by Greg McConiga
Last time, we covered history, operating principles, and design fundamentals. Now, for failures, diagnostics, and replacement alternatives
Let’s start by putting detonation into perspective: It’s the biggest problem with the high cylinder pressures that turbocharging can produce. Charge air coolers, proper compression ratios, proper turbo sizing and waste gate settings, engine temperature and fuel control, timing rates, quality fuels and tight oil control all help stave off these explosions.
Sub or supersonic
While we’re on the topic, detonation is NOT and never has been colliding flame fronts. Flame fronts do not make noise when they hit. You can collide flame fronts all day long and never enter detonation. Ford twin-plug 2.3 and Nissan Nap-Z engines intentionally created two flame fronts, as have innumerable aircraft, racing and specialty engines. Normal combustion proceeds at subsonic speeds and spreads by thermal conductivity. Detonation is supersonic and spreads by shock compression. Subsonic and supersonic: propagated by heat, propagated by shock; that’s the difference. Detonation occurs when the cylinder pressure and temperature cause the last bit of unburned fuel in the cylinder – called “end gases†– to spontaneously explode in uncontrolled combustion. Normally, a flame front rolls or proceeds through the air-fuel mixture in a few thousandths of a second – depending on air-fuel ratio and cylinder design it varies between .001 and .004 seconds – but the explosion of detonation occurs so quickly it’s measured in microseconds – literally thousands of times faster than a normal combustion process.
Detonation exists in three phases: Inaudible (can’t even hear it over normal engine sounds), audible (the BBs or marbles-in-a-can sound we’re all familiar with), and hard detonation, which sounds like a really bad rod knock or someone with a big ball-peen under the hood. Trust me, you’ll know it if you hear it, and you won’t hear it long before you end up walking! In over thirty years I’ve only seen it a couple of times in a street vehicle, and in both cases it was too late. Depending on severity, detonation unseats rings, anneals parts, turns valves inside-out, sets up violent ringing vibrations in the assembly, breaks rings, cracks heads and blocks, destroys head gaskets, fractures piston tops and pounds the tar out of the reciprocating assembly.
Diagnosing a tornado
Diagnosing detonation is easy — the damage is so pervasive it’s like diagnosing a tornado. On a teardown, the piston top will be clean and appear almost sandblasted. The land above the upper ring may be beaten down and the second ring pinched. In a lot of cases, the piston will be burned down the side or have a hole burned through the dome. The upper half of the rod bearings and the lower half of the mains will show signs of fretting or damage. Piston pins may be stuck or sticky, rods twisted or cracked and crankshafts fractured. On spark plugs, you’ll see clean, almost sand-blasted appearing porcelain and under magnification you’ll see tiny blue-black balls of molten aluminum stuck to the insulator. In loud high-performance engines, you’ll feel it before you hear it, and if it’s hard detonation you can’t lift fast enough to keep from tearing something up.
For causes, think lean (less evaporative cooling during the gas exchange cycle), insufficient octane (the numerical measure of a fuel’s ability to withstand detonation), secondary ignition sources and over-advanced timing (lights the mixture early, and pressure builds while the piston is still trying to rise in the bore), too much compression or boost (or any other cause of high cylinder pressures), cam timing and profiles (early or late intake closing affects cylinder pressure) and overheating, either generally or locally (heat is pressure in a closed system.)
Brave new world
Growing population aside, there are a lot of things looming on the horizon. Like all old technologies that grew into modern applications, turbocharging is evolving. The improved efficiencies of variable nozzle turbines, wastegate elimination and ball bearing center housing rotating assemblies are just the start. Compressor and turbine wheel shapes are evolving, housing designs with multiple flow paths are on the market, and lighter titanium wheels and machined-from-solid parts are just entering the world of automotive turbocharging (you’ll recognize the titanium compressors – they will have cast iron compressor housings instead of alloy to meet burst wheel containment requirements — think a scattershield for 20 times the rpm of an engine).

New compressor and turbine wheels are not through-bored. On this “boreless†wheel, a partial bore-through is threaded, and the wheel threads directly onto the shaft.
Even wheel-to-shaft attachment methods are changing. The oldest design bore is smooth, with no threads in the wheel, retained on the shaft by a nut.
The treaded bore is just that; the wheel bore is threaded and screws right onto the shaft. The latest wheels are boreless; they are bored and threaded part way through the wheel to eliminate the stress risers that emanate from a through-bored wheel face, which is a good thing at 100,000 rpm. Expect to see even more advances in gas and air flow control, and more improved oil control, better cooling, and reduced turbo lag.
Given good fuel control and normal exhaust temperatures, clean, properly maintained and undiluted engine oil, water-cooled center housings, properly maintained air filtration and just a few precautions on the part of the owner, a turbocharger will last the life of the car. If these conditions aren’t met, there will be a failure, and if there is a failure there is very often little left to rebuild, especially in the event of foreign object damage (FOD), or lack of lubrication, the two most common turbo disasters. This is one reason that more and more rebuilding is moving to the manufacturers. Shafts, housings, wheels and bearings are often completely destroyed, making field rebuilding financially impractical.
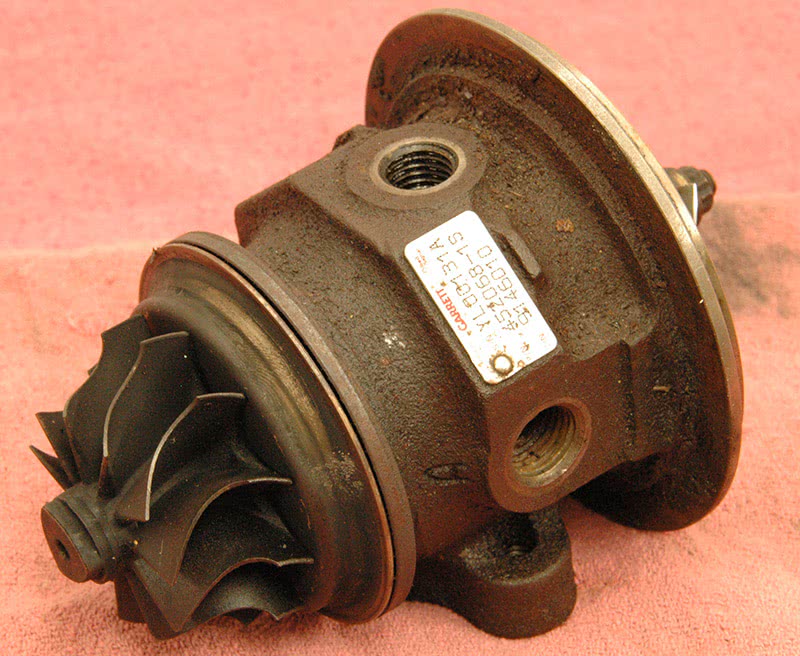
The oil feed inlet is on the top, the oil feed outlet is on the flange it’s sitting on and one of the two water supply ports faces the camera. Water cooling the center section is what really made turbocharging practical on passenger cars and light trucks.
Before grabbing a fistful of tools and tearing something apart, stop, look and listen. Most people know what a turbo-equipped vehicle sounds like. There’s that characteristic turbo sound, sort of a low pitched whistle that rises in pitch with engine speed. Take the time to road test the vehicle and see if you’re hearing and feeling what you should be hearing and feeling. You might just uncover an exhaust or intake system leak by listening, or you might hear something whirring or screeching that ought to be silent. Plus, if you know what it did before you’ll know that you fixed it when you do your final quality control road test.
Oil-related failures are usually due to some manufacturer’s incredibly long recommended oil drain interval (What the hell are they thinking? Let’s see… $30 oil change, or $2,000 turbo? Brains not necessary, apparently), or poor maintenance on the part of the owner. Turbos handle and retain a huge amount of heat, even after shutdown. You must use the correct oil type and viscosity. Many of these engines specify synthetic oils, so pay attention. After the oil change, never rev the engine until oil pressure builds. If you don’t get proper gauge movement, or the engine low-pressure oil light isn’t out in 15 seconds, shut ‘er down and investigate. Even at idle speeds it only takes about thirty seconds to damage the turbocharger bearings. If you rev the engine right after oil change, you might damage the bearings instantly. Don’t do it! If you get a lubrication-related turbo failure and it’s a water-cooled unit make sure the cooling supply in and out is unrestricted and that the cooling system is operating properly. It’s also a good idea to replace the oil supply and return lines at the same time since there have been many instances of these lines coking shut with heat. I’d advise anybody with a turbocharged car to allow 30 seconds of idle time prior to each shutdown after a normal drive cycle. I know it’s a pain, but those few seconds will extend turbo life and save money. I’d also advise that if they’ve been out “whuppin’ it up†to allow two or three minutes of cool-down time prior to securing the engine. It’s a small price to pay.
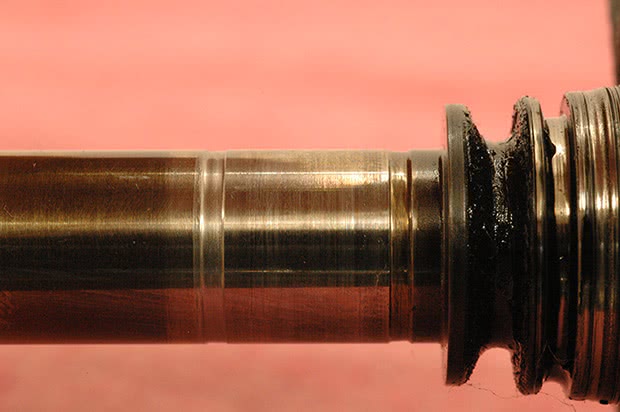
It’s not uncommon to seize bearings and snap shafts. Look for discoloration and tiny “welded†spots any time you have one apart.
FOD
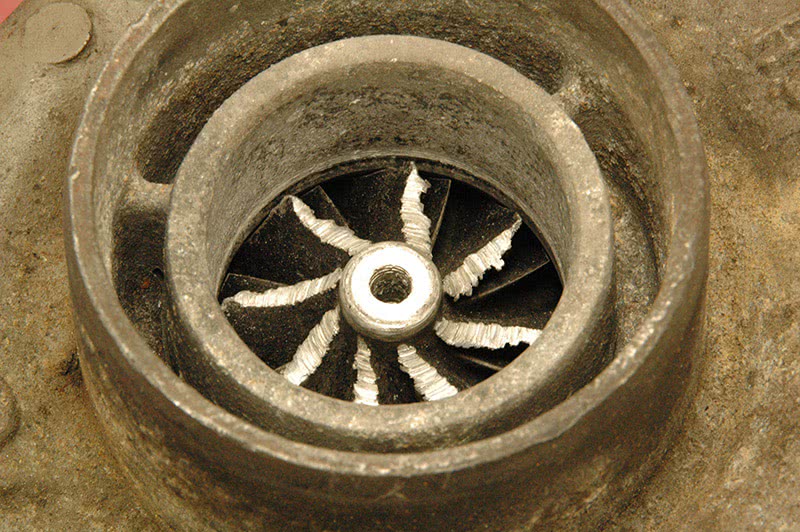
So, tell me what happens when the nut from the wheel comes off and gets sucked up into the compressor wheel? On car machining!
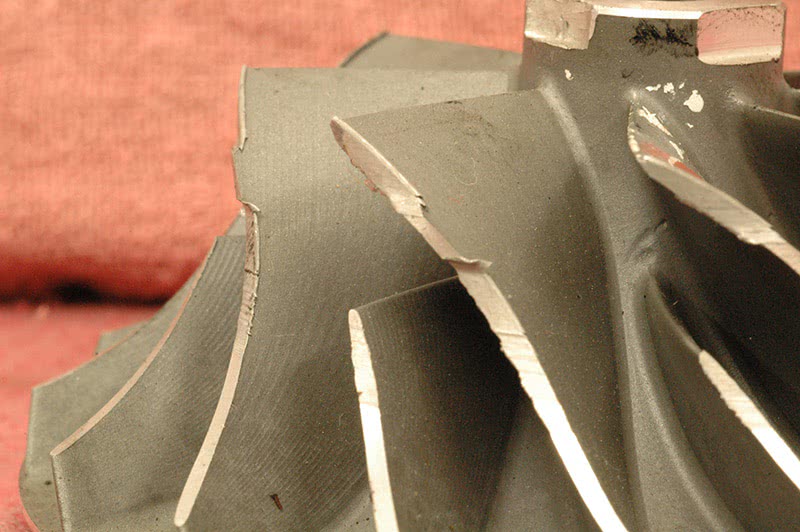
It doesn’t take a lot to trim off the ends of the blades. Even opening up the relationship between wheel and housing a few thousands will dramatically change the pump efficiency.
The second most common failure is foreign object damage (or FOD.) Make sure that during routine service all shop towels, nuts, bolts and wrenches are accounted for prior to startup. Foreign objects may be introduced by others, may fall off the turbo itself – like the nut holding the compressor wheel on the shaft – or in the case of a severely restricted air filter they may come from the inlet system. A restricted air filter could collapse and shred and become the source of all kinds of debris in the intake tract, and anything that touches either wheel guarantees instant shrapnel. There is no forgiveness if something is ingested into a wheel spinning at 50,000-125,000 rpm. If you have a FOD failure, you’ll need to clean the inlet and charge air cooler to prevent a repeat. If there’s any question about whether the charge air cooler got clean, replace it. On diesel engines, remember that whatever you used to clean the charge air cooler cannot be combustible unless you’re willing to risk a runaway engine.
Low-power concerns are often assigned to the turbocharger immediately, but that’s not always a good idea. First of all, see if there’s a lot of detonation sensor activity. On late-model turbocharged vehicles, not only will timing be retarded, but boost may be shut off or limited. I’d certainly put a pressure gauge on the intake side, but don’t forget to look at overheating, timing belt/cam timing issues, restricted exhaust systems, fuel pressure and volume and base timing, if adjustable. Don’t step over the obvious to get to the obscure. Once the basics are covered, check waste gate operation. I don’t have a dedicated tester for waste gates, but I do have a radiator pressure tester that I’ve adapted to check the pressure at which the waste gate starts to open. If that’s good, and you’re still not making boost, then you may find yourself pulling the turbo off to examine the wheels and shaft, which is not always a pleasant job.
Intercooled RegalWhen we were putting this story together, we came across a review we did back in 1987 of the Buick Regal Grand National 3.8L V6 (“Last of the Brutal Buicksâ€), the first turbocharged car that had ever really impressed us. On a cool day with good gas and sticky tires, it could turn in the high 13s, yet we got 27 mpg on the highway. Part of that excellent performance was due to an intercooler, the operation of which we explained as follows: ChillerThe addition of an air‑to‑air intercooler really pumped up this powerplant . . . A turbocharger, of course, compresses the intake stream, and that raises the temperature of the air. Add to this the heat radiated into it from all that warm metal, and you get a very steamy charge entering the cylinders, which tends to cause detonation. So, boost and timing have to be kept down considerably below their optimum levels. Enter the intercooler ‑‑ actually just a radiator for air (this one flows 350 cfm). This substantially lowers the temperature of the intake stream, increasing its density while reducing the danger of pinging. Ergo, boost pressure can be increased (up to 13‑14 psi can be tolerated), and the knock sensor‑controlled electronic spark advance (ESA), which operates within a 30‑degree range, allows plenty of ignition lead. The 12 lb. intercooler, by the way, is mounted low behind the radiator and has a continual flow of air drawn over its fins by a little plastic fan on the crank pulley. -Bob Freudenberger |
If you have to pull the turbo, now’s the time to check for oil in the intake manifold after the turbo, and the exhaust system ahead of the turbine and after. Even if you don’t have oil consumption complaints, remember that most people don’t check their oil and that catalytic converters may “eat†the oil smoke. Some turbos use a mechanical oil seal, some use a labyrinth seal and others rely on the high shaft speed combined with dams and diverters to sling the oil away from the area where the shaft passes through to the wheel. In most cases, oil consumption will be the result of shaft and bearing damage, which should also show up as rub marks on wheels and housings. If you find a compressor or turbine wheel coked or carboned up, it’s okay to clean it, but never with any kind of metal object, including a wire brush. The slightest scoring on the wheel will create a stress riser that will lead to a burst wheel. Soft bristled brushes and solvent only, please.
Once removed, examine the compressor wheel, turbine wheel and their respective housings for signs of damage or rubbing. Using a bright light, take a careful look at the compressor wheel. It should not have a sandblasted or “softened edges†appearance. If it does, it may have been damaged by running without an air filter. Turn the turbo by hand. It should spin freely with no scraping or rubbing. Next, push in on one of the wheels and turn it by hand. Again, there should be no rubbing. Finally, push in on the other wheel and turn it by hand and check for rubbing. Any failure that changes the shape of the wheel or the contour bore renders the turbo useless.
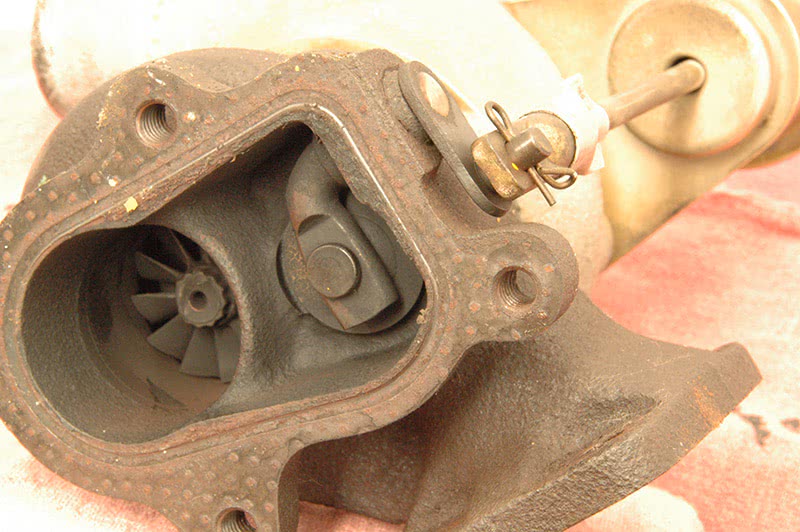
It’s pretty obvious what we’re doing here. If you open the gate, the exhaust gases bypass the turbine wheel, slowing shaft speed.
One last failure to mention: overboost. If there is a waste gate or VNT system failure, you could end up with more intake pressure than the engine was designed to handle. In many cases, overboost is the result of an overzealous owner bolting on power-up parts to gain that extra edge when he and his buddies are out drag racing their three-quarter ton pickups in the country (Hey! I’m a Hoosier, remember? I never said I was sophisticated!) Okay, here’s the story. I won’t say who was involved in this, but I have intimate knowledge of a certain middle-aged fellow who once owned a GMC Syclone turbocharged pickup truck. Said middle-aged crazy individual expressed a need for more speed, and mysteriously an extra “tee†appeared in the wastegate line and said line was terminated with a carburetor jet as a calibrated air leak. Seems that the computer control system was smart enough to shut the fuel off in the event of gross overboost (and you haven’t experienced something lying down hard until you hit fuel shut-off on a turbocharged engine that’s building boost like an Atlas 5 launch vehicle – you’ll leave teeth marks in the steering wheel), but not smart enough to detect, say, 2.5-3.0 psi of extra intake pressure.
After a good many fun Fridays nights laying waste to members of the local street-racing crowd, the truck appeared one day with a rather annoying ticking sound going on in the engine. On further investigation, it was determined that the noise was low, and seemed to be at crankshaft cadence. On teardown, we discovered that one connecting rod was twisted about 8-10 degrees, and shortened just enough for the pin boss to hit the counterweight of the crankshaft as the piston swung through bottom dead center. Now THAT is cutting it pretty close! Moral of the story? If you get complaints of sudden violent shut down, or if you see overboost occurring during your diagnosis, remember there may be some other clown like that (moi?) out there trying to get that extra little edge by modifying the boost map.
Finding replacements
Turbochargers aren’t really that complicated. For the most part, they are no longer field-serviceable, and repairs are confined to replacement AND making sure that the root cause of failure is identified – nothing is worse than calling your supplier with a “defective part†only to find that the swarf from the last failure clobbered your new unit. In my case, I’d see our friends at Fort Wayne Diesel for remanufactured replacement turbos (and they have other locations; check the website below), but Googling “remanufactured turbocharger†brought up dozens of potential suppliers. Depending on the application and mileage, having a good reman supplier could save you and your customers a lot of time and money. The majority of remanufactured units out there are probably going to have a new center housing rotating assembly with used compressor and turbine housings around it, so service life should be good. Keep it oiled, keep it cooled, and keep debris out and you and everybody will be happy.
Special thanks to Pat Kiel of Fort Wayne Diesel (part of Diesel Injection Service Company – www.dieselusa.com/) for several hours of help. Pat donated three boxes of parts and pieces, new and used for my use over a weekend to get this story done.
I would also like to thank an extraordinarily professional group of people at Garrett Turbo (
www.turbobygarrett.comEdit: garrettmotion.com), including Kyle Snyder and Craig Gibbs for sending us photos and answering some very technical questions on short notice. Check out their website for more technical information about turbocharging. If these guys don’t know it, it isn’t worth knowing!
0 Comments