How and why Mercedes-Benz brake lining recipes have evolved, and why you should install only the genuine article
The invention of the wheel, what an amazing discovery and revelation that must have been in its day! A way to power and leverage larger objects and move them in an easier fashion. Now that you’ve got things rolling, the question arises: How do we stop this thing? That’s where friction comes in.
If we’re to understand the chemistry and engineering behind Mercedes’ latest friction materials then we need a short course on exactly what friction is and how it comes into play in the modern automobile. We see friction in action constantly when we examine how the automobile functions. Friction is used when the tire grips the road to accelerate and when the brake pads squeeze the rotors to slow things down.
Friction is defined as the resistance that one surface or object encounters when moving over another. For the purposes of this article we will be looking at two types of friction:
Static friction is a force between two surfaces that prevents those surfaces from sliding or slipping across each other. This friction allows a car to accelerate forward — the rubber compound in the tire can grip the road and push backward, which causes the ground to push forward on the tire. If there were no static friction between an automobile’s tire and the ground, you would be unable to propel the car forward when accelerating and would simply end up spinning the wheels.
Kinetic friction is the force when two materials slide across each other. It always opposes any sliding or slipping motion and tries to reduce the speed at which the surfaces slide across each other. For example, a baseball player sliding into third base plate uses kinetic friction to slow down. If there were no kinetic friction, the baseball player would just continue sliding right past the base.
Both types of friction come into play in the braking of the modern automobile. Static friction will come into play when your customer parks their car on a hill. The force of the parking brake shoes (or pads, depending on the system) squeezing against the parking drum will keep it from sliding down the hill. Kinetic friction comes into play when your customer applies the brakes to slow down. The force of the brake pads against the rotors will oppose the sliding motion and begin to reduce the speed at which those two items slide against each other.
The higher a brake pad’s coefficient of friction (expressed by the Greek letter mu (µ), pronounced myoo) the more aggressive the pad and the greater its stopping potential (the same amount of pedal force provides more stopping power). In theory, µ ranges from 0 (full lubricity, no friction at all) to 1.0 (solid, no slippage possible). Fifteen to 20 years ago, most production brake pads were lucky to see the high 0.20s. Today, OEM pads are well into the 0.30s, top-tier performance street pads in the 0.40 to 0.45 range, and some race cars in the high 0.60s.
A pad’s friction is not constant, varying due to changes in temperature, humidity, moisture, wear, age, and many other factors. Brake pad designers strive to develop highly stable pad compounds that maintain friction consistency over a wide range of operating conditions. But as compounds become more exotic, they also become more expensive. And more aggressive (higher µ) compounds tend to increase rotor wear. Mercedes-Benz engineers strive to find just the right balance in these factoring equations.
When the brakes are actuated, the kinetic energy of the vehicle is converted into heat. The temperature of the brake discs can then rise to as much as about 700 degrees Celsius (1,300 degrees F), more than hot enough to glow. High-quality materials and workmanship on Mercedes-Benz genuine brake discs ensure that they can handle the temperature extremes while maintaining structural and dimensional stability so that the vehicle quickly comes to a standstill when needed, helping ensure a short stopping distance.
Friction Coefficient | Code |
Up to 0.15 µ | C |
Over 0.15 µ up to 0.25 µ | D |
Over 0.25 µ up to 0.35 µ | E |
Over 0.35 µ up to 0.45 µ | F |
Over 0.45 µ up to 0.55 µ | G |
Over 0.55 µ | H |
Unclassified | Z |
The frictional performance of brake pads intended for typical street usage is classified under SAE Standard J866, expressed as a two-letter code: The first letter designates the low-temperature (0 to 200 degrees F) friction performance, and the second letter the high-temperature (200 to 600 degrees F) performance. The letters generally appear on the backing plate as a prefix or suffix to the part number. If the first letter is lower than the second, the pad works better at high temperatures and needs a warm-up; if the second letter is lower than the first, the pad may fade at high temperatures. The best street pads have good friction at both high and low temperatures (ideally, both letters would be the same, as in FF). Most pads will have this designation code printed on the back or edge, but not always: Some manufacturers may choose to use proprietary numbering or coding systems on their pads.
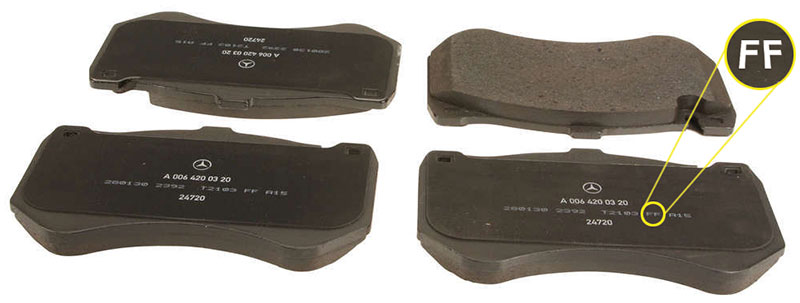
Early friction materials
The earliest automotive brake friction materials were credited to Bertha Benz, business partner and wife of automobile inventor Karl Benz. She is also known as the first person to take an automobile long distance, thus promoting the automobile as the modern alternative to the horse and carriage. In the course of her journey the wooden brakes failed and Mrs. Benz visited a cobbler to install a leather covering, making the world’s first lined brake shoe. Since that time engineers have spent years and countless hours developing the proper friction materials to provide the ultimate braking performance. In 1961 the 220 SE model was the first Mercedes-Benz to be fitted with four wheel disc brakes, ahead of the 300 SL which had to wait a few additional weeks to have discs fitted.
Modern brake pads are constructed of various materials, chosen for their characteristics. The materials used, and the relative amount of these ingredients in the friction material, as well as the fabrication methodology, strongly affect the braking efficiency, wear resistance, and propensity of a brake pad towards brake-induced noise, vibration, and harshness (NVH).
Vehicles have different braking requirements, depending on the way the vehicle is expected to be used. Different friction materials offer application-specific formulas and designs. Brake pads with a higher coefficient of friction provide good braking with a lower brake pedal pressure requirement, but tend to lose efficiency at higher temperatures and suffer from faster wear. Brake pads with a smaller and more constant coefficient of friction might not lose efficiency or stability at higher temperatures, but generally require higher brake pedal force.
Brake pads were originally made with asbestos because its properties allowed it to deal with both the heat and drag that braking exerts on the pads. However, as the serious health-related hazards of asbestos became apparent, other materials had to be found.
Beyond Asbestos
Today, brake pad materials are classified into one of four principal categories, as follows:
Non-metallic or organic materials — these are made from a combination of various synthetic substances bonded into a composite, principally in the form of cellulose, aramid, Polyacrylonitrile (PAN), and sintered glass. They are gentle on rotors, but produce a fair amount of dust, thus having a short service life.
Semi-metallic materials — synthetics mixed with varying proportions of flaked metals. These are harder than non-metallic pads, more fade-resistant and longer-lasting, but at the cost of increased wear to the rotors which then must be replaced sooner. They also require more actuating force than non-metallic pads in order to generate braking torque.
Fully metallic materials — these pads are used only in racing vehicles, and are composed of sintered steel without any synthetic or organic additives. They are very long-lasting, but require more force to slow a vehicle while wearing the rotors faster. They also tend to be very loud.
Ceramic materials — Composed of clay and porcelain bonded with copper flakes and filaments, these are a good compromise between the durability of the metal pads, and the grip and fade-resistance of the synthetic variety. Their principal drawback, however, is that unlike the previous three types (and despite the presence of the copper, which has a high thermal conductivity) ceramic pads generally do not dissipate heat well. Phenol formaldehyde resin is frequently used as a binding agent. Graphite can serve as a friction material as well as binding agent. Ceramic brake pads are exceptionally quiet, because the ceramic materials cause the braking sound frequencies to be elevated beyond that of human hearing.
Of primary concern of course is the noise factor. Probably the number one complaint after brake service is noise. Consider the ringing sound when rubbing a finger around the rim of a wine glass: The harmonic vibrations that result are similar to the noise that can be generated by the brake pads contacting the rotors. The installation of aftermarket brake pads, instead of the genuine Mercedes-Benz offerings, will have your customers complaining about noise and wondering about the quality of the work.
There are environmental factors that govern the selection of brake pad materials. For example, the bill SSB 6557 adopted in Washington state in 2010, along with a similar bill in California, limits the amount of copper that is allowed to be used in friction materials. This will be eventually phased out to only trace amounts, due to the negative impact of high copper levels on aquatic life. As the brake pad manufacturers see this trend continue they have decided to make the reduction for all brake pads sold in the future.
What about the rotors?
Brake rotors are made of several materials.
- Cast Iron
The oldest material when it comes to a brake rotor. It’s one or two pieces and gets the job done. It used to be the most common material for brake rotors. However, it’s also the heaviest option, which affects unsprung weight, the overall weight of the car and its handling. - Steel
Steel has been the racer’s choice for years, because a steel brake rotor is thinner (thus weighing less than cast iron) while still handling heat better. The downside: Steel rotors aren’t as durable as some others, and warped rotors can cause noise and a pulsating pedal when braking. - Layered Steel
Layering sheets of steel together and laminating them makes them resistant to the warping you might find in a straight steel brake rotor. It’s a favorite of racers who don’t want frequent brake rotor replacement and repair, but manufacturers are currently targeting only professional racers. Production is limited, so it’s not terribly common in passenger vehicle applications. - Aluminum
Aluminum brake rotors dissipate heat quickly, but they also melt at a lower temperature than other options. Aluminum is a favorite for motorcycles, which weigh far less than a car or truck. Although aluminum doesn’t have the wear-resistance of ferrous metals, the lighter motorcycle doesn’t tax the brake rotors as much as a heavier car, truck or SUV. - High Carbon
These are iron, but with a lot of carbon mixed in. They can take a lot of heat and dissipate it quickly. The metallic content helps the rotor avoid cracking under high stress, and brake noise and vibration are reduced as well. - Ceramic
They offer the highest heat capacity (85 percent higher than cast iron) and superior dissipation, and they maintain a more consistent force and pressure as the temperature of the rotors rises. Ceramic is the highest-performance brake rotor available today, but it is also the most expensive.
On several Mercedes-Benz models, such as the GT (190), C-Class (205), S-Class (222), CLS (217) and GLC (253), you’ll find a composite rotor, which is a two piece design consisting of the brake rotor surface and a steel casing ‘hat’ where the rotor mounts to the hub. These rotors have built in corrosion protection. The steel casing is galvanized with a zinc-nickel coating and the disc is also painted with zinc dust paint. These composite rotors need to be handled with far greater care than the traditional rotors, as we explained in our article in our article Hang Pads, in the September 2018 issue of StarTuned.
- Never carry them by the hat or central hole, only by the outside rim.
- Always leave them in their packaging box until just before installation.
- Never allow them to be treated roughly, or set down on the hat.
- Protect the anti-corrosion coating of the hat, avoid impacts or scrapes.
- Avoid shocks or impacts to the brake disk.
- Never use the brake disk to turn the wheels against the steering resistance.
Improper handling can damage these disks and make them unusable.
The optimum braking result can only be achieved with brake discs precisely tailored to the brake pad. It is this philosophy that has also made Mercedes-Benz engineers into experts, in terms of the right “friction partner†for their brake pads. The genuine Mercedes-Benz brake disc range is manufactured in strict engineering tolerances and meets the ECE R90 requirements for quality and performance. Would you expect anything less?
Genuine Mercedes-Benz brake pads are perfectly designed and engineered for genuine Mercedes-Benz brake discs. The optimum friction pairing helps ensure high braking power, short stopping distances, reduced wear and tear, and prevents brake noises from occurring. This is how Mercedes-Benz genuine brake linings contribute to accident-free driving. If customer satisfaction is your goal, installing the original friction materials the vehicle came with will result in happy customers and no comebacks.
Download PDF
0 Comments