They call it “go-juice†for a reason. Until we perfect the electric car you just can’t go without it. The diagnostics of fuel delivery systems have changed over the years and have become a lot more involved, but don’t let that scare you. Let’s take a look at the most common systems and how to fix them when things go wrong.
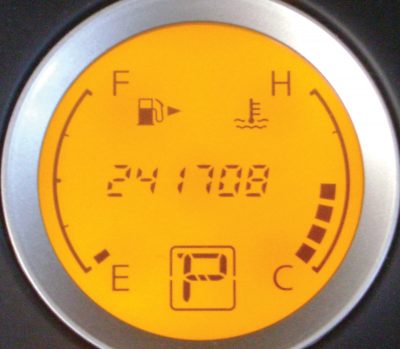
As the technology of the internal combustion engine increases, so does the need to get a reliable supply of fuel to the powerplant. This is the story of increasing pressures. Back in the days of the carburetor-equipped Datsun, all that was needed to supply the fuel was about 4 psi. Basically, all the fuel pump had to do was get the fuel from the fuel tank to a tiny little fuel tank on the side of the carburetor known as a float bowl.
With the introduction of throttle body fuel injection in the late 1970s, and even the early 1980s for Nissan pickups, we saw pressures rise to 35 psi so that an electronically controlled fuel injector on the throttle body could quickly deliver a charge of fuel on demand. These systems were used well into the 1990s, but were eventually phased out in favor of the multi-port fuel injection system. With a separate injector for each cylinder, the charge of fuel had to be delivered even faster, so the fuel pressure was increased once again to about 50 psi.
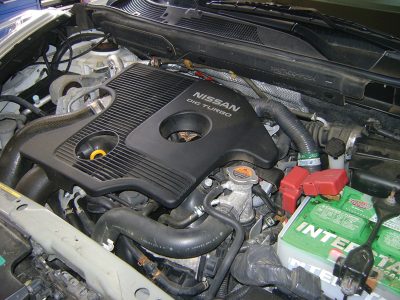
The next stage is the most dramatic jump in pressure yet. With pressures in excess of 2,000 psi, Direct Injected Gasoline, or DIG for short, is Nissan’s contribution to the race for better engine efficiency. Just as the name suggests, this system injects fuel directly into the cylinder while the engine is building compression. The reason for the high pressure is that the fuel has to squirt into the cylinder against compression pressure in an extremely fast manner to get the fuel in there before the spark plug fires.
With advanced computer-controlled fuel injectors and an engine-mounted high pressure pump, the injector can fire multiple times per stroke to cool the piston before compression, then inject more fuel just as it fires. It sounds like a real fancy way of doing what fuel injection has been doing all along, but the end result is a dramatic increase in the amount of energy that can be extracted from the same amount of fuel.
As fuel delivery systems advanced, so did the components needed to make them work. About the only thing that stayed the same is that they all have fuel tanks, but even then we’ve switched from metal to plastic. Carbureted engines typically use a fuel pump mounted to the engine, driven by an eccentric attached to the camshaft. A fuel filter will usually be in-line between the fuel tank and the pump and is a great place to start looking if fuel starvation is expected.
With the introduction of fuel injection, the fuel pump was moved into the gas tank and is operated with electricity controlled by relays and, ultimately, the ECM. A fuel filter is mounted between the tank and the fuel rail or throttle body to keep any particles out of the injectors.
Another important addition is the fuel pressure regulator. In older systems the fuel pressure regulator is mounted on the end of the fuel rail and has the return line to the fuel tank connected to it. It’s controlled by a vacuum hose connected to manifold vacuum. As engine load is increased, manifold vacuum decreases and the pressure regulator, in turn, increases the fuel rail pressure, providing more fuel for the increased load.
On a returnless system the fuel pressure regulator is part of the fuel pump module and maintains pressure from the pump to the fuel rail. This change does more than simplify the fuel delivery system; it also decreases the extra heat introduced to the fuel tank by cycling fuel through the engine on a continual basis. Less heat in the tank means less fuel vapors to deal with. The DIG system uses fuel delivery similar to other fuel injected vehicles until the fuel gets to the engine. At the engine there is a mechanically driven high-pressure pump to deliver the extra pressure needed to overcome the engine’s compression.
There is a point that is often overlooked when working on gasoline powered vehicles. Gasoline is extraordinarily dangerous. Just like you wouldn’t risk working on an air bag without following the proper safety procedures, you shouldn’t work on the fuel system without taking precautions. On any service that involves opening the pressurized fuel system, Nissan recommends releasing the fuel pressure prior to performing the repairs. Check the service manual for the particulars on the system you’re working on.
Typically fuel pressure is released by removing the fuel pump relay or fuse and running the engine until it stalls. Then continue to crank the engine a couple of times to ensure that all remaining pressure is purged from the fuel lines. When opening connections, use a rag to catch any gas that spills. Any fuel that misses the rag and ends up on the engine should be cleaned up before attempting a startup.
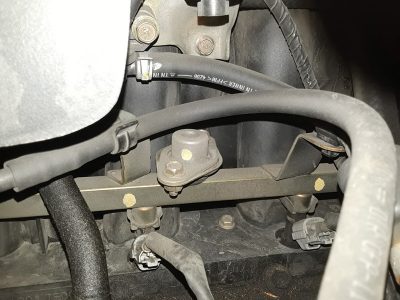
Since these fuel systems run at such high pressures, some leaks in the system can actually spray fuel. Although it’s not that common, and though most leaks tend to be seeping or slow dripping leaks, a spraying fuel leak is one of the most dangerous conditions you can have in the automotive industry. Any time you can smell fuel from the outside of the vehicle it is critical that you identify where the smell is coming from first just in case it is a dangerous leak.
Most often leaks will be small drips or seeping from the o-rings in the connections, rail mounted fuel pressure regulators, or fuel rail dampers. These should most certainly be resolved as a priority and, as a policy, vehicles with known fuel leaks should not be driven.
Many Nissan vehicles use a fuel pressure damper on the fuel rail as a means of stabilizing the fuel pressure. It works much the same way as the anti-hammer devices in your home plumbing system work. Some have suggested removing them as a preventive measure to prevent their eventual failure, and leakage. Don’t do it. They help smooth the fuel pressure to the injectors, and removing them can cause everything from misfires to even some reports of fuel injector failures due the extra hammering stress.
On another safety note, fuel system leaks in the direct injected gasoline fuel system pose a much more serious danger for the technician servicing them. If a fuel leak is suspected, keep your hands away from the engine. The intense fuel pressure can not only cut you, it can literally inject fuel into and under your skin.
Recognizing a leak, besides the obvious smell of gasoline, might present as an extended cranking time when starting, or a slightly rough idle immediately on start-up. Fuel leaks are rare as Nissan designs this system to be safe, but ultimately your safety isn’t an odds game. When in doubt, take the time to be sure.
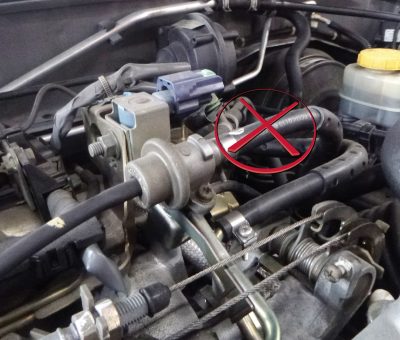
Identifying a fuel delivery problem usually isn’t all that tough. Leaks are smelly and a lack of fuel means the engine isn’t running. Some of the more subtle issues might be something like an extended cranking time on cold soak start-up, or a loss of power under full throttle operation. A fuel pressure gauge will give you a solid start in which direction to look. When connecting a fuel pressure gauge look for the service port, a threaded connection that looks like a tire valve stem, and use that whenever possible.
Unfortunately, many Nissan vehicles don’t have these easy connections. They will, however, have easily accessible hose connections. Keep in mind that a lot of Nissan systems in particular will have similar pressure and return hoses. Connecting to a return line will definitely lead you down the wrong path diagnostically speaking.
Take the example of a turn of the century Altima 2.4L. The fuel pressure regulator is right on top and easy to get to. That would be the return line to the fuel tank and connecting your gauge there won’t help. Just below it is the pressure line. There are two easy ways to be sure you’ve got the right line. First, remember that if the pressure regulator is on the fuel rail it’s on the return side. Second, spring type hose clamps are not used for high pressure fuel lines. If the connection is secured with an external hose clamp it will be held with a screw and make contact all the way around the hose.
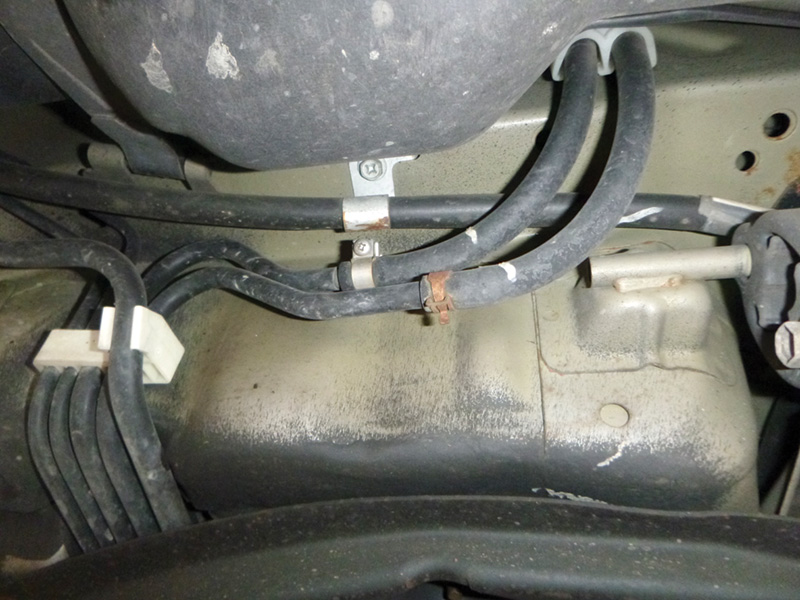
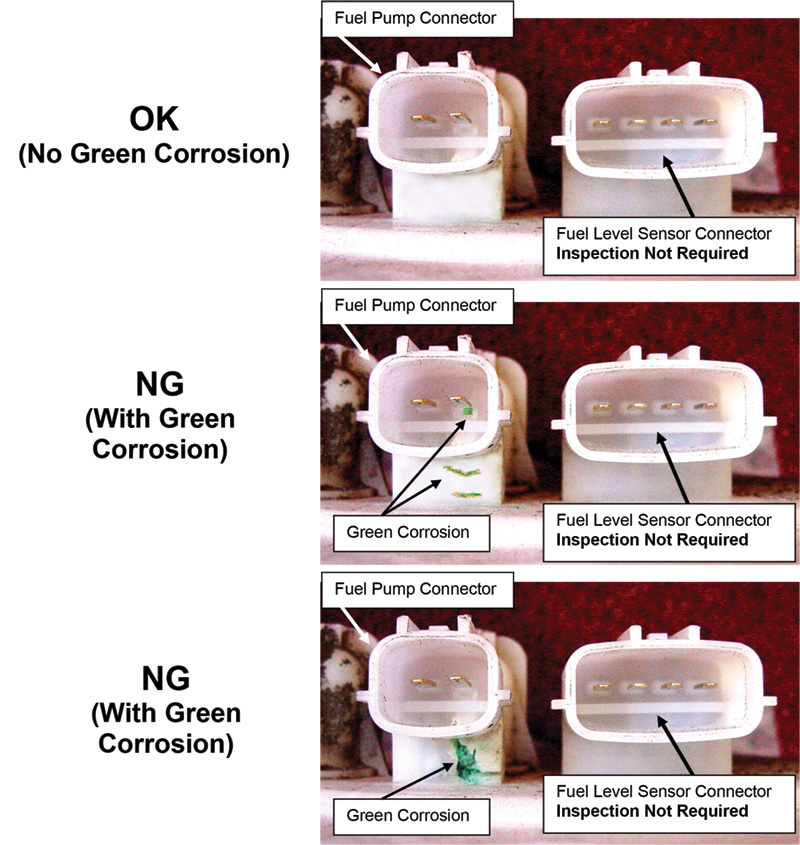
Whenever you have a fuel pressure gauge connected, Nissan recommends checking the connections for leaks every 3 minutes when the engine or fuel pump are running. A good rule of thumb is to be diligent enough about fuel spills that you don’t smell any fuel during your diagnostics. This may not be completely possible, but keep in mind, the stronger fuel you smell the more used to the smell you get, and thus the greater chance of missing a leak. It also doesn’t hurt to mention to a co-worker if you smell fuel walking past their bay. You never know, they may not be aware of it.
Fuel pressure can give your diagnosis a direction in many ways. An intermittent or “jumpy†pressure reading might indicate an empty fuel tank. As the tank runs dry, the fuel pump sucks air, causing the fuel pressure to change erratically. Just add a gallon of gas to confirm your hypothesis. Remember, the fuel gauge is not a bulletproof system. It doesn’t have to be correct. Just because it’s pointing at a quarter tank doesn’t mean it can’t be out of fuel. Poor grounds and corroded connections can alter the gauge readings. A gallon added to the tank takes a lot less time than pulling the tank down to verify.
When fuel pressure is simply absent, verify you have fuel pump operation. Can you hear the fuel pump come on when the key is turned to the On position? If not, verify power to the pump module. If you have power and ground to the pump and it’s not coming on, you know the fuel pump module is coming out for inspection. One of the nice things about Nissan vehicles is that their fuel pumps very rarely fail. You will, however, find that certain models in certain climates can develop corrosion in the connections in the module, especially in climates that use salt on the roads.
Fuel pressure will often be at the center of an extended cranking situation on cold startup. Before the engine is started, the fuel pump will be activated for a few seconds to make sure the fuel pressure is at its peak when the engine cranks. This little bit of run time isn’t enough to completely fill the fuel lines, it’s only there to make the pressure right. If the fuel is allowed to bleed back out of the system overnight, that 3 second burst isn’t enough to make the engine fire up in a timely manner.
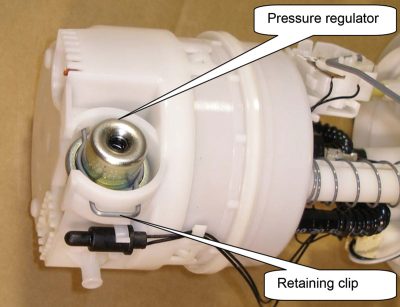
The 2007 to 2009 Nissan Versa has a known issue with the original fuel pressure regulator in the tank (since this is a returnless system). TSB NTB07-094a gives a great description of how to test for and repair the issue. The test is simple enough. If the pressure drops lower than 29 psi after 30 minutes of engine shut down, the fuel pressure regulator has failed and is leaking down too much. There is a replacement available that isn’t prone to the same failure. In other vehicles a little more diagnosis may be needed to confirm the regulator as the failure. Other possible causes might include a failed check valve in the fuel pump (in a return type system), an external fuel leak, or even a leaking fuel injector.
Unfortunately, many failures in the fuel delivery system will be in failures on the control side. From fuses to relays and even ECM issues, the electronic side of the fuel system can present a daunting diagnostic challenge.
Use the divide and conquer method by testing for power and ground at the fuel pump module first. With many Nissan cars and SUVs there is relatively easy access to the fuel pump module from the top under the back seat, or even in the trunk area thanks to cleverly installed inspection covers.
Checking for power supply at the fuel pump is relatively easy. Some exceptions to this are in the Frontiers and Titans. There are no access holes in the truck beds to get to the fuel pump. Typically, there are other connectors on these vehicles you can test at that don’t require removing the tank. On the late 2000s Titan, for example, there is a connector in the chassis harness behind the right front mud flap on the frame. Simply check out the wiring diagram to confirm the wire colors for the fuel pump, back probe the connection and verify that the pump is getting power. This does leave one glaring possible failure point, and that’s the wire harness between the connector on the frame and the connector at the tank. Simply test again when the fuel tank is down if a fuel pump problem is indicated.
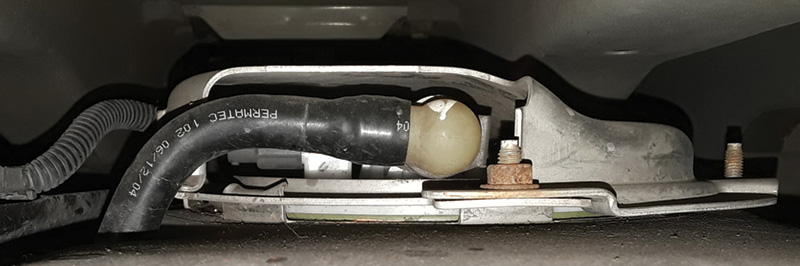
Aside from the normal, mundane corroded connectors, small leaks, and failed regulators, take into consideration that basic maintenance and human error do get forgotten and do cause problems. Is the fuel in the tank actually fuel? Has the fuel filter been changed, ever? Does this model even have a fuel filter?
With the increase in technology, external fuel filters are becoming a thing of the past. Unfortunately, that leads many technicians to forget that some cars have them and they do get plugged. Also, people putting bad gas and fluids classified as “other†into their fuel tanks is still happening. Water, diesel fuel, and various other fluids will still pour down the filler neck, so don’t forget to check a fuel sample.
0 Comments