By Greg McConiga
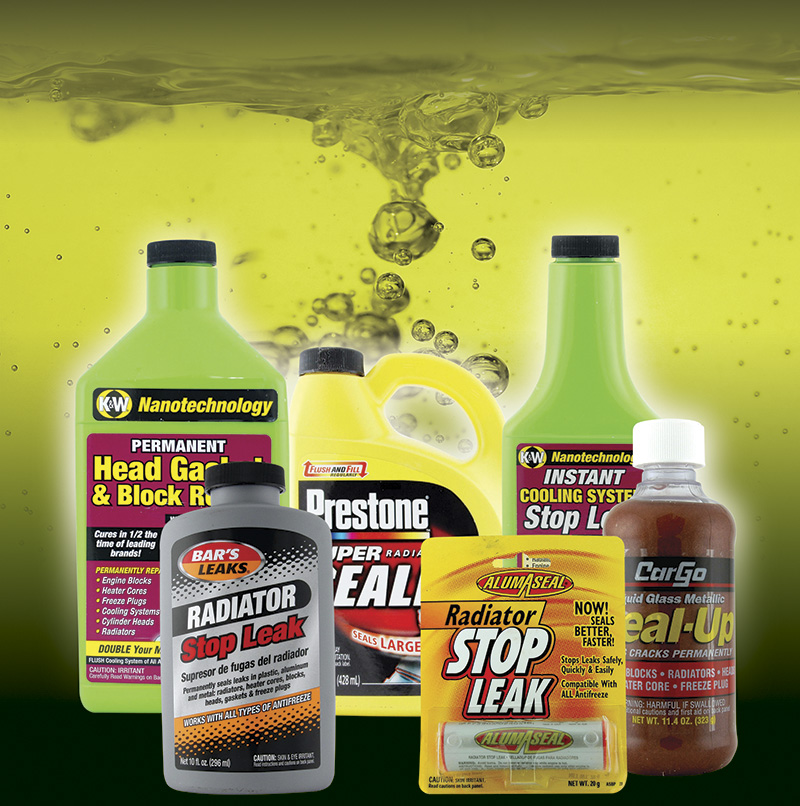
These products are commonly found at mass merchandisers, and the directions on all of them state that the system must be clean prior to use. Some also say that the system must be first flushed, then filled with plain water, then flushed again before re-introducing antifreeze.
We’ve all seen it: a customer with little or no money driving a car near the end of the trail with something major leaking coolant. It’s difficult to give good people in mean circumstances bad news, isn’t it? I don’t like it, either.
Engine cooling system sealers have gotten a bad name with professionals over the years, a reputation that may or may not be deserved. In nearly all cases, cooling system sealers are sold over the counter at major discounters and poured in by car owners themselves. As service professionals, we see the results of improper use, but rarely see instances of successful application. To us on the outside looking in, it seems the thought process runs along the lines of, “If one can is good, six should be great!†Or, “Hot engine? Clean the cooling system? I’m not pulling the cap off of a hot engine and I’m damn sure not flushing this wreck! They aren’t really directions, right? More like suggestions. This stuff will work in a cold engine with a crapped up cooling system . . . let’s just dump it in,†and so on. All of which might be part of the reason why sealing products have the reputation they have.
Sometimes the Magic Works . . .
Before we write another word, we need to clarify one point: This isn’t Mechanic-In-A-Can. It can help some conditions, but it can cause problems if misused. If you misuse it, do so at your peril because the one thing engine cooling system sealers do is seal stuff up — including radiators and heater cores when used incorrectly. Should sealers even have a place in the “toolbox†of professionals, or do we just condemn the car and let the customer walk? The answer is, “It depends.†Or, as they say, “A definite maybe.†We need to know a bit more to make a good decision. There are professional-grade products out there that radiator repair specialists use, such as Barbee’s SpotWeld or Air-Flo. So, perhaps we’re safe in assuming that sealing products might make sense in our shops as well.
Not all sealing products work well in all designs of radiators, or with all cooling system materials. Some sealers work well with copper/brass, others with aluminum, and some parts of radiators don’t like sealers at all – especially plastic or resin. Our sources tell us that they’ve never seen a sealer that provides anything other than a temporary fix for plastics and resins. For some reason, the chemical and sealing agents will not permanently adhere to non-metallic parts. They might seal for a while, but long term the leaks return.
The Nature of the Beast
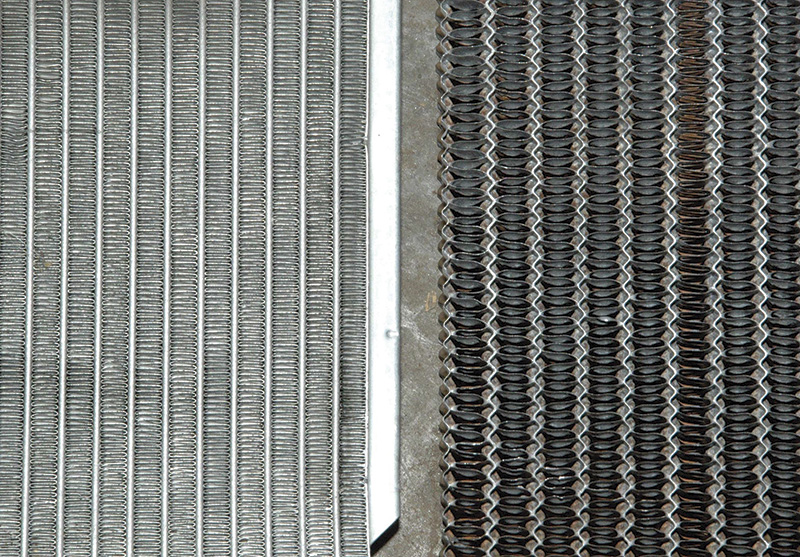
Heater core design runs parallel to that of radiator core. Early versions (on the right) suffered from the same tendency to become restricted as radiators sharing the same construction style.
A quick primer on radiator and heater core design is in order. While we will only refer to “radiators†in the next few paragraphs, remember that heater cores are similar, and core affinity for sealers will be the same for any given heat exchanger design.
Early radiators used a core design called a diamond cell. If you look closely at antique radiators you’ll see why they were so named. The air flows through a diamond-shaped hole with two tiny fluid paths diverging at the top point, passing around the border of the diamond, and converging at the bottom, which becomes the top of the next diamond only to divide and converge again, repeating the process over and over to the bottom of the core. These cores were heavy, difficult to build, expensive and had a myriad of tiny passages susceptible to plugging with the addition of any foreign substance. Ever hear grandpa talk about making it home by putting pepper in his radiator? This is the core type he was probably talking about. Repairs were difficult, time-consuming and required patience. They were hand stacked and built cell by cell by skilled artisans.
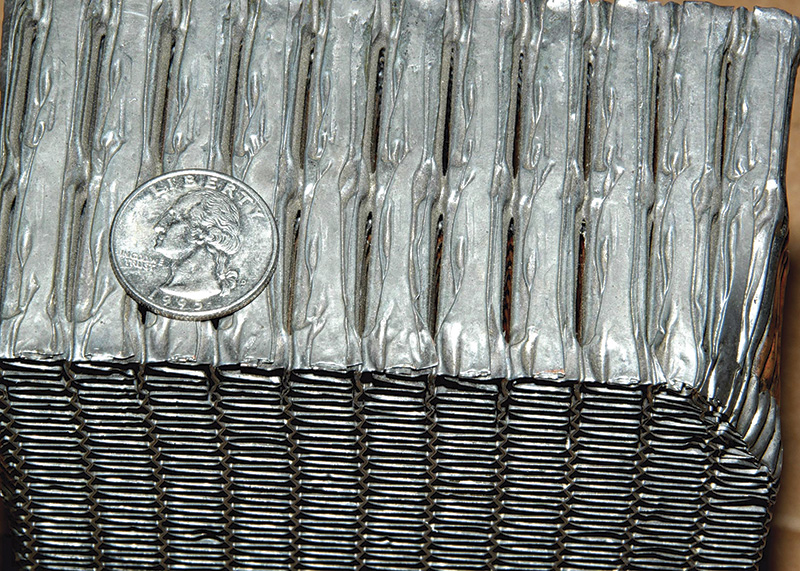
The dipped construction technique for a “U†cell core is evident in this photo. Note the narrow coolant channels and the excess solder built up around them.
The next generation of radiators had “U†cell and “V†cell cores. Made up of a series of stamped plates, these cores are assembled by dip-soldering. They are structurally strong and offer excellent cooling performance. Plates are stacked with the end of each plate folded over its neighbor until the desired width is reached, and the assembly is then dipped in molten solder, front, back and both ends. Thickness and height is determined by the physical dimension of the plate and width of the core by the total number of plates in the stack. While the solder is still molten, the coolant flow path is blown clear or allowed to drip clear of excess solder. The coolant side is made up of the void between plates, and the passageways are relatively small with irregular and rough tube walls – again, susceptible to plugging. This core is also heavy and expensive to make. Remember; with diamond cell, “U†cell and “V†cell cores, the common theme is narrow coolant flow channels with rough or uneven walls in the fluid channel. These were the dominant designs through the early seventies.
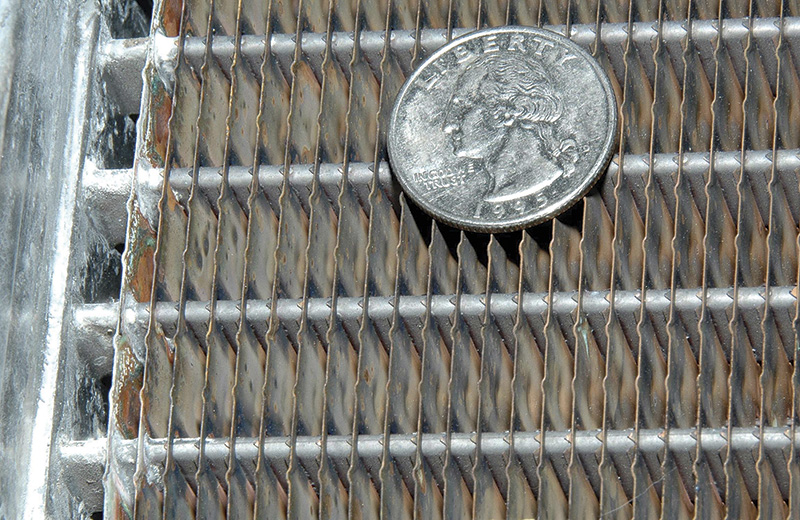
This is a great example of two design features, a flat fin core with a plated corner (note the additional plate attached to the header).
Next came the flat fin. Basically, this radiator is a series of fins that are held fast in a jig while a mandrel-formed tube is punched through them top to bottom or side to side. The fins may be flat, dimpled or louvered. These cores are strong, offer a larger coolant flow channel with smooth walls and perform well, but, again, they tend to be heavy and expensive to make.
Beginning in the ‘70s, reducing mass became a prime engineering focus as government-mandated fuel economy and emissions standards ramped up. We saw the results of this dieting binge in the next generation of radiators, the serpentine tube core. Basically just very thin fin stock folded and bonded to pre-formed tubes, its thermodynamic performance is acceptable, but the core suffers from a serious lack of strength. Corner leaks were common as these cores tried to expand across the diagonal until someone thought to add strength by plating or reinforcing the corners. Weight and costs were coming down, but at the expense of durability.
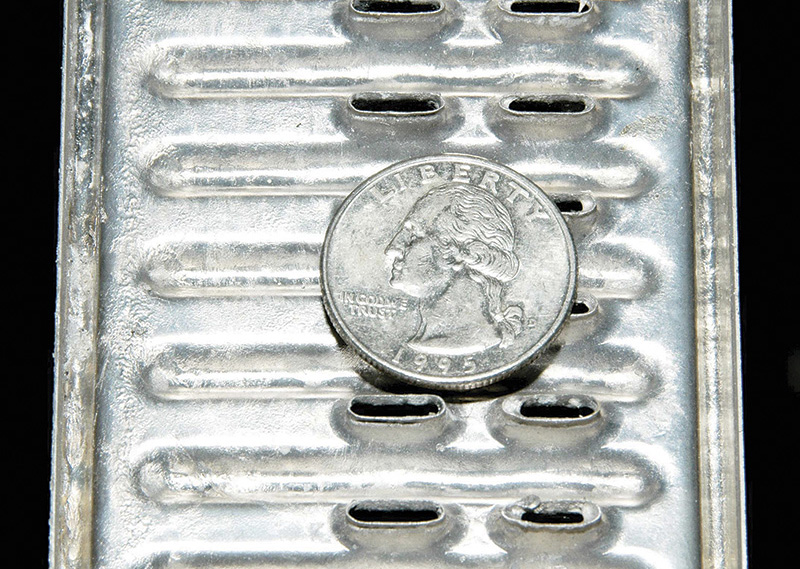
Compared to modern aluminums, the serpentine core tube size is tiny. If you look closely, you can see bits of solder slag partially blocking the flow channel. This core is much, much more prone to plugging up than the aluminum core shown. Design and construction determines susceptibility.
Fast-forward to today and the ubiquitous aluminum core and resin end tank radiators, a.k.a. “PTRs†(Plastic Tank Radiators). How well do they work? Just great. Widespread use was delayed only by the need for an affordable manufacturing process that would produce a durable product. Square inch for square inch, aluminum cores do as well as the best designs of the past with the added benefit of being light and durable.
We walked through this design time-line only because it highlights something that we need to think about: Much of the negative reputation of sealing products came about during a time when the core design itself aggravated the tendency of a stop leak product to “over perform†its mission. The core tubes were too small and the rough surfaces of the tube walls too eager to grab onto the product, contributing to what is often an undeserved reputation for clogging up the works each and every time they’re used. Today, with the large, smooth flow channels found in aluminum radiators, the biggest problem with sealing products is misuse.
Something to think about here is that there are many very low quality off-shore cooling system components making their way to our market. Just because a radiator appears to be of a modern design doesn’t mean its construction will tolerate the use of sealing products. Cheap suppliers often skimp on materials and engineering, and the cores may be just as bad at plugging as earlier designs if the flow channels are improperly made. Any tube design that’s rough, small and uneven can cause problems.
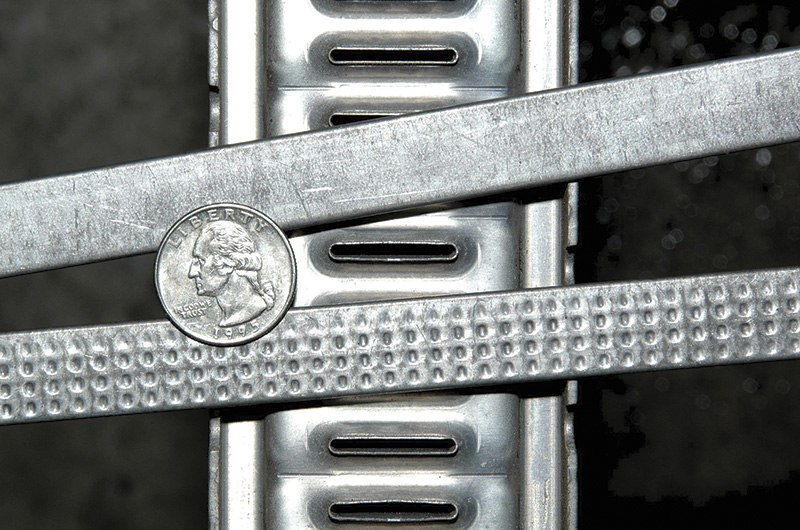
Take a look at the size of the coolant flow channel in a late model aluminum core. The tube inlet is smooth and clear. Tubes may be dimpled or smooth walled.
Read the Directions!
If you read the directions of virtually any brand of cooling system sealer you will see that they all state that the cooling system must be flushed prior to installation. Let’s be honest here: Most cars that are candidates for products like these have been abused. If the cooling system were pristine, it wouldn’t need a sealer, right? Several products also state that the system must be filled with plain water before they are introduced into the cooling system, and that the product will gel antifreeze. Also, in many cases the directions clearly point out that the product must be removed and the system re-flushed with clean water prior to the reintroduction of antifreeze.
We stopped at a major discounter to purchase several of the products you see pictured here, and we saw a customer dumping sealer into the radiator of his steaming heap right in the parking lot. Care to guess how often that’s happened? In our mind, it’s hard to blame the product for poor performance if the guy pouring it in won’t follow the directions.
From the Factory
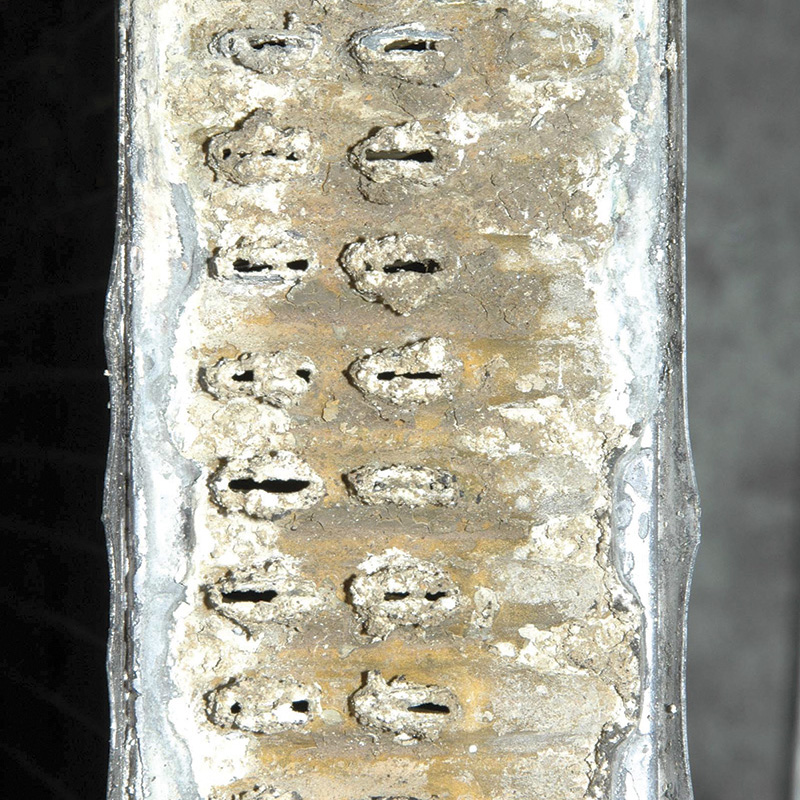
It doesn’t take a lot to plug up a serpentine core. This is what nasty make-up water does when combined with an extended service interval. Alkaline deposits like these are often mistakenly referred to as “solder bloom.â€
Nearly all manufacturers add a mild stop leak/cooling system conditioner to new car on the assembly line to stop cosmetic or nuisance seepage that might affect customer satisfaction — can you think of anything worse for the carmaker’s reputation than having a customer sign up for sixty to eighty-four months of payments on his or her new iron-pile only to find that it marks its territory on the maiden voyage to the driveway? From what we were able to determine, the factory-installed products all seem to be very mild organic stop leaks made from (of all things) tree bark or other plant material. From our own experience and from the vast of experience of the best cooling system guy we know — John Wood of Ace Radiator in Ft. Wayne, IN — we’ve never seen a problem that could be attributed to the factory-installed sealing/conditioner. After spending a Saturday rummaging through John’s scrap pile at his Fort Wayne location, we could find no evidence of any core plugging caused by the O.E. products. We did see lots of problems with lime deposits, solder bloom and crud due to poor make-up water quality, but nothing that could be blamed on sealing agents.
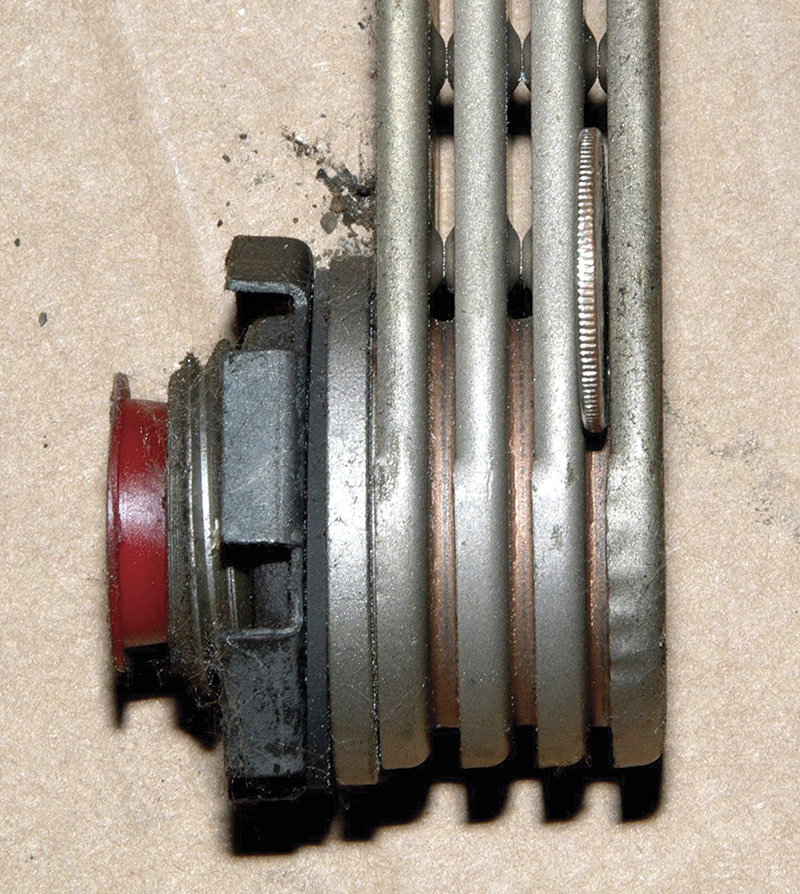
Plate-type transmission oil coolers can end up trapping cooling system debris, including excess sealers. Narrow channels and high rates of localized heat exchange contribute to the problem. High transmission oil temperatures will damage a transmission in short order.
Following these simple rules when adding a sealer will keep you out of trouble:
- Keep the cooling system full because air is the activator.
- Check the water level several times a day until the leak subsides.
- Follow the directions for use exactly since each product reacts differently.
- Avoid use in older systems with cores prone to plugging due to design.
- Don’t use more than specified because more is not good in this case.
- Instruct the customer to keep a close eye on engine temperature if the car is equipped with a gauge, and have the leaking component properly replaced or repaired at the first opportunity.
Engine cooling system sealers are not a cure-all and they won’t replace the repair that’s actually needed. When improperly used or when used in excess they will cause secondary plugging of heater cores, radiators and, in some cases, transmission coolers, which leads to transmission damage. When used properly they will often buy a customer time to save up for major repairs.
We would like to thank CRC (maker of KW engine sealing products with nanotechnology), especially since it was the only company contacted that responded (and we called them all!). Why did phone calls and e-mails to other manufacturers go unanswered? Our guess is that they thought this was going to be a smear campaign. Fooled them, didn’t we?
We’d also like to thank our good friend John Wood for giving up several hours for the benefit of MT readers, and letting us mess up half his shop (sorry about your scrap pile, buddy!) You can reach John at 1-800-288-7964, or jwood@aceradiatorinc.com.
0 Comments