MLS technology takes us from spongy to rigid, and from tenuous to permanent, but you have to live by the rules.
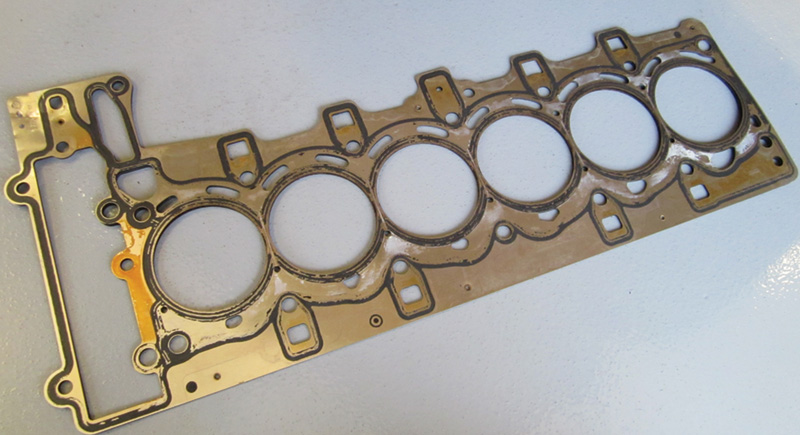
Here’s a used late-model MLS gasket. Note the loss of the thin sealant layer, which means these gaskets cannot be reused.
If you’ve been a technician for as long as the contributors to StarTuned have, you’ll believe us when we say we know how easy it is to get stuck in your old ways and assume that you can just keep doing things the way you have all along. In reality, that mentality could cost you big with today’s sophisticated engines.
The nature of our industry is that it’s always evolving. Sometimes the change is very noticeable, such as the move from carburetors to electronic fuel injection, but other times a change is barely acknowledged, if at all. In this case, we’ll take a peek at the often-overlooked head gasket. As simple as it may seem, alterations in gasket design have brought important changes to the way we deal with these parts. Long gone are the days when cylinder head gaskets needed a re-torque after about the first 1,000 miles of operation. And gone are the days of breaking out “ye olde†pneumatic-powered wire brush or abrasive pads to clean up block and head surfaces. Mercedes-Benz engines of today require a delicate touch.
Gaskets of the past were mainly of the composite type, meaning some combination of graphite, brass, copper, and asbestos on earlier versions. These gaskets were good for their time and did their job satisfactorily, although as they aged they were prone to oil and coolant leaks. Typically, these failures were not catastrophic, but they were still the main reason for head gasket replacement. Less common was a total failure: the dreaded “blown head gasket.†More times than not, this was the end result of severe overheating.
Extreme reliability
Stop and think: Since 1998 or so, have you, the independent Mercedes-Benz service provider, seen a head gasket failure that wasn’t caused by extenuating circumstances, such as an internal engine repair done improperly? We’re betting very few, if any at all. Why is that? Because in the late 1990s, Mercedes-Benz made the move from composite to multi-layer steel head gaskets (or, as they are commonly known, MLS gaskets). Just as their name suggests, MLS gaskets comprise multiple layers of thin steel. Depending on the application, there are typically three to five layers of stainless or alloy steel pre-coated with an elastomer sealant. Â
MLS technology has proven to be extremely reliable and far superior to composite gaskets for a number of reasons:
- Thinner profile – This allows for more accurate cylinder head-to-block tolerances resulting in a more precise combustion chamber size. The benefits being that Mercedes-Benz engineers are able to fine-tune the engine even more than they could in previous generations, producing more power, fuel efficiency, and smoother operation.
- Rigidity – A stiffer gasket provides a more uniform sealing surface and less movement between the castings.
- Steel construction – Metal-to-metal sealing takes advantage of a more consistent and uniform thermal expansion and contraction to promote a better seal. Also, the stainless or alloy composition resists corrosion.
- Multiple layers – This type of construction adds to the gasket’s ability to uniformly expand and contract during engine warm-up and cool-down. Thermal expansion is not linear (meaning only moving in one direction) in an internal combustion engine. Heat creates volume expansion (meaning expansion in all directions). Although movement is very minute, multiple layers are able to shift with the movement to maintain a cohesive seal.    Â
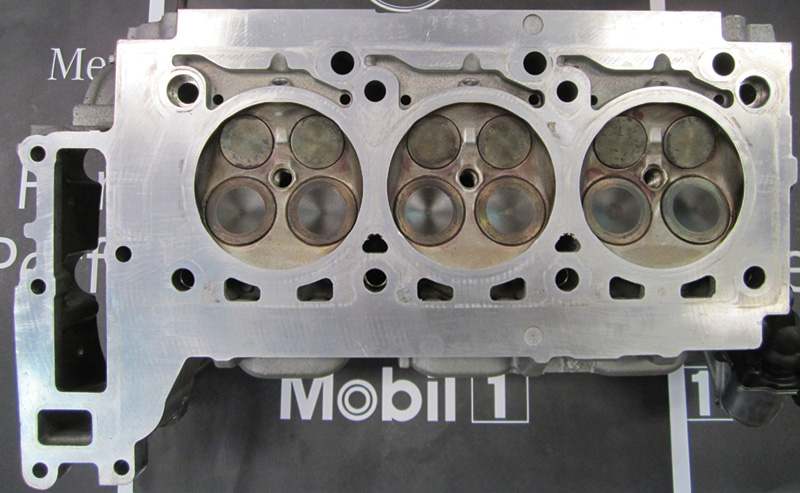
When cleaned and prepped for reinstallation, discolorations and trace impressions can still be seen from the previous gasket, as on this 272 engine. These are particles embedded in the pores of the aluminum. As long as they can be seen and not felt, they will not affect the new gasket’s seal.
The adoption of MLS gasket technology also set the stage for the latest evolution in Mercedes-Benz engines. Stronger gaskets have allowed for higher cylinder pressures with the additions of turbocharging and direct injection. Now being able to reliably handle the increased force, Mercedes-Benz engines are able to produce some of the most powerful and fuel-efficient engines the world has ever seen.
Working in tandemÂ
A gasket is only as consistent as the bolts that hold it in place. MLS gaskets could not perform as well as they do without torque-to-yield fasteners, or, as they are more commonly known, stretch bolts. Having been around since the 1980s, stretch bolts are seasoned veterans of the automotive industry. Developed primarily for economic reasons, the advent of stretch bolts eliminated the need for partial tear down to re-torque head gaskets after sale. They also reduced the number of torque steps needed to achieve specified tightness on the assembly line. This saves time and money for the consumer and manufacturer alike.
A stretch bolt’s benefit lies in its ability to be tightened beyond the elastic limit (yield point) into the metal’s plastic region. This produces a high uniform clamping force that’s superior to the harder, non-flexing head bolts of the past. Using this elastic property, these bolts are able to expand and contract with temperature and maintain a reliable clamp. Much the same as if you were to put a good stretch on a rubber band (not to the breaking point) and them let off just slightly. You have some “give,†but there’s still pressure, or an applied force. Another advantage of stretch bolts is the accuracy of the clamping force. Research has shown that with stretch bolts variations in clamping force are within + or – 10 % from one to the next, compared to the + or – 30% of non-stretch bolts. Such accuracy makes for much more consistent clamping force across the cylinder head. Combine these advantages with those of MLS gaskets mentioned above and you have a very reliable seal.Â
Prepping for perfection
Even though head gasket failure itself is not commonplace anymore, the need to remove a cylinder head for other repairs is still a possibility. Most techniques for disassembly and reassembly of a cylinder head-to-block still apply, but there are some important fundamental differences for installing MLS gaskets that need to be followed to ensure a successful repair.
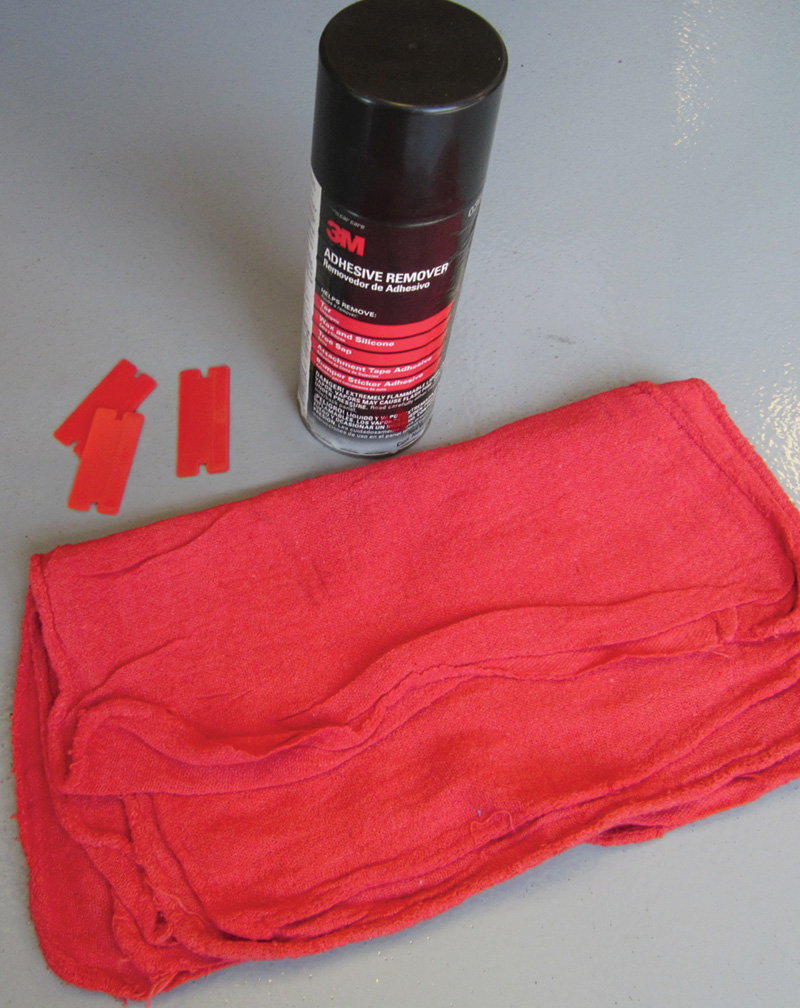
The tools now needed to prep cylinder block deck and head sealing surfaces for the installation of an MLS gasket.
Older composition gaskets were thicker and more flexible, so they could absorb or accommodate minor defects on sealing surfaces; therefore more aggressive (to a point) cleaning of the mating surfaces was permissable. MLS gaskets being solid with only a very thin coating of sealant, on the other hand, are far less forgiving and cannot conform to irregularities. Engine block decks and cylinder heads must be kept as damage-free as possible. To get technical about it, composite or soft-faced gaskets can generally seal surface roughness of 60RA to 90RA. RA refers to “Roughness Average.†Using a special meter that can detect the peaks and valleys of a surface finish, this is the measurement in microns — millionths of a meter. By comparison, a crankshaft journal usually has finish of about 10RA. MLS gaskets need a finish of 15 RA to 30 RA for optimum reliability. For this reason, extreme care must be taken during disassembly and reassembly preparation. Mercedes-Benz recommends using no metal-to-metal or abrasive friction for cleaning surfaces (i.e. scrapers, sanding discs, or any tool that could scratch). Instead, it is recommended that an aerosol adhesive remover such as products from 3M and a plastic blade be used for cleaning. Experience has shown that a soft brass brush with very light pressure could be used if needed — just be sure no bristles are left behind.
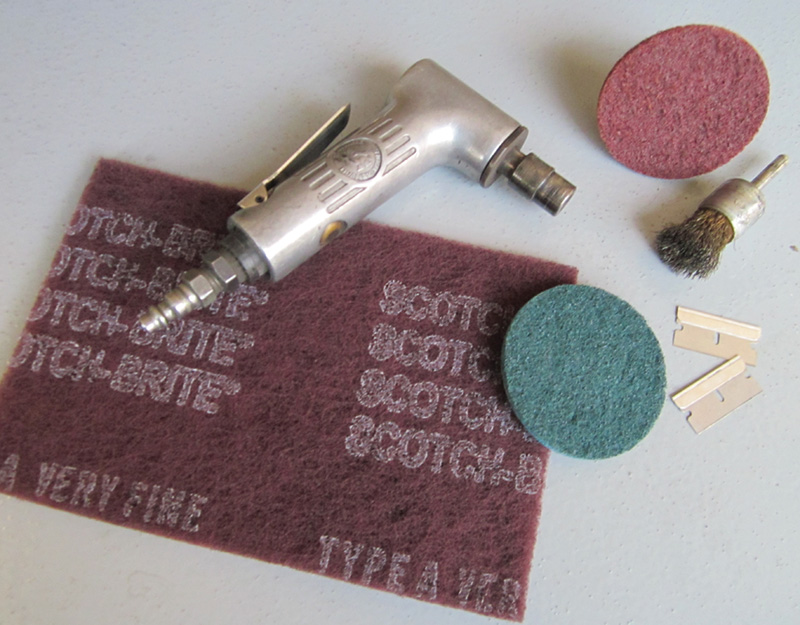
The tools we used to clean sealing surfaces on older engines are way too aggressive for today’s engines, and would quickly destroy any chance of proper sealing with an MLS gasket.
Just as on older engines, clean surfaces are a must — debris can compromise sealing. Bolt holes must also not be overlooked. Debris in the holes could cause a false torque, or liquid that may have spilled into the holes would cause the head bolt to hydro-lock resulting in stripped threads. Checking the cylinder head and block deck for warping with a quality straight edge is required whenever they are apart. It should go without saying, but we’ll mention it anyway, head gaskets cannot be reused. MLS gaskets have Load Control Embossments (LCE) that are designed to compress during the initial installation. Trying to reuse a gasket that has already been crushed will leak and possibly cause damage to the cylinder head and/or the engine block.
During reassembly no additional sealant is needed as the gaskets are pre-coated, unless directed otherwise by Mercedes-Benz work instructions (such as where the cylinder head meets the timing cover on some models). It is also recommended that a new set of head bolts be used during repair, even though stretch bolts may be re-used if within the measured limit. A few facts make us lean toward replacement.
Once the bolts are stretched, they stay stretched. Service limits normally only being 1 to 2 mm longer than a virgin bolt, there is still a risk of bottoming the bolt out in the block during reassembly.
Stretch bolts have a thin upper shank that allows them to elongate. Once stretched, the shank can become warped depending on stresses it may have been subject to during its initial use. Reusing a warped bolt could deform threads or give uneven clamping pressure at the bolt head if re-installed.
These bolts are responsible for keeping everything together. They’re given the task of containing 1,000 to 1,500 psi of combustion pressure every millisecond day in and day out. Given the risk, a new set of bolts can be looked at as cheap insurance. As always, make sure the bolt threads and those in the casting are clean to keep the bolt from binding when screwed in, thus preventing a false torque during the bolts’ initial pre-load.
Sweating the details
This brief overview is no substitute for following Mercedes-Benz’s official work instructions. Paying attention to the details is the best practice for producing a quality repair. The goal is to fix it right the first time; nobody wins when you have a comeback. Another important detail is making sure you have the correct parts to begin with. Verify you have the right gasket for the cylinder bore size, and correct bolt length. Double-checking could save you from a costly mistake. The best source for correct parts the first time is your local Mercedes-Benz parts professional who will not only ensure that you get the correct part, but also that it’s a quality part that was specifically engineered to keep the vehicle firing on all cylinders.Â
0 Comments