Editor’s note: This is the third and final article about the Mercedes-Benz collision repair certification program. All content in this article was developed through conversations with three Certified Collision Program instructors, and we thank them: Kevin King, Technical Collision Instructor & Welding Inspector and Clint Allen, Collision and Technical Trainer, both teaching at the Mercedes-Benz Learning & Performance Center in Grapevine, Texas; and Bob Laurino, Collision and Technical Trainer at the Learning & Performance Center in Robbinsville, New Jersey.
Previously in StarTuned, we discussed the three tiers of Certified Collision Centers, as well as the significant benefits to the independent collision center of becoming a Mercedes-Benz Certified Collision Center. While certification does require effort and commitment on behalf of the shop, the benefits of certification are considerable, particularly in terms of profitability and cycle times. The training required to realize these benefits is delivered by experienced instructors at Mercedes-Benz USA’s modern state-of-the-art facilities near Dallas, TX and Trenton, NJ, as well as through MBUSA’s extensive online training offerings.
In this issue of StarTuned, we’ll discuss this training, some of the things you and your technicians can expect, and what makes it so effective.
Training effectiveness
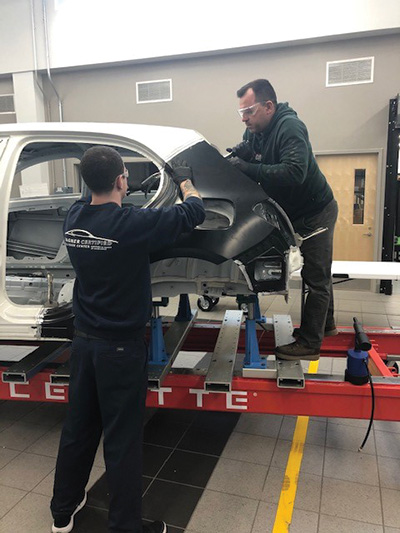
Clint Allen, Collision and Technical Trainer at the Mercedes-Benz Learning & Performance Center (LPC) in Grapevine, Texas was a collision technician for over a decade, and still enjoys working with his hands. “I can read it in a book or watch a presentation, but when I get my hands on it is when I really learn,†he said. “It really sinks in when you’re in the shop and can see how this bumper comes off. Theory and hands-on learning complement each other.â€
Mercedes-Benz USA has been delivering collision training for decades, and they know from experience and talking with participants just what works best. When students disassemble and install a non-structural part, Mercedes-Benz instructors spend time discussing the implications for the advanced driver assistance systems (ADAS) on that vehicle, for example. “Students get to see all of the sensors and other ADAS technologies that live in that bumper, door, fender, or other component,†said Kevin King, Technical Collision Instructor & Welding Inspector at the LPC in Grapevine, Texas. “They learn what needs calibration or other digital configuration procedures performed in order to restore key vehicle systems to full, safe operating parameters.â€
New body repair technicians have historically learned on the job from a guy who may have been doing that work the same way for many years. Much of ADAS technology, vehicle metallurgy, and structural reinforcement design did not exist fifteen years ago. The technologies and design elements that were on vehicles as little as ten years ago have evolved so much that a five-year-old or younger Mercedes-Benz now requires completely different diagnostic and repair procedures.
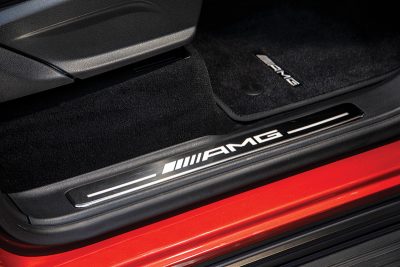
“If you’re repairing collision damage the same way your mentor did ten years ago, you’re doing it wrong,†said Allen. “Still using methods from five years ago? You’re also probably doing it wrong. Collision repair has evolved so rapidly in recent years that if you’re not up-to-date, you’re risking repair safety.†The required biannual facility recertification and six-month cycle of instructor-led training (ILT) for technicians is the Mercedes-Benz way of helping body shops keep up.
Joining Techniques
The joining techniques course covers riveting, adhesive bonding, and welding (not including aluminum welding, which is taught in the separate Elite certification track). Students do hands-on work with Mercedes-Benz adhesive kits, all of the approved spot welders, and various rivet guns, including the XPress 800 Riveting System and the PNP 90 XT2 Universal Riveting System.
Structural Repairs
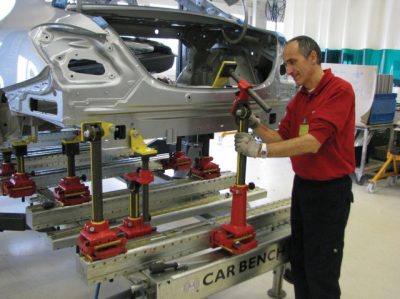
In Structural Damage training the number of students is limited to six per class. The instructor pairs technicians in groups of two and assigns each group a different project. For example, he may task one group to replace a frame rail extension, the second to remove and install an A-Pillar, and the third group to repair another structural component.
The instructor checks the student’s choice of repair documents, including component removal, repair preparation, installation steps, and parts list. “We review the documents they find, make sure they’ve correctly identified every necessary resource, and then have them start the repairs,†said Bob Laurino, Collision and Technical Trainer at the LPC in Robbinsville, New Jersey. “Because classes are small, the students get a lot of attention,†he notes.
Instructors watch over their progress while the technicians work. “We point out things like when a rail is too far off the specified measuring point and must be replaced, not straightened,†said Allen. “We give examples of hidden damage and walk them through the procedure to remove and replace the affected section or component. We point out components that contain or are connected to devices that must be calibrated or initialized after that component is removed and replaced or reinstalled.â€
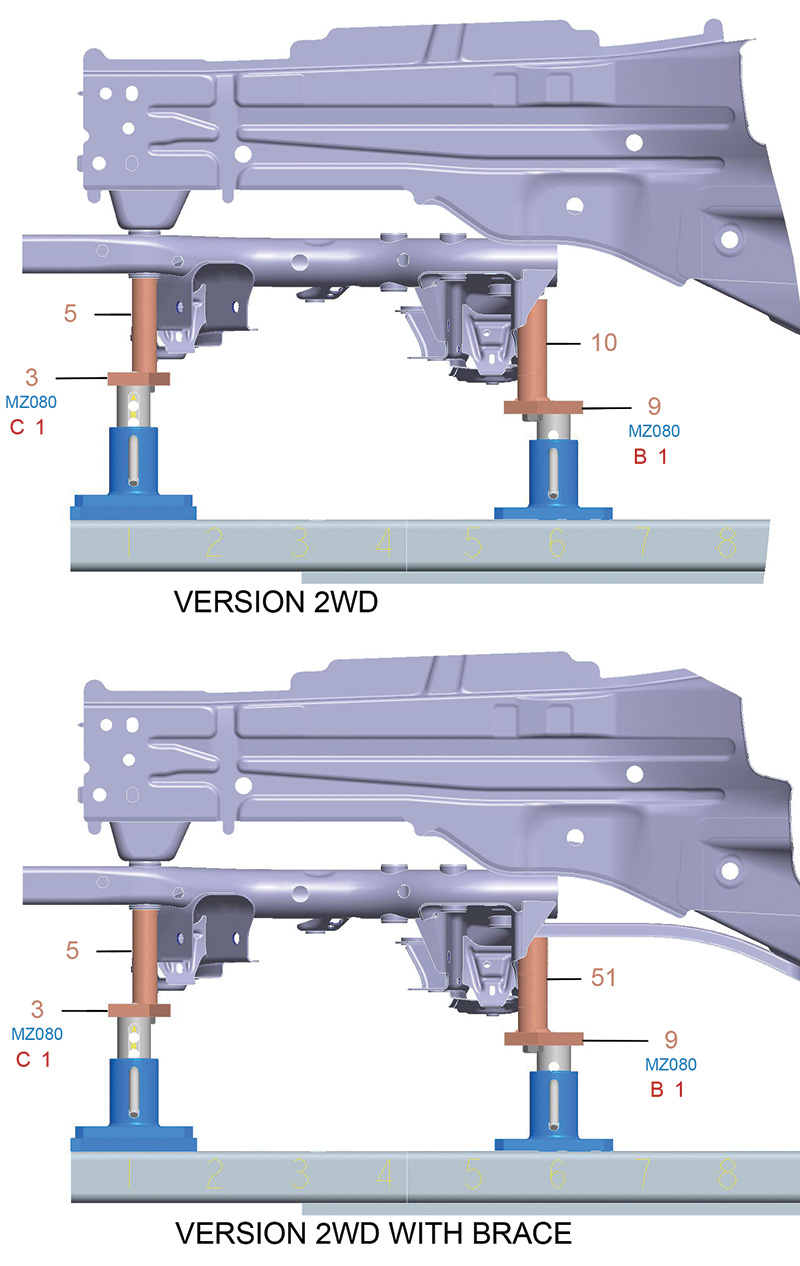
The Business Side
Training isn’t just for technicians: Running a more efficient business benefits everyone. Topics like how to do thorough damage assessment and repair planning helps the facility manager develop a good estimate. When estimators know what details to include in the repair estimate, and have familiarity with the specifics of a given model, they are far less likely to later need a supplement. Detailed estimates help prevent job delays, limit car rental expense, and maintain customer satisfaction.
Instructional Staff
As you might expect, Mercedes-Benz has some of the best instructors in the industry. Daimler AG, the parent company of Mercedes-Benz, insists that all technical trainers become Master Trainer Certified. This multi-year program emphasizes instruction delivery techniques, classroom flow and the psychology of learning. “It’s a lot easier to just show the students what to do, but that’s not how most people learn,†said Allen. “Instead, we have to let them make their own mistakes and get them to think about what they are doing. If I see something wrong, I’ll ask them to explain why they are doing it that way.â€
“Asking questions is the Socratic method of teaching, and it gets them thinking,†agreed Laurino. “Then we’ll talk about why Mercedes-Benz procedures ask that it be done in a certain manner.â€
The instructors guide students to the correct repair solution without telling them what to do. Encouraging the technician to dig deeper until he or she understands the documents prepares them so when they get back to their shop they confidently interpret instructions. “They no longer need an instructor looking over their shoulder,†said King.
Cycle Times
Instructors also emphasize cycle time, to help shops run more efficiently and to increase customer satisfaction. “We have them use the XENTRY Diagnostics tool, so they can be familiar with recalibration for Advanced Driver Assistance System sensors,†said King. While a XENTRY tool is not required for a collision center, the value quickly becomes evident. “Most calibrations take ten minutes or less using XENTRY, avoiding the time involved with a trip to the dealer,†said Laurino.
Peer Interaction
One often-overlooked benefit to instructor-led training is the chance to interact with peers from around the country. Once in the Mercedes-Benz training facility, students often get excited upon seeing something they have not seen before. “They call each other over,†Allen explains, ‘‘‘Hey, you have to see this new bumper. It has a different inside pull,’ or ‘They moved the plug over here.’â€
Students work alongside colleagues they haven’t before, and get exposed to different work styles. Because they come from different markets, some see a lot of one type of Mercedes-Benz model while others often see different models and problems. Or one technician comes from a market that has a harsher winter, while another hails from a region with higher average temperature and humidity. They learn a lot just from interacting with each other.
Get Certified!
This concludes our series explaining the Mercedes-Benz collision repair certification program. To learn more about the program, or to apply to become a Mercedes-Benz Certified Collision Center, go to www.mbcollisioncenters.com and scroll down to the link “Become a Certified Collision Center.†Once there you will find links to answers about a variety of questions, including a list of required tools and equipment, a document explaining the standards by which repair facilities, technicians, and staff are evaluated, a brochure that provides an overview of the entire program, and a program application form.
All you need to attend a Mercedes-Benz hands-on training class is a willingness to learn something new.
0 Comments