This series of articles will cover how to troubleshoot, diagnose and repair common suspension noises on Volvo Vehicles.
Customers come into shops every day, all around the world and say the same thing: “My car is making a noise when I go over bumps,†or some version of that question.
“What does it sound like,†you ask?
The customer will say something like â€I don’t know†or try their best to verbally imitate the noise.
This is where asking the customer the right questions can be the key to quickly and accurately solving the customer’s problem. Because more often than not, when you or any technician takes the customer’s car out for a test drive, he or she may hear multiple noises, especially on higher mileage cars.
Or, more commonly, the technician that test drives the car cannot get the car to reproduce the noises the customer is experiencing. This happens for many reasons.
The customer may not know how to explain the symptoms or noises to the service adviser, or the person that drops off the car may not be the primary driver and he or she gives a third-hand vague explanation of the noise and symptoms.
The service writer needs to get as much information about the noise or noises as possible. Questions like, When, Where and How Often are the basic ones, but in a lot of cases you or the service adviser will have to dig deeper to get the clues to help the technician that’s working on the car save time, money and be able to accurately find the causes of the noises and be able to recommend the needed repairs and parts.
Questions about how the car is used, and what kind of roads cause the customer to hear the noises can be very helpful in reproducing the noise complaint, and that’s what it’s all about. That’s what the customer brought the car in for, and they want answers, not guesses.
If you can’t reproduce the noise, how can you verify that you fixed it?
Of course the best thing that you can do is to have the tech that will be working on the car go on a test drive with the customer. This will not only help pinpoint the noise that the customer is concerned with, but will also allow the tech to eliminate and point out other noises that the customer may have gotten used to or just blocked out.
If on the test drive with the customer you cannot reproduce the noise, try to have the customer drive and observe their driving style for clues.
While on the test drive with the customer, ask them again under what conditions does the noise happen. Is the car cold or will the noise only happen on turns at 90 mph?
More questions about the symptoms and noises while driving with the customer may help him or her be able to explain them better.
What about the other noises you hear that the customer may be oblivious to?
Have you ever had a customer bring a car in for a noise complaint that he/she thought was a very minor issue, only to find that the noise that they have gotten used to, and may think is normal, turns out to be a major problem?
Yes, we all have, but before we start concerning the customer about what it could be, you should perform a complete inspection on the car with extra focus on the problem areas.
It’s a good idea to keep in mind that the noise the customer brought the car in for in the first place is very important to them, even if it’s a minor problem that will not affect anything.
Don’t just dismiss it because it’s a very minor problem like a rattling cup holder; always address their initial complaint before you talk to them about the “real†problems with their car. Let them make the decisions about fixing the minor issues or not.
Are all suspension noises easy to find?
Sometimes yes, sometimes no, but as with anything in life, the more you experience something the easier it is to identify the noises and get to the cause.
If you do this long enough, you will get to the point that you will be able to identify most noises and their causes just by taking the car for a short test drive.
Volvo has issued a lot of service bulletins and technical journals (TJs) for suspension noises over the years on all of their models.
The right service bulletin can save you a lot of time and misery. So, as always, it’s a good idea to check for any available information first, on the Volvo that you are working on.
Tools like the chassis ear tool can help you find some elusive suspension noises but will not work in all cases. Here are a few common worn parts that can cause suspension noises on some Volvo models.
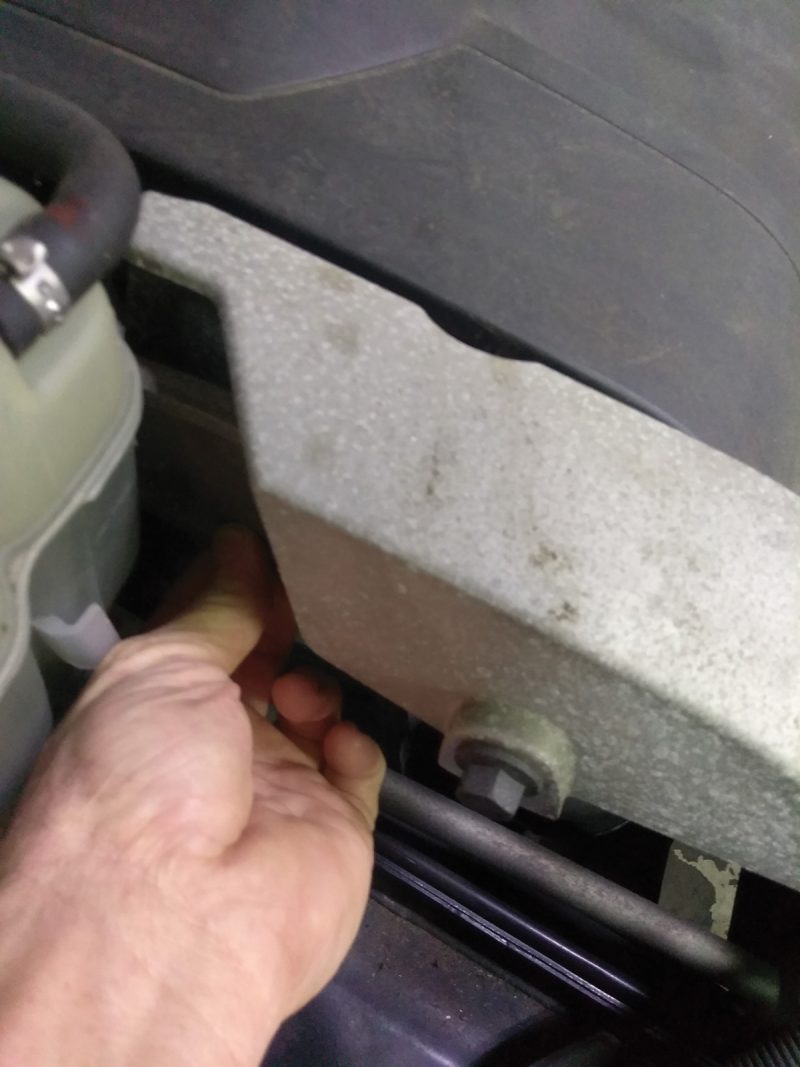
On the Volvo XC90 with the 3.2L engine, the upper torque rod mount, located on the right side of the engine, will start to rattle under light to medium load while accelerating from a stop. This noise can fool you if you don’t know what to look for. The noise that this one makes is unusual and can sound like it’s coming from the transmission or angle gear.
Some shops that have heard this sound have mistakenly replaced the bevel gear and even the transmission to try to “fix†this noise, only to find out that the noise was caused by a much cheaper part.
The noise usually presents itself under light acceleration at around 10 to 20 mph. It sounds like grinding gears in the transmission, much like a metallic rattle.
The noise usually sounds like it’s coming from the area where the transmission meets the angle gear and can make the same noise as worn or broken gear teeth inside a gear box. But before you start pulling apart the drive train, try this.
On the right side of the engine is the upper engine torque mount rod. During your regular inspections on these cars, you should make it a habit of checking these rods for play and rattles.
The best and simplest way to check the upper engine torque rod on a Volvo XC90 with the 3.2L SI engine is to simply grasp the bottom of the rod with two fingers and shake it. If the bushings at either end of the torque rod are worn and dried out it will feel loose and rattle when you shake it.
SWAY BAR LINK RODS ALL VOLVO YEARS AND MODELS
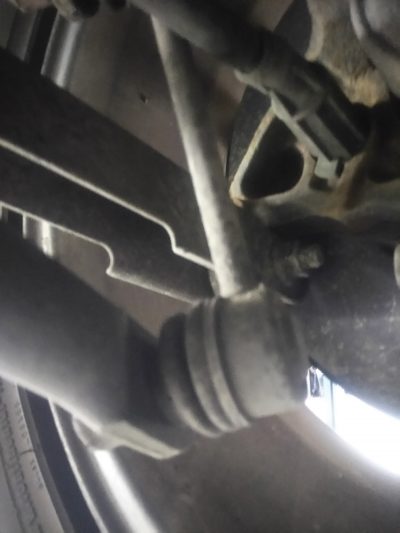
Sway bar end links are suspect. You have probably changed a lot of these parts in your day to day work for various reasons.
Most of the time these rods are easy to spot when they need replacement; either the dust boots are torn, they have excessive play, or they are simply broken. But when you are checking for suspension noises, don’t overlook them just because they don’t exhibit the descriptions above or they look new. They can fool even the most experienced technicians.
One of the most common noise problems with these sway bar links can be hard to spot. That’s because the most common sway bar link noise is caused by one or more of the nuts on the end links becoming slightly loose, allowing the end link to rattle when the car is driven over bumpy roads. So always check the end link nuts with a wrench for tightness; you will be glad you did.
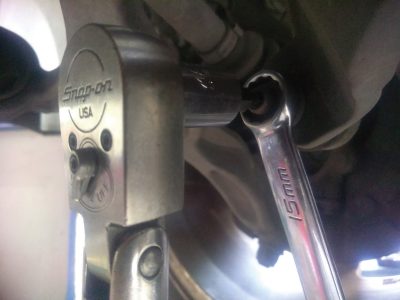
When installing new sway bar link rods on a Volvo, too many technicians are in the habit of using air tools to tighten the end link nuts. This is a bad habit even though it will save time. In a lot of cases using an impact gun can under- or over-tighten the nut, which can cause a noise comeback or, in the case of over-tightening, can cause the end link stud to break prematurely.
The right way to tighten the sway bar end link nuts is with a combination wrench and a Torx or Allen socket to hold the stud in place as you tighten the nut.
You can use a ratcheting box wrench to speed up
this process.
FRONT SPRING SEATS (or STRUT MOUNTS)
If you have been working on Volvos for a while you have replaced your fair share of these. Of course they should be replaced when they are broken, but if you make it a habit of closely inspecting the spring seats on every Volvo that comes through your shop, you could prevent the customer from having to find out about the worn spring seats only after they hear that loud popping sound when they go over a bump.
The best way to inspect these spring seats is with the car fully on the ground so that the struts are loaded. Use a flashlight to look under the strut washer and check to see if the seat is starting to crack or is completely torn. They don’t always make noise when they are damaged or broken.
When you make a recommendation to your customer to replace the spring seats, always recommend them in pairs. If the customer’s struts are worn or have a lot of miles on them, explain to the customer that replacing the struts at the same time as the seats will save them a lot of money on labor since they have to be removed to replace the spring seats anyway.
A WORD ON REPLACEMENT PARTS
Parts like spring seats are available from multiple parts suppliers, and the price of some of these parts can be very low, but of course so can the quality of the parts. The materials used to manufacture these parts can vary too.
So why use OE Volvo parts?
Volvo engineers have designed these replacement parts to the highest standards of quality. They are made of the same quality materials that the originals were, and they are tested in all possible driving conditions for performance and longevity. OE Volvo parts will always fit properly the first time and outperform the aftermarket parts.
In the case of the spring seat, which is just rubber bonded to steel and has a relatively high failure rate, don’t you want to install the best quality part you can?
WORN AND LOOSE FRONT STRUT PISTONS ON P1 VOLVOS CAUSING INTERMITTENT RATTLE NOISE WHEN DRIVING OVER BUMPS AND ROUGH ROADS
When evaluating the condition of struts on cars, most technicians only look for leaks and the number of times the car bounces when the car goes over a bump.
Of course every technician has their own way of evaluating the condition of shocks and struts. And the opinions about the number of miles that shocks and struts should be replaced vary from technician to technician and from one parts manufacturer to another.
There is evidence out there to prove that a strut or shock with a lot of miles on it is not as responsive as a new one that has not been cycled over a million times. And the way the car is used and where it is driven is a major factor on how long the struts will last.
But when it comes to suspension noise, some of the higher mileage P1 Volvos have come into shops with worn strut pistons that can cause a rattling noise over rough roads even though there are no visible signs of fluid leaks coming from the strut assembly.
So if you have one of these Volvos come in with a rattle in the front suspension that has no obvious causes, take a closer look at the struts.
Of course the only way to check for this kind of play in the piston is to disassemble the strut and spring assembly and shake the piston side to side.
You will feel the piston moving and hitting the sides of the cylinder.
2001- 2015 V70/XC90/XC70/S80/S60
Volvo suspension bushings are very high quality and can last for a lot of miles and a lot of years. But as with any high mileage parts that are subjected to constant pressure, varied loads, extreme temperatures and exposure to all kinds of road conditions, there is a lifespan.
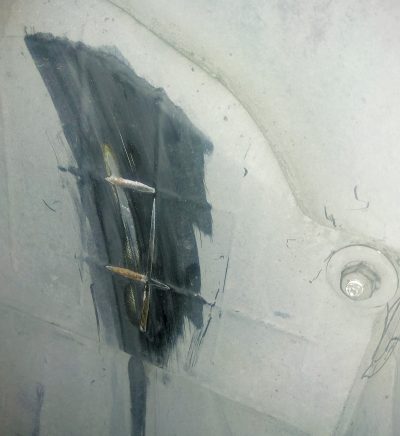
When these bushings break down and crack, they don’t usually make noise themselves. But by allowing the suspension to move further than it was designed to, the worn lower control arm bushings can be responsible for a lot of front end noises.
The most common noise heard by drivers when they have worn out lower control arm bushings happens when the wheels are turned to the full lock position. The excess travel in the suspension can cause the inner sidewall of the tire to rub against the inner fender well.
The other common noise that can be caused by worn or cracked lower control arm bushings is a clunking noise on sharp application of the brakes or on fast acceleration from a stop.
On a car with badly cracked lower control arm bushings, the control arm will travel hard rearward on braking which can cause the front tires to rock back until they almost hit the back of the fender liners. When these bushings are in this condition they can cause problems like poor handling, oversteer and uneven tire wear.
The best way to impress the importance of these bushings to your customer is to have your customer stand outside the car and look at the front tires as you slowly drive the car forward and jab on the brakes.
The sight of their front tires moving 3 to 5 inches to the rear, will convince even the most cynical customer.
Download PDF
0 Comments