Steel’s century of dominance in motor vehicles is now joined by aluminum’s surging use to save energy.
For a century after Karl Benz’s Patent Motor Wagen appeared in 1886, cars were made primarily of steel and iron. Aluminum occasionally crept into vehicles, but only minimally.
Then came the past 40 years, with a profound need to conserve energy and a strong emphasis on passenger safety. With those imperatives came the surging inclusion of aluminum as an integral part of the modern car. Instead of being nearly 100 percent steel or iron, today’s cars are roughly 65 percent steel and 30 percent aluminum — and aluminum increases its percentage with each new model year and vehicle refinement.
One of the main reasons for this is to shrink the “energy footprint†the automobile leaves on the environment. Recent independent studies claim that aluminum in automobiles has a 20 percent smaller life-cycle CO2 footprint than steel, and that aluminum vehicles prevent 44 million tons of CO2 emissions when compared to steel vehicles.
Steel Still King, Bolstered by Aluminum
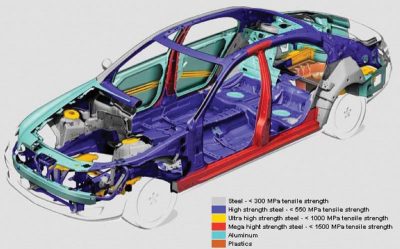
Most steel employed in Mercedes-Benz vehicle bodies is low-carbon annealed cold-rolled, or simple mild steel. Low carbon content and annealing makes this steel soft and malleable, suitable for undergoing the severe deformation required for forming complex shapes. The body and chassis make up over half the weight of the average vehicle, and the tensile strength of steel is significantly stronger than that of the strongest aluminum alloys.
This means that aluminum parts need substantially increased thickness compared to steel to meet strength and safety standards, and newly-developed high-strength steel (AHSS) can reduce steel’s weight by being thinner and still meeting requirements.
Still, aluminum yields weight savings of up to 50 percent compared with the traditional mild steel structure, while being equal in strength.
However, advanced high-strength steels with different properties compared to conventional carbon steels offer advantages comparable to aluminum in weight savings. Also, ferrous metals are easier to weld. Mechanical fastening is about the same for steel or aluminum in terms of complexity, although galvanic corrosion is an issue if aluminum must be joined to a steel substructure.
Aluminum is lighter, and can be formed from relatively thick sheets, but high-strength steels can match aluminum parts through redesign and thinner gauge sheet. Steel and aluminum are both 100 percent recyclable, although steel is somewhat easier to handle.
Mild Steel Bolstered by HSLA Bodies Ruled 20th Century
For the latter part of the 20th Century, Mercedes-Benz vehicles for the most part were made with variations of mild cold rolled steel strengthened and somewhat lightened by extensive use of HSLA (High Strength Low Alloy) steels. Also included were occasional but growing additions of aluminum, plus magnesium and more and more plastics.
But the extreme pressures of the past few years have brought significant changes to steel. Still representing roughly 60-65 percent of the vehicle body and chassis, newly developed AHSS (Advanced High Strength Steel) is beginning to replace HSLA as the steel of choice to add significant strength and lower weight in the vehicle. While most StarTuned readers are repairing vehicles with extensive use of HSLA, some vehicles introduced in the past few years are going big time in using AHSS.
Meeting the fuel economy and lower footprint challenges with less steel at a lighter weight, these steels feature improved formability and crash-worthiness. They can be manufactured at very thin gauges while maintaining the strength of mild steel, and better than conventional steel of a couple of decades ago. This allows using AHSS in the same amount of packaging space as conventional steels — less material used and a lot of mass saved.
Steels with higher tensile elongation have better cold formability for stamping and more automotive energy absorbing capacity, and first-generation AHSS normally gets its formability from ferrite microstructure and its strength from “martensite†microstructures. Second-generation AHSS uses induced plasticity effects, and is the key to the Transformation Induced Plasticity (TRIP) effect. When austenite is deformed, it transforms into martensite and thus gets stronger, delaying sheet metal forming fracture. Their formability is significantly better than that of other first-generation steels.
For the moment, we’ll concentrate on the use of conventional or mild steel augmented by HSLA steels.
Avoid Prolonged High Temperature with HSLA Welds
Heat treatment can be time-consuming and costly, and can affect the strength and toughness of a welded joint, its corrosion resistance, and the joint’s residual stress level. But it is also a mandatory operation required in many welding application codes and standards.
The welded joints of steel, including HSLA, usually require post -weld heat treatment (PWHT) to reduce residual stress and improve the weld’s performance. If the PWHT is conducted at an appropriate temperature and time, the welded joint gains favorable mechanical properties, but if the PWHT temperature is too low, the weld metal exhibits inadequate toughness due to insufficient tempering effect.
CAUTION: If the PWHT temperature is too high, however, the tensile strength at ambient and elevated temperatures is reduced from the excessive tempering effect. PWHT involves heating the metal to a high temperature, where re-crystallization and/or a phase transformation take place, and then cooling slowly to soften the metal after it has been hardened. Normal repair facility welding procedures involving HSLA steel are fine, but avoid overheating or “cooking†the weld to make sure it takes.
Initial PWHT temperatures should be brought down and held at about 600 deg. C, then finally cool the weld down to avoid modifying the mechanical characteristics of the metals involved. If temperature remains too high and is then brought down suddenly, this can actually weaken the weld rather than strengthen it. This camn potentially cause later weld failure and require re-welding.
In cases where the PWHT hold temperature exceeds the transformation point of the weld metal, the weld metal undergoes reverse transformation, which results in a microstructure containing fresh “martensite,†a substance that generates high strength, but low toughness. This deteriorates the overall welded joint performance. The PWHT temperature should be carefully controlled to avoid this problem.
Crash Worthiness is a Strong Aluminum Advantage
Aluminum absorbs about twice as much crash-induced energy as does the same weight in steel, another strong advantage for aluminum use in a passenger car. But, and this could be highly important, the higher cost of aluminum versus steel could add to the cost of the vehicle. Aluminum materials are generally two to three times more expensive per pound than steel.
MIG Welding Aluminum Generally Used
Aluminum has a much lower melting point – half that of steel — and higher thermal conductivity – as much as five time that of steel – and the heat in the aluminum dissipates very quickly. Aluminum must be treated with care compared to welding straight steel, and welding aluminum requires different techniques and possibly different – or expanded — equipment. However, MIG welding or Gas Metal Arc Welding (GMAW) of aluminum are very important aluminum welding methods used in most Mercedes-Benz collision centers, and basic MIG is relatively straightforward to perform.
Aluminum thermal conductivity is double that of steel, aluminum heat dissipates quickly and welding currents and voltages must be higher than for steel. But keep track of correct temperatures and don’t overheat aluminum welds! Basically, you cannot overheat an aluminum joint and achieve a successful weld.
When welding:
- Turn up the wire feed speed for out-of-position joints to avoid a fused tip or weld that does not take.
- Push the wire into the joint.
- Avoid pre-heating to prevent degrading the aluminum’s mechanical properties.
- Keep track of and control the welding “puddle.â€
Gas-shielded flux core welding (FCAW) may be an option rather than MIG for indoor out-of-position applications. This system avoids producing spatter, delivers high deposition rates, and requires very little material pre-cleaning. FCAW filler metals allow higher heat inputs and deposition rates, and perhaps double deposition rates for out-of-position (overhead, upright, or otherwise not flat) welding with excellent bead quality. Some consider FCAW wires more forgiving and easier to use, especially with applications requiring a lot of welding.
It is possible to use the same welding parameters for in-position (flat or horizontal) welding as for out-of-position welding due to FCAW’s wide parameter window.
Tips on MIG Welding
Aluminum welds very well with MIG, and this is best used on thicker materials that are in a flat position. Thinner and out-of-position materials are basically for highly-skilled and experienced aluminum MIG welders. In many cases, even experienced welders find this difficult to learn because of the way the welding puddle looks and the fast travel speeds used to weld out-of-position.
Gas Metal Arc Welding Aluminum (GMAW)/MIG
- Good for most welds
- Creates fast weld deposits
- Welds in every position
- Yields x-ray quality welds
- But pay attention!
- Take great care with temperature in out-of-position welds – do not overheat!
- Needs real skill, appropriate equipment
- Difficulties welding thin aluminum

MIG welding aluminum machine settings are similar for all positions, normally needing about 20 to 24 volts to achieve arc spray transfer. Welding out-of- position, which may account for most collision center applications, however, requires increasing wire feed speed to keep the weld full of metal, with the wire feed pushing the wire into the joint. If feed speed becomes too slow, a fused tip or a weld that does not take might be the result. In other words, turn up the wire feed speed for out-of-position joints.
The thickness of the material to be welded determines some of the techniques. The base material must be thick enough to handle the heat.
Generally Limit or Avoid Preheating
While a little preheat is okay to clear up moisture, limit preheating to avoid degrading the aluminum’s mechanical properties. The maximum heat treatment for heat-treatable alloys is 400 degrees F. (204 degrees C), but if the aluminum is preheated to 350 degrees F. (177 degrees C) and holds the temperature in that range while welding, the aluminum’s mechanical properties are changed, and not necessarily for the better. For non-heat-treatable alloys such as 5000 series aluminum, holding the temperature even as low as 200 degrees F. (93 degrees C) can sensitize the material and make it prone to stress corrosion cracking.
Compared to steel’s 2,600 degrees F (1427 degrees C), aluminum’s low 1200 degrees F. (649 degrees C) melting point does not mean that light-duty equipment is okay for welding aluminum. With thermal conductivity more than double that of steel, aluminum heat dissipates quickly and welding currents and voltages for welding aluminum must be higher than for steel.
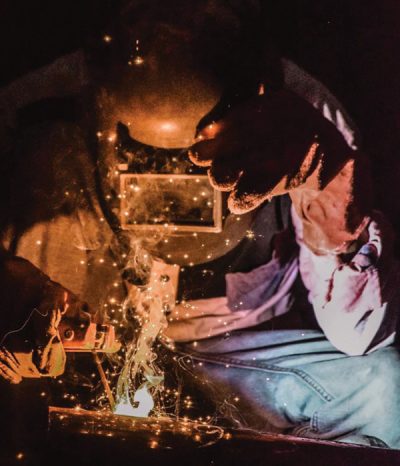
Machining to remove the material tends to distort and create dimensional instability. This is different from steel welding, where stress-relieving is performed by heating the material hot enough to allow movement of the atoms. The stress-relieving temperature with steel is about 1,100 degrees F. (566 degrees C), but the post-weld stress-relief temperature for aluminum (650 degrees F/343 degrees C) is so high, the mechanical properties of the alloy are lost — basically a no-no.
CAUTION: Do Not Overheat Aluminum Joints!
When setting up MIG welding machinery, the operator will need to utilize machine speed to react to the temperature of the aluminum. If welding cold aluminum or spot/tack welding, machine settings are standard, but if welding joints, temperature becomes quite important. When welding a cold joint it may appear that the machine heat is too low; however, heat settings will seem too high as the weld progresses, so be careful.
Overheating may cause the entire joint to turn semi-liquid and fall apart, without real warning. This affects all types of aluminum welding using an arc or flame to melt the metal. When the joint is overheating the molten puddle almost appears to be the base metal. Experience and “feel†are required to determine whether the temperature is correct or too hot, and a heat stick marking next to the weld can help – and basically you cannot overheat an aluminum joint and achieve a successful weld.
Out-of-Position MIG Welding
If welding in-position (flat or horizontal), there’s room for changes if needed because there’s time to react and correct if the weld is going awry, but it’s basically just a feeling with out-of-position welding (overhead, upright, or otherwise not flat). The liquid weld pool tends to drip or sag, and generally welding slower and with lower welding parameters or heat input will reduce the fluid weld pool. Out-of-position welding requires a fast whipping or steady motion concentrating on staying ahead of the puddle. When MIG welding aluminum, the technique used is always forehand and pushing the puddle.
Welding thicker aluminum out-of-position has to be accomplished as a matter of course when appropriate at the collision facility, but the weld appearance can be ugly. The process demands moving fast while preventing the puddle from “rolling over.â€
Aluminum MIG or Aluminum TIG?
Choosing welding processes depends on thickness of the material. MIG welding is great on anything that is 1/8 of an inch or thicker and is in-position. TIG welding works best on thinner stuff and pipe. TIG welding, which stands for “Tungsten Inert Gas Welding,†is the slang term widely used for this system, although TIG welding’s proper name is “Gas Tungsten Arc Welding,†or “GTAW.â€
TIG welding as we know it today was introduced in the 1940s using helium, with “heliarc welding†being the common term for it. It is now a registered trademark “GENUINE HELIARC,†and older welders often refer to TIG welding as “heliarc.†But “TIG welding†and “heliarc welding†are one and the same.
What will the future hold for automotive bodies? Probably more aluminum and less steel. Aluminum offers higher MPG and a lower carbon footprint, and is known as the heart of aircraft and space vehicles, as well as exotic performance and specialty vehicles. This metal virtually exudes “21st Century normal†— but with comparatively limited use due to higher costs as well as greater forming requirements. Its greater utilization for auto bodies may be a combination of engineering and fuel saving advantages and subtle marketing.
Related: Certified Collision Centers Offer Timely, Convenient, Top-Quality Collision Repair Download PDF 〉
0 Comments