For years, Mercedes-Benz chose not to compete at the low end of the luxury vehicle price range. Then the company shocked the world with the introduction of its first ever FWD sedan, the 2014 CLA, at a price point just under $30,000.
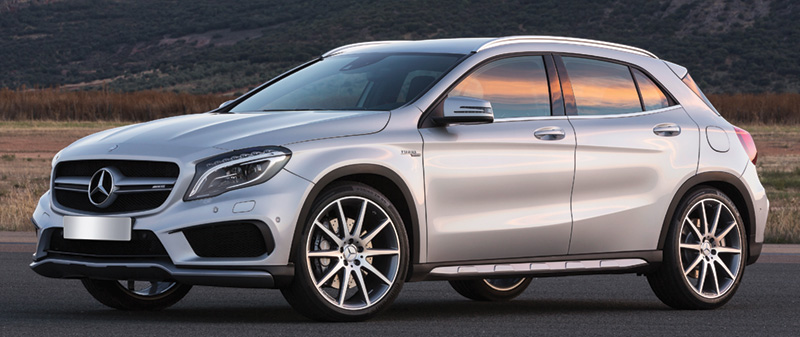
The 2015 GLA-Class includes a souped-up AMG version that turns the small crossover into a wolf in sheep’s clothing.
Mercedes-Benz engineers gave the CLA a fun-to-drive turbocharged four cylinder that delivers 208 hp and 258 ft. lbs. of torque, while offering 26 city/38 highway mpg. Add all-wheel drive, stunningly beautiful flowing body lines and an aggressive stance, and the CLA is winning new converts among upwardly-mobile young adults, a market segment that can move up to bigger Mercedes-Benz models as their careers blossom.
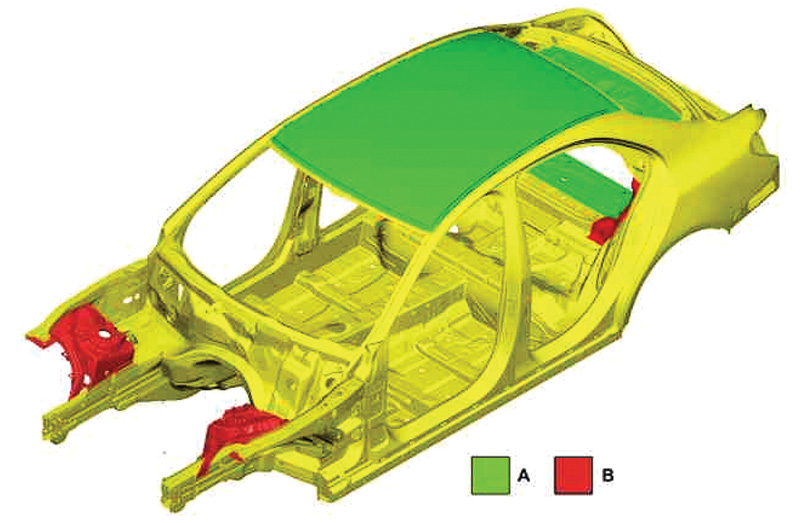
On the 2015 C-Class, the strut tower mounting bracket shown in red is cast aluminum. The roof and rear floor panels are stamped aluminum.
More Class
Mercedes-Benz is following its successful introduction of the CLA with two additional dramatic model changes. First, the company has upped the ante on the venerable C-Class, giving the 2015 line more power, a slightly larger wheelbase, and sexy styling borrowed from its upper-crust big brother, the S-Class.
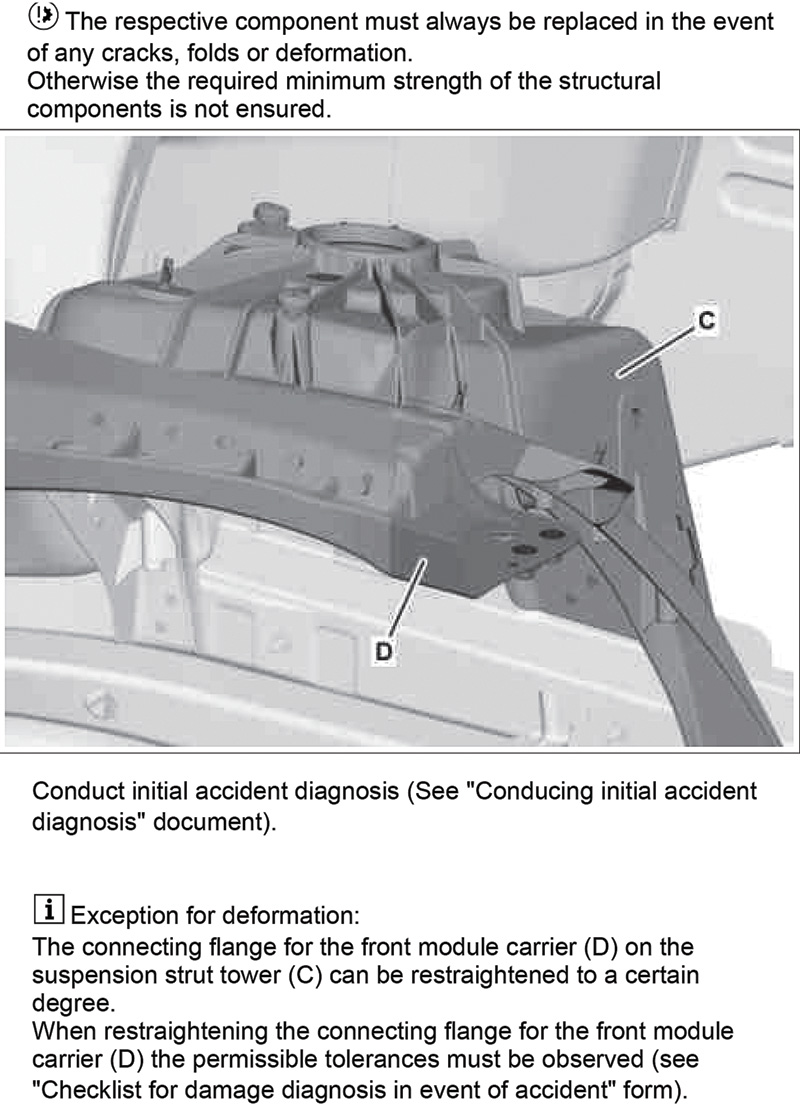
The connecting flange for the front module carrier (D) on the suspension strut tower (C) can be straightened only if the deviation is vertical, i.e., higher or lower than specified, and only if it is off by a minor amount. If the deviation from the measuring point is greater than 10 mm, the suspension strut tower component must be replaced rather than straightened (see “Checklist for damage diagnosis in the event of an accident†in WIS for further details).
Also drawn from the S-Class is a book-length list of safety and performance-enhancing high-tech features. A high percentage of these were popular options with many C-Class purchasers of previous years. Mercedes-Benz wisely made significant portions of the technology standard instead of optional, helping to ease prospects into the higher price of the new 2015 C-Class.
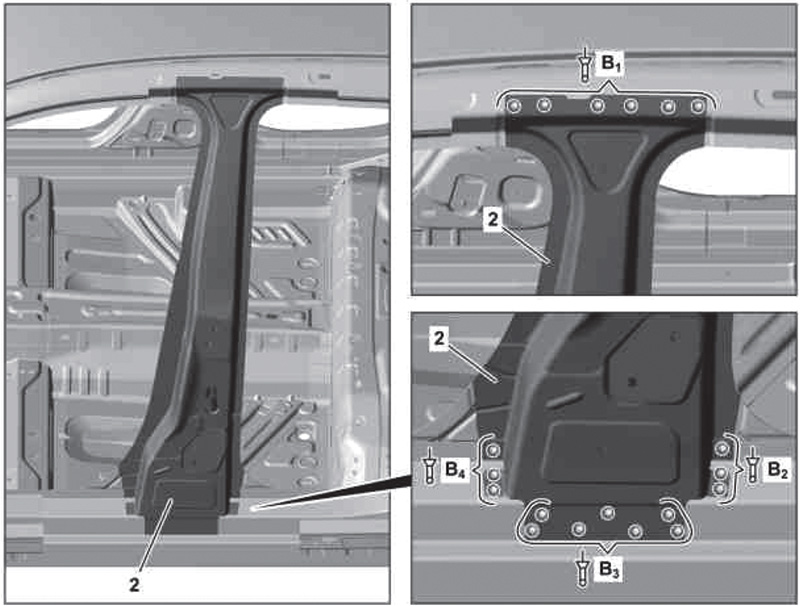
On the GLA 250, the B-Pillar reinforcement is made of Ultra-High-Strength Steel. To replace, fit the new B-Pillar reinforcement (2) in place, drill 6.7 mm rivet holes at areas B1, B2, B3, and B4. Remove the B-Pillar reinforcement, deburr rivet holes on B-Pillar reinforcement (2) on both sides. Remove drilling shavings with wet/dry vacuum, then coat the inside of the riveted joints with zinc dust paint.
Second, Mercedes-Benz introduced the 2015 GLA 250, its first in a line of compact SUV models. Based on the front-drive CLA platform, the GLA 250 features the same turbocharged 208 hp four-cylinder engine, seven-speed dual-clutch automatic transmission, and all-wheel drive, and is also available in a fire-breathing GLA 45 AMG version.
The different vehicle families give Mercedes-Benz three lines with list prices under $50,000, starting with the CLA under $30,000, the GLA starting under $35,000, and the C-Class starting at $39,000 to $49,000, depending on the specific model.
So no matter what market segment your facility services most often, you will see more Mercedes-Benz vehicles to repair in the future. And as collisions don’t wait for vehicles to age, it will be sooner rather than later.
More Aluminum and Ultra High Strength Steel
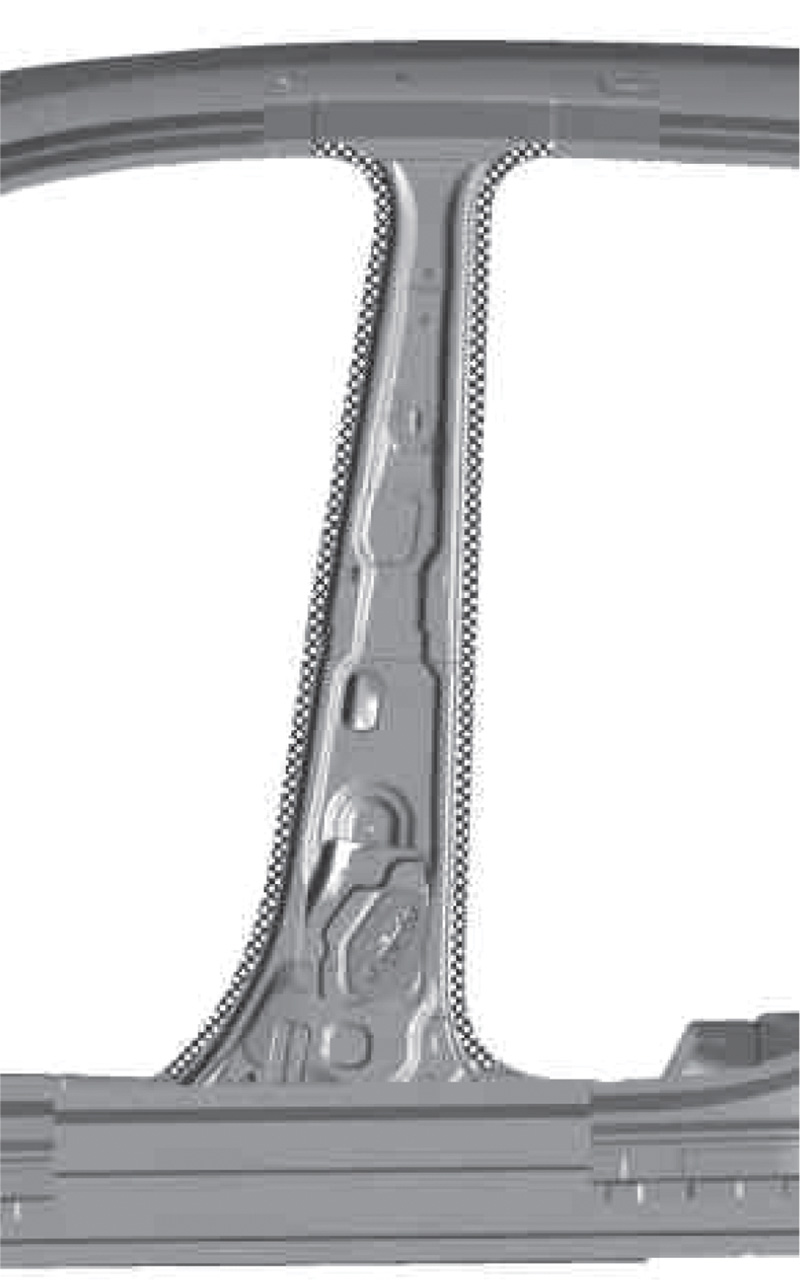
Apply two-component adhesive to the body in the crosshatched areas. Follow adhesive manufacturer’s instructions for pretreatment of bonding surfaces, and adhesive curing time recommendation.
Both the 2015 C-Class and GLA-Class use aluminum and ultra-high-strength steel (UHSS) extensively. The C-Class features aluminum hood, roof, trunk lid, door, and rear floor panels. It also includes aluminum strut mounting brackets, front crumple zone crash boxes, and rear longitudinal and cross members.
In the GLA, the hood, wheel carriers and upper and lower control arms are aluminum. The front crumple zone includes aluminum crash boxes that are bolted to the front side members, and aluminum struts to connect the subframe to the aluminum radiator mount.
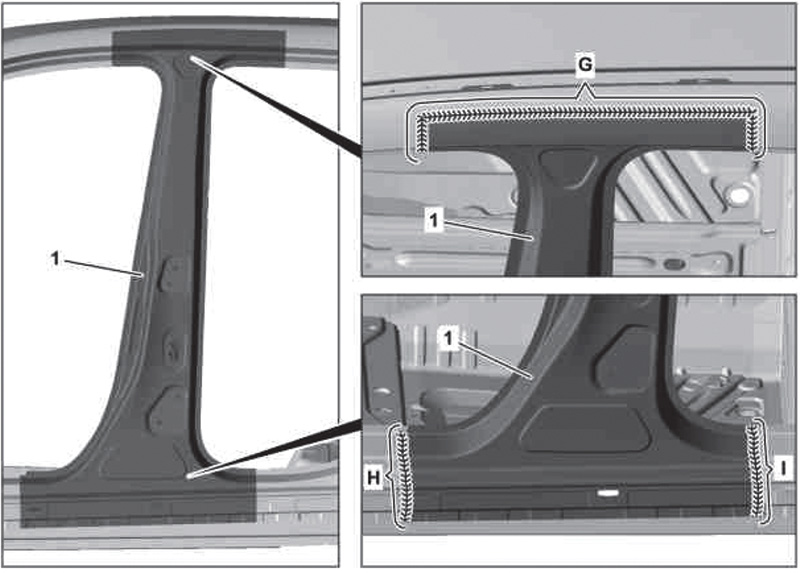
After assembling all B-Pillar components, inert gas weld in areas G, H and I on the outer B-Pillar, allowing each weld to cool before starting the next area. Grind the welds down flat. Solder surfaces in areas G, H, and I with body solder and smooth over.
Many of these components are extruded or cast aluminum, and must be replaced rather than straightened. Even the stamped aluminum body panels can be pulled only if they are less than a few millimeters off of the factory measurements (see sidebar for aluminum repair tips).
Ultra-high-strength steel, a group of steel products that offer a tensile strength greater than 700 MPa, include boron, martensitic (MS), and press-hardened steel (PHS). UHSS is found throughout both the C-Class and GLA-Class models. This includes the UHSS pillar, firewall crossmember, and other substructure components.
There is a very small allowance for repair to some aluminum components. What is/is not allowed and how much is documented in WIS (see sidebar for UHSS repair tips). As a general rule, there is NO recovery pull allowed on aluminum structural parts. There are a few minor exceptions to this and they are stated in WIS as pertains to specific vehicles.
For both aluminum and Ultra-High-Strength Steel, if there are any cracks in the structural component or body panel, the component must be replaced rather than repaired.
HSS can be MaG welded, but once we reach the strength of UHSS (hot-reformed), or what’s commonly called boron steel, we cannot MaG weld. It must be resistance welded and/or riveted – usually in conjunction with structural adhesive.
Easier done than said
Don’t let the need to learn new procedures for aluminum and UHSS collision repair intimidate you. It may sound like a lot when you hear how welding is no longer appropriate, but it boils down to getting three things: application-specific repair information, the proper tools, and a little practice to familiarize yourself with working aluminum alloys and high strength steel.
Mercedes-Benz Workshop Information System (WIS)
The Mercedes-Benz Workshop Information System (WIS) provides step-by-step instructions for specific repair or replacement of collision-damaged aluminum and UHSS components. WIS also offers brief, real-world “how-to“ guidelines that introduce you to cold-straightening aluminum, controlling heat application, adhesive bonding and riveting techniques, and other new restoration and component joining procedures, without a lot of fancy words or heavy technical theory.Â
Â
Aluminum Repair TipsAluminum responds more negatively than steel to heat, to pressure from hammering, and to straightening. For example, holding a flame pointing at a 90° angle straight down onto an aluminum panel or flange can punch a hole through the metal in less than a minute. Follow the Mercedes-Benz guidelines on how much heat, hammer work, and straightening a given aluminum component can accept.
|
 |
Working with UHSSUse of excessive heat, extensive straightening, or improper tools can damage Ultra-High-Strength Steel.
|
 |
Riveting NowAdhesive bonding combined with riveting offers significant advantages over metal inert gas (MIG) welding. Connections are made cold, so there is no heat to cause deformation of joined parts. The adhesive provides a sealed connection over more surface area, making the joint less vulnerable to corrosion after the repair. Together, adhesive bonding and riveting create a stronger, more durable connection than MIG welding.
|
Â
0 Comments