-Frank Walker and Bob Freudenberger
There’s a whole lot of tech involved in high-performance brake systems, and here we’ll start off our ongoing series on the subject with the parts that pinch the pads.
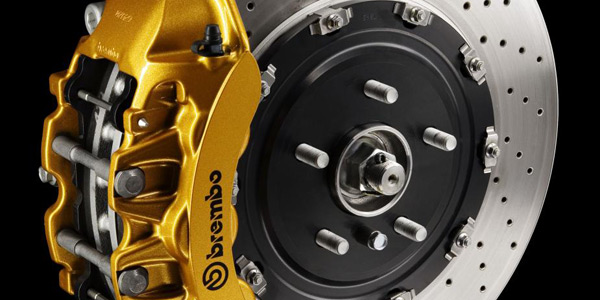
Quite a contrast to a premium HP caliper and rotor combo, not only in appearance, but also in feel and performance.
When it comes right down to it, stopping distance is limited by the adhesion of the tires, and unless you’re driving a vintage vehicle the ABS is going to kick in whenever that’s exceeded. All the stock brakes we know of are powerful enough to lock the wheels and induce this condition on dry pavement (we’ve always said one of the benefits of ABS is the avoidance of flat-spotting that expensive rubber during a panic stop).
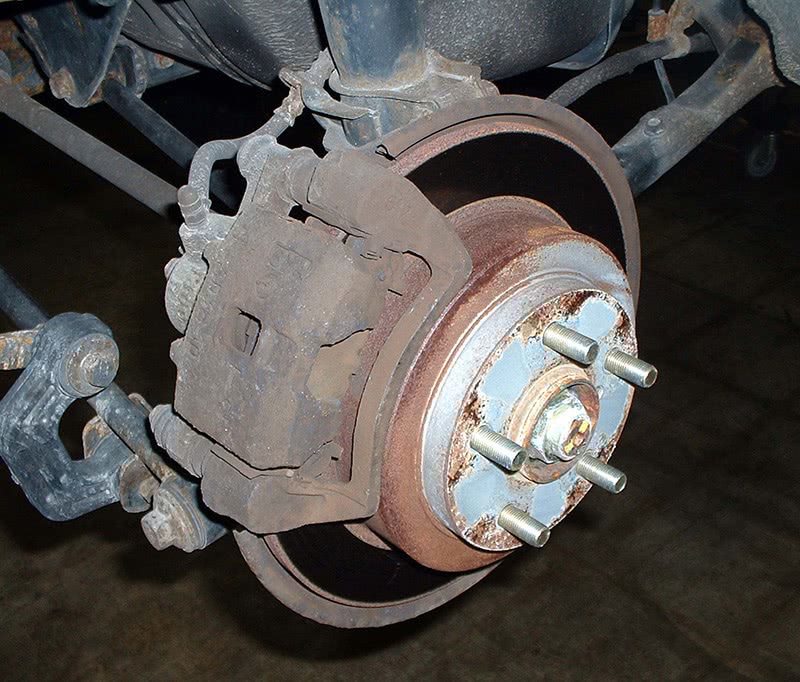
This car isn’t even that old, and look what an ugly, rusty lump that stock floating single-piston caliper is. It’s a wonder they keep working.
The weakness of factory brake systems shows up during repeated heavy decel events in the form of the scary phenomenon known as “fade.†You’re apt to encounter it very quickly on a road course, or on a long, steep downhill run in the mountains, especially if you’re towing a race car or a boat. We’ve experienced it to the point of simply not being able to come to a complete stop at all — talk about white knuckles!
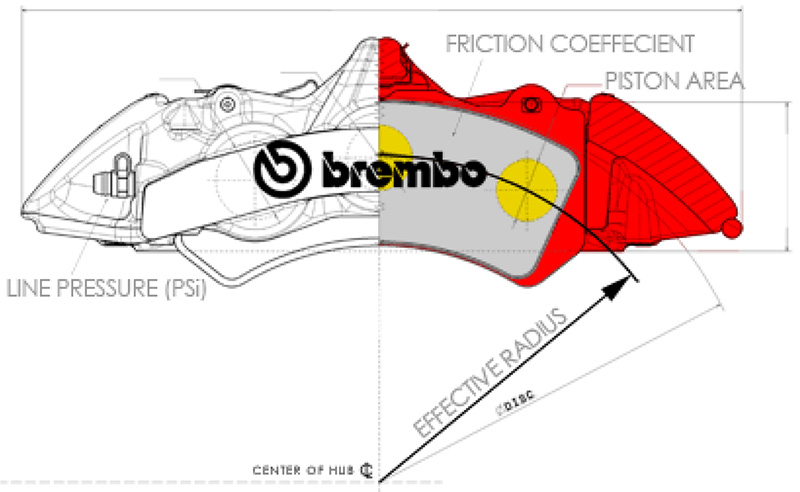
A disc of a larger-than-stock diameter gives combined with a trim multi-piston caliper gives more brake torque through increased leverage (courtesy Brembo).
The main thing the installation of a “big brake kit,†or of any wisely-chosen set of high-performance brake components, will give you is dependability during severe use. The combination of more leverage from bigger diameter rotors, powerful and even clamping force, better heat dissipation, and premium friction material formulas make for peace of mind. Enhanced pedal feel, mostly from the use of braided hoses, also inspires confidence.
Appearance is another part of the mystique. No matter how neat a job you might do with your six-dollar can of red caliper paint, you’re not really going to fool anybody who actually stoops down to take a look. There’s no doubt that high-performance brake parts not only handle heat well, they look cool, too.
Our friend Pascal
In the early days of the automobile, some very clever engineering was employed to apply brakes mechanically. For example, the Italian Bugatti routed the cables over the top of the front axle so that the twisting action generated by stopping added force to the shoe cam lever.
No matter how ingenious the design, however, there was always a major drawback: Nothing could insure that braking force would be exactly equal at any pair of wheels, so there was a good chance that stepping on the pedal would cause swerving and skidding.
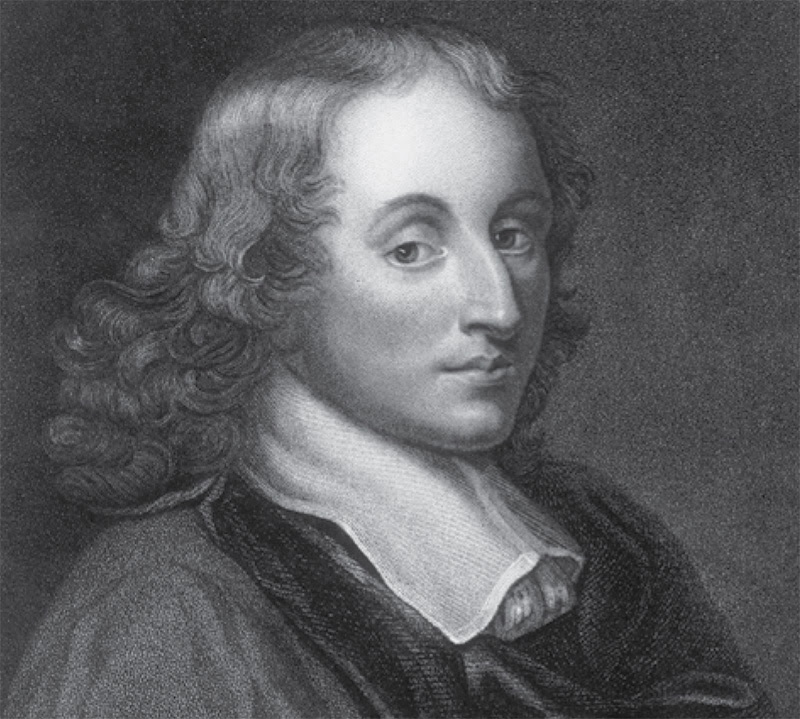
Blaise Pascal, 1623 to 1662
Here’s where 17th-century French mathematician, physicist, inventor, and philosopher Blaise Pascal comes in. In simple terms, Pascal’s Principle (also called Pascal’s Law, or the principle of transmission of fluid pressure) states that any change of pressure at any point in a closed vessel or system containing a liquid or gas at rest will result in a change of pressure at every other point in the vessel or system. For example, when pressure is increased in the master cylinder of a brake hydraulic system, pressure will also increase an equal amount in all the wheel cylinders or calipers.
This made the idea of hydraulically-actuated brakes attractive, but it took many years to develop reasonable dependability. The first car of any consequence to carry four-wheel hydraulic brakes was the 1921 Dusenberg, followed shortly by the first Chrysler.
But how can a puny human leg generate enough pressure to stop a couple of tons of hurtling steel? Again, the science of hydraulics provides the answer. Say, you have a master cylinder piston with a diameter of one inch. If the total of the diameters of the caliper pistons is three inches, the force applied to the master is multiplied by three BUT the distance the master cylinder’s piston travels is three times as far. Think of a hydraulic bottle jack. You’ve got to pump lots and lots of times for the small cylinder to feed the big one to get your mechanical advantage and lift the car. Add to that the leveraged force of the brake pedal linkage (typically three to one) and the assistance of the brake booster, and that tiny column of fluid can transmit sufficient force to the cylinders to stop a vehicle, and then some.
Rigid vs. floating
When disc brakes first started showing up on domestic cars in the 1960s, the calipers were of the rigidly-mounted four-piston variety. They were heavily-built, and their pads wore evenly and lasted for a long, long time. Our editor particularly remembers a ‘67 Thunderbird, all 5,000+ lbs. of it, that still had plenty of (asbestos!) lining left at more than 70,000 miles.
Then the idea was promulgated that you didn’t need to have pistons pushing on both sides of the rotor. Couldn’t the clamping force be transferred from one side to the other by using a sliding or floating caliper design? Not only would using a single piston reduce the possibility of seal leaks (fewer seals, fewer leaks), but it would also be a lot cheaper to manufacture. One more factor was that since rigidly-mounted calipers have no tolerance for side-to-side movement, as little as .004 in. of rear axle end play could push the pistons into their bores enough so that extra fluid displacement is needed before the pads touch the rotor, which can cause a low-pedal condition. Ditto for rotor run-out — the caliper can’t float to follow the waves, so they knock against the pads, and the increased lining-to-rotor clearance is only taken up when the pedal is pumped. The carmakers avoided this potential problem by embracing the floating design.
We’ve always considered this a cost compromise, but apparently it was so compelling to the auto companies that, except for certain imports and sporty cars that continued with two or four pistons, single-piston calipers became the norm. Really, though, when was the last time you saw a leaky caliper, multi- or single piston? Also, since floating types were prone to fore-and-aft rocking, pads mostly exhibited tapered wear, thinner at one end than the other — not something any mechanically-inclined person likes to see. It implies crude engineering and sloppy tolerances.
Multi pot
A calipers may have one to eight (or even more!) pistons. The count, however, isn’t as important as the total piston surface area, and how the force provided is distributed over the brake pad.
The more caliper piston area, the more force is exerted by a given amount of fluid displacement from the master cylinder. A caliper can have a single large piston that offers more surface area than a design featuring multiple smaller pistons.
But a huge piston requires a very large caliper body, which presents problems with fitting the system inside the wheel. Multiple smaller pistons allow engineers to design a longer, narrower caliper that fits in the available space.
More importantly, multiple pistons with different displacements allow a thoughtful distribution of force over the brake pad. To reduce the potential for the leading edge of the pad to wear at a faster rate than the trailing edge, designers place smaller pistons near the leading edge.
Larger pistons placed near the point of rotor exit from the caliper provide slightly greater clamping force to compensate for pad taper. This helps balance pad loading, ensure high pad pressure against a greater portion of the rotor contact area, and increase stopping power.
Calipers with differential piston bore design are directional and cannot be interchanged from side to side. There is a left hand and a right hand caliper, and each should be marked with a rotor rotation arrow that indicates the direction of rotor entry and exit to and from the caliper.
Stressed out
Wheel components take a hit every time you accelerate, stomp on the brake pedal, or tilt through a curve. If you race, drive in the mountains, tow a heavy load, you must also include excessive temperature in the assessment of the amount of stress on your brake components.
As this stress builds, brake components can flex, altering the delivery of fluid pressure throughout the system. Brake hydraulics work well only if the pressure generated by the brake pedal, multiplied by the master cylinder, and transferred to the pads by the caliper has an unaltered path to its destination.
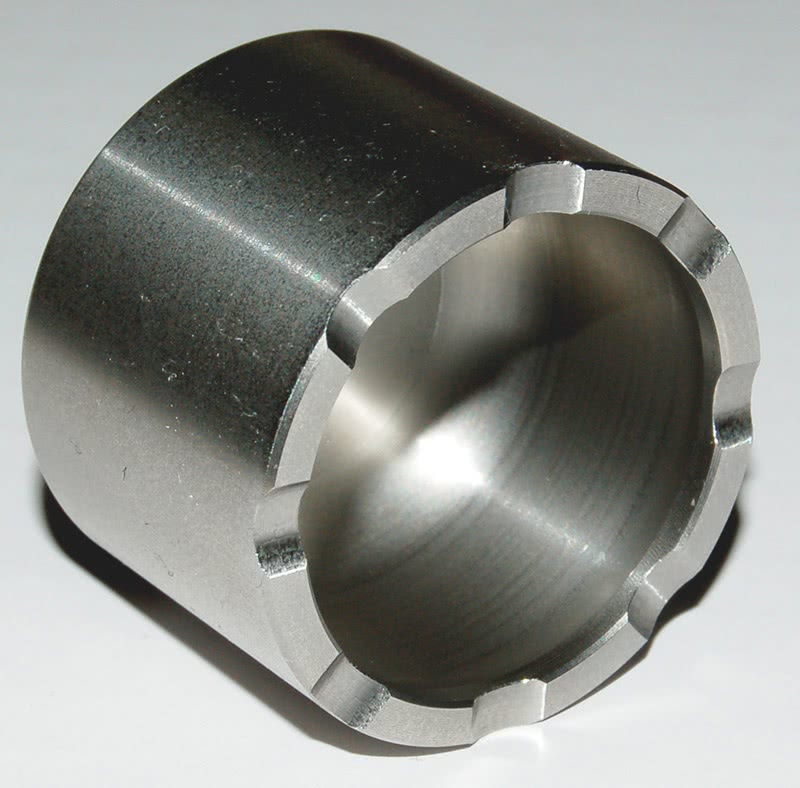
This cleverly-designed stainless-steel piston has gaps that permit air flow between it and the back of the pad (courtesy AP Racing).
Flexing of the pedal lever or its mount, the master cylinder mount, caliper mountings, or the caliper itself can cause the component to reach its movement limit before enough pressure has been created to accomplish the goal. Air trapped in the system, expansion of non-reinforced or aging hoses, unevenly worn pads, and worn wheel components can also cause unwanted deflection.
The result is inconsistent braking performance and a spongy pedal feel. Under severe conditions, these factors can result in a pedal that hits the floor before maximum braking force is achieved.
High performance brake makers upgrade components in many ways to minimize deflection. Assuming no air is in the system and other wheel components are in good condition, you can reduce deflection by installing stiffer calipers, better quality hoses, and stronger mountings and pedals.
Race-bred calipers are machined from substantially higher tensile strength billet aluminum. The higher psi capabilities of the premium grade material makes caliper weight reduction possible without sacrificing rigidity.
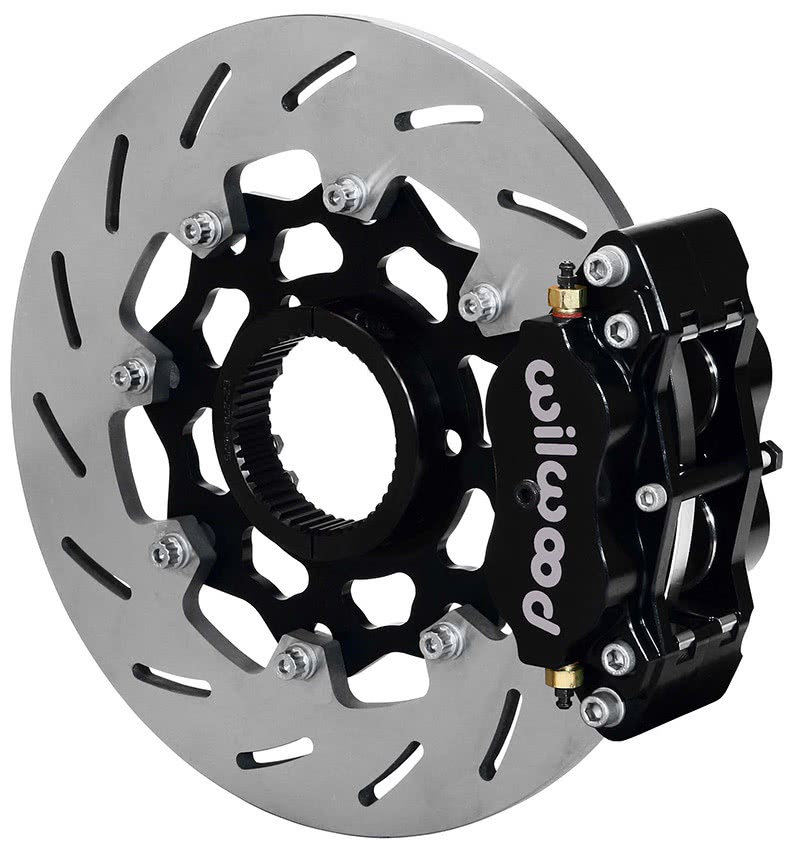
Things get pretty wild and high-tech when you move up to sprint cars where you have to do some of the engineering.
Two-piece aluminum calipers may achieve rigidity by using high-strength steel cross bolts or steel crossmembers and support plates. High-strength steel bolts have an elastic modulus (a measure of the tensile strength of a material) approximately three times stronger than that of aluminum. Steel has another advantage – it maintains its tensile strength longer than aluminum as temperatures rise.
Besides the caliper body, the design and material of the pistons is important. Stainless steel pistons are superior to aluminum at creating a thermal barrier. They help prevent a soft pedal by reducing heat-related brake fluid fade. Some have a castellated edge on the contact face. The gaps allow a cooling air circulation between the pad and piston, thus slowing the flow of heat into the fluid. Others use a separate metal insulating plate that sits on the piston face and prevents direct contact between the hot brake pad and the piston body.
Boiled down
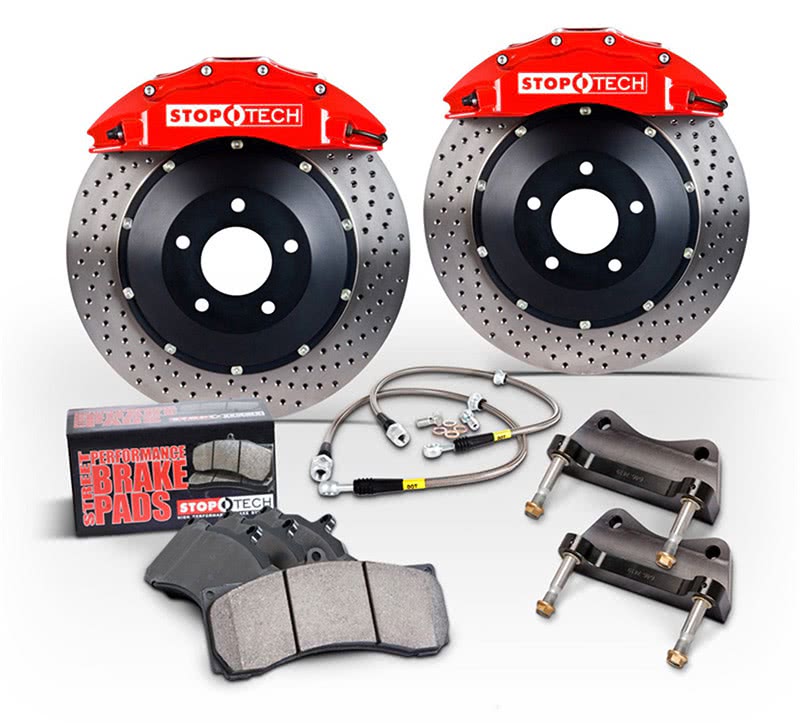
A quality brand’s “big brake kit†will typically include these items, and will bolt right on. The difference, as they say, is like night and day (courtesy StopTech).
We thought it was important to make sure you knew about all the scientific and technological concepts described above, but you know what? Unless you’re putting a hydraulic system together from scratch for a pure race car, most of the subtleties have already been worked out for you by the brand-name high-performance aftermarket brake manufacturers.
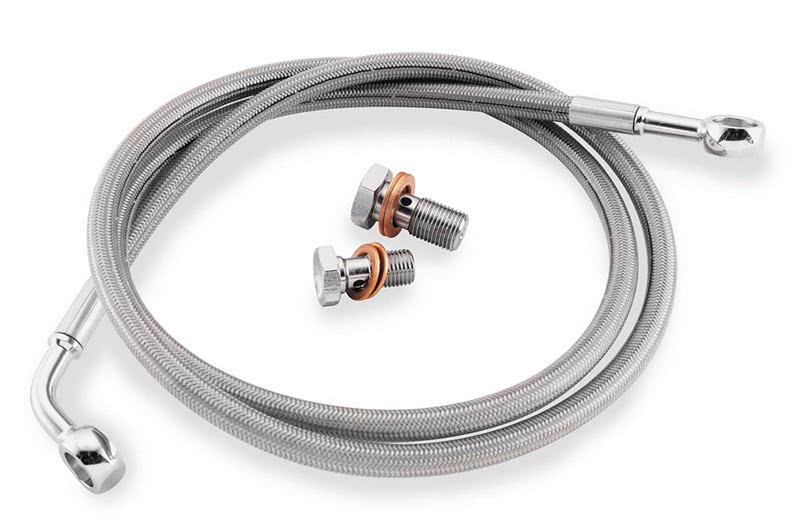
Goodridge braided steel hose combines a smooth PTFE inner lining with a strong braided stainless steel outer mesh. You get unrestricted flow, a brake line with a high bend radius and superior resistance to abrasion, corrosion, and heat-induced expansion. Not only does it look great, but it gives a solid pedal feel.
or example, if you’re contemplating an upgrade to one of the many quality “big brake kits†out there, you might be fretting about what kinds of modifications you’ll have to make to the hydraulic system, say the substitution of a special master cylinder. You can stop worrying. All the quality suppliers have engineered their calipers to work just fine with what you’ve already got in the way of fluid pressure generating and controlling hardware.
The big names typically offer two or three levels of upgrades starting with what’s variously called “Sport,†or “Aggressive Street,†which might include multi-piston calipers and direct-fit mounting brackets, premium pads with linings made using a proprietary friction recipe, rotors that are far superior to the stock items, and the braided stainless-steel reinforced hoses that help provide a great pedal feel, last forever, and look great. The next level might have even more highly-evolved calipers, and perhaps carbon/ceramic discs. Beyond that, it’s serious track-only business, which will require a lot more research than an we can support here.
That was interesting about the reasons of the differing size bores as the rotor exits. I didn’t know that.