Turbocharging is all about making use of energy that would otherwise be wasted to pack the cylinders and make a little engine act like a big one, or a diesel perform like a gasoline burner. A new wave of turbos is arriving from Mercedes-Benz to take advantage of the concept, and here we’ll prepare you with operating principles, design fundamentals, and service info.
Once a car reaches cruising speed, it doesn’t need very much power to keep up the pace. But acceleration — especially the thrilling sort that makes driving fun — requires plenty of horses. Wouldn’t it be great if you could have a small engine to propel you down the highway economically, but with the ability to grow miraculously in displacement when you ask it to do so by the action of your right foot?
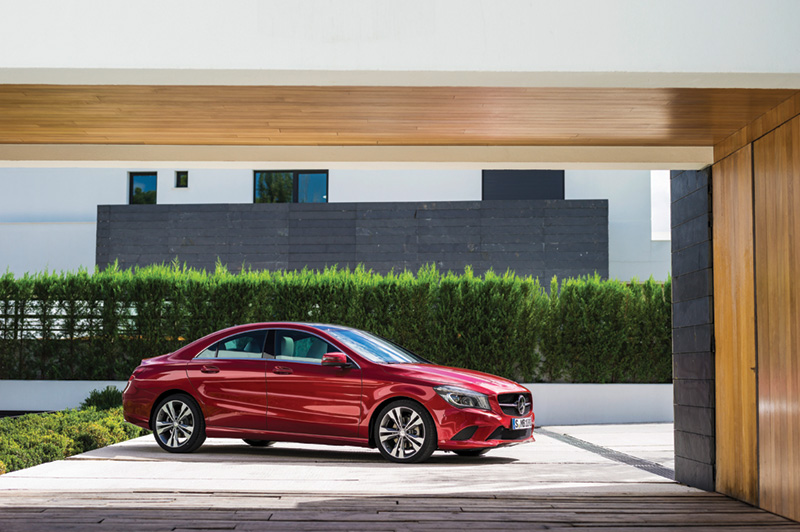
The CLA 250’s turbocharged 2.0L makes 208 hp, does 0-60 mph in 6.9 seconds, and still scores 38 mpg on the highway.
And that’s the idea behind the turbocharger. It allows you to have the seemingly magical combination of small-powerplant mpg and gorilla-motor 0 to 60 times.
111-year-old patent
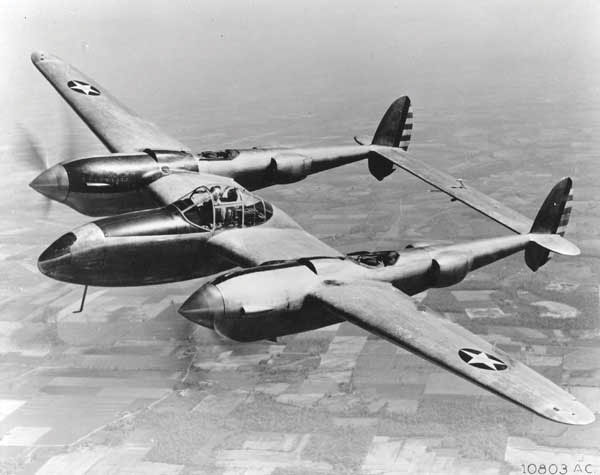
In WWII, turbocharging gave many of our warplanes, such as this Lockheed P-38 Lightning, superior performance at high altitudes where the air is thin. (Courtesy Airforce Image Gallery.)
The history of turbochargers began in 1905 when Swiss engineer Alfred J. Buchi patented the first supercharger powered by exhaust heat. It took another ten years to develop a prototype of a turbocharged diesel engine, but the industrial processes and materials did not yet exist that would allow the manufacture of a true production model.
By 1920, the first turbocharged diesel locomotives and ship engines appeared. That same year Mercedes-Benz began turbocharging cars. By World War II, turbochargers — often equipped with charge air coolers — were used in warplanes such as the Lockheed P-38 Lighting and B-17 Flying Fortress to overcome the lack of oxygen per cubic foot of intake at high altitude. The demonstrated reliability of turbocharging as used in aircraft opened the door to automotive and truck use after the war. Practical turbo-equipped diesel trucks appeared in 1957, and today most light- and heavy-duty diesels are turbocharged.
Flash in the pan?
Although a few decades ago this idea was hyped by quite a few carmakers as the ideal means of putting high-performance excitement back into cars after emissions and fuel mileage regulations took it out. Back then it was really just a stopgap, a temporary phenomenon with several drawbacks. Besides bearing issues and the cluttering-up of the underhood environment, there was throttle lag. The T charged engines of the ’70s and ’80s just didn’t have that “right now†feeling.
Then, multi-valves, ingenious intake manifold designs, seriously-efficient engine management and fuel injection systems, and VVT started to give us that sought-after combination of high performance, great fuel mileage, and low emissions without the need of an expensive add-on. So, turbos faded away except in some premium sporty cars — and diesels. Ever since Mercedes-Benz built the first-ever turbocharged passenger-car diesel in the form of the 1977 300 SD, any boost possible was sought after to get the performance of compression-ignition-powered vehicles up at least somewhat near that of the gasoline-burning competition. So, those are really the only turbos any dedicated Mercedes-Benz shop is familiar with.
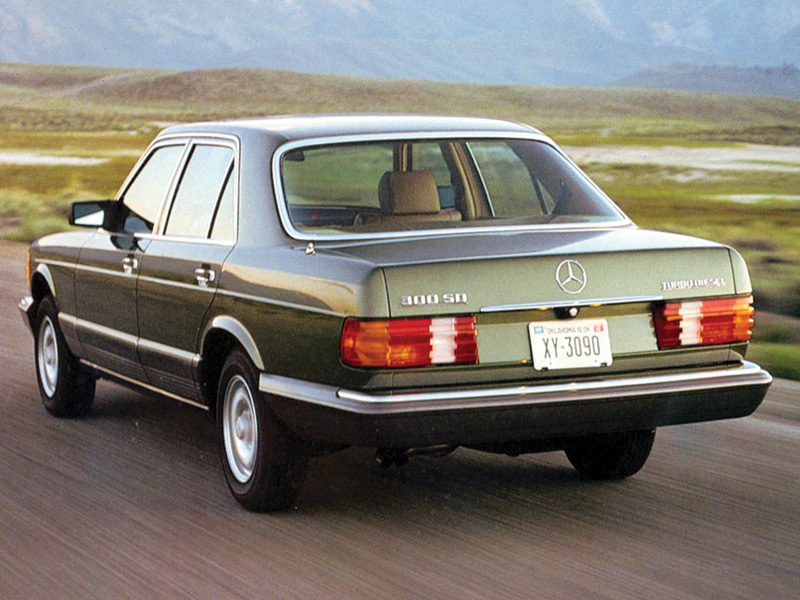
Introduced in 1977, the 300 SD was the first-ever turbodiesel passenger car. With a 0-60 time of about 14 seconds, its performance was a lot better than that of a normally-aspirated diesel.
There’s no denying the benefits of the basic concept, however, especially in the current environmental and regulatory climate, so Mercedes-Benz has expended tremendous amounts of engineering and R&D time refining turbocharging systems, and has lately produced some spectacular results. The CLA 250 2.0L, for example, makes 208hp, does 0-60 mph in 6.9 seconds, and still scores 38 mpg in highway driving. High-performance hasn’t been neglected, either. How about the AMG version at 375hp(!), 0-60 in 4.1 seconds, and 31 highway mpg? Even more impressive is the mean-looking AMG GT-R with its 4.0L bi-turbo V8 that pumps out 577hp for a 0-60 time of just over three seconds.
The lag mentioned above? Just about gone with twin turbos (not the type in the GT-R) — one small high-pressure stage to spin up fast, the other a large low-pressure stage for max power.
Blueprint
A basic turbocharger consists of an axial inflow, radial outflow compressor on the intake side coupled on a common shaft with a radial inflow, axial outflow turbine on the exhaust side. “Radial†and “axial†refer to the direction of gas movement.
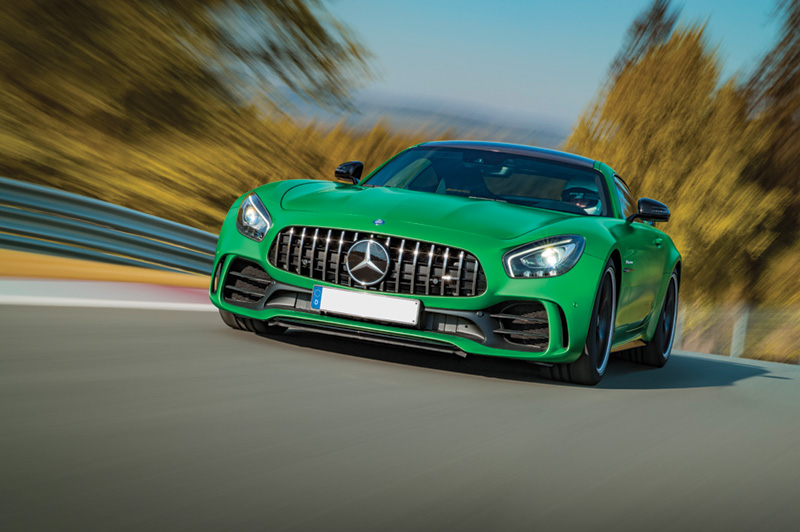
The 4.0L V8 in the breathtaking AMG GT-R has its two turbochargers mounted inside the “V.†Electronically-regulated blow-off valves guarantee immediate response. Charge pressure can reach 18 psi, which provides 2.3 times as many oxygen atoms for combustion as natural aspiration would.
The heat and pressure of the exhaust side is harnessed in the turbine, which drives the compressor through the common shaft. The shaft may be supported by a pair of plain bronze journal bearings and a separate thrust system, or by the newer ball bearing design with integral thrust control, and there are good reasons why the former is giving away to the latter. Ball bearing center housing rotating assemblies don’t need separate thrust control since the shouldered faces of the two ball bearings are installed opposing each other, thus controlling thrust in both directions. Plus, ball bearings are more tolerant of lubrication shortcomings, and also spool up 15% more quickly, dramatically reducing the dreaded turbo lag.
If you were looking for a word to describe turbochargers, that word would be “precise.†The turbine and compressor wheels are carefully positioned in their respective housings with .010-.020 in. of clearance to the contour bores. The precision-machined housings change in volume from inlet to outlet to maximize energy extraction on the turbine side and air movement on the compressor side. The size, shape and contour of the volutes (the spiral, scroll-shaped form of the housing that resembles a ram’s horn) are critical to turbocharger flow rates and efficiency.
By convention, the inlet of a turbine or compressor section is called the inducer section and the outlet the exducer section. A ratio of the relative sizes of the inducer and exducer is often expressed as a trim number, helpful in sizing the turbo correctly. Blade shapes on the turbine and compressor wheels are engineered to reduce losses as gases make the 90-degree turn through the housing. Turbine blade shape constricts at the exducer to extract maximum power from gases that are gradually slowing and cooling.
Inlet pressure on the turbine (hot) side is generally within a few pounds of the actual boost, about 15-20 psi, which translates into a pressure drop of about 13-18 psi across the turbine wheel at full load if the exhaust system backpressure is two pounds. Typically, full-load temperatures drop about 300 deg. F. from a 1,200-1,500 deg. inlet reading. It’s that temperature and pressure drop across the turbine wheel that provides the energy necessary to spin the compressor.
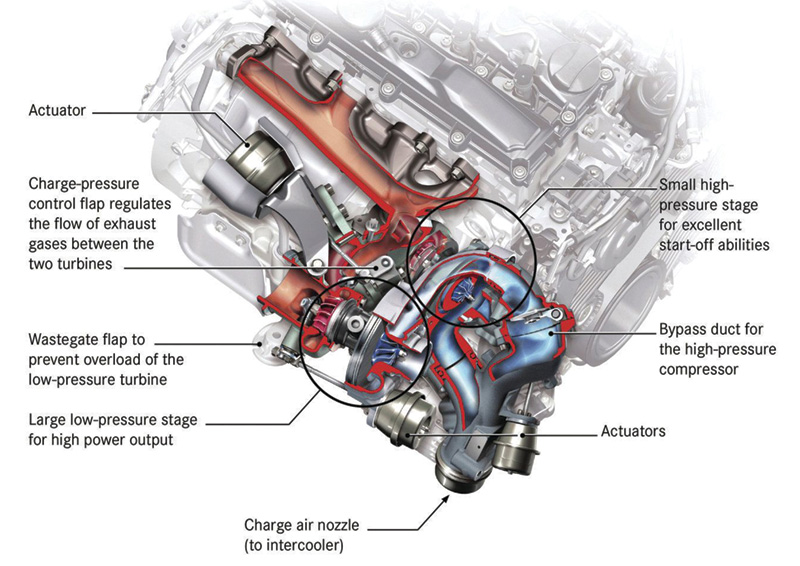
The 4.0L V8 in the breathtaking AMG GT-R has its two turbochargers mounted inside the “V.†Electronically-regulated blow-off valves guarantee immediate response. Charge pressure can reach 18 psi, which provides 2.3 times as many oxygen atoms for combustion as natural aspiration would.
On the compressor side, the amount of boost is controlled by a wastegate or by a variable nozzle arrangement on the turbine side. The wastegate is a simple bypass system. Inlet pressure is routed over to a spring-loaded diaphragm that opens a passage to bleed exhaust gas around the turbine. Less flow and heat through the wheel means slower turbine speed, hence slower compressor speed and less inlet pressure. Simple and elegant.
Limits
Of course, no matter how rugged the design or advanced the materials, there are limits to the power you can get out of any internal-combustion engine. With turbocharging (or supercharging, for that matter), there’s always the risk of destructive detonation, or finding the mechanical limits of the head gasket, block, fasteners, or cylinder head. The engineering challenge is getting as much benefit from artificial respiration as possible without breaking anything, but today’s electronic engine management systems make that easier.
If you’re wondering about the possibility that a pressurized intake manifold could keep the intake valves from closing, that’s only an issue in all-out racing engines with tremendous amounts of boost — an ordinary two-inch valve with 15 psi in the intake only has about 50 lbs. of force counteracting the valve spring.
Tough enough
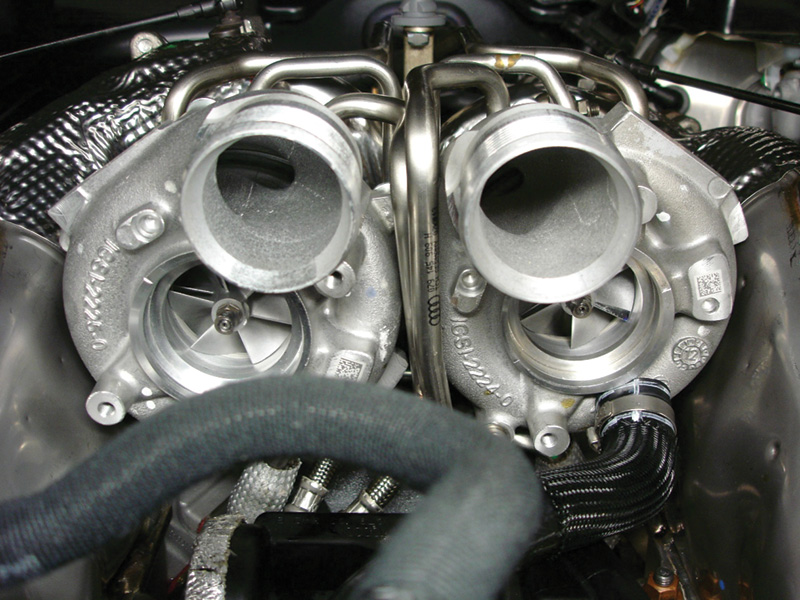
The 4.0L V8 in the breathtaking AMG GT-R has its two turbochargers mounted inside the “V.†Electronically-regulated blow-off valves guarantee immediate response. Charge pressure can reach 18 psi, which provides 2.3 times as many oxygen atoms for combustion as natural aspiration would.
They spin 30,000 rpm at idle and spool up to almost two hundred thousand during boost on some late models, all the while with one side cooking in exhaust heat and the other bathed in cool air. Regardless, turbos have turned out to be quite reliable and durable. As long as they are treated to frequent oil changes using synthetic oil and excellent cooling system maintenance, the number of failures has been quite low. Not non-existent, however.
Over the years, we’ve collected information on turbo troubles from independent service providers. While much of it doesn’t apply to new-generation models, some of it does.
The most common complaint historically? As one shop owner told us years ago, “Noise, usually whining — the customer may say it sounds like he’s got a police car following him. We see this on high-mileage cars, usually with over 80,000 miles. There’s no severe change in power. The loss is gradual.â€
High oil consumption from a leaky seal on either the intake or exhaust side isn’t unusual, and another shop owner mentioned a different type of failure that showed up in his California shop: a seized turbine. Naturally, the drop in power was dramatic.
Examination
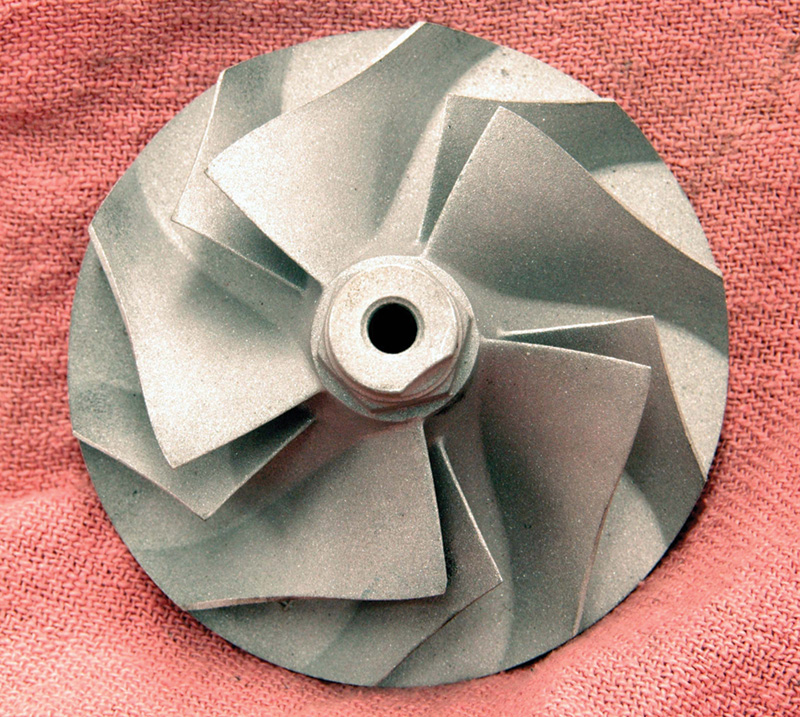
A whole lot of sophisticated engineering and manufacturing processes were needed to produce this compressor wheel.
As far as diagnosis is concerned, one expert said, “Pull the boot off the intake and spin and rock the rotor by hand. Look for too much side play, but it’s interesting how many have play, but aren’t causing problems.
“For example, we had a Mercedes-Benz turbodiesel in for other service, but checked the turbo anyway. I saw what seemed like excessive side play, so I advised the customer that it was okay for now, but that he ought to bring it in after 5,000 miles or so for me to check it again. Well, it was exactly the same, and I expect it to just keep going with no problem.â€
Worrying about excessive side play is common among techs, but it’s the result of a perfectly understandable feature of older turbo designs. Floating bearings are used, meaning there’s oil clearance on both sides and the bearing itself rotates at one-half shaft speed. This provides extra protection, yet makes the fit seem loose. This situation illustrates a basic point: Turbos are different from anything else you’re used to working on. They require a little special knowledge.
Another turbo expert told us, “Stress the basics before jumping on the turbocharger. If a car’s blowing smoke, the turbo often gets blamed when the problem is actually the valve seals.
“Next, you have to make absolutely sure to diagnose the cause of the failure before you install a new turbo, or there’s a good chance it’ll fail immediately,†he says. “For instance, the biggest reason for bearing failure is lack of oil supply. Oil supply lines tend to coke up. Some technicians disconnect the line and see oil squirt, so they think it’s okay. But what they’ve got is pressure, but no flow. If you try to clean the old line, you’ll dislodge the deposits, but might not get them all out. And the oil passages inside a turbo are very tiny, so just a small piece of coke can clog them. Buy a new line.
“Oil return is by gravity only, so the drain line is important, too. If it gets plugged, excessive pressure will force oil past the seals. But you can clean these lines because you don’t have to be so worried about particles. The oil goes back into the crankcase and through the filter anyway.
“You can disassemble a turbocharger and see very clearly why it failed. The parts read like a book. If the shaft and bearings are blue, you know there’s been a lack of lubrication. If they’re scored, contaminated oil is the trouble.â€
Lube loss and codes
When excessive oil consumption or smoking is the complaint, you’ve got to enlist a little logic to determine the cause. If the plugs are clean, a bad shaft seal on the exhaust side of the turbo is a good bet. If only a few plugs are oil fouled, valve stem seals are implicated. But if all the plugs show equal evidence of oil burning and there’s a film of lube on the inside of the duct to the manifold, the turbo is leaking on the compressor side.
Oil burning brings up a related situation: too much backpressure due to a clogged cat, which may have destroyed the shaft seal, and will do the same to the new one if not corrected.
Troubleshooting the electronics involved in boost control is beyond the scope of this article, so we’ll just mention that there are sometimes fault codes in the OBD system that pertain, and that your XENTRY will show you if there’s been a lot of detonation sensor activity, and walk you through diagnosis.
Keep ‘em alive
At installation, make sure to prime the bearings with fresh lube, and, as was mentioned above, get a new oil supply line and clean the drain line. Kill ignition or injection and crank the engine for half a minute or so to get the oil pressure up before starting. Of course, you already did an oil and filter change as S.O.P., right?
And this brings up recommendations you should be making to your customer. Oil change intervals should never be stretched to the limit, and here’s a case where the synthetic Mercedes-Benz recommends is absolutely mandatory. Also, caution him or her not to run around a quart low, and that allowing a short idle period before shut down will help those bearings survive. As one turbo authority said, “When you suddenly shut off the oil flow to something that’s spinning that fast, you’re going to have problems.†Not as critical today as it once was, but still good advice.
Download PDF 〉
0 Comments