It’s only a matter of time before your state passes legislation mandating the use of water-borne paint in an effort to reduce VOC emissions. What’s really involved in managing this change?
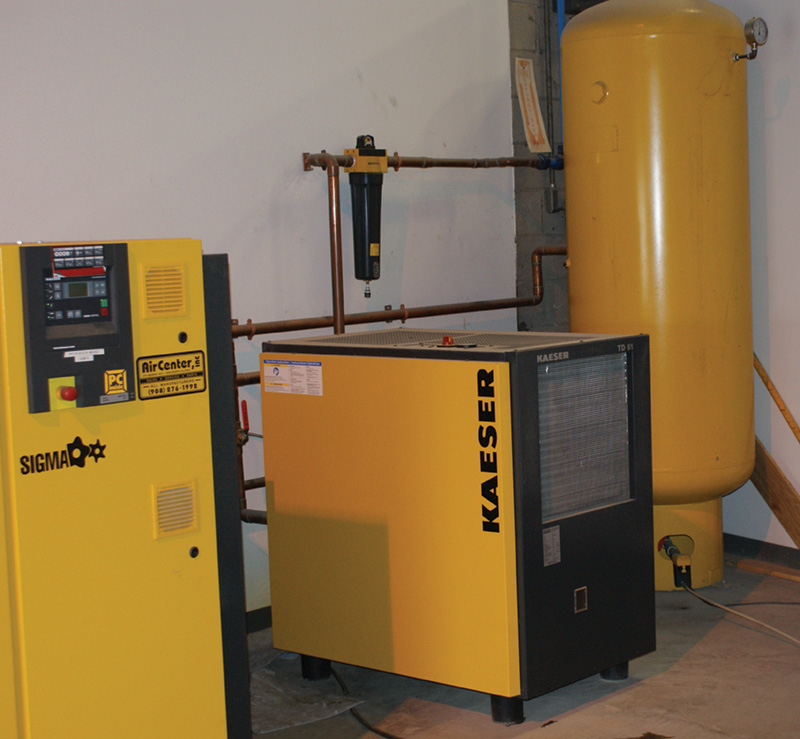
In large-volume shops, you may need a more elaborate air filtration system. This one has a large storage tank for the paint booths. Smaller systems are available, but Mercedes-Benz recommends that they have at least three-stages.
Water-borne paint technology is not as new as you may think. During the 1990s the German government required its use in auto body facilities, so its development has been going on for 20 years or so. Typically, paint pigments are suspended in a liquid that can be evenly applied to a surface. As the liquid medium evaporates it leaves the color coat behind. Solvents or VOC (Volatile Organic Compounds) are the most common fluid mediums. Solvents evaporate easier, quicker and at lower temperatures than water. These solvent-based VOCs are not only harmful to your painter, but also to anyone else in your collision repair facility. So, an organization called OTC (Ozone Transport Commission) is working on legislation mandating the use of the water-borne paint application process in several states over the next few years. In addition, water-borne technology has turned out to be a more cost-effective solution when it comes to refinishing.
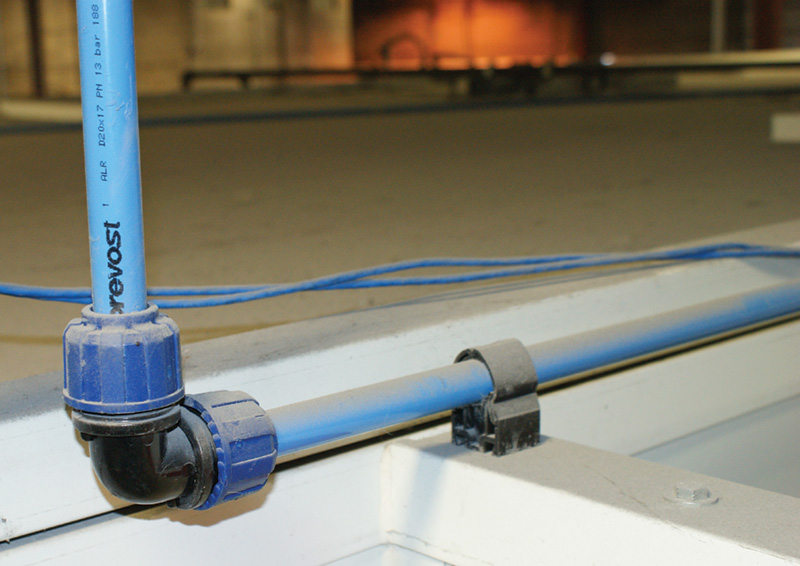
In order to prevent rust contamination as your equipment gets older it’s necessary to install aluminum, plastic, or copper piping from you filtration system to your paint booths.
Due to metal panel oxidation, you still need to use solvent-based coat primers and high-solid clear coats, but using water-borne in the color coat process does help reduce the VOCs in our atmosphere. There are other benefits to water-based paints, too. The application process is slightly different, but there is less over-spray, which makes it easier to control color blending. Also, with a reduction in over-spray it’s possible to cut paint costs by up to 30 percent. During the vehicle production painting process special paints are used where the chemical composition is suited to larger volumes and higher temperatures. In collision-repair paint booths, the conditions are slightly different. That doesn’t mean we can’t match the color, chip resistance, and gloss. As a matter of fact, Mercedes-Benz has approved four different paint brands produced by three different manufacturers that fulfill all requirements (not all paint brands by these manufacturers are approved). This means your current supplier, or your Mercedes-Benz dealer, should be able to sell you what you need.
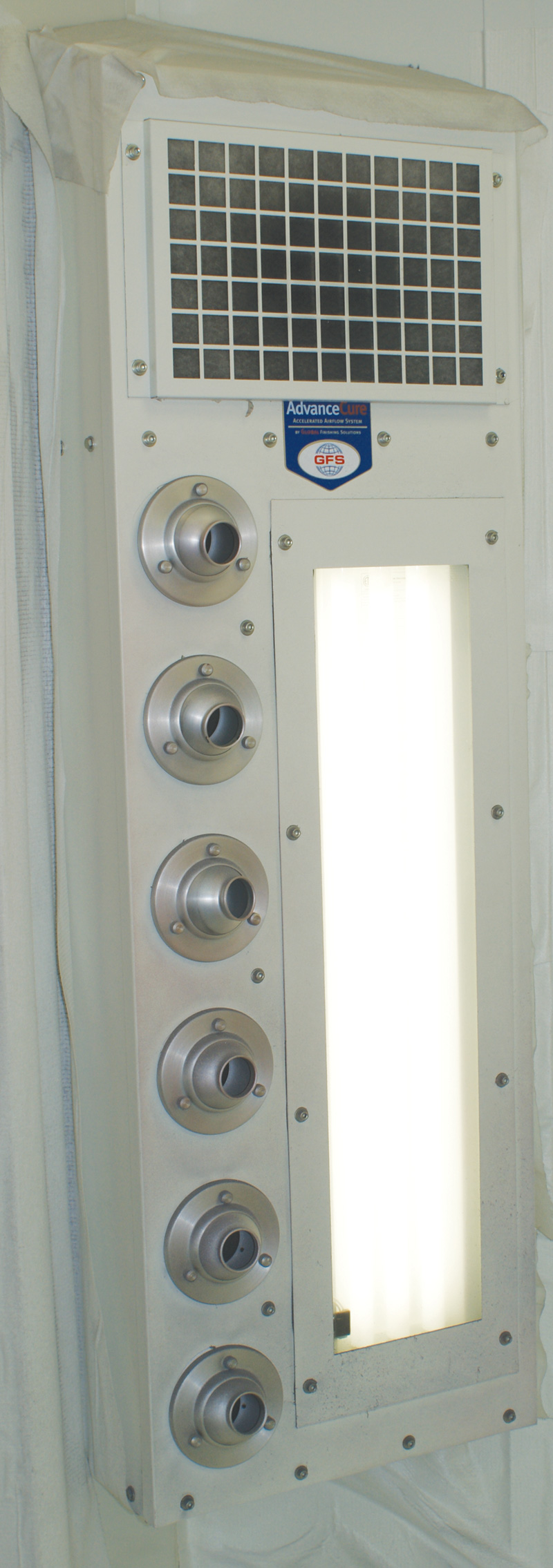
Air movement is the most important factor in drying water-borne paints. Temperature has less effect. Paint manufacturers have developed paint with improved drying times comparable to solvent-based finishes.
The approved brands are:
- Glasurit 90 Series from BASF (for more information on working with 90 Series paints, visit: www.basfrefinish.com).
- Permahyd from Dupont’s Spies Hecker Division (
www.SpiesHeckerUSA.com). - Standohyd from Dupont’s Standox Division (
www.standoxna.com). - Envirobase from PPG (www.ppg.com – look under “Paints & Coatings†for “Automotive Refinish,†and you will be directed to the correct website).
As we said, each of these paints meets or exceeds Mercedes-Benz requirements for color matching, chip resistance, and gloss.
But there’s something else you can get from these companies besides excellent paints: Training in how to handle and apply them. As BASF puts it, “At the core of BASF training is an extensive curriculum of classes in product knowledge and use, refinish techniques, troubleshooting, specialty finish repair and color matching. In addition, BASF offers many courses on business management, profitability and productivity enhancement.â€Â Pretty much the same can be said for the other two manufacturers. And this training is available both in a traditional classroom, and as e-learning. As PPG says, “Courses are scheduled throughout the year at 16 PPG Business Development Centers across North America. Instructional videos and online courses are also available so you can study on your own time, at your own pace.â€
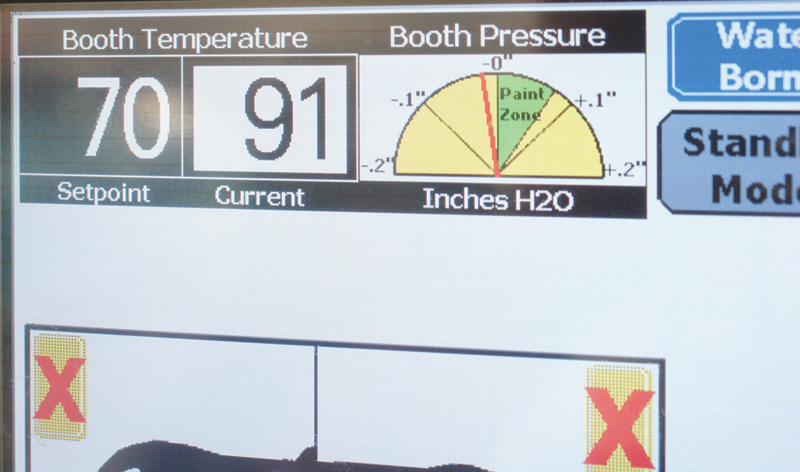
You may have to vary the settings of your paint booth to account for ambient temperature. As you can see here the temperature is set for 70 deg. F., but the actual reading is 90. Use lower temperatures for longer drying times.
The biggest expense when switching to water-based is going to be whatever you decide to do about your paint booth – adapting it, or replacing it. Does your current booth have the ability to flow sufficient air, which results in quick drying times? Another part of the curing process is heat. Heated booths dry paint faster and would work well in high- production shops with this new type of paint. If the investment in a newer high air flow/heated booth is not in your financial future, then you can think about auxiliary systems. You probably already have heat lamps, but the more heat the better. You should add auxiliary blowers to help circulate the warm air. Two larger blower units and one handheld unit should be all that you need for most repair jobs. Moving on to the clear coat without proper drying of the color coat could result in “fisheye†or “solvent pop†in the finish. Improvements have been made by the paint manufacturers to improve drying time. That’s a big help, but ambient humidity can still have a negative effect.
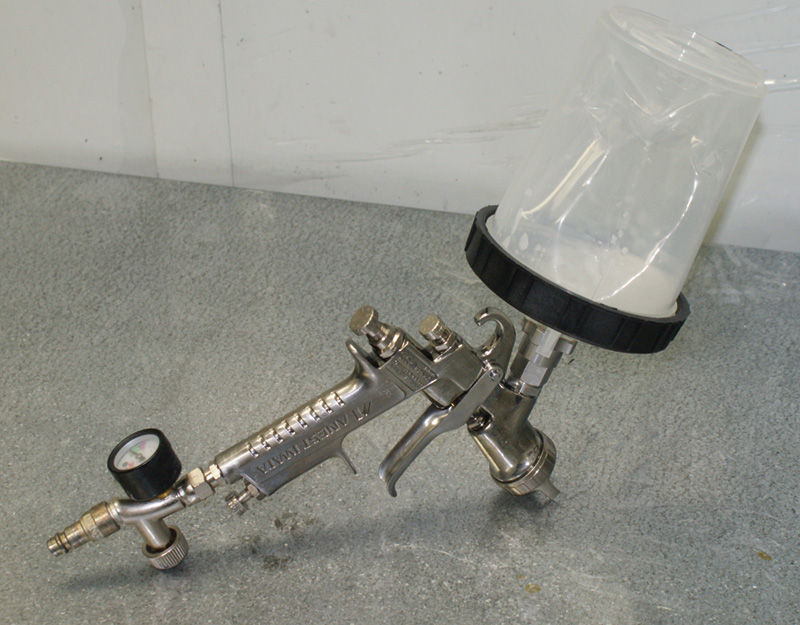
Your HVLP gun should be set to between 25 and 35 psi while applying the color coat. The regulator on the gun will allow you to precisely control this pressure. Try to stay away from metal reservoirs as they will corrode over time.
Another important part of converting to water-borne is your compressor. HVLP (High Volume Low Pressure) means your compressor is going to need to be able to supply more CFM (Cubic Feet per Minute) for your HVLP guns. You may think you already have enough, but if you look at the load created by operating air tools in other parts of the shop you have to ask yourself if your compressor is actually up to the task. And CFM isn’t the only issue; dry air is another. You need to remove as much moisture from the air as possible, and that can only be done with a multiple-stage filtration system. Also, you should not be using cast iron piping for your air lines because rust will interfere with the painting process. Copper, aluminum, or plastic are the lines of choice when supplying air to your paint booth.
Now, how are we actually going to apply the paint? First, HVLP guns are needed for water-based paints. Even though a high volume of paint is sprayed, less over-spray is created. You may have to change your technique from what you normally do to apply solvent-based paint, but most refinishers have found that once they get the hang of it, it is actually easier to control paint thickness and blending. Very often, if done properly, you only have to apply one and a half to two coats before the flash-off period to finish the job. With water-based paints, stay away from metal cups. Switch to a plastic reservoir for the same reason you shouldn’t use cast iron pipe for air. You must keep metal corrosion out of the equation. You need to have two sets of tools to work on steel and aluminum, and, for the same reason you need to have two different guns for applying solvent- and water-based paints. Cross-contamination is verboten and should be avoided at all costs.
Once properly tooled up, you will find that refinishing vehicles with water-borne paints can be a healthy, cost-effective solution that most of us never thought of. Paint manufacturers have addressed the issues with these paints so the transition should be fairly smooth. In this day and age, who couldn’t use that!
Special thanks to the staff of Mercedes-Benz of Manhattan for their help with the photography for this article. Â
0 Comments