While tracking down the source of bad vibes may not make you a lot of money, it sure can make you a hero to your customers.
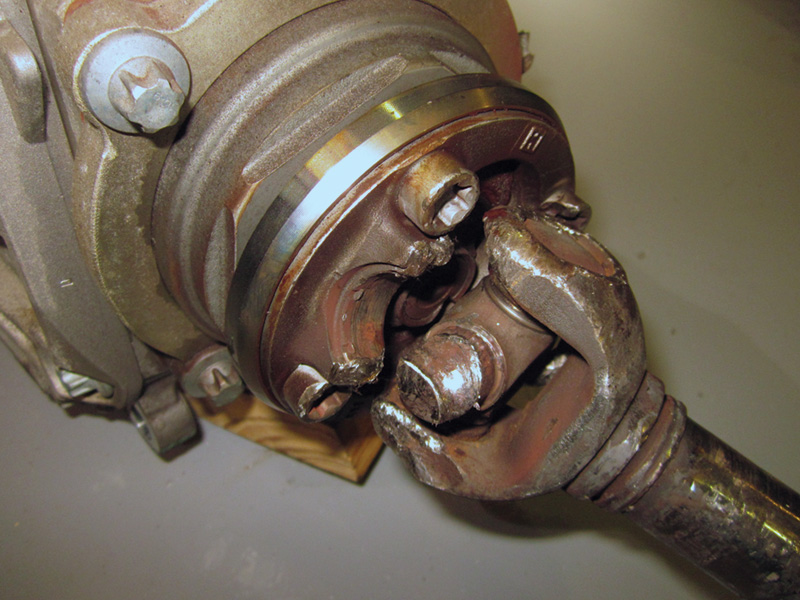
This is the front driveshaft and differential of a 2007 S550 w221 S-Class. This car had a vibration that the owner kept ignoring until the front universal joint finally gave out altogether causing extensive drivetrain damage.
Next to squeaks and rattles, vibration can be one of the most difficult vehicle complaints to diagnose. Driveline vibration that only presents itself at a certain speed or under a given load is a formidable foe because of the inability to reproduce the condition in a normal shop setting. There are many factors that can upset driveline balance and even the most seasoned technician can struggle with tracking down this type of problem. Often time-consuming and not a significant source of revenue, driveline vibration diagnosis can be made less stressful by exploring the subject until you reach a full understanding of the dynamics involved so that your next encounter with this situation will work out smoothly. Pleasing the customer is the main benefit you’ll get from this, and that’s paramount to your reputation.
Straight Talk
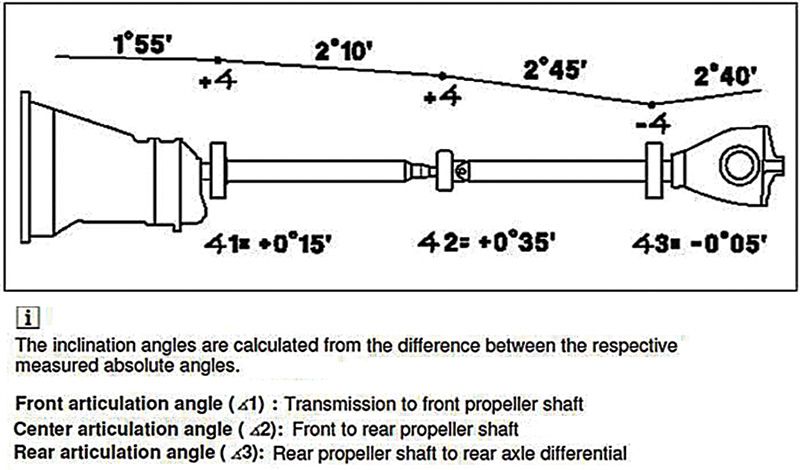
This WIS diagram shows where to take measurements for calculating the actual working angle of the shaft.
When dealing with driveline components, things are not always straightforward; getting and keeping parts to work in harmony is a balancing act. Luckily for us independent service providers, Mercedes-Benz has done an exceptional job engineering and building a remarkable, mostly problem-free driveline. That said, the driveline is not maintenance-free — there are components that need to be inspected for damage during routine maintenance and replaced when they have reached the end of their service life.
When we say driveline, what exactly do we mean? The generally-accepted thought is that it comprises the driven components from the output shaft of the transmission to the drive wheels. This would include the propeller shaft and its connecting joints, differential, axles, hubs, and wheels. Mercedes-Benz does not use a single driveline system to transmit power. Instead, a combination of different technologies is employed depending on the application. Each vehicle line has its own specifically-engineered system, and because of these differences driveline vibrations usually do not all share the same characteristics. Getting to know each component and its operation goes a long way in helping to diagnose vibrations.
Pieces of the Puzzle
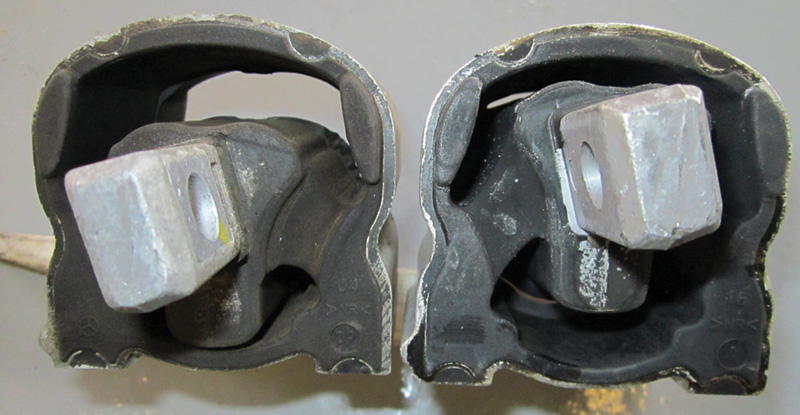
A shot of Mercedes Transmission mounts side by side. The transmission mount on the left is old and collapsed, which caused a driveshaft vibration under acceleration. The right one is the new transmission mount to be installed.
Mercedes-Benz uses the most common type of drive or propeller shaft set-up, which is known as a Hotchkiss drive (except for the new CLA and GLA FWDs). A Hotchkiss design may employ one of several different flexible-mounting joints on each end, as opposed to the torque tube design that’s rigidly fixed between the transmission and differential. On the majority of passenger vehicles built by Mercedes-Benz, a two-piece rear drive shaft is used (with 4Matic, a single shaft routes power to the front drive). Using a two-piece shaft for the rear drive has a number of advantages:
- The same distance can be spanned as with a single shaft, but it can be done with smaller diameter tubing.
- It saves weight, meaning there’s less rotating mass, which translates into smoother, quieter, and more efficient operation.
- The two-shaft design allows for a center-mounted slip joint. This allows the shaft to lengthen and shorten with changes in chassis flexing, drive train, and suspension movement. By center-mounting the slip joint instead of using a splined yoke at the transmission output shaft, a common fluid leak point is eliminated.
- Added Safety; In the event of severe collisions, these shafts can collapse into themselves. This lessens the chance of intrusion into the cabin, or dropping onto the pavement where it can dig in and act as a catapult.
- With the smaller diameter, there’s less need for a tunnel inside the vehicle.
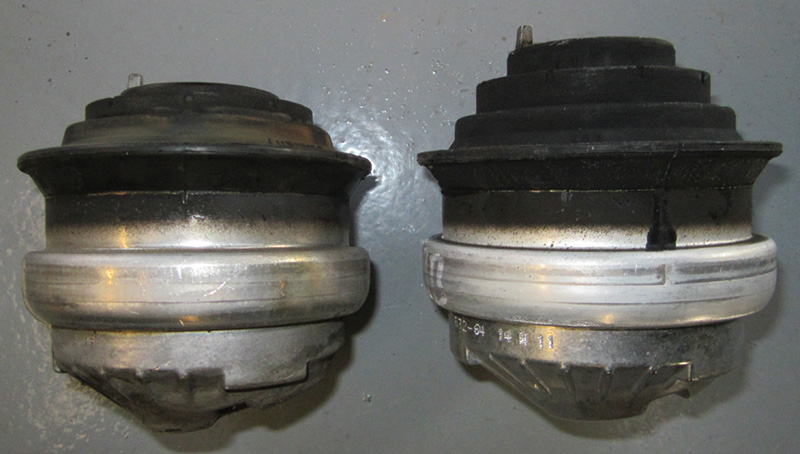
The worn and broken engine mount on the left was causing drive train vibration at all speeds. Notice the height difference to the new one on the right. Installing new mounts restored the vehicle’s driveline angles back to normal.
The dominant form of drive shaft coupling used by Mercedes-Benz is a flexible “Giubo.†More commonly know as “flex discs,†these are used in various sizes on many European passenger cars. Made of nylon-reinforced flexible rubber, these discs are known for their ability to reduce vibration, compensate for small amounts of misalignment, operate quietly, and live a long service life with little to no maintenance.
On other applications, Mercedes-Benz uses a combination of mechanical flexible joints. These include the Cardan universal joint (U-joint), double Cardan joint, and Rzeppa-style constant velocity joint (CV). Each has its own advantages, the most notable of which being high strength and the ability to operate at greater angles or degrees of misalignment.
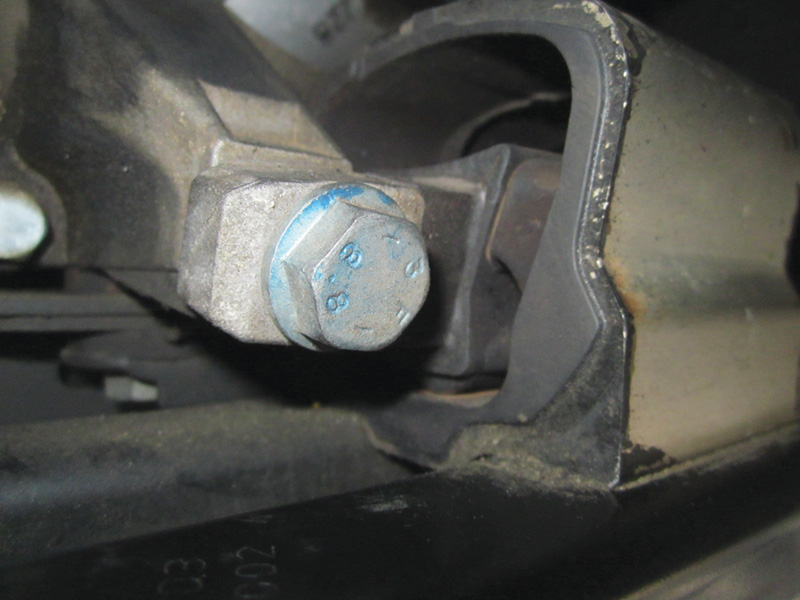
A collapsed transmission mount still in the car. This 2007 E320 had driveline vibration above 40 mph.
Virtually anything that moves in a vehicle can produce an unwanted vibration. The upside to this is that most problems can be broken into two groups: stationary vehicle vibration and moving vehicle vibration. The downside is that there is no magic way to easily diagnose either type. Like most problems that are brought into the shop, asking the right questions may possibly narrow the complaint down more quickly. These questions may include, but are not limited to:
- When did the vibration start?
- Is this a constant vibration, or only at certain speeds? At what rpm and gear does the fault occur?
- Is the vibration more pronounced during hot or cold operation?
- Has the vehicle recently been serviced?
- Ask yourself if the vehicle was in for a repair that you performed and now there is a vibration? If this is the case, be honest (we’ve all done it). You probably broke this car and need to retrace your steps.
- Was the vehicle in any recent collisions?
- Has anyone else preformed any repairs recently? (body shop, tire and lube shop, a family member who supposedly knows about cars, and so on.)
- Specifics about the vibration speed, direction, and severity.
- Are there any other symptoms associated with the vibration, such as malfunction warnings, squeaks, rattles, or odors?
- After a test drive and complaint verification, the detective work continues. A thorough visual inspection to look for obvious signs of damage or worn components is a must. If no fault is apparent, a search of Mercedes-Benz technical service bulletins related to your problem is warranted. This may already be a known problem with a documented fix. Next is to weigh what type of vibration — do you have a vibration when driving in a straight line or a vibration associated with turning? This clue can also help you narrow the search for a cause.
Train of Thought
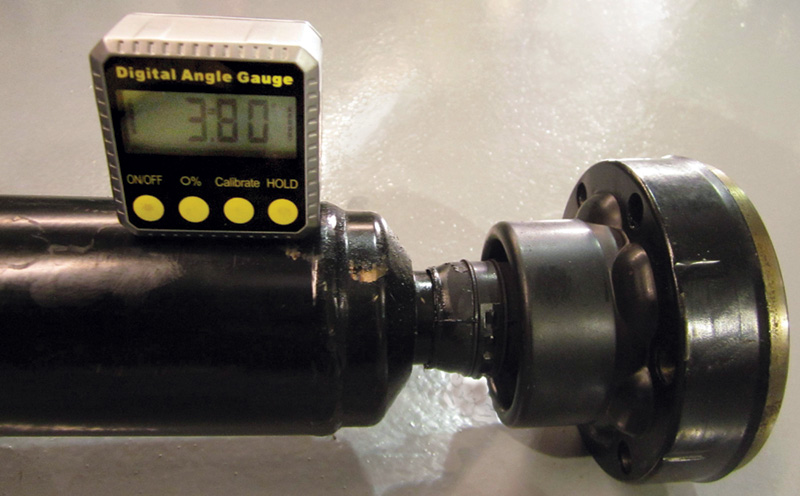
A digital angle gauge is an accurate means of measuring driveshaft slope so that you can calculate the working angles.
Mercedes-Benz vehicles are known for their smooth ride; it’s one of the many reasons they stand out from the crowd in the luxury market. Getting that cloud-like ride back as quickly as possible when it goes awry requires some serious thought about the driveline, drive train, and how one part can affect another. Over the years, we have seen many instances where people become lazy and say, “Let’s throw parts at it till it’s fixed.â€
We know first hand how headache-inducing these vibrations can be. Let’s break down some of the common parts, mistakes, and misconceptions so that in the event that a guess has to be made, at least it can be an educated one.Â
- First off, let’s not forget the basics: tire balance, condition, rim damage, loose lug bolts, and wheel run-out (including lateral and horizontal). These are all possibilities that can generate mild to severe vibration, usually very distinctive to one corner or side of the chassis. Tire/wheel problems have a tendency to start light and gradually get worse as rotational speed increases. A suspect wheel should be checked for proper tire inflation, a missing weight, tire and rim damage, tire age, and wear pattern.Â
- Driveshafts are balanced when manufactured, and just like anything else that has mass and spins, balance is critical to avoiding vibration. It’s extremely rare for the driveshaft to become unbalanced. Unless it’s been damaged by impact or is missing the welded-on weight, shaft balance is an unlikely suspect. A balance problem tends to start light and get progressively worse as vehicle speed increases. The most common cause of shaft vibration is misalignment. This type of vibration tends to show up generally over 30 mph and decreases as load decreases. Shafts are engineered to work within specific angles, meaning the transition between the drive and driven shaft is not strictly linear. The coupling from the transmission or transfer case output flange to the driveshaft and at the differential flange has to be flexible to account for this difference. Misalignment occurs when the working angles at each end of the driveshafts are not equal. Why are equal angles so important? Because of the vibration-canceling characteristics. When power is transmitted at an angle, the natural tendency is for the driven shaft to speed up or slow down. The best example we can think of is when you use a flex joint to drive a socket. When turning the joint, it’s easy (speeds up), then gets tight (slows down), and the steeper the angle the more pronounced the change. If there is misalignment, end speed will be different; this causes vibration. This phenomenon, depending on the severity of the misalignment, will produce an oscillation twice per revolution, giving you an almost come-and-go low-frequency drumming vibration. Since a picture is worth a thousand words, an online search shows several videos of drive shaft trainers that will shed light on how shaft alignment affects acceleration/deceleration of rotation.Â
-
The key to diagnosing a misalignment is ascertaining the working angle. For this you need a digital spirit level, protractor, or angle gauge. Given the precision built into today’s Mercedes-Benz vehicles, the accuracy of digital over analog is vastly superior. Measuring the centerline slope on both sides of a joint and subtracting the difference between the two gives you the actual angle for the joint. This needs to be done for every coupling in the line. Again, if you’re like us and learn by seeing, we would urge you to take advantage of the many online sources that show this process in great detail.  Â
- Mounts play a crucial role in driveline harmony. Engine, transmission, shaft center support, and differential mounts in addition to absorbing vibration, also maintain driveline alignment. If any of these are worn to the point of collapse, or are improperly installed, drive vibration may result. The most common culprit on today’s vehicles (and easiest to repair) is the transmission mount.
- Joint health is another consideration. U-joints and Rzeppa joints need to be inspected for wear, play, and binding. Some telltale signs of problems are rust rings around the U-joint bearing caps, or a torn boot cover on the Rzeppa joint. History tells us that these joints can cause significant vibration, but usually have a noise complaint associated with them. Unfortunately, a true inspection of these types of joints requires removal. Luckily, flex discs on many models can be easily inspected on the car. Excessive dry cracks or improper installation are the most common disc issues. And, yes, you can install a disc wrong! If you look close enough, you will see that most discs are manufactured with thin and thick layers between the mounting points. The disc must be oriented so that it’s driven from thick to thick and not thick to thin. Doing the latter could lead to a disc that will deform into producing an elliptical rotation, and drastically shorten part life. Remember, as with all parts, there is a torque pattern and specification.Â
- Vibration associated with turning is most commonly found on vehicles with the 4Matic option, and can be traced to a transfer case problem — often a severely neglected component. Because of its being attached to the transmission, it’s often forgotten that it has its own fluid. Hence the fluid never gets checked or changed until adverse symptoms appear.
- Half-axle shafts can also generate vibration and noise if damaged, and may need to be scrutinized. Half-axle problems can be especially difficult since the shafts employ different constant velocity joints on the inboard and outboard ends. This allows the axles to produce the same noises and vibration mentioned before. Therefore, all of the same techniques are used to determine the fault. Â Â
Tools of the trade
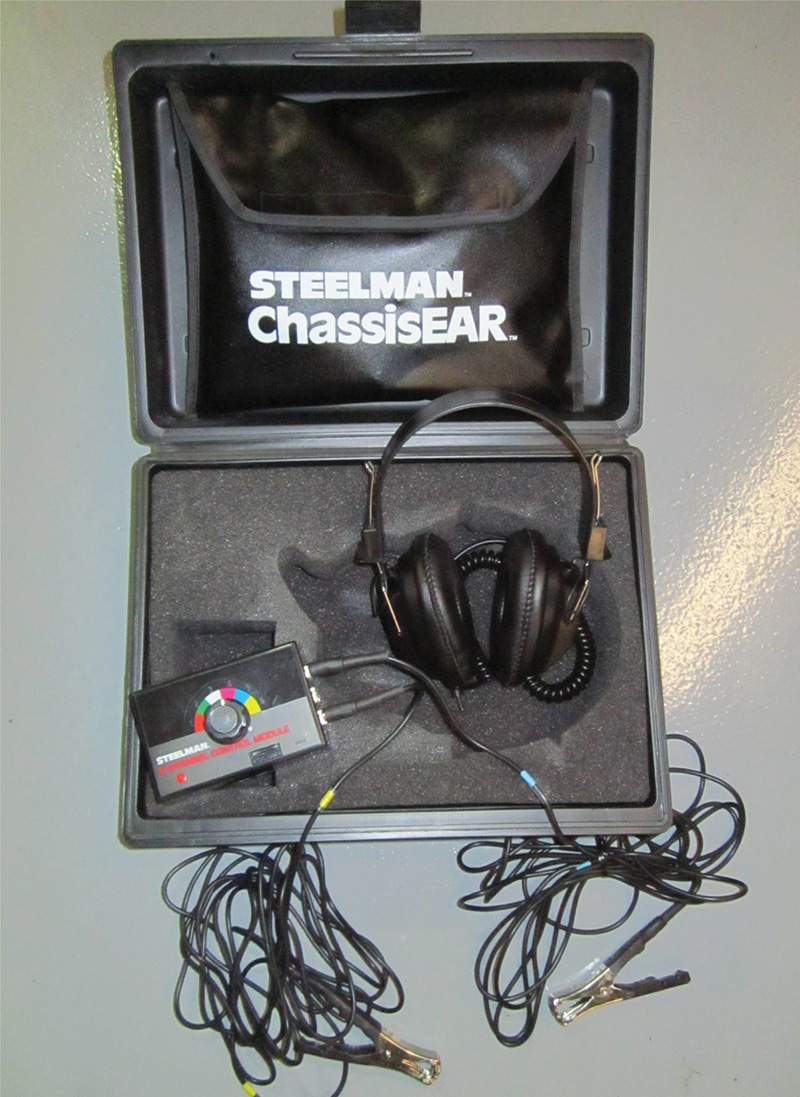
The Steelman ChassisEAR is becoming more and more popular in auto service. It’s designed to help track down noises, but is also useful on vibrations because of the harmonics emitted. This tool employs very sensitive microphones and is much less expensive than specialized vibration detection equipment.
There are some sophisticated tools on the market for detecting and analyzing vibration. Most are very expensive and cost-prohibitive for many ISPs (Independent Service Providers). After all, driveline vibration develops in Mercedes-Benz vehicles quite infrequently, so why make the investment? A good alterative, however, would be a listening tool. The ChassisEAR, manufactured by Steelman Company, is a tool that uses remote microphones to help trace noises. Since most vibrations produce a type of harmonic noise, use of these microphones can help you isolate a general location a vibration is originating from. In addition, the capability of tracking down squeaks and rattles makes purchasing this type of relatively inexpensive tool a good investment.
Quality Resource
Having previously discussed mechanical aspects, another tip is having your trusted local MBUSA parts supplier check the vehicle identification number to insure that the correct Mercedes-Benz original parts were and are being used. There is no substitute for the O.E.M part that was designed for the vehicle. Also, don’t be afraid to ask for help; your Mercedes-Benz parts counter is staffed with knowledgeable personnel. He or she deals with countless shops just like yours daily and may have insights into the part you suspect of being the culprit. It could be the case that it’s a commonly sold part, further validating your diagnosis. Or, maybe your part request is very unusual, suggesting that you should go back and rethink the problem.
We hope that getting your thoughts on this topic in motion will help make the next encounter you have with a driveline complaint smooth sailing.Â
0 Comments