydroxy alcohol. It has a sweet smell and taste, but is poisonous if ingested. It is often colored a greenish gold or yellow for the automotive industry. Ethylene glycol was first synthesized in 1856 by French chemist Charles-Adolphe Wurtz, but, very little was done with the substance until the 20th century. It was first produced commercially in 1917, but at that time is was used primarily in the manufacture of dynamite.
In addition to being an effective substitute for glycerol as an ingredient of high explosives, ethylene glycol also turned out to have a number of characteristics that made it an ideal antifreeze. In addition to mixing readily with water in any proportion, it has a much lower freezing point than water and its boiling point is nearly twice as high.
Ethylene glycol was first used as an automotive antifreeze in 1926, and it saw widespread use in military applications during World War II. After the war, it became the dominant chemical antifreeze. The molecular formula is (C2H4O) nH2O, where n = number of ethylene oxide units corresponding to a molecular weight of 6000, (about 140). Now you’re thinking, “Why do I need to know this?†Well, you don’t necessarily, but the engineers who develop these compounds do and what you put into the vehicles you service will matter as we will see later in this article.
Generally, the color of an antifreeze has no bearing on its properties — it’s an identifier. Coolants developed for different vehicle applications are dyed different colors.
What’s wrong with the good old green stuff?
Oxidation and corrosion occur inside the cooling system. Corrosion occurs when oxygen and dissolved minerals or salts in the coolant react with metal surfaces. It can also be the result of electrolysis, an electro-chemical reaction between dissimilar metals (such as aluminum and cast iron), or from stray electrical currents that pass though the coolant due to poor grounding between the engine and chassis. It’s possible to do a voltage check of the coolant with the negative lead of your DMM to battery ground, and the positive lead in the coolant. You should see less than 0.1 V. If it’s 0.3 V or higher, and all vehicle grounds are good, replacing the coolant should reduce the voltage to an acceptable level.
In general, corrosion inhibitors keep the coolant slightly alkaline chemically (as opposed to acidic). This keeps corrosion in check as long as there is enough inhibitor present to neutralize the acids. Over time, the coolant becomes acidic. At this point, corrosion begins and bad things start to happen. Compound this with the ever-increasing usage of various and dissimilar metals in the modern automobile engine and it’s a recipe for trouble. “Green†formula coolant contains fast-acting, but relatively short-lived corrosion inhibitors that last about two to three years, or 24,000 to 36,000 miles.
About 93% to 95% of most antifreeze is ethylene glycol, another few percentage points are water or maybe a solvent to keep rust and corrosion inhibitors in solution, and the remainder are those inhibitors. The inhibitors make a huge difference, and they’re what the discussion of what to use is all about.
By the way, at concentrations above 70% antifreeze, the freeze point of the coolant actually starts to rise, so more antifreeze is not better. The 50-50 mixture provides the best combination of freeze and boil-over protection, and good heat transfer from the engine.
Organic acid technology (OAT)
Organic Acid Technology describes the ingredients responsible for the corrosion protection offered by an antifreeze of this type. OATs are long-life chemicals based on minimally-depleting carboxylate technology. Carboxylates provide corrosion protection by chemically interacting at the metallic corrosion sites, rather than by forming a layer of inhibitors that cover the total surface. In other words, instead of painting a layer of protection on the metals the actual chemistry is changed by carboxylates in order to provide the protection needed. This technology provides superior protection to all components of the cooling system including those materials such as the aluminum and magnesium found in modern-day engines. Unlike with traditional antifreeze, the need for regular additions of supplemental coolant additives at scheduled service intervals is no longer required, providing a true long-life product that can represent significant cost savings. In some heavy-duty diesel applications, you may see a reference to a coolant extender, which can be used with an OAT antifreeze to top-up certain additives at the product’s half-life, typically around 300,000 miles (480,000 km). In general, OAT-based corrosion inhibitors are recognized for their non-toxic properties that make them readily biodegradable, addressing any environmental and occupational health and safety issues.
First-generation OATs were specific to automotive applications. This was quickly followed by their use in heavy-duty diesels (as in Asia and Europe), or in North America where OAT was used along with nitrite or nitrite and molybdate to ensure adequate wet-sleeve liner cavitation protection.
Manufacturers have become increasingly aware of the varying needs of different regions where compounds and formulas are concerned. European countries have extremely hard water. As antifreeze and water are a 50/50 mix, water quality drastically impacts the overall mix (see sidebar). European manufacturers began to move away from phosphate-based technology because of its tendency to form scale. On the other side of the world, Japanese manufacturers began to move away from silicates due to issues with silicate gel drop-out.
Hybrid Organic Acid Technology (HOAT)
Silicated Hybrid Organic Acid Technology (HOAT) antifreezes, which are sometimes referred to as “G-05,†contain organic acids in combination with one or more inorganic inhibitors. As the name suggests, it is a hybrid of the traditional green inorganic coolant properties and OAT properties. The most common inhibitor is silicate. The addition of silicates increases corrosion protection for aluminum engines, radiators, and heater cores, and helps protect the water pump against erosion wear. Generally, silica additions improve the corrosion resistance due to the formation of protective oxide films, which act as a barrier to oxygen diffusion to the metal surface.
If you look at the chart of the makeup of the Mercedes-Benz spec 325.0, you’ll see the addition of Silica (Si) and Boron (B). Boron has traditionally been used in HOAT and OAT as it acts as an excellent corrosion inhibitor and helps to extend fluid life by slowing down the development of bacteria and helping the fluid to be more inherently stable.
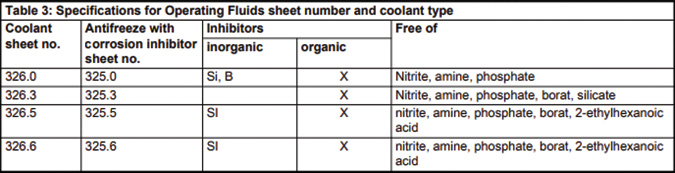
What about Universal Antifreeze?
Universal formula antifreezes are marketed as being suitable for all passenger cars and light trucks, regardless of year, make, or model, or of the type of coolant that’s already in the cooling system. Some of these claims have been challenged in court on the basis that no single additive package can match the conflicting requirements of the different OEMs. Even so, the makers of universal coolant say their products can be used in any vehicle, whether it matches the original coolant chemistry or not. The universal coolants use OAT-based corrosion inhibitors with proprietary organic acids to provide broad spectrum protection. The coolant may be dyed yellow or amber (yellow-orange).
The service life of most universal formula products is typically five years or 150,000 miles, with one exception. When used to top off a cooling system in an older vehicle that contains standard green antifreeze, the service life of the product is reduced to that of the original type, which is two to three years, or 24,000 to 36,000 miles.
The main advantages of a universal coolant is that it simplifies the selection process to a single product, and it eliminates the need to carry the many different types of coolant (green, orange, yellow hybrid, blue, pink, red, and even purple) to cover the market. Those who are opposed to universal coolants say one product simply cannot match the conflicting requirements of all vehicle manufacturers, and that it is safer to offer specific types that meet these specifications. Consequently, many parts stores carry not only the many different types of antifreeze (often in multiple brands), but also a universal coolant for customers who prefer that kind of product.
Clearly, the Mercedes-Benz specification of 325.0 is the right choice for those of you servicing that company’s vehicles. First of all, it’s a long-life antifreeze and therefore doesn’t need changing as often. If you consider price, the cost of the genuine article is only slightly higher than cheaper alternatives and really is a no-brainer in terms of the overall cost of maintaining a vehicle.
Testing
Keeping accurate maintenance records will go a long way towards knowing the time and frequency of service for the cooling system. Testing the coolant mixture is pretty straightforward. You can use the old floating-balls type of hydrometer, which will give you the ethylene glycol count, but not much else. Then there’s the refractometer, on which you place a drop of coolant, then look through to determine the refractive index of the mixture. The simplest thing, which is quite accurate, is the quick and easy test strip. Simply dip the strip, compare the results with the color chart on the bottle, and you’ll have a test result showing you freeze point, and nitrite and PH levels. You can also staple it to the repair order to show the customer.
What about mixing coolants?
Here again we can enter into lots of debate. Can you mix different types of coolants? A quick search of the Internet will give a thousand different answers to this question, some ranging from no problems whatsoever to the cooling system clogging and causing the engine to overheat and blow up. Since the actual chemical makeup of the antifreezes on the market is about 93% to 95% ethylene glycol and the rest solvents and additives, and since they are mixed 50% with water, we doubt the reports that it will do serious harm short-term if someone has added the wrong product either accidentally or just without due diligence. It’s the additives that will react with each other and possibly cause some long-term -issues.
One brand of antifreeze, let’s say “orange,†has two additives. One is called sebacate, the other 2-EHA (which stands for 2-ethylhexanoic acid). The inhibitor 2-EHA works well in hard water and is more effective than sebacate at lower pH levels (when the coolant moves from the alkaline end toward the acid side), particularly for cast iron. When there’s a low coolant level in the coolant passages, the exposed cast iron rusts. Apparently, that rust is washed away later by flowing coolant, and is deposited in the heat exchangers (radiator and heater cores). It eventually produces the rust powder problems that have been so widely observed and is even the basis of some lawsuits.
That said, if you are working on a Mercedes-Benz automobile, don’t do it! Why take the chance? Trust the engineers and metallurgists on this one and use the real stuff. If you find that perhaps the owner or someone else has mixed coolants in your customer’s car, simply change it out. Explain to your customers that taking the utmost care of their vehicles and making them last is your top priority and you need to flush out the system and begin with a fresh batch of the latest-specification antifreeze. It should be noted that the older Mercedes-Benz antifreeze was a goldish yellow in color. The new antifreeze is blue. As long as they both meet the specification of the 325.0, they are okay to use together, but the resulting color might be ugly. We would suggest changing the antifreeze altogether so that you and the customer both know what’s in the automobile.
Download PDF 〉
0 Comments