Mercedes-Benz fuel cell vehicles can refuel in less than half the time it takes to recharge the fastest-charging electric vehicle, and can travel twice as far on a single tankful of hydrogen as a pure electric can on its batteries.
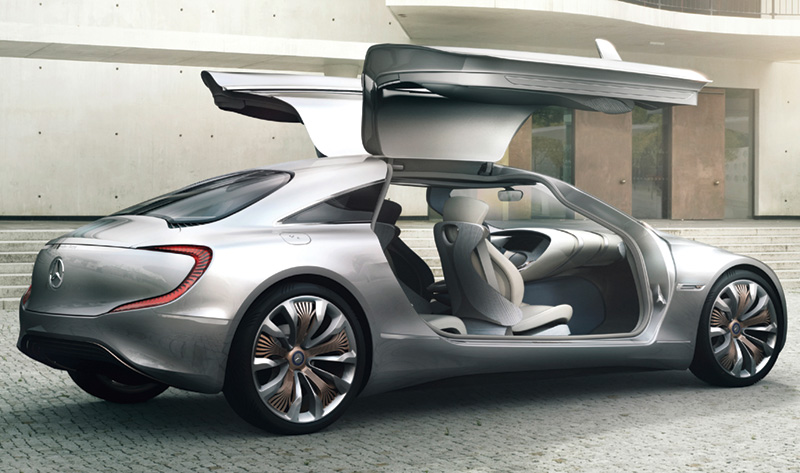
The Mercedes-Benz F 125! Research Vehicle incorporates fuel cell electric vehicle and a cornucopia of additional cutting-edge technologies to make a zero-emission, renewable fuel vehicle with the safety and comfort of a full-size sedan, yet the fuel economy of a much more lightly-constructed model. High-strength materials along with crash-responsive protective systems in the gull-wing doors allow for the elimination of B-pillars. It also allows widening of the doors for full access to all four seats.
Fuel cell electric vehicle (FCEV) technology is a green alternative to hybrid and battery electric vehicles (BEV). Like a BEV, a fuel cell vehicle has no on-board hydrocarbon combustion and no harmful greenhouse gas emissions. A Mercedes-Benz fuel cell vehicle uses hydrogen – a renewable resource – and can refuel in only slightly more time than it takes to fill a tank with gasoline, whereas even the fastest-charging electric vehicle will take at least an hour. Also, an FCEV can travel twice as far on a single tankful of hydrogen as a pure electric can on its batteries. Mercedes-Benz has field-proven fuel cell vehicles today, and engineers promise to push fuel cell technology over the next decade to deliver more benefits in models that are affordable and offer Mercedes-Benz quality, power, and comfort.
You should be learning how to diagnose and repair hybrid and/or pure electric vehicles. The knowledge will give you a leg up, as fuel cell and battery electric vehicle designs will likely be combined to increase the power and range of each technology.
In 1994, Mercedes-Benz introduced the world’s first fuel cell vehicle, built on the Mercedes-Benz 100 van chassis. The vehicle needed almost the entire van interior to house the fuel cell equipment and operating system. Twenty years and almost three million real-world miles driven later, the technology has evolved tremendously. It is field-proven and has magically been shrunk to fit under the hood (and floor) of a regular-size Mercedes-Benz B-class F-CELL crossover.
Field-proven
Mercedes-Benz has driven innovation in the development of a consumer-friendly vehicle based on renewable, zero-emission hydrogen fuel cell technology. Over the last two decades, the technology has increased in performance while the components became progressively smaller. In 2011, the company proved the practicality and robustness of its offering by driving the B-class F-CELL around the world in 125 days.
A fleet of 70 B-class F-CELL models in California has completed the automotive world’s equivalent of beta testing, and performed so well that after the test most became available to the public for lease as reliable previously-owned vehicles.
The Mercedes-Benz B-class F-CELL combines zero-emission hydrogen fuel cell technology with a high-torque electric motor. The electric motor offers an instant-on torque of 290 Newton meters and develops a peak output of 100 kilowatts, giving it power equal to that of a two-liter gasoline engine. A 700-bar (10,000 psi) hydrogen tank sandwiched into the floor gives the car an operating range of approximately 250 miles.
The B-class F-CELL delivers its quick-response power and hill-climbing torque with quiet confidence. Even at maximum power, the sound of the electric motor is barely audible.
Generating power on the fly
Fuel cell electric vehicles operate much like a battery electric vehicle, except that instead of a battery supplying electrical power to the motor, hydrogen does the job. Unlike a battery which must be charged from the electrical grid before it can be used, a fuel cell uses an electrochemical process to generate power on the fly.
The fuel cell consists of a negatively charged anode, a positively charged cathode, a catalyst and a selective membrane. Hydrogen is forced in at the anode, and oxygen is added on the cathode side. The catalyst on the anode side separates the hydrogen electrons (negative ions) from its protons (positive ions). The polymer electrolyte membrane allows the protons to pass through to the anode.
The electrons cannot pass through the membrane, and must take another route to the cathode. The electrical current created as the electrons travel their ‘bypass’ route to the cathode drives the electric motors, which are the load on the circuit.
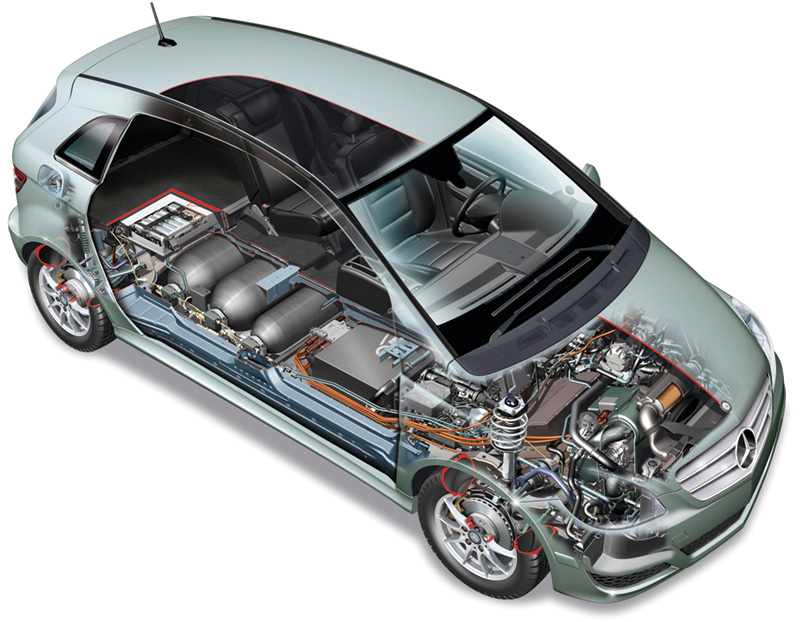
The 2011 Mercedes-Benz B-Class F-CELL locates the main drive components and hydrogen tanks in a sandwich floor under the passenger compartment.
An individual fuel cell is only about two millimeters thick, and generates no more than 1 volt of power. Several hundred cells must be combined in series – called a ‘stack’ – to generate up to 200 volts, enough to power a vehicle.
No hydrocarbon combustion occurs, so there are no harmful emissions created or released to the atmosphere. The only by-products beyond electrical energy are heat and water. When the protons and electrons reunite at the cathode, two atoms of hydrogen combine with one of oxygen and form H2O, which, due to the heat, is released from the exhaust primarily as pure water vapor.
The Mercedes-Benz fuel cell electric vehicle (FCEV), like battery electric vehicles (BEV), replaces the conventional internal combustion engine with electric motors.
When the driver accelerates, a compressor increases the air supply, and system valves respond by regulating the flow of hydrogen appropriately. As the amount of electrical current increases it supplies more power to the electric motors, increasing vehicle speed and performance. Instead of a transmission, four electric motors transfer their driving power directly to the wheels through fixed ratio gears.
Electric drive motors operate at far lower average temperature and pressures, and have fewer moving parts, than an internal combustion engine. That leads to less mileage-related wear and tear and lower maintenance and repair expense than that of conventional vehicles, at least for drivetrain components.
An on-board high-voltage battery system handles power demand at initial motor start and at starts after a traffic stop. Once above a set power demand threshold, the fuel cell system cuts in, seamlessly, and the battery switches from supplying drive power to recharge or storage mode. An electronic control module receives driver demand and other sensor inputs and determines the best mix of fuel cell and battery power to match the load. If needed for acceleration or for maximum load conditions, the battery kicks in and supplements the fuel cell system.
No plug
Instead of needing to be plugged into a source of electricity, a fuel cell needs to have hydrogen added to an on-board storage tank. The fuel cell assembly generates DC voltage that can either be converted to AC to directly power the electric motors on demand, or be sent to the on-board battery for charging and storage. The battery system also recharges itself using kinetic energy recovered from regenerative braking.
The process of filling a fuel cell vehicle’s tank with hydrogen is strikingly similar to gassing up an internal combustion engine vehicle. The hydrogen ‘filling station’ features a pump that looks a lot like a gasoline pump, except the hose has a nozzle that locks into the vehicle intake tube before any hydrogen can flow. The high pressure — up to 10,000 psi — that keeps hydrogen in a liquid state requires a closed system at all times.
The original B-class F-CELL fuel tank was designed to hold enough compressed hydrogen to enable the vehicle to travel approximately 250 miles. The aluminum tank was lined with carbon fiber to help withstand the high pressure.
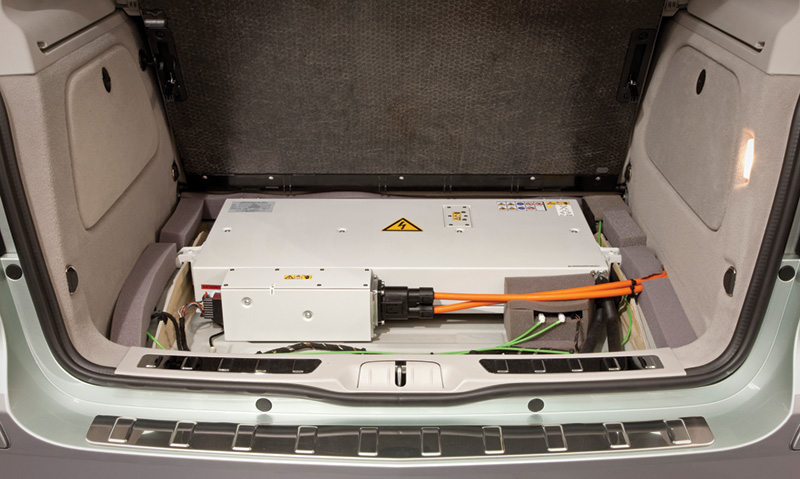
The F-CELL places the high-voltage battery in the trunk floor. The Mercedes-Benz fuel cell system features modular assembly that allows installation in various vehicle configurations.
Near-future technologies
An experimental “F 125!†research vehicle combines state-of-the-art and anticipated near-future technologies to create a prototype zero-emission fuel cell plug-in hybrid with an extended range of over 600 miles in the footprint and luxury accoutrements of a full-size Mercedes-Benz sedan.
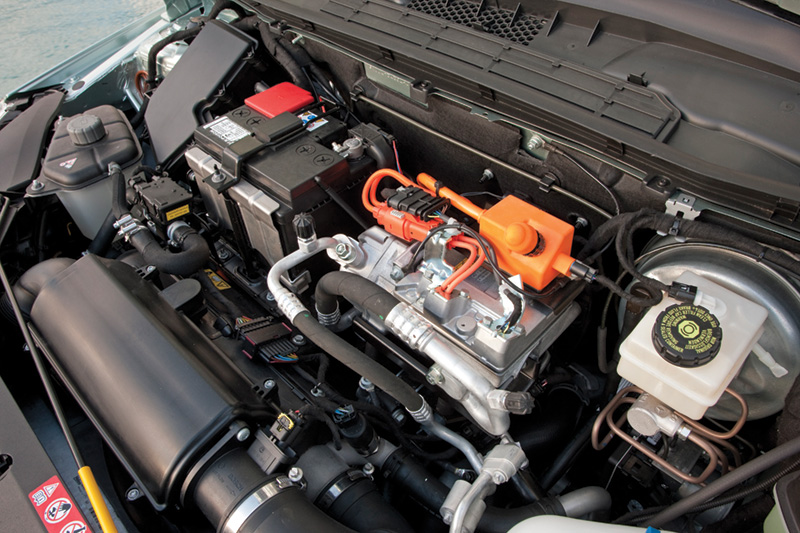
The 2011 Mercedes-Benz B-Class F-CELL packs a power control unit and a fuel cell cooling system underhood where the gatsoline engine would be on a traditional ICE (Internal Combustion Engine) powered vehicle.
A major technological advance enabling the creation of the F 125! is a revolutionary hydrogen tank that is an integral part of the vehicle substructure. The tank design that is robust enough to withstand the 10,000 psi of current hydrogen storage systems is typically a cylinder. The cylinder unfortunately creates cavities between tanks installed next to or above each other.
Mercedes-Benz engineers have designed a system that stores hydrogen at a pressure of 435 psi or less. The lower pressure allows the design of hydrogen storage tanks that are contoured to fit into the vehicle body shell with less space wasted to cavities between the tank exterior and the vehicle structure. In some areas, the tanks can be designed to fit and function as structural components, eliminating wasted space, reducing weight, and reinforcing body shell strength.
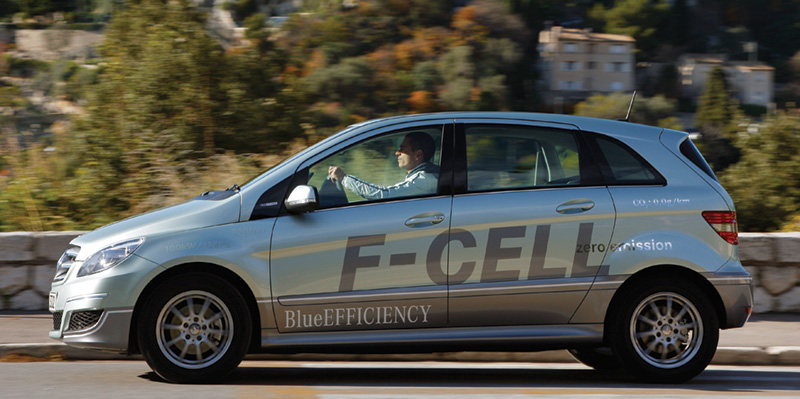
A small fleet of 2011 Mercedes-Benz B-Class F-CELLs traveled around-the-world in 2011 as a proof-of-performance road trip. Five of them covered 30,000 kilometers (18,621 miles) through 14 countries in 125 days.
Mercedes-Benz has fitted a highly advanced, powerful lithium-sulphur battery into the F 125!, which, combined with more efficient fuel cell and hybrid electric control technology, larger hydrogen storage systems, and regenerative braking technologies, enable over 600 miles of travel on a single tankful of hydrogen.
Shared basic development
Mercedes-Benz has also recently partnered with Renault-Nissan and Ford Motor Company to jointly develop new fuel cell stack and control technologies. By sharing research resources and intellectual capital, the partnership should reduce development cost and time-to-market for significant innovations in fuel cell technology.
An additional benefit may be that the shared basic fuel cell design and control technologies will reduce the number of different systems that technicians will have to learn in order to diagnose and repair these vehicles.Â
0 Comments