With each new generation, Volkswagens have become increasingly high-tech. Innovations, including advanced safety systems, adaptive cruise control, parking systems, etc., all rely on one thing to work together — the wiring. VW, being one of the largest auto manufacturers in the world, strives to lead the pack in advances. And, with more and more convenience and safety designed into their vehicles, the enormous amount of wiring required can be staggering.
The wiring harness that connects every system of a modern VW works like the central nervous system of a body, connecting every part of the vehicle to critical systems. VW does its best to maximize wiring efficiency and design. It is an essential assembly of cables or wires that transmit signals or electrical power. And it has the potential to save lives, from the most mundane task of a lighting circuit, to the safety system wiring that connects to air bag circuits, to ABS systems, and to other critical safety, comfort, and convenience systems.
Without these systems functioning correctly, several different issues may arise. Some problems may seem random, others not. Often, faulty wiring connections cause sensors to give false readings, leading to a misdiagnosis of problems. As with most vehicle issues, it is wise to begin diagnosis with a full vehicle scan. Volkswagen designs vehicle systems with diagnosis in mind, and many electrical faults may be stored in vehicle control units.
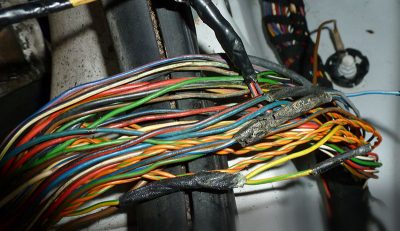
Great care is taken by Volkswagen to protect the wiring on their vehicles. However, issues sometimes still occur as a vehicle leads a very difficult life, subjected to extreme heat, cold, vibration, and water intrusion, which is the most damaging to the wiring system.
Issues with wiring and connections can be challenging to diagnose properly because they are much less common than individual component failures. But with some patience and basic understanding, even difficult issues can be resolved.
Flexing
Any time a wire is flexed, it is stressed. Constantly stressing a wire eventually begins to break down its insulation. This is bad for several reasons. If enough insulation becomes damaged or destroyed, the exposed wiring may short out. If multiple wires short out simultaneously, this can be very problematic. Burnt wiring, popped fuses, and loss of vehicle system functionality can occur.
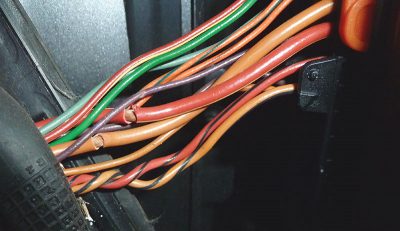
There are many locations in a vehicle that require wire movement, or flex, to allow proper use. Doors, seats, tailgates, trunk lids, and even the hood of a car may have wiring running through it that must flex. Many VW harness kits are available seperately, and can be replaced rather than repaired.
All doors have wiring that must move or flex so they can be fully opened. Certain VW models offer door handles that have wiring for lights or keyless entry that must be able to move. The door harness, particularly on the driver’s side, gets a great deal of abuse in most vehicles. This harness usually has numereous systems dependent on its proper operation. The power locks and vehicle alarm both have to pass through the door. Power windows, power mirrors, and speakers all rely on the door harness. The most critical of these wires is for any air bag wiring that may run through the door. Side impact sensors often reside in door cavities. That is a lot of wire to run to each door!
Accidents
In cases when a VW is in a collision, wiring damage may not be apparent or easily identifiable. During repairs at a body shop, a wire that has been scraped or crushed from an accident may go unnoticed.
Most commonly damaged, from accidents to front and rear bumpers, are parking sensor and marker light wiring. These often run across the bumper frame just beneath the bumper cover. Any impact can damage these sensitive wires, and such damage may not be readily apparent.
When there is accident damage to vehicle doors and body panels, other systems may be affected, in particular air bag impact sensors and window motors/modules that reside inside the door panels of certain models.
Body panels, particularly in the rear, typically house several components that can be damaged from accidents. Often, stereo and connectivity components are located in the trunk recesses, particularly in larger VW models. If damage to modules or wiring is suspected in this area, close inspection is necessary. Crushed or pinched wiring is often the culprit in these cases.
Water Intrusion
Water intrusion is also a large contributor to wire damage. Great care has been taken by VW engineers to properly manage water intrusion, but it is difficult to plan for every aspect of harsh environments. It is common knowledge that water and electricity do not mix. Water can short out connectors, build corrosion that may cause intermittent connection issues and, if water gets inside any of the electronic control modules in a vehicle, it can destroy them in short order.
Cars have to live in a harsh environment, which complicates protecting important components. Two key areas that are the most susceptible to water ingress are the sunroof and the cowl drains under hood. These have to deal with the majority of rainwater and divert it for proper draining.
VW service states that sunroof drains should be cleaned at least every 30K miles, and sooner in cases where the vehicle may be parked outside under trees or in certain climates. Most often, a blocked drain is due to dirt and plant matter accumulation. If such blockages are left without repair, the drain water can quickly become an issue. Front sunroof drains are the most common to experience clogging. When these drains become obstructed, rainwater travels down the A-pillar and drains inside the vehicle. The components that lie below this part of the vehicle are susceptible to damage, as they may be electrical components. These can be fuse/relay boxes, door harness connectors, and electronic throttle units.
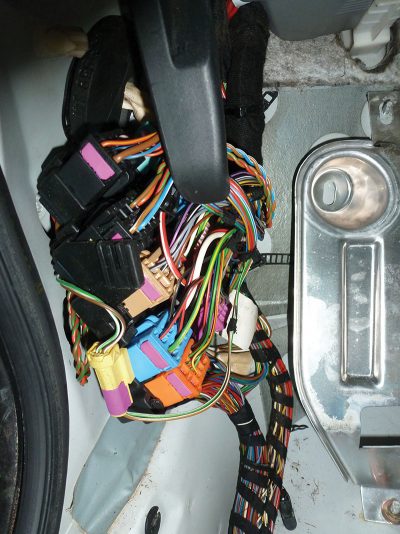
Rear sunroof drains also must be cleaned periodically. Failure to clean these drains, particularly in Jetta and Passat wagon models, can result in ingress at the rear corners of the vehicle, which also may contain electronic components. Often stereo and connectivity components are placed here.
If you suspect water damage at a certain connector or area of the vehicle, it is easy to undo the connector and inspect for corrosion. In cases where there is water damage, the connector may appear discolored, usually appearing to have a light greenish chalky color. This is corrosion buildup that is impeding current and signal flow. Over time, this corrosion can completely cut off flow. The damaged wire, connector, and water leak will all need to be repaired to return the vehicle to proper working order.
The cowl drains elsewhere in a vehicle also contribute to water ingress if left unchecked. When the underhood cowl drains become clogged, the water often overflows directly into the vehicle’s fresh air inlet. This will force water into the interior of the vehicle and collect on the floorboards. Many early 2000 Passat models suffered from water ingress issues. The main body harness typically runs through the floors, and water can make its way into connectors and splices there, resulting in a myriad of issues. Close visual inspection is best here, checking for split insulation, corrosion, and broken wires. Often, electronic modules are also located in the floorboards and can quickly be submerged and damaged from water.
Doors
Another area of the vehicle that sees tremendous use is doors. With numerous convenience features available in modern VWs, a lot of wiring has to travel to the doors, more so in the driver’s side. This wiring, being constantly flexed, sometimes degrades. Often, a customer’s complaints will lead you to a faulty door harness wiring. Nonfunctioning windows and inoperative power locks are the most common complaints. It is smart to do a full vehicle scan as a first step in diagnosis. This will help take you in the right direction if there are multiple system faults such as short to ground or open circuit faults in any of the vehicle systems that share the door wiring.
If the door harness is suspected to be compromised, it is sometimes easy to visually examine the harness for failure. Most vehicles have a rubber covering with grommets to seal the door harness where it flexes. This can be popped off from one end and slid back, exposing the point in the wire that flexes the most. This is where most door harness breaks occur. Any open/cracked insulation has failed. The Mk5 Jetta model is known to have common door harness failure. The flex section was originally designed too short, causing wire stress and insulation failure.
If it is not possible to completely see the flex point in the door wiring, a tug test may work as well. Lightly pulling on each wire to determine if it is broken is a great way to check for failure. Test every wire because it is common to have multiple breaks in the same harness. Take extra care with power wires. You do not want to ground these out on the chassis or any other wiring near by.
Repair is often possible. But care must be taken to allow for proper movement of the wiring, as well as any air bag connections, in which extra care must be taken. In cases where multiple wires have been damaged or show signs of deterioration, replacement is your best option to eliminate future issues with the same area.
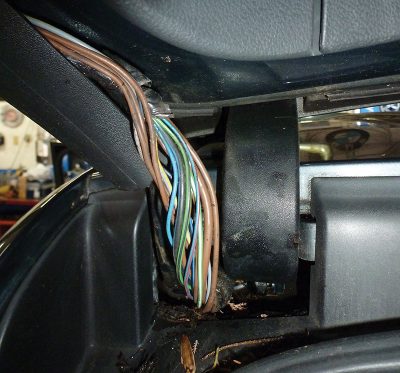
Trunk
The trunk or tailgate of cars also have wire looms passing through them. These are usually for lighting circuits and trunk latch wiring. If a vehicle gets a lot of use, the trunk harness insulation may begin to degrade. Issues with power to lighting and finicky trunk latches can usually can be traced back to a broken wire in the trunk harness. This is common with vehicles across all makes.
Seats
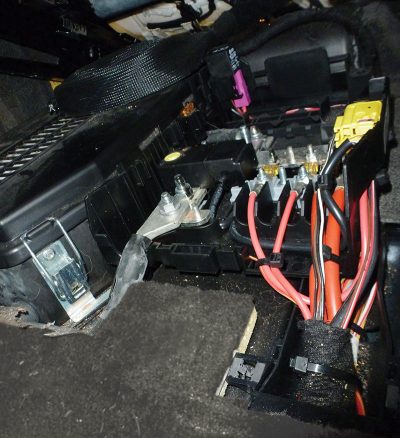
The seats of most vehicles are also susceptible to wiring issues. Through constant movement, and even liquid intrusion, the seat harness gets a lot of abuse. This harness can power seat adjustment motors, heated seats, and, most importantly, the air bag wiring for the side impact bags, which are commonly located in the seat bottom.
The air bag system for seats relies on a specific resistance value to properly report air bag condition. Any damage to the wiring can degrade the signal sent to the vehicle’s air bag module. This most often results in an air bag fault stating high resistance in the circuit or air bag itself.
The most common source of faults in the air bag circuit is the connector under the seat. This connector gets stretched every time the seat is moved. It can eventually spread the pins on the connector, causing intermittent connections. This area of the car is also susceptible to liquid intrusion, and if liquid is spilled onto these connections, it affects the resistance of the wiring, resulting in an air bag warning light. Often, merely releasing the connector then re-seating it is enough to return the wiring to reading properly. A more complete repair for this issue involves replacing and re-pinning the connector to the seat air bag.
When repairing air bag connectors, it is critical to follow proper precautions. In certain cases, VW does not recommend repairing connectors or harnesses, and replacement may be necessary.
The first step in any air bag work is to disconnect the vehicle battery. Many technicians avoid or forget to do this critical step. If an air bag accidentally deploys, particularly while being worked on, it can be deadly. Do not forget to disconnect the battery! Death or serious injury may occur if care is not taken in the repair process.
VW designs air bag connectors specifically for their task. They rely on certain resistance values, and pins in most of these connections are gold tinned. This ensures very low connection loss. Repairing an air bag connector is not a standard wiring repair. Cutting and splicing a butt connector will not suffice and may cause resistance values to fall out of spec. A crimped/sealed water-tight connection is the best possible repair to ensure proper function and long-term durability.
Any time a repair is made where multiple wires lead to a connector, it is wise to stagger the splices. Don’t merely cut all the wires in one spot, as this creates a huge bundle of splices in one location. This can cause fitment issues, as well as potentially create future issues due to wire stress. Following the wire back an inch or two for each splice keeps the harness tighter for better fitment and wear, particularly in an area where the harness must have flex and movement.
Fiber Optic Data Transfer
With modern vehicles, it is also increasingly common to have fiber optic data transfer systems. These are mainly used for entertainment systems, also known as the MOST bus system. From audio, voice, video, and data, they ensure a lightning fast communication with very high bandwidth, allowing maximum data transfer speed. The difference between fiber optic and normal wiring is how the data is transferred.
In a normal copper wound wire, the data is sent and received via electrical impulses. In an optical system, light is used to communicate to multiple modules, then decoded back to a digital signal.
Just like with standard wiring, the fiber optic system must be completely intact to communicate properly. The fiber optic wiring is comprised of a plastic core, which in itself is not as flexible as a standard wire. Care must be taken when handling. The wire is relatively strong. However, it can be snapped or scraped. Any light loss in the system will cause data loss. This data loss will be transferred to any module connected to the optical system.
When searching for damaged fiber optic wiring, keep in mind the characteristics of the material. It is a semi-rigid plastic material that is not as flexible as normal wiring. It must have smooth radius bends. Otherwise, it may be damaged. If a vehicle has been damaged from an accident and CAN issues are suspected, it is wise to inspect the wiring for this system. Any hard kinks or bends can be the root of communication issues. Remember, this system must transfer light and will not operate properly without a clean signal line.
When diagnosing an optical data system, only a few tools are required. The most crucial tool to help diagnose these systems is a fiber optic system jumper. This tool can be placed in the optical wiring connector of a module to bypass the suspected failed module. If the module is bad, communication will be restored to systems further down the data line.
The optical data systems in automotive applications all work off of the MOST bus system. This is a ring of modules that all communicate to a main control unit. The data flow is one way on these systems, which means that any failed module or wiring on the “ring†will disrupt communication to the modules after the failure. This is why the fiber optic jumper tool is such a good tool to use in diagnosis.
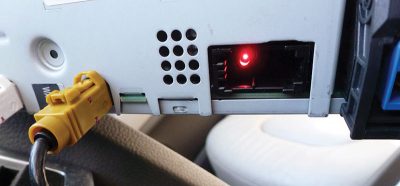
If damage to fiber optic systems is found, it is more complicated to fix than a standard wire, where cutting and crimping may suffice. To ensure proper optical data transfer, the light signal must not be degraded. Special cutting tools, as well as polishing equipment, are necessary to ensure a flush even connection, as well as a clear polished connection between the two surfaces. It may be necessary to repair an optical line in cases where it may not be possible to replace the entire section of wiring.
With every wire or connector repair, it is critical to have the correct tool for the job. Having the right connector release tools and crimping tools is essential. Improperly removing wiring can damage connections, spreading the contacts and causing poor connection issues. When crimping new connectors on repair wire, it is important to follow proper procedures; otherwise poor connections may result.
Download PDF
0 Comments