The determination as to which structural components are permitted to be sectioned differs among different Nissan models. Dig into the Nissan Body Repair Manual for accurate, current and model-specific sectioning procedures.
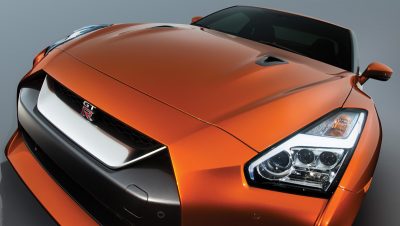
Collision impact force propagates throughout the vehicle, creating a combination of visible and hidden damage. This may include some or all of the following: bending, twisting, crushing, sagging and side-sway.
When a structural component is out of specification in any of three dimensions: vertical, lateral (sideways), and longitudinal (front-to-back), you have only two options.
Sectioning, or full assembly replacement?
- Assembly panel replacement – Cut out the assembly at the factory welds and replace the complete panel.
- Partial panel replacement (sectioning) — Replace only the damaged parts. Cut and replace part of the panel if full assembly replacement is very labor-intensive and costly, and only when damage is confined to a portion of the part.
Sectioning of structural components is permitted in a limited number of areas and only in specific locations. The determination as to which components and which areas can be sectioned varies based on body structure, material strength, part shape and other factors affecting how the vehicle responds to collision impact.
Body pillars, frame rails and other structural components may be sectionable on one Nissan model but not another. Where partial repair is permitted, the Body Repair Manual for that year and model shows the cut location (or area) measured from a reference point specified on the component.
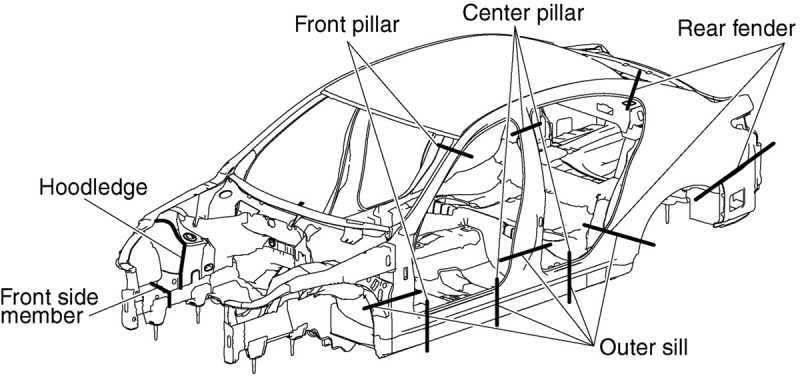
Plan benefits
Planning your repair based on knowledge of which parts can be sectioned and which will be replaced as a complete assembly is invaluable. It helps you write an accurate estimate, develop a more thorough parts ordering list, improve cycle time, and restore the vehicle to its pre-accident condition.
Multilayer construction
Many Nissan structural assemblies contain multiple layers of plates, with different material composition and performance objectives determining which can or cannot be sectioned. A typical structural assembly may have an outer plate that is regular steel that can be sectioned, and a reinforcement that is UHSS and cannot. Structural assemblies designed to handle high stress loads may include multiple layers of reinforcement and permit sectioning of some plates but not all.
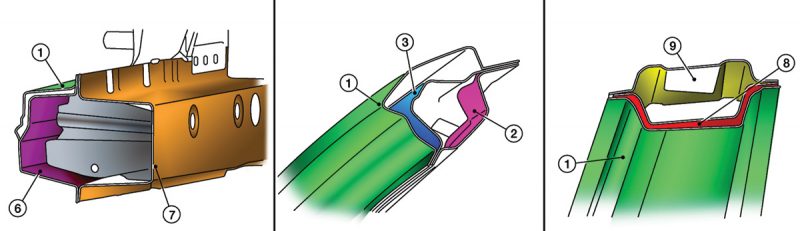
Why some parts cannot be sectioned
A few things that make sectioning less likely to be allowed for a given panel include:
- The component contains reinforcement made of UHSS. The high-strength material loses a significant amount of its impact resistance at the point where it is cut and welded back together.
- The part contains internal ducting or baffles. Complex internal structures are impossible to restore to full strength after being cut.
- Damage occurred in an area that is part of a crumple zone, or that must absorb a high amount of impact force to prevent it from passing into another component. If the concentration of stress is more likely to overwhelm a welded joint than a solid panel, the component should not be sectioned in that area.
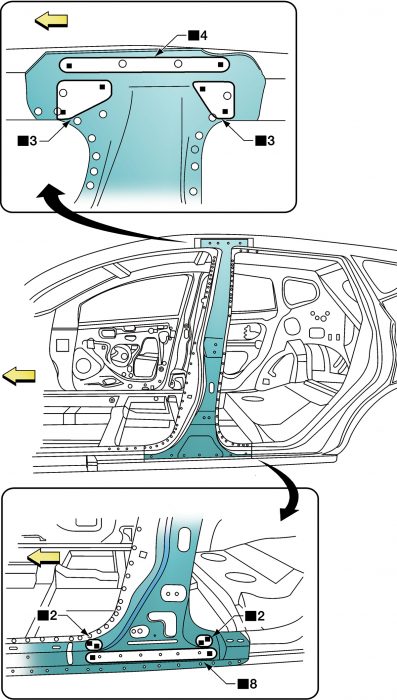
Complete assembly replacement is undesirable. If removal and replacement of the complete component requires excessive labor time, sectioning may be recommended. Additional reinforcement of the new joint may also be specified.
Sectioning that is allowed for a part on one model may not be permitted for the same component on another Nissan. The front pillar reinforcement on one model may be made of UHSS, while on another model it may be made of a traditional steel that can be sectioned.
The model year also affects whether partial repair is an option for an assembly or plate. A structural component of a newer vehicle may be made of UHSS, while that part on an older version of the same Nissan model may be constructed of traditional steel and is permitted to be sectioned.
Strength and sectioning
The strength of steel is measured in megaPascals (mPa). High strength steel is used extensively in automotive bodies and ranges from 440 mPa to 979 mPa. Ultra high strength steel is used in many vehicle structural components and rates from 980 mPa and up.
Use of heat on UHSS structural parts is not recommended as it may reduce the component’s crash resistance. Nissan requires replacement rather than partial repair for key structural components such as side member and center pillar reinforcements. Even if repair is permitted for the component, do not heat HSS or UHSS parts above 550 degrees C (1,022 degrees F). Temperatures above 550 degrees C alter the configuration of atoms in the steel and weaken the component.
Cutting and re-joining parts made of UHSS (980 mPa or higher) create a new part that may be weaker than the component it replaces. Even if it is comparable in strength to the original component it may, in a collision, not offer the crumple zone performance specified by Nissan engineers. If a structural part or reinforcement made of UHSS is damaged, replace the part.
The “Fundamentals†section of the BRM includes charts that show the tensile strength of structural components, whether they contain aluminum, and other factors affecting which repair methods best apply. Check there if in doubt about whether or not a part is UHSS, HSS, or made of a material that cannot be sectioned or partially repaired.
Locating the cut
If sectioning is permitted for a given component, the Body Repair Manual specifies an area on the part where you can section and re-join it to the vehicle. The area may be narrowly defined so as to avoid reinforcements or other internal supports having complex angles or baffles. The specification may locate a sectioning cut in a place where it has the least impact on the crumple zone performance of the repaired component. It may also be positioned or restricted in size so it reduces the possibility of heat damage or spot welding stress affecting nearby components.
Body construction and materials can differ from model to model and change for the same model over time. Thus the same component on different vehicles may differ on whether or not it can be sectioned. Refer to the Body Repair Manual for the vehicle year and model and follow its specifications to the letter.
Cutting UHSS and HSS panels with a torch (gas) is not recommended, as the heat will weaken areas surrounding the cut. Use a saw instead. If torch cutting is the only option (due perhaps to a restricted access location), allow a minimum of 50 mm (1.97 inches) margin around the cut line.
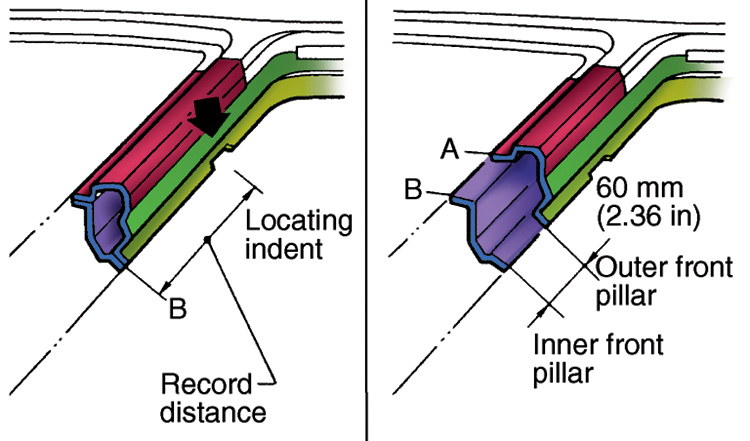
Service panel sectioning
Nissan offers two types of outer body side assemblies as service panels for use in collision repair. One is an integral type comprised of a one-piece outer panel plus smaller, separate reinforcement plates that together form an inner support structure. The second is a separate type in which the outer panel consists of a series of individual parts that join together to form a whole.
In either the integral or separate type, various components may be made of different materials or material strengths in mPa. Nissan may permit sectioning of individual components from each outer body side assembly type if they are below 440 megaPascals (mPa). Always refer to the Body Repair Manual for procedures and specifications that are applicable to the vehicle model and year that you are repairing.
What’s in a name?
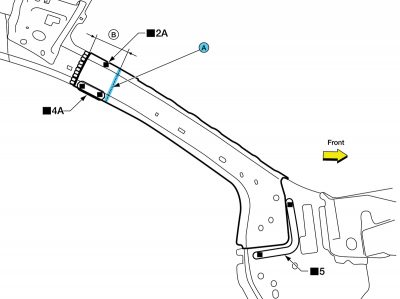
The front pillar on a 2017 Altima sedan has at least two support plates: one called a “reinforcement†and the other labeled “front pillar inner.†The reinforcement cannot be sectioned, while the pillar inner can.
TIP: In at least one location in the BRM, the instruction refers to the front pillar inner as an “inner reinforcement.†Check the BRM section entitled “Fundamentals†to confirm that you are looking at the correct part. This applies to any Nissan model for which you need clarification of structural part names. The Fundamentals section for each model includes a list of body component parts. It shows illustrations of each key structural part, with the correct name next to each part number.
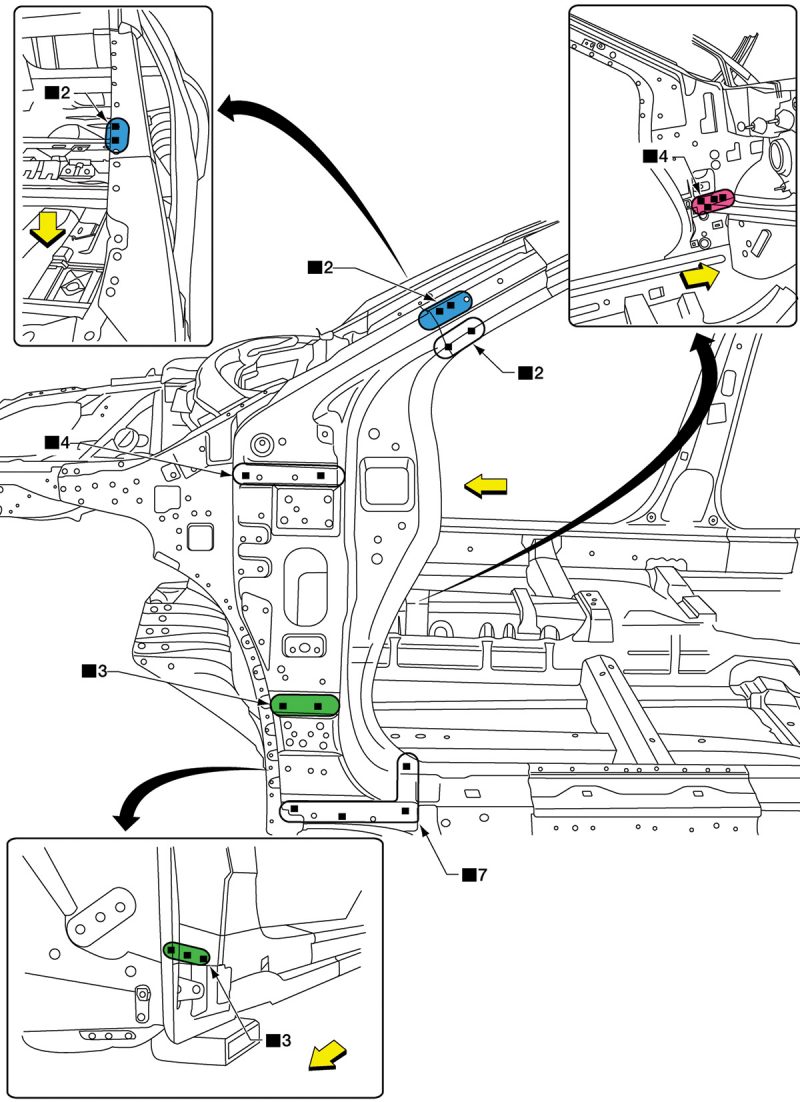
Similar assembly, different cars
Never assume that because a part on one vehicle looks similar to one on another model, it can be repaired in the same manner. For example, the front pillar areas of the 2017 Nissan Maxima, Murano and Rogue do not have the same sectioning options.
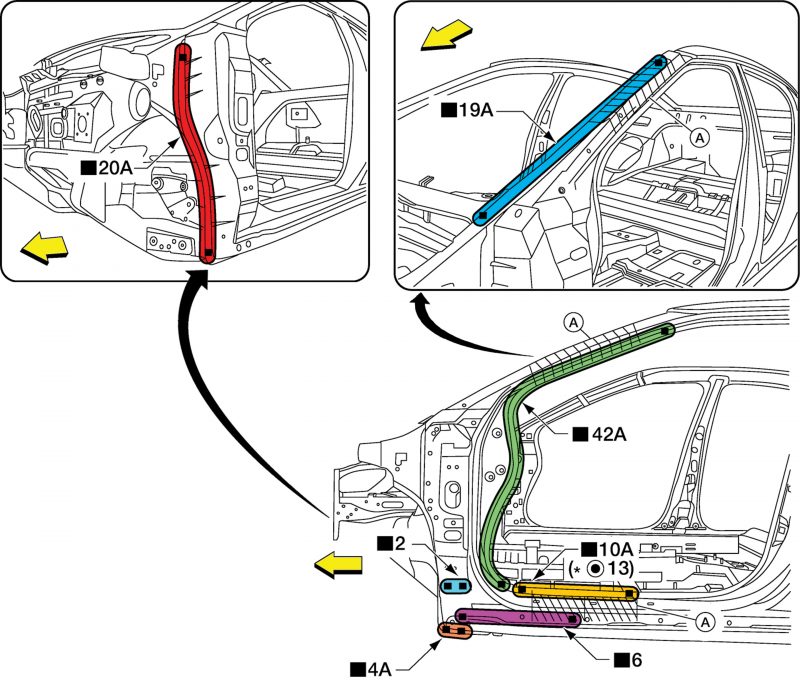
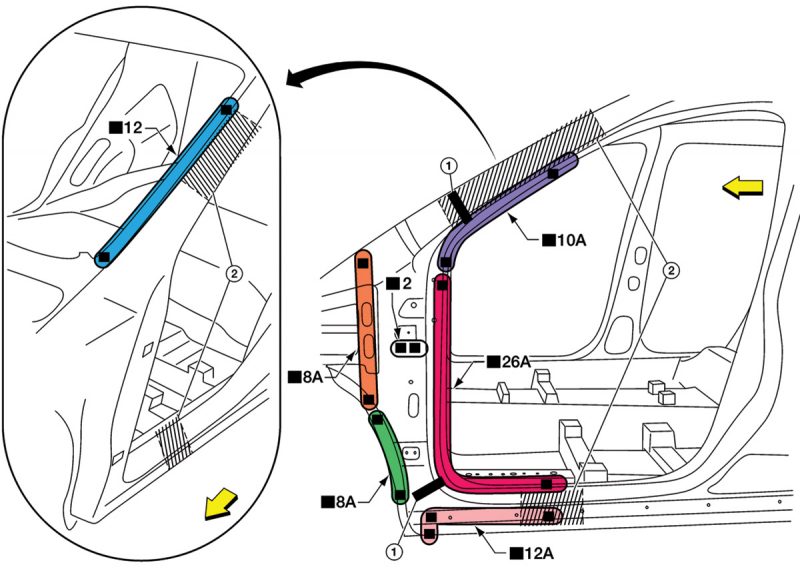
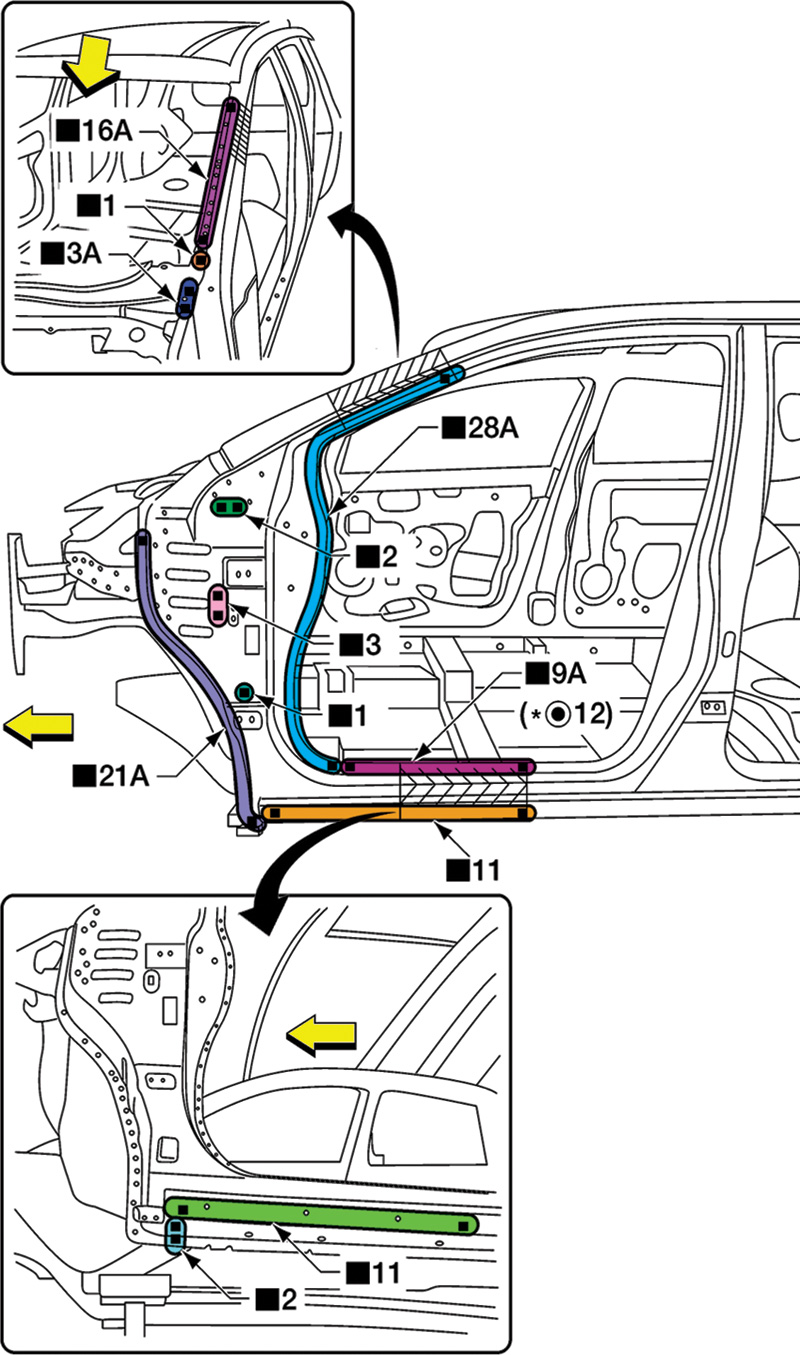
MIG plug welding or spot welds?
The Body Repair Manual often specifies MIG plug welding to replace factory spot welds, but that is the last resort when access is only available on one side of the joint. Although not explicitly stated in the manual, Nissan prefers the use of spot welding instead wherever two-sided access to the joint or flange is possible. Spot welding minimizes the spread of heat beyond the immediate weld location, reducing the chance of weakening surrounding areas.
Use resistance spot welding instead of plug, seam, or torch welding for HSS or UHSS panels. Do not use gas (acetylene torch) welding as it creates a lower strength weld joint.
Note that spot welds on HSS and UHSS parts are harder than those of regular steel panels. When cutting spot welds out of a HSS or UHSS panel, use a low speed high torque drill (1,000- 1,200 rpm) to make cutting easier and help drill bits last longer.
Normal MIG welding is good for use on plate thickness of 2 mm (0.079 inch) or more. Additional types of MIG welding more appropriate for use on thinner plate thicknesses include short arc and pulse welding. Short arc welding requires less heat than the regular MIG process and is thus good for use on plate thicknesses as thin as 1 mm (0.04 inch). Pulsed Arc welding features a low pulse waveform that creates a stable weld puddle penetration and bead shape while maintaining a low heat profile. Pulse welding makes it easier to create finely detailed weld bead patterns.
Combine the thicknesses of the two upper panels to use as the upper panel thickness when calculating the plug hole diameter, current, and voltage (or using a lookup chart) for MIG plug welding a three-plate joint.
Tack weld the joint at approximately 10 mm (0.39 inch) intervals to hold it securely until you complete the butt weld. NOTE: Remove aluminum oxides and magnesium oxides generated at tack weld locations. Not doing so before you start the butt weld results in a weak joint.
Planned success
As you develop your repair plan you must research the vehicle construction and identify which damaged assemblies have subcomponents made of materials that cannot be cut without reducing their strength or intended crumple zone performance.
Always check the Body Repair Manual for the Nissan model you are repairing to determine which damaged components can be sectioned and which must be replaced as a complete assembly. Having this information at the blueprinting stage helps ensure not only a safe repair, but also helps you develop an accurate estimate, order the correct parts, and improve cycle time.
0 Comments