Specific Sanden and Denso compressors are interchangeable in many 2011-2015 Volkswagen R134a systems. Here’s why you’ll need to flush the oil in the system whenever you switch from one compressor brand to the other.
Lubrication is critical to maintaining the service reliability of an air conditioning compressor. The lubricant must first and foremost create an oil film that reduces friction between moving parts, to enhance fuel economy and minimize wear. It must also carry heat away from moving parts, and help seal system clearances and reduce compressor noise.
Additionally, the lubricant must be able to withstand high operating pressures, plus temperatures that change from extremely high near the compressor outlet, to very low around the evaporator.
Further, it must have no chemical interactions that reduce cooling efficiency or create by-products that may be harmful to seals and metallurgy in the system.
Dancing together: The refrigerant/lubricant mix
This is further complicated by the fact that the lubricant must mix with and be transported around the system by the refrigerant. As it moves through the system, the refrigerant/lubricant mix must meet different requirements in various components.
The compressor tends to need a lubricant-rich, higher viscosity mix to protect moving parts and assist with sealing and noise reduction. In the vapor line, high viscosity lubricant may be less desirable. A thicker oil is more difficult for the vapor to transport. This can result in lubricant building up in traps in the evaporator or low points in lines, where it can alter pressures and reduce heat transfer. The evaporator would prefer a mix that features just the right amount of refrigerant: not so much as to cause flooding or allow liquid refrigerant to flow back into the compressor (liquid is not compressible, and can cause excess wear on compressor parts), and not so little that the refrigerant boils away before allowing the evaporator to extract the maximum heat from the airflow.
Temperature and pressure are bossy
Whether or not a refrigerant/lubricant mix remains in the proportion required by the system at different temperatures is a function of the interaction between the temperature and load in various regions of the A/C system, the lubricant formulation, the refrigerant, and the operating envelope of the A/C system. The Critical Solubility Temperature (CST) is the temperature at which the viscosity of an air conditioning oil will change enough to make it drop out of solution with the refrigerant. At either end of a CST range determined by the lubricant formulation, the oil can alter its structure enough to drop out of solution. At temperatures above approximately 100 degrees F (40 degrees C), a polyalkylene glycol (PAG) oil formulation not matched to the A/C system on the vehicle could separate from the refrigerant. A/C refrigerant can see as much as 500 degrees F (260 degrees C) in certain areas.
PAG is available in 46, 100 and 150 centistoke (cSt) viscosities, plus a few other less widely used formulations. Viscosity is a way of rating how thick an oil is and how easily it flows. The oil must be thick enough to maintain a film on which moving parts can float, and thin enough to flow into narrow spaces between those parts.
A higher cSt (viscosity) number indicates greater resistance to flow. A lower cSt rating means the lubricant flows more easily.
Of course, it is not as simple as that. An oil’s thickness and ability to flow are significantly affected by temperature and, to a lesser extent, other factors.
As the temperature of the lubricant increases, its viscosity decreases, allowing the oil to flow more freely. As temperature goes down, lubricant resistance to flow goes up, and its measured viscosity increases.
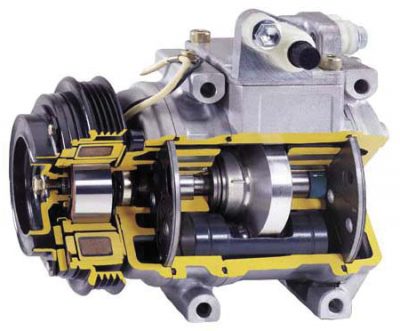
Pressure, or load, also influences viscosity. As the load increases, it makes it harder for lubricant to flow, which raises the measured viscosity of the fluid. The lower the load, the easier the lubricant flows, and the lower its viscosity. Gas temperature increases as pressure goes up, so a lubricant’s ability to resist heat is critical in high-load conditions. Excess heat causes lubricant decomposition, which can lead to oil starvation and compressor failure.
Application-specific requirements
The nature of demands on the refrigerant/lubricant mix – having a viscosity range that is thick enough to provide an oil film that doesn’t break down under high-temperature, high-pressure conditions in the compressor, while thin enough to provide low-temperature flowability in the evaporator, offering compatibility with seals and metals, and resisting moisture absorption – is further complicated by the fact that each compressor and air conditioning system can be very different. In addition to the presence of different metals and seal materials, something as simple as different inside diameter of the lines in various systems can significantly impact flow velocity, pressure drop, and other performance parameters of the refrigerant/lubricant mixture. This of course means that the lubricant selected must be fine-tuned to the specific operating envelope of the vehicle and A/C system in which it is installed.
Application-specific R134a lubrication recommendations typically exist because the compressor has certain engineered characteristics that maximize performance when used with either a lighter or heavier viscosity oil. For example, while most modern compressors are designed with tight tolerances and will deliver better fuel economy when used with a lightweight oil, some heavy-duty compressors need a thicker oil in order to withstand the load and temperature extremes they are designed to handle.
Slick switch
A real-world scenario is the need to switch lubricant if you are replacing a Sanden with a Denso compressor (or vice-versa) in a 2011-2015 Volkswagen (all models except the Routan). Both are R134a systems and use PAG oil, but each compressor brand requires a different PAG formulation. You must flush the entire system to remove all of the existing PAG oil before installing the replacement compressor.

For example, in a 2012 Passat, the VW-approved Sanden compressor is model number PXE 16, and the alternative from Denso is model number 7SEU17C. The approved PAG oil for the Sanden is VW part number G 052 154 A2; for the Denso it is G 052 300 A2. See the Volkswagen Tech Tip (TT 87-14-01) for details.
Not only are the lubricants different for each compressor brand, but the total system capacity also differs. The lubricant capacity of the Denso compressor is 140 +/- 10 cm3 (4.7 +/- 0.3 ounces), for the Sanden, it is one ounce less (3.7 +/- 0.3 ounces).
Trust, but verify
As a new vehicle is on the drawing board, engineers test and approve a potential lubricant for its specific air conditioning system application. Only lubricants that maintain their viscosity, solubility with R134a, chemical stability, and resistance to moisture and acid over a wide range of temperature and operating pressures, among other requirements, receive Volkswagen approval. Without testing, the company has no way of knowing whether a lubricant meets the performance requirements of a specific application, and so use of non-approved lubricants cannot be honored in the event of a resulting problem.
No oil balancing
Factory-new Sanden and Denso replacement compressors for 2012 and newer Volkswagen vehicles ship with the correct type and amount of PAG oil pre-installed. Unless you are working on a dual-evaporator vehicle, do not add more lubricant. The oil in the new replacement compressor is equal to the total system capacity, and will be distributed through the refrigerant circuit upon initial startup. If you are installing a new replacement compressor for an older Volkswagen, check the literature that came with the compressor to determine how much, if any, oil was pre-installed.
After the hoses are connected, but before initial engine start, rotate the compressor by hand at least fifteen times. This moves some of the oil out of the compressor, which helps reduce the potential for liquid slugging upon startup.
If you are repairing a vehicle with two evaporators, you will likely need to inject additional lubricant. Refer to the sticker under the hood for the system capacity.
Look up the repair procedure in the VW ElsaPro system or in your service information system. The most up-to-date information will be in ElsaPro. It is a VIN-driven system that provides individual vehicle lookup based on the build specifications for each vehicle. It eliminates the variables and unknown factors of the old-school oil balancing method. You simply flush the system and install the specified oil charge.
If installing an aftermarket compressor that was sold without pre-installed lubricant, or re-installing the existing compressor after repairs to other A/C system components, drain the oil from the compressor before re-installation. To extract as much oil as possible (applies to 2012 and newer Beetle, 2010 and newer CC, 2006 and up Eon, and 1992 and up Golf), remove the oil drain plug and hand-turn the ribbed belt pulley or magnetic clutch plate on the compressor until oil stops flowing out.
After flushing the A/C system, add the amount of refrigerant oil specified by ElsaPro or your repair service information. Inject approximately half of the total lubricant charge directly into the compressor. Make sure to include any additional lubricant needed for systems with a second evaporator.
In the era of R-12 refrigerant use, mineral oil was the lubricant of choice. Mineral oil is miscible with R-12, meaning it dissolves into and flows with the refrigerant throughout the A/C system. But mineral oil does not mix well with R134a, the refrigerant charge for all Volkswagen vehicles manufactured for sale in the U.S. from the mid-1990’s up through 2016.
R134a systems in Volkswagen vehicles use PAG as the factory fill lubricant. PAG oil is a synthetic lubricant that offers better solubility in R134a than mineral oil. PAG oil will not dissolve completely into R134a, rather it will form little globs or clumps that are pushed around the system by the refrigerant.
In addition, Volkswagen-approved PAG oil contains lubricity and antioxidant additives and end-capped formulation that help it remain chemically stable over a wide temperature range. It better resists breakdown of its lubricating film, even under high pressure and temperature in the compressor.
Water torture
PAG oil is hygroscopic (attracts moisture). Moisture in high temperature and pressure conditions can react with any impurities in the system and form acids, which are corrosive to metals. Close PAG oil containers immediately after use to prevent moisture entry.
The dryer, dryer bag or dryer cartridge in the system can absorb approximately 7 grams (1.42 teaspoons) of water before becoming saturated. If any more water is in the system, it flows up to the expansion valve (TXV) nozzle or restrictor. There it freezes, causing the TXV to become stuck open or closed, and reducing cooling performance. Pull a deep vacuum after refrigerant recovery – the A/C system will thank you.
Also, do not add other types of lubricant to R134a systems containing PAG oil. It does not mix well with other oils.
Flush with Refrigerant
Inspect the extracted oil for any signs of contamination. If you find increased opacity versus fresh oil, color change to red, or the presence in the oil of metal filings or other foreign matter, you need to flush the system before installing replacement components. If you are switching from a Sanden to a Denso (or vice versa) replacement compressor, you must flush all of the existing oil out of the system even if you found no evidence of contamination, as each compressor requires a different PAG oil formulation. On vehicles with two evaporators, disconnect the circuit to the second evaporator and flush it separately from the first evaporator.
Volkswagen allows flushing with R134a refrigerant, or with compressed air plus nitrogen. Flushing with refrigerant R134a is the preferred method. Using compressed air and nitrogen does not achieve the level of cleanliness of flushing with refrigerant R134a. The refrigerant loosens oil deposits, allowing more effective cleaning with less effort.
Compressed air and nitrogen should be used for cleaning individual components, and only if there is no possibility of flushing the entire system with refrigerant R134a. If contaminants are located in a single component, or pressure and temperature readings indicate the likelihood of moisture in the system, the combination of compressed air and nitrogen may force moisture and contaminants out of the component or system. Note that the restrictor (orifice tube), expansion valve, compressor, receiver and reservoir (accumulator) cannot be flushed using compressed air and nitrogen. On condensers that contain an integrated receiver/dryer, remove the dryer cartridge before using compressed air and nitrogen.
First, blow out particulates with compressed air, then remove moisture from components using nitrogen. Refer to ElsaPro or your service information for details about the correct selection and usage of adapter(s) for connecting the pressure hose to the refrigerant circuit.
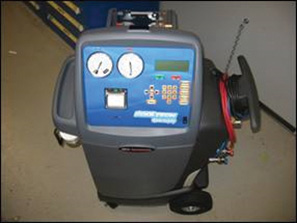
Use the A/C Service Station with Flushing Device – VAS6381 – or Air Conditioning Flush Tool – VAS6337 – for refrigerant flushing. The flush function and flushing tool are built-in on these A/C service machines, and appropriate adapter sets are available through the Volkswagen Special Tools Catalog.
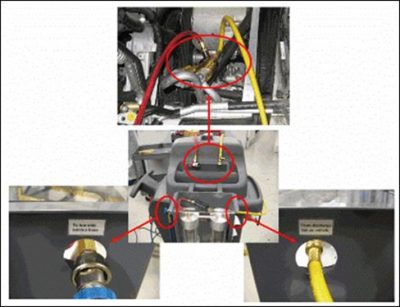
Remove the orifice tube and accumulator, or expansion valve and receiver/dryer, if equipped. The accumulator could be flushed, but it requires a lot of refrigerant due to its large size. When this refrigerant is extracted, the accumulator ices up and prolongs the extraction process significantly.
An adapter may not be available for the new expansion valve design on the 2016 Jetta, Passat and Beetle. If not, drill open the expansion valve, use it as a connector during flushing, then replace it with a new one. Refer to ElsaPro or your service information for details on prepping and drilling open the TXV. Make sure the sealing surfaces are not damaged when drilling the TXV, or refrigerant will leak out during flushing.
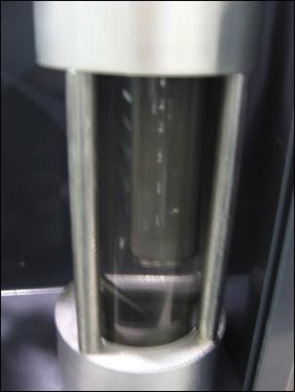
You will need at least 7 kg (approximately 15 pounds) of R134a to completely flush an A/C system. Warm your refrigerant cylinder for 30 minutes prior to beginning the flush procedure. This increases pressure in the cylinder and accelerates the flush process.
Perform flushing according to the operating instructions of the A/C Service System. Plan to do at least three flush procedures. Depending on the type of contamination, dirt (old refrigerant oil and abraded material from the compressor) is deposited on the viewing glass(es). If the refrigerant oil from the flush process is black and viscous or there are many shavings in the refrigerant circuit, replace the filter in the flushing device. Clean the viewing glass and flush a fourth time to confirm that the A/C circuit is clean.
When done, check the pressure in the refrigerant circuit. There should be no positive pressure in the system. If there is, evacuate the refrigerant system briefly once more.
Vehicle and compressor manufacturers select air conditioning lubricants based primarily on their viscosity and lubricity, but there are a range of additional properties that make one oil a better choice for a specific A/C system application than another.
It is vital to choose the right oil for the job. Check the underhood label for the correct A/C system lubricant, and refer to ElsaPro or your service information for details if you are swapping one brand or model of compressor for another. It will help keep your customer cool, and your customer satisfaction high.
0 Comments