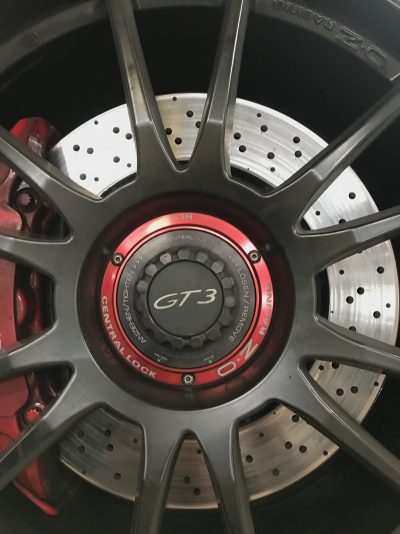
One of the hallmarks of Porsche cars has always been their reputation of having excellent brakes. Superior braking is one of the features that, in the earlier years, helped to earn Porsche’s reputation of being a “giant killer†at the race track. Lightweight vehicle platforms and monster brakes made up for what Porsches lacked in sheer horsepower.
Over the years, Porsche began to build street cars with engines that had been purposely built for racing and produced significant horsepower. Many of the gains in power have found their way into Porsche’s lineup of street cars, but braking systems have never taken a back seat in Porsche cars, and to this day they are a leader in advanced braking systems.
The Porsche Club of America has been hosting high performance driver education events at race tracks around the country for many years now, and more and more Porsches are showing up at these PCA sponsored events as well as independently sponsored high speed events. The Porsche specialist repair facility plays an important role in preparing these extraordinary cars for being pushed to their limits.
Extreme care, diligent maintenance and attention to detail are the keys to success when it comes to preparing and maintaining a vehicle for even the friendliest of competition. There is no worse feeling for a shop owner than to hear that one of your customers had an unfortunate incident during a high speed event.
There are specific challenges to be met when evaluating a vehicle for track use, and it is imperative to maintain the inherent safety engineered into braking systems while addressing normal functionality. In simpler terms; things that look bad may be acceptable and things that look good may not. Brake systems always require careful scrutiny and this applies doubly when a vehicle is being driven at a race track.
Brakes are easy, right? It is true that braking systems have been engineered for ease of service but that doesn’t mean things can’t go wrong or the systems don’t have complexity. It is a recipe for failure as well as a huge legal liability to not follow best practices when servicing any vehicle’s braking system, let alone one that will be pushed to its limits. Be certain to read any technical service bulletins before starting the work. Make sure you are aware of critical fastener torque values as well as recommended torque cycles (how many times a bolt can be reused) and sequences.
Brake Inspections!
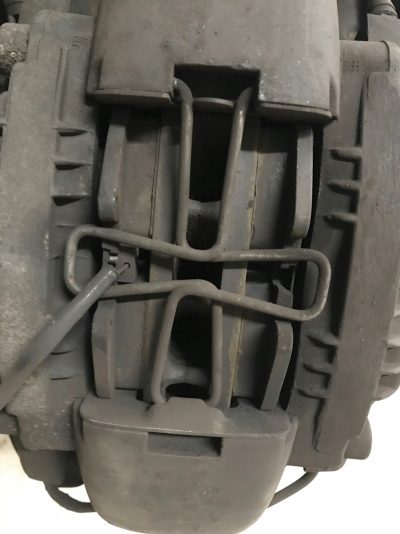
All brake jobs should begin with a thorough evaluation of all the components. Most shops have their own brake inspection form. If you don’t have one, get one and customize it for your specific needs. Always start with a road test and note any pulling conditions, unusual noises, firmness of the pedal, pedal effort and vibrations or pulsations coming through the brake pedal. Once on the hoist be certain to remove all wheels. Estimating brake pad wear by looking through the spokes of wheels will not necessarily give you an accurate assessment of brake pads and rotors.
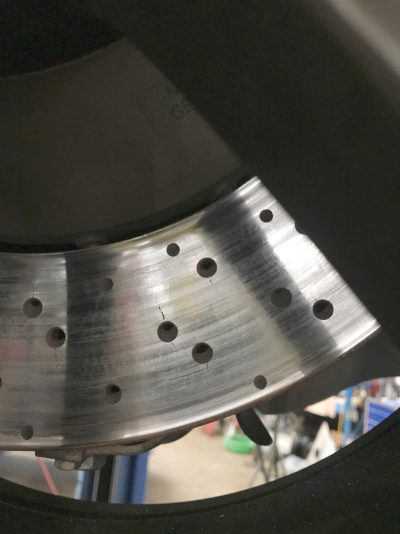
Pay special attention to the surface of the rotors and note any cracking that might be developing. Most modern rotors are now cross drilled which aid in cooling and the release of gasses that burn off brake pad binding material. The holes are also a great place for cracks to being to propagate. However just because a crack is developing does not mean the rotor should wind up in the recycling bin, especially on street-driven cars.
There are technical service bulletins that specifically describe the allowable depth, length and location of any cracks that might be developing. Always follow the specifications while determining the suitability for re-use of rotors and inspect the drilled holes themselves to make sure that they haven’t become blocked with rust or pad debris. Clearly, the function of the holes will be negated if they are packed closed.
Porsche rotors are thicker than its “grocery getter†low-performance cousins used for daily commutes. This additional material may allow for machining and re-use of this relatively expensive brake component. The problem is that many, if not most, shops have abandoned the practice of machining brake rotors and for good reasons. Brake rotors in service on “everyday†cars are typically not intended to be resurfaced. Conventional brake lathes are often crude and too lightweight to do a proper job and leave a professional, non-directional surface. How often has a well-intentioned technician attempted to machine a rotor only to wind up with a finished surface that has been compromised by a harmonic “chatter†as the result of ineffective equipment?
Rotors leave the manufacturing factory having been ground using a hard stone as opposed to being turned on a lathe with a metal bit. During the grinding process the rotor is rotated and the grinding stone contacting the surface is spinning as well. Grinding a metal surface is much better than turning due to two reasons; the aforementioned non-directional surface it leaves, and a more even surface without removing unnecessary amounts of material. Rotor grinding provides a better break-in surface for the new brake pads. Consider either finding a local machine shop with a proper rotor/flywheel surface grinder to resurface these rotors properly as opposed to risk ruining them on a dedicated brake lathe.
Cross Drilled Rotors
Drilling holes through the surface of a brake rotor has been a practice now for many years. The purpose for cross drilling rotors is to allow gasses to be released from the friction material’s bonding agent to disburse or “gas off†easily. If the gasses can’t escape quickly they will interfere with the ability of the brake pad to directly contact the rotor surface.
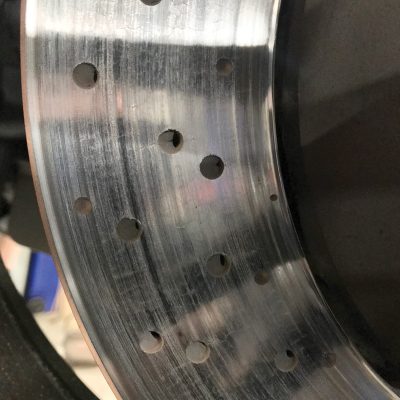
Another benefit for cross drilling is its ability to aid in cooling as well as the holes providing another pathway for heat to escape the surface of the rotor. The downfall of cross drilling is that often these holes become blocked either from brake pad and rotor material as it wears off the surface, or they can simply become filled with rust.
Once most of the holes are blocked the benefits are obviously negated. Cleaning the holes by running an appropriate size drill through them is an appropriate method for restoring their proper function. This is a simple but time consuming process and it is sometimes challenging to justify its value to your customer.
Brake hoses are an often overlooked component when servicing any brake system, Porsche or otherwise. It is still not uncommon, but it used to be a frequent practice, to replace the factory provided rubber hoses with a racing style “teflon†tube sheathed in stainless steel.
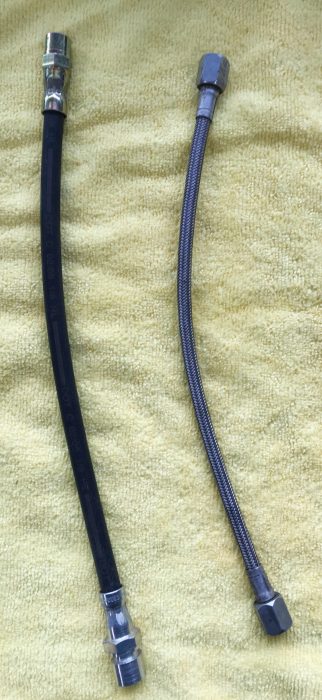
These were and still are credited with providing a more firm pedal feel due to an advertised resistance to bulging slightly under pressure. Like so many claims made by aftermarket marketeers, however, this and other claimed improvements are typically unsubstantiated. Certainly the stainless steel surrounding the tubing which carries the brake fluid is more durable and resistant to damage from foreign objects or debris one might encounter while racing.
It has been witnessed where a wheel, tire, hub and brake caliper, detached from their normal location on a race car as a result of an accident, can be dragged along by nothing more than the aforementioned stainless steel encasing the brake hose. While these may have been proven to be crash resistant in the racing industry, they often have not been tested by the DOT standards that the original equipment rubber hoses were subjected to.

Any repair facility installing such a critical component as the hose providing pressure from the master cylinder to the caliper had better be certain of its integrity over the long run. Brake hoses don’t often develop a leak from the material itself, but more frequently will fail where the flexible member (hose) interfaces with the threaded steel component that either threads to the steel line feeding it or the brake caliper itself.
Unless you are preparing a car dedicated for track use, a vehicle where brake hoses and all safety components are carefully monitored in an ongoing basis, it is better to stick to original equipment rubber style hoses that were provided when the car left the factory. These have been tested for long term use and often fit better than aftermarket counterparts. This also has the benefit of mitigating any liability issues as well. Any improvement in the pedal “feel†obtained by using a “racing†brake hose is often imagined by the end user.
The stock rubber hoses should be considered for replacement based on inspection as well as service history or aging. Any abrasion or cracking of the outermost rubber layer is reason for replacement. Inspect carefully the area where the rubber connects to the steel, threaded component as this is a common failure point.
If there is a complaint of a spongy pedal feel, have a second technician apply the brakes firmly while watching all of the rubber hoses for any bulging. Bulging can occur as a result of a structural breakdown of the hose’s internal reinforcing material. The innermost rubber lining of these flexible hoses can occasionally swell up and restrict the flow of brake fluid. Having an extreme amount of pressure available at a driver’s foot in the form of a power assisted master cylinder, a driver can push fluid through this restriction.
The return pressure, on the other hand, is not nearly as great, and the result is that an internally restricted brake hose can mimic a seized brake caliper. A simple means of diagnosing such a condition is to open the bleeder valve at the dragging wheel. If the wheel begins to turn easily as fluid flows from the caliper then the brake hose can be pinpointed as the culprit. If, however, the wheel is still reluctant to turn, it is likely that a piston is seized in the bore of its corresponding brake caliper.
Most Porsche specialists know the importance of flushing a car’s brake hydraulic system. Manufacturers generally specify that the brake hydraulic system be flushed about every two years. Due to the hygroscopic nature of brake fluid, mileage is not a factor, only age.
If a vehicle is being prepared for a track event the officiating club may have a more stringent interval for renewing brake fluid, with some clubs requiring the renewal of the brake fluid before each event. The more frequent interval is required due to the fact that the brakes will likely be used more aggressively than they ever have before. This hard usage can be especially true of a novice driver. Even a tiny amount of moisture in a vehicle’s brake fluid can dramatically lower the boiling temperature which can then result in dramatic brake pedal fade.
It is incumbent on the repair facility which is preparing the car to be certain to use a high quality brake fluid that meets the highest boiling temperatures while also meeting or exceeding the manufacturer’s specifications. It is also important to adhere to the sanctioning club’s requirement, which should be defined on the tech inspection form provided by the club itself.
ABS braking systems have been around a long time and require no special care during normal service. Proper maintenance is nothing more than inspection of the sensors and tone rings at each wheel and a bit of additional care during bleeding procedures.
The majority of problems arise as the result of a speed sensor being unable to “read†a tone ring. This can be caused by an internal sensor failure or dirt buildup in the form of rust at the tone ring. Rust can occasionally be the cause of a tone ring cracking. Be certain to look closely at these items and clean any debris or rust that might be accumulating.
During bleeding procedures it is also best practice to flush fluid out of the ABS valve body itself using a proper scan tool to actuate the valves which modulate brake pressure. There is very little fluid volume in the pump module valve body itself, so one need not necessarily account for additional fluid.
Many technicians have developed a bleeding technique which relies solely on using the pump and control module. This method does not require either a second technician or the use of a pressure bleeder and addresses the issue of bringing fresh fluid through the pump. ABS function is monitored through the system’s control unit and will illuminate a warning light if the system is not working properly.
Repairing brakes, either to be used at a track or “normally,†is an area that exposes a facility to significant liability. Utmost care and attention to manufacturers’ procedures is the key to keeping your customer as well as your business safe.
Download PDF
0 Comments