Don’t rush to replace that transmission, check for service bulletins and updates first! We present some cases where problems were solved with control unit updates or replacements.
Shifting and slipping concerns can be a serious challenge, even for the most advanced drivability technicians. So many factors affect how the modern transmission shifts that it is somewhat daunting to figure out how to solve your customer’s concern. You can, however, begin to narrow down the possibilities with the proper scan tool and procedures. The majority of faults lie in the mechanical or electrical areas: Here we will be only concerned with the electrical issues you may encounter with a shifting or slipping concern.
Sometimes you will be faced with problems from both areas, particularly in high mileage cars, so it is important to be diligent with diagnostic procedures. Nothing is more frustrating than to repair an electrical concern, only to find that the clutch packs are worn out. We should also point out from the onset that without XENTRY Diagnostics or at least a J2534 v05.00 API tool (preferably with a 4 CAN channel) and a subscription to Mercedes-Benz STAR TekInfo (included with the XENTRY machine) you will be very limited in the way of diagnosis, and certainly unable to perform any programing or SCN coding.
Be sure to always follow the proper initial steps when deciding to code or replace a module. Checking the fluid levels, including the proper fluid and its quality, as well as inspection of the driveline, external leaks, and a thorough test drive are always standard procedure. You have to be able to duplicate the complaint to have a chance of knowing when it is fixed
As the title implies, many transmission complaints can be corrected in software, but of course some also need some hardware. Let’s take a look at some examples where a module update has solved a customer’s complaint.
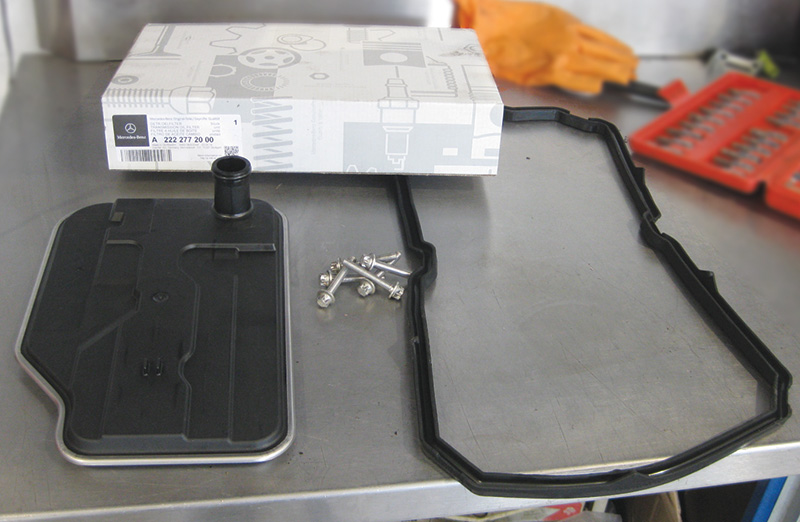
The 722.9 transmission
One of the most popular transmissions in the Mercedes-Benz line, this is also the one that many times you will find a module update (or possibly a replacement) will solve many drivability concerns.
An electronically-controlled unit with 7 forward and 2 reverse gears, all controlling elements are within the transmission case, so there are only 5 wires leading to the rest of the car. Shift quality, service life, maintenance costs and reliability are optimized by the use of electronic controls operating hydraulic elements.
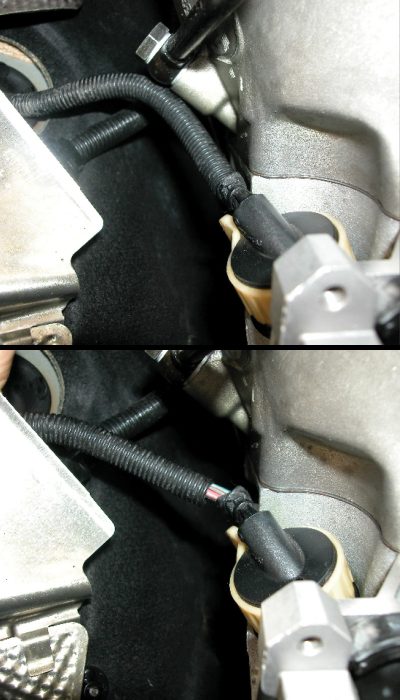
The famous plug connection at the transmission housing where it enters above the pan is a spot that can routinely cause some issues. Obviously a module update isn’t going to fix a mechanical issue with the contacts, but if you have CAN communication errors with the VGS, check the plug. It is not unusual to find it moist from fluid seepage (this was more common on the older 722.6 models) and a thorough inspection of the pins may reveal the source of your communication error. Also important, check the other ends of the harness: Fluid can wick all the way up the harness and wind up in places you’d never expect.
The 722.9 can be broken down into four major assemblies:
- Torque converter with torsional damper and torque converter lockup clutch.
- Oil pump for generating the necessary oil pressure and for reliable lubrication of the actuators and bearing points.
- Transmission housing with mechanical transmission components including the planetary gear sets, park pawl, multidisc clutches and multidisc brakes.
- The electrohydraulic control unit, located in the oil pan.
Data from the control unit is exchanged with the following control units via the engine CAN-C:
- Instrument cluster
- Intelligent servo module (the shifter on the side of the transmission housing)
- CDI or ME-SFI control unit (diesel/gasoline engine controller)
- ESP control unit
- EIS control unit
- Steering column module
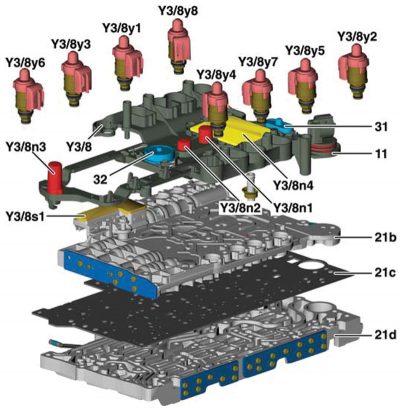
With all these connections and systems involved, proper software coding is critical to proper function. The TCM has self-diagnostics, with several sensors and actuators monitored along with shift performance. Gear selection and shift adaptation are handled electronically, but hydraulic oil is used to move transmission elements as needed. This system allows very precise adaptation of system pressures to vehicle operating conditions, resulting in near-perfect shift quality. This precise control offers the advantage of a flexible adaptation to various vehicle model and engine combinations.
The basic shift program sequence starts with upshift and downshift characteristics for all 7 gears based on an empty vehicle, at operating temperature on a level road, and at sea level. Then the shift program is adapted by offsetting those characteristics depending on the vehicle load, change in driving resistance and accelerator pedal movement and position. Some other influences include vehicle speed, selector lever position (including the mode switch), signals from the engine CAN and the measured characteristics of the shift valves and clutch packs. Fine-tuning of the program can include preventing undesired downshifts in the upper vehicle speed range with a slow accelerator release or the prevention of upshifting to the next gear up with a rapid accelerator release.
Now that you’re familiar with the transmission, let’s look at a few case studies.
2005 CLK500
Vehicle won’t shift and has a check engine light on. After performing a quick test the technician found DTC P2112 stored in the Engine Control Module. He tested the throttle body and APP sensor at idle and in the shop with KOEO and found both to be within specifications.
This false setting of throttle body and APP sensor codes can occur with transmission issues. What can happen is that if you are applying the throttle and the car isn’t moving, the ECM may set some codes for those components. The TCM also stored codes 0778 and 0798, which are for the brake solenoids in the valve body, indicating that an internal check has failed.
After clearing the codes and a test drive, 0778 and 0798 returned, and the scan tool indicated the transmission would not come out of second gear. At this point, an internal test of the brake solenoids is called for. The technician pulled the pan and tested the brake solenoids and found them out of spec. See the image from the workshop manual for the remedial action to take if a brake solenoid has failed.
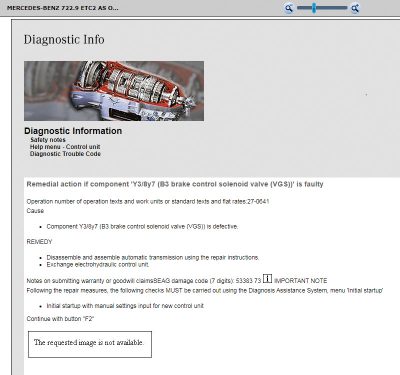
If you suspect the circuit board is faulty, be aware that there are no tests that can check its integrity. Even though the solenoids are available separately, Mercedes-Benz recommends replacement of the entire valve body plus TCM, which includes all sensors, valves and the control unit, as an assembly During production, the characteristics of each solenoid are measured and stored in the TCM’s permanent memory, so individual solenoid replacement is less than optimal.
To properly replace the TCM, you need an online connection to the Mercedes-Benz ‘flash’ servers. The process also includes transferring calibration data if you decide to keep the old valve body, so be sure to use the same XENTRY Diagnostic machine that was used to extract the data from the old TCM, or you’ll end up with a really unhappy transmission that needs a full adaptation sequence. When pricing the control unit separately, the price of the complete unit was more cost effective the just the control unit, so the technician wisely opted for the replacement unit. Remember that 722.9 transmission control units are Theft-Relevant Parts, so you’ll need some owner and personal documentation to get one.
Before starting work, the area around the valve body separation point on the transmission must be thoroughly cleaned, we call it surgically clean: Even the slightest dirt particles introduced into the hydraulic components can lead to malfunctions or even a total failure of the transmission.
After installing the replacement valve body and control unit, along with a new filter and fluid (remember: those aluminum bolts are stretch bolts and must always be replaced), the technician used his XENTRY Diagnostics machine to perform an initial startup, flash in the latest TCM software, reset the adaptations, and perform SCN coding. In this particular case, the diagnostic menu indicated an update of the engine control unit as well. After all repairs were completed, a thorough test drive (including the adaptation routines) was performed, the fluid level verified and the shifting concern was completely eliminated.
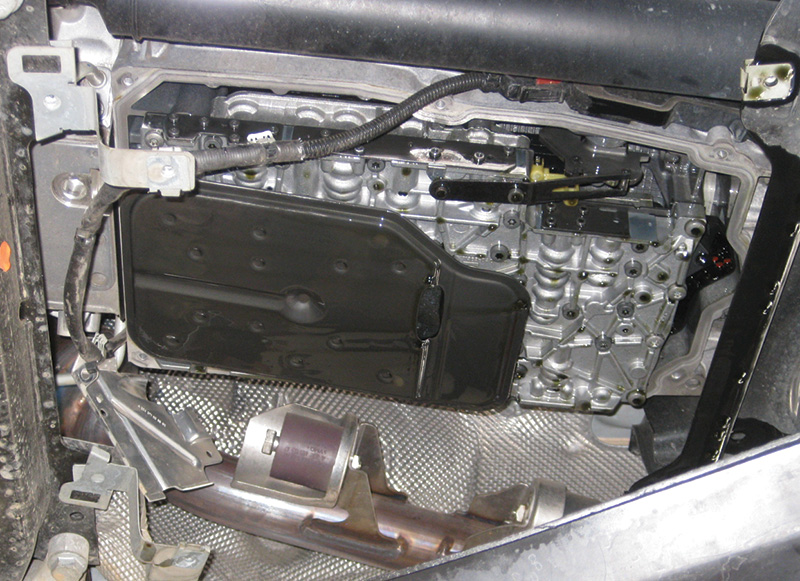
2006 C280
Customer concern: check engine light is on with erratic shifting, sometimes going into limp mode. Customer can shut the vehicle off and restart after a brief wait, and shifting will be normal for a short period of time.
After performing a test drive to verify the concern, a thorough inspection was completed including a fluid check and history of maintenance. Scan tool diagnosis revealed DTCs 2767 and 2768 (Y3/8n2 (Internal speed sensor (VGS)) is faulty). XENTRY Tips article LI27.50-P-049710 was found to have specific instructions pertaining to this and several other codes. The technician followed the guided test steps in XENTRY and, in this particular case, was directed to replace the electrohydraulic controller unit. It should be noted that in some cases there is a repair kit available when directed to do so, which is detailed in document AR27.19-P0220B.
It is so important to install all solenoid valves back to their original positions if they are removed. If you don’t, the calibration data stored in the TCM will be incorrect, resulting in shifting complaints. The control unit was replaced with the proper module update and programing resulting in the transmission shifting properly again.
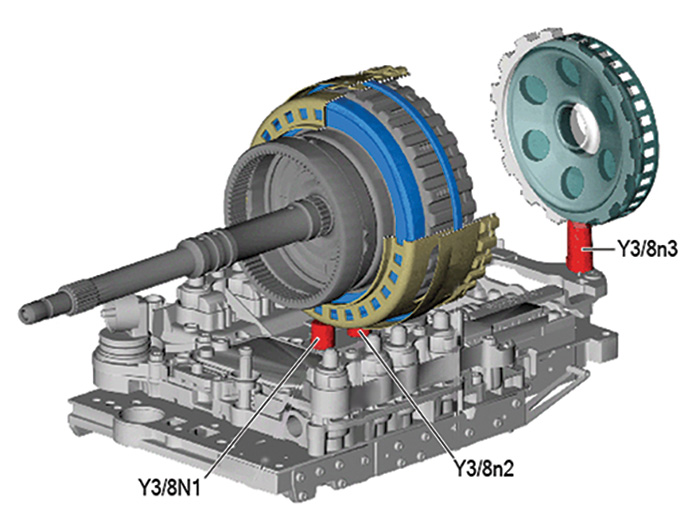
2008 C300 4MATIC
Customer complaint: After a cold start, slight slippage is felt in the 2-3 shift when the vehicle drives off for the first time. This problem can occur if a full pressurization of the K1 piston does not occur when cold.
After the technician verified both the complaint and all the basics (including fluid fill, condition and type) a quick check of STAR TekInfo showed an available service bulletin: According to bulletin LI27.00-P-048552, which was found to apply to the specific engine and controller installed, new software was available to solve this complaint. The new software was flashed into the TCM which solved the issue. Even though the shop had to keep the car overnight (to be sure it was cold), the actual repair took just a few minutes.
2011 ML350 4MATIC 3.5L
The customer described the concern as a shudder, misfire or hesitation on acceleration. After a thorough inspection the technician verified the proper fluid and amount. The technician did note that the fluid was due to be changed from a maintenance standpoint. A quick test revealed no problems with the engine or associated tune-up parts. In particular it’s wise to look at the misfire data if possible just to rule out other possibilities.
No related codes were found, but the technician did find a bulletin related to this issue: LI27.20-P-055758. This bulletin provides a step by step troubleshooting tree to address this complaint. A road test was performed to verify the issue is with the torque converter. The technician was able to deactivate the torque converter solenoid and found the shudder had disappeared. The bulletin states that sometimes, on certain models, the torque converter will have increased wear on the torque converter bearing bushing, or in other models there may be slight internal leakage at the sealing ring between the transmission input shaft and the torque converter lockup clutch.
There was new software version available for this complaint, so the technician updated it and erased the fault codes in the VGS, along with a reset of the lifecycle data of the torque converter (Follow the XENTRY menu: VGS – Fully integrated transmission control (Y3/8n4) > Teach-in processes > Reset of adaptation values > Torque converter > Confirm torque converter replacement > Confirm reset of adaptation data). The transmission fluid was flushed and a new filter was installed. After a test drive the technician noted that the customer concern was no longer present.
Although in this case the original torque converter remained installed, the bulletin advises that it is possible the torque converter must be replaced, especially if the software update was not effective. According to WIS, the torque converter mount on the crankshaft must be thoroughly cleaned, polished with fine grit emery cloth and lubricated with multipurpose high heat paste before installation.
Still have fault codes?
If after programming Engine and/or Transmission Control Units, you still have Fault Code 061B Stored in the TCU, there is also a bulletin that deals with this. The cause may be a torque interface issue between the engine and transmission control modules. To resolve it, check for and install the latest software for the engine control module using XENTRY and perform SCN coding of the engine control module as well. Perform a quick test and erase all fault codes.
The bulletin offers two notes: If the fault code 061B reappears, it can be ignored. This is not cause for any parts replacement. And, if no newer software is available for the engine control module, simply perform the SCN coding of the engine control module.
More bulletins
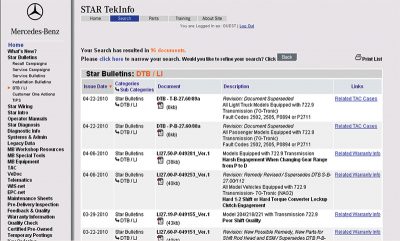
On 164, 211, and 251 models, if you receive customer reports of a brief sensation of delayed acceleration (hesitation) when accelerating back up from low speeds with only light pressure on the accelerator pedal, which does not occur when the accelerator pedal is depressed into the “kick down†range or when the vehicle is moving at higher speeds, this may be caused by the transmission shifting down with a slight delay and the engine only delivering the required power after the delayed shift is completed. To remedy, flash and SCN code the transmission with the latest software.
Although the focus of this article was on the 722.9 transmission introduced in 2004, the same basic principles apply to any electronic transmission. Without XENTRY Diagnostics, which includes access to the Mercedes-Benz flash servers, your ability to address customer complaints may be limited. But even if you have to farm out the actual flashing (which takes only minutes) to someone else, finding the cause is the most important part. In models that are a few years old, don’t think you’re the first one to see this complaint: By now you are probably getting the idea: Check for bulletins! There is a library of information contained in STAR TekInfo (including bulletins, XENTRY Tips and the Workshop Information System) that deal with almost every situation you might encounter in your diagnosis of transmission concerns.
Download PDF
0 Comments