Electronic power steering systems (EPS) are now more common than ever on newer Nissan vehicles. This article covers the three types Nissan uses for its EPS, a discussion of its advantages, and tips for diagnosis and repair.
Electronic Power Assist Systems (EPS) are starting to see wider implementation due to the advantages they bring for fuel economy and manufacturing savings. American consumers expect power steering as a standard feature. Nissan works to meet that expectation by going beyond the conventional hydraulic power assist methods to create vehicles that utilize modern electronic controls for improved efficiency. With any new technology comes the need for more training. Here, we’ll help clarify the reasons for using EPS and describe system components, their function, and how to diagnose and repair each design.
The Advantages of EPS
It’s often tempting to dismiss some new automotive inventions as niche market or luxury-car-only developments. EPS is here to stay, and it will become more common. When compared to conventional hydraulic assist, EPS is cheaper to make, malfunctions or breaks down less often, and reduces the load on the engine for performance gains and greater fuel efficiency. You’ll find EPS installed in the newest Nissan Juke, Sentra, Versa, Rogue, LEAF, Altima, and Infiniti M-Series hybrids, and likely more models in the coming generations. This is a wide-scale shift in the manufacturing process, and it is our responsibility as technicians to stay informed about the details of function, diagnosis, and repair.
Let’s discuss how Electronic Power Steering achieves these benefits before we launch into the different designs that Nissan uses. First and foremost, power assist is generated with a DC electric motor instead of a pump connected to the crankshaft. Motor speed can be directly controlled to produce the necessary assist pressures based on sensor input.
Conventional power assist is dependent on engine rpm, and requires idle-up signals for slow-speed parking to prevent engine stalling, and to provide adequate rpm for the necessary fluid pressure. Furthermore, conventional power steering pumps are always generating fluid pressure even when the steering wheel is in the straight-ahead position, simply because it’s attached to the crank, and it must be available when requested. EPS is “smart enough” to know if the driver is turning the wheel, and can determine how much assist is needed. Most driving is going straight ahead, so it is a logical improvement for efficiency to only use engine power (as consumed by the alternator) when necessary.
EPS also requires fewer individual components, reducing the costs of manufacturing and maintenance. Some technicians may groan at the loss of “broken things to fix,” but EPS still relies on sensor input and control modules, all of which may need diagnosis and repair. On the bright side, cars will be less messy to work on without power steering fluid leaks! Modern vehicles are shifting the role of the technician toward computer system diagnosis; EPS just confirms the transition.
Different EPS Designs
Let’s explore the three different ways that Nissan implements EPS in its vehicles. Most common is the steering column-mounted EPS, in which the motor, control module, steering wheel torque sensor, and reduction gear are located under the dashboard in one large group. This EPS design simply boosts the driver’s steering wheel input torque, rotating the steering shaft and causing the steering gear to move. That’s really the entire setup! It eliminates the need for engine bay design to accommodate a pump, pressure and return hoses, reservoir, and a heavy power assist rack. We will explore the components in depth later.
Another EPS design has the motor mounted directly on the power steering rack. The EPS rack assembly contains the DC motor, motor angle sensor, and steering torque sensor. In the Altima hybrid, high voltage from the battery is stepped down to 42V for the EPS motor within a DC/DC converter that is on top of the battery pack. The steering angle sensor is mounted within the steering column. All EPS sensor input is collected by the EPS control unit, which is located under the hood, by the left strut top mount. This design is comparatively more complicated than the above-mentioned steering column EPS. Nevertheless, rack-mounted EPS is more elegant and less spread out than a bunch of hydraulic components strewn about the engine bay.
The last design is a combined, electronic-hydraulic power assist system. Quite simply, the crank-driven power steering pump is replaced by an electronically-controlled DC motor-driven pump that generates the necessary fluid pressure. Nissan calls this hybrid EPS. The hybrid EPS control module calculates pressure based on input from the steering angle sensor on the column and the steering torque sensor in the steering gear. The pump, motor, and control unit are combined into one hybrid EPS unit located under hood. Fluid pressure is transmitted conventionally into a hydraulic power steering rack that works on the steering linkage. This system retains the primary efficiency advantage of being able to control the running time of the power steering pump.
All EPS control modules use CAN communication to get the vehicle speed from the primary ECU or ABS computer. Vehicle speed will affect output torque signals because low-speed steering will require greater assist than high-speed driving.
Any electronic power steering has fail-safe modes designed to protect the DC motor from over-running or the driver from losing steering control in case of emergency. In most instances, if electric assist is impossible, the steering wheel input will still move the steering gear or rack requiring increased driver effort. A warning indicator will illuminate on the gauge cluster, and DTC information is stored that can be retrieved using a CONSULT III PLUS. In the case of the hybrid-electric EPS, the steering rack will fail-safe to having equal fluid pressures on either side of the internal rack piston, and open the flow connection valve to alleviate resistance. In the case of prolonged assist demands, the EPS motor will reduce output gradually. This protection function also works in the event the motor is shorted or otherwise powered incorrectly and does not rely on prolonged steering input.
A Closer Look at the Steering Column EPS
The steering column EPS is the most common system, and also the most simple in design. Until the driver moves the steering wheel, the system does nothing and remains in standby. If the steering wheel is moved, the torque sensor within the column will report the value to the EPS control unit. At that time, the control module will get vehicle speed information from CAN and perform a calculation to determine the assist torque signal. Depending on whether the driver is turning left or right, the torque signal will be a positive (right) or negative (left) value. The signal is interpreted by the EPS motor, which draws enough current to match the determined output torque. Like a window motor, the EPS motor turns clockwise or counterclockwise based on the path of the current determined by the control unit. The EPS motor rotates a reduction gear that will move the steering shaft and change the final drive torque that actually works on the steering gear pinion.
Because the steering shaft receives more torque directly applied to it, the U-joints are strengthened to accommodate the design. The dashboard and chassis have to be designed to allow for a larger steering column, as the EPS set-up is quite a bit larger than a normal column.
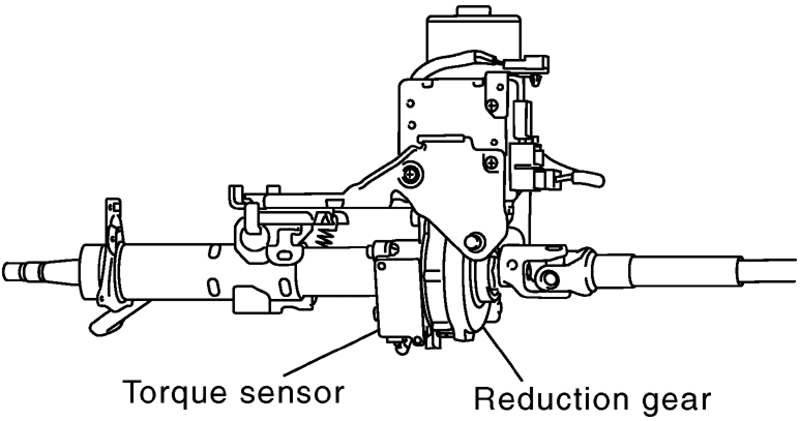
Seen from the side, the torque sensor and reduction gear. You can get a sense of the additional height and size a steering column will require under the dash to add EPS.
In the event of collision where damage to the steering column is a possibility, it may be necessary to replace the complete column and EPS assembly. With the column out of the vehicle, measure the length between the input of the steering wheel to the output of the EPS motor and compare with the specification in the service manual. Also, check the steering column rotating torque with a preload gauge (SST: ST3127S000) to determine whether the column is bent or there is an internal problem. Increased column rotating torque at certain points of travel may cause erratic power assist.
Components of the Rack-Mounted EPS Design
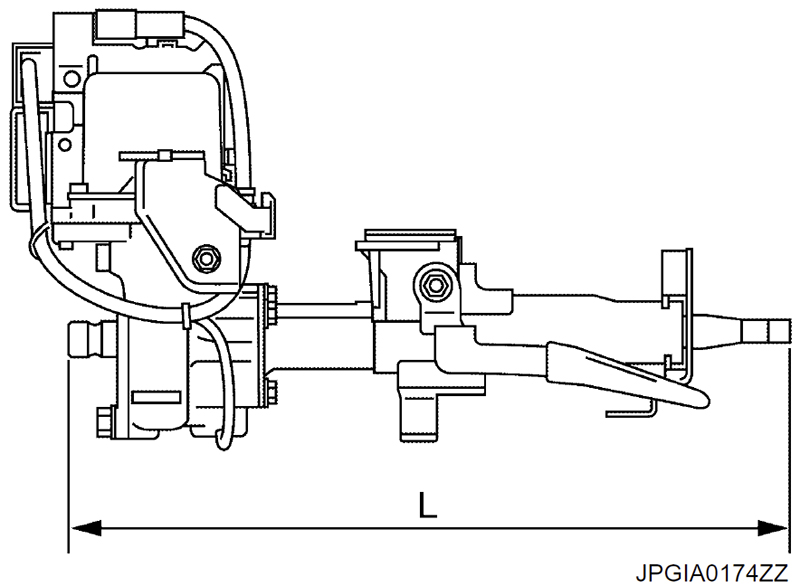
Make sure the column is the specified length in the case of accident repair. A small amount of compression can create a lot of problems.
Control of the electric steering rack design is functionally identical to the steering column-mounted EPS. Steering wheel torque input is processed by the EPS control unit, which then determines the necessary amount of motor assist to provide. The control unit requests and distributes power from the DC/DC converter to step down the high voltage into the maximum 42V needed by the EPS motor. CAN communications provide the steering angle and vehicle speed data. The electric motor moves a worm gear, and a sensor reports its rotation angle to the EPS control module. Consult the service manual to determine the precise locations of every component within a rack-mounted EPS design. The motor and torque sensor are part of the EPS rack, but the control module and DC/DC converter will be located elsewhere.
The Hydraulic-Electric Hybrid EPS
The layout and design of a hydraulic-electric hybrid EPS setup will look similar to conventional systems. In fact, it may actually fool you at first glance as the design requires pressure lines, a fluid reservoir, and hydraulic rack and pinion. The EPS motor is also the pump, reservoir, and control unit, so it is more or less self-contained like the steering column-mounted EPS. The hybrid EPS works just like conventional power steering, but with the exception that the pump motor is controlled identically to the above-mentioned EPS designs. Based on steering torque and vehicle speed, the hybrid EPS control unit determines the necessary amount of fluid pressure, and rotates the vanes of the pump in the appropriate direction to provide assist pressure to the correct side of the steering rack. In other words, it’s an on-demand power steering pump that only works when the steering wheel is turned. Just like conventional hydraulic systems, fluid leaks can develop; plus, any EPS component control may require diagnosis and repair.
EPS Maintenance and Repair
The non-hybrid EPS designs do not require any periodic maintenance. In the event of a malfunction, the customer will complain of noises, steering feedback sensations (vibration, pulsation, judder, etc.), or the “EP” indicator on the gauge cluster may illuminate. The CONSULT III PLUS is necessary for diagnosis. It is possible that low battery voltage can cause loss of important information within the EPS control module.
If a primary EPS component requires replacement, it will be necessary to adjust the neutral position of the steering angle sensor, and/or calibrate the steering torque sensor. This is sometimes referred to as a zero-point calibration. Basically, the EPS needs to be told what things look like when the wheels are pointed straight ahead, and the steering wheel is centered without being actively turned. To set the zero-point for the steering angle sensor, you must use the CONSULT III PLUS and navigate to the ABS ECU work support section to choose ST ANGLE SENSOR ADJUSTMENT.
When performing alignments, the steering angle is not adjustable at the steering gear itself. It is necessary to finish the physical alignment process with adjusting the neutral position of the steering angle sensor as noted above. Forgetting this step may cause the customer to literally have to fight the power steering system to drive straight.
Some Debate
It has been argued that electronically-controlled steering assist may not be as safe as conventional systems, but this is simply not supported by the facts. EPS failures that result in loss of power assist are cited as the primary risk for crash, yet how is this any different from a hydraulic system that loses pressure from a slipping or broken belt, or fluid volume due to a leak? More often, motor assist remains ON despite having completed a turn, which means driver input is required to return the wheels forward. This is more annoying than dangerous. Sensationalism would have us believe the EPS motor gets stuck on and drives the car off the road. How often does a power window get stuck on indefinitely? Nissan is convinced that the future of efficient vehicles will involve EPS, and extensive quality control is involved in guaranteeing the safety of steering control systems.
What Will Happen to the Drive Belt?
Electronic accessories are gaining momentum and support as vehicle inter-system communications and processing power improve. The ultimate goal is to remove the yoke of pulley-driven accessories from under the hood. Electric A/C compressors, EPS, and possibly a replacement for the alternator will reduce the energy wasted on accessories, freeing up the engine for better performance and economy. Stay up to date on new Nissan technology with a subscription to www.nissan-techinfo.com for online training materials and new model introductions.
0 Comments