Make sure you have a clear overall picture of what’s actually happening using function diagrams and flow charts, then zero-in with a process of elimination and XENTRY.
Putting stress-free and controller area network diagnosis in one sentence may seem to some as a bit of an oxymoron but honestly, the answers are there. The challenge is to master a process for running through a diagnostic routine and developing a surefire technique for troubleshooting. Developed in 1983 by Robert Bosch and installed in 1991, the first production vehicle to feature a CAN-based multiplex wiring system was the Mercedes-Benz W140. Since that time hundreds of articles have been devoted to CAN bus diagnostics and development, including many good StarTuned articles. We will try not to repeat too much redundant information and focus on some of the latest strategies and especially using the newest version of XENTRY Diagnostics Kit 3.
A Multiple CAN Network
Keep in mind Mercedes-Benz also uses several different bus speeds on their vehicles. Depending on the application, there may be a high-speed 500 Kbps CAN-C bus for the powertrain, transmission and ABS modules, and a slower-speed 83 Kbps CAN-B bus for the body control functions. On some Mercedes-Benz cars, there may be as many as 30 modules on the CAN-B bus. Up to model year 2002, all communication between the CAN-C and CAN-B bus went through the electronic ignition switch (EIS) module. After 2002, a new “gateway†module handles the inter-bus communications as well as onboard diagnostics via a CAN-D bus. Now you may find CAN-G, CAN-H as well as MOST (Media Oriented Systems Transport). MOST is a high-speed multimedia network technology optimized by the automotive industry. It can be used for applications inside or outside the car. The serial MOST bus uses a daisy-chain topology or ring topology and synchronous data communication to transport audio, video, voice and data signals via optical fiber. More on that later. In addition to these you may have a LIN bus and a K line. LIN (Local Interconnect Network) is a serial network protocol used for communication between components in vehicles. The need for a low-cost serial network arose as the technologies and the facilities implemented in the car grew, while the CAN bus was too expensive to implement for every component in the car. The K-line is a single-wire connection and thus a serial interface, which is directed via a data strand and has a ground connection. Accordingly, in practice the K-line has two physical conductor connections being used. Power supply and control of transmission and reception are the main tasks of these technical components.
Steps to CAN diagnosis
The independent service provider is usually working on vehicles that may have more age and mileage on them that what the dealer may see. Many of the factory repairs have been done while the car was under warranty. Belonging to a network that has a database of vehicles similar to the ones in which you are working on in which to compare can be very helpful at times. That said, too many technicians fail to develop good diagnostic strategies and rely on the network for their diagnostic work. Here is a good strategy to implement in CAN diagnostics:
- Verify the customer’s concern and develop a general direction to follow.
- Do some research. You may find you need to purchase a subscription to startekinfo.com to get workshop information. Check TSBs. Understand the problem, the components and the systems possibly involved in the complaint .
- Form a theory of the cause through testing and then test to see if you are correct.
- Perform the required repairs and verify the customer concern has been taken care of.
If the vehicle is roadworthy a test drive and verification of the complaint may be the first order of business. After you have verified the customer concern the first step is to connect your scanner (XENTRY) and perform a quick test. Although a good aftermarket scan tool may be able to perform this test, I’ll be honest here, you won’t get very far in your diagnosis after that. Beyond reading codes and data, you won’t be able to see if version coding is up to date or correct. See previous article in StarTuned “Why you need XENTRYâ€.
Be sure to connect a battery maintainer on the vehicle and plug in the scan tool to an 110V outlet. XENTRY Diagnostics Kit 3 will have different menus when you open diagnosis depending upon which year vehicle you are working on. Newer vehicles will have the six button cells on the left after you have selected the proper vehicle. Usually 2008 models and newer will have auto detect and will communicate with the vehicle to select the proper VIN and variant. Although sometimes you will be asked to choose some variants. The six cells are:
- The home screen which has notes, the quick test cell, and the current quick test cell. It should be noted that there is an option to choose a customer complaint but XENTRY will only allow it after a quick test.Â
- The next cell looks like a doctor’s stethoscope with a notepad and choosing it will list all the components fitted to the vehicle.Â
- The cell with the car with an exclamation mark is the customer complaint screen. Again XENTRY will ask you to perform a quick test first.Â
- The bullet point tab will give you the control unit view.
- The next tab is very handy. It looks like a diagnosis tree and it’s a tree of all the CAN networks on the model you are working on. This will be very helpful for communications problems when trying to find which components are off line or shorted.Â
- The last tab on the left of the main menu screen is a picture of manuals with a wrench. This window opens up a special functions tab which may have various items in it such as but not limited to:Â Stored control unit logs, Entry for retrofits and modifications, and System information.
Start your initial quick test, the XENTRY will drop down to the next cell and give an option to start the test. The XENTRY and some aftermarket enhanced scan tools automatically poll or ping the modules or perform a “health check†to confirm that all modules are online. If your scan tool indicates “no communication†with a specific module, then you must diagnose the reason for the non-communication.
The full module scan or quick test is important because it will show a good general picture of what modules are on line, any communication faults. A printout of this test is good to have on hand for verification purposes. Sometimes at this point a good look under the hood or even an under the vehicle inspection may turn up some items you will notice may have been damaged or tampered with, thereby causing your symptoms.
Each module after the initial quick test will have either a green check mark, an F for fail or an I for “more information†available. Many times at this stage you may often have multiple codes in several modules. Remember to go back to your original strategy, “What is my customers concern and what are the most likely places to find fault that relates to that complaint.†Many codes may be stored from previous events and are completely unrelated. This is why it’s good to have a printed report for the customer. Although the stored codes may not have relevancy to the vehicle concern, it’s prudent to advise them that there may be other possible problems with the vehicle that they may want to direct their attention to. Now that you have selected the control units and codes that relate to the problem you are trying to solve, you can open each one up individually. A further menu will open that has each individual fault in the control unit itemized. A further drop down menu for each one will give you supplemental information regarding the occurrence of the event. This is your “freeze frame†data and it can be quite extensive and give you much information that will help in your diagnosis. You will also be informed as to whether it is a current fault or intermittent.
At this point you have the option of clearing the codes and rechecking for hard faults or proceeding on with tests of the failed components. Unless you are certain you have a hard fault I would advise against erasing the fault memory. In doing so if the fault does not occur again right away, you won’t have the availability of the tests tab on the XENTRY to zero in on the most probable causes. If you click on each of the faults individually you will find a “tests†tab located at the bottom screen. One or more tests will pop up in the field in which XENTRY will instruct you to perform certain tasks and report on the outcome in a YES/NO format. These tests may involve checking voltages at various pins and using a lab scope to record a wave form on a crank position sensor, to using bi directional controls to see if the actual data on the scan tool show whether or not the component you are activating is working or not. Continue on with each command, the menu will sometimes give you the exact cause, sometimes the most probable or possible cause and other time the problem may not repeat.
Dependent upon the flow chart you will be able to pull up WIS/ASRA, TIPS, wiring diagrams, connector assignments etc. in another menu window. Again, having a clear overall understanding of the complaint coupled with TSBs and history of similar vehicles will help you to formulate and accurate diagnosis.
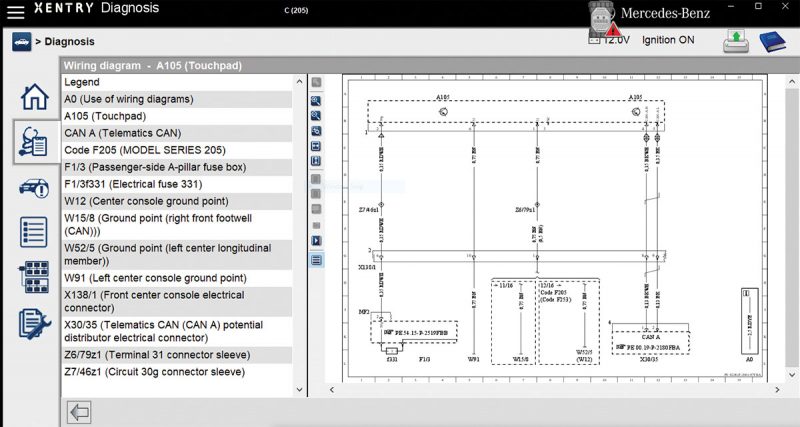
General Notes
Some general guidelines to follow in CAN diagnostics are common sense but worth a reminder. Your XENTRY unit will also remind you of these items:
- Use only a cable with a fuse to bridge connections.
- Each time after replacing a component, always carry out a component test.
- This will assure you that the component is functioning properly, connections are good and coding of the component is correct.
- When processing a fault code, the instructions to follow may generate a test step which will be interrogated by a YES/NO cell. Please note that this test sequence may generate other fault codes
- which must be ignored. This is why it’s important to print out or have a list of your original fault codes so that you understand which codes you generated in your testing.
- Only generate a counter fault by short circuiting or open if this is expressly requested in the diagnosis tree.
XENTRY Measurement Technology HMS 990
Optional with the purchase of the XENTRY is the HMS 990. This devise coupled with the XENTRY Diagnostics Kit 3 give the technician extensive measuring options. Service technicians can carry out a wide range of measurements on the vehicle‘s electrical system. Various voltages, ignition and dwell angles – all the essential values can be checked. The equipment can even be used to check all the alternator values. The multimeter provides the opportunity to accurately check the basic electrical parameters such as voltage, current, resistance, frequency, temperature, and pressure.
HMS 990 USB Measurement Technology also makes it possible to check the duration of combustion by analyzing individual cylinders. Compression and rotational speed are also always in check. The service technician is immediately notified of deviations from the specified values.
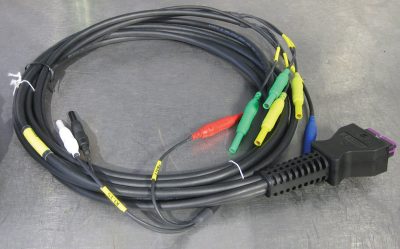
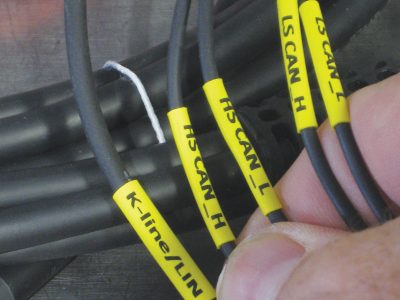
Also incorporated is the use of a universal oscilloscope and the 12-channel oscilloscope to measure various signals such as those from the crankshaft position sensor or the camshaft Hall sensor. Recordings over the long term are also possible. You can also store the measurements taken with the recorder function and retrieve them at a later point.
As you work through your fault diagnosis the test sequence as we mentioned earlier may ask you to use a lab scope to say, graph a crank or cam sensor signal. You can do this perfectly well with your lab scope and check voltage signals with a high quality multimeter. The HMS 990 just incorporates these tools and makes the job more convenient.
Other Specialty Tools
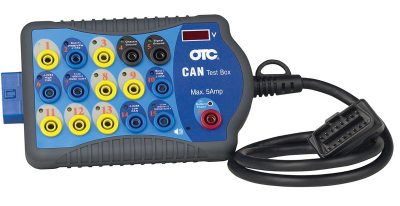
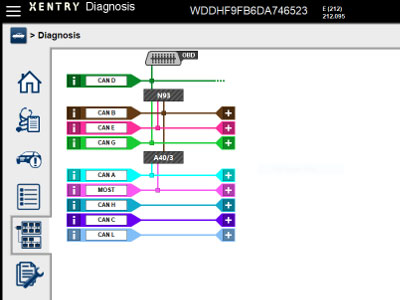
One item worth having is a DLC connector breakout box. When diagnosing a CAN communications problem, you can use this device at times to diagnose which items are off line. If your fault codes indicates a bus problem that is connected to the DLC you can do a resistance test at that point. There are two 120 ohm termination resistors connected in parallel so the resistance should be 60 ohms. If the resistance is incorrect you will need to start isolating which node on the bus may be the problem. Here is where the CAN bus tree diagram comes in handy. A lab scope comes in handy here as well. By viewing the data packets being transferred between controllers you can look for clean lines without noise or interference which might indicate a problem with one of the controllers. Voltages are important too, if you see your voltage drop to zero, that’s going to indicate a ground issue in the line or one of the modules on the line. Conversely if you see voltage up to 5 volts or even 12 volts then the indication would be that you are shorted to power and you can start tracing things from there.
MOST
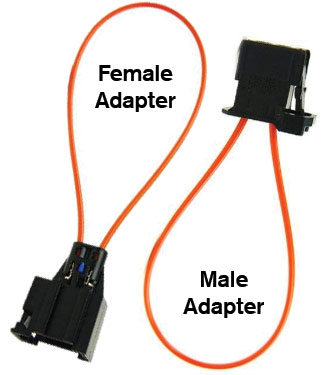
We mentioned the use of the MOST technology in CAN diagnostics. In diagnosing a MOST equipped vehicle the test sequence may have you remove the device from the loop. In order to do this since it is an optical network, measuring terminating voltages isn’t relevant. A very handy tool is a MOST loop tool. You simply unplug the suspect controller, plug in the loop which essentially by-passes the unit and if your communication is restored you’ve found the culprit. A must have tool to have if you get these vehicles in your shop.
See, no sweat! Have a clear cut strategy in place, understand the vehicle and its components that you are servicing. Work through a methodical approach using the steps and information that XENTRY supplies you with and you are well on your way to solving problems.
Download PDF
0 Comments